When he started his firm focused on removing obsolete offshore structures, Brian Twomey chose the name: Reverse Engineering Services. The thinking was that taking out a structure is like building it, but in reverse.
Based on a career spent planning, managing, analyzing, and teaching classes on decommissioning, the managing director of Reverse Engineering has concluded: “It is the wrong name.”
“I started out thinking decommissioning is the reverse of installation; it is not,” Twomey said. “The first thing to know about decommissioning is there is a lot of uncertainty and unknowns that have developed over time due to wear and tear, changes, the environment, and loading all this other stuff” on the structure.
Those complications can lead to costly jobs and budget overruns when plugging wells and removing platforms. That adds to the pain of an obligation with no return on the investment.
“You are not really making money taking the platform out. You have made the money already,” said Jon Khachaturian, president and chief executive officer of Versabar. “We constantly hear: ‘We are going to take it out but we are going to do one more thing.’”
Khachaturian is the founder of the lifting company known as an innovator in the Gulf of Mexico, with advances aimed at reducing the time and risk of removing structures by removing single pieces, grabbing damaged iron where a cable could not be attached, and is now testing an automated cable-cutting system.
Versabar established a technology development partnership with Chevron at a time when the major and other operators were looking for a better way to deal with a large backlog of wells to plug and structures to remove, many of which had been battered by a series of hurricanes from 2005 to 2008.
The average number of structures removed from the Outer Continental Shelf in the Gulf surged from 2003 to 2013 to an average of 250 a year, up from fewer than 150 a year in the previous 5 years, according to data from the US Bureau of Safety and Environmental Enforcement (BSEE). Activity over the first 9 months of 2014 is down sharply. This may mean a change in the trend, but companies doing decommissioning often wait until late in the year when more equipment is available after the prime summer season for well construction projects, said Bill Lee, a spokesman for BSEE.
In the North Sea, a surge in decommissioning spending has long been expected, but has been slow to arrive. Year after year, surveys of industry expectations regularly show an expected higher level of spending on decommissioning about 4 years into the future, said Alan Stokes, global decommissioning manager for WorleyParsons in Aberdeen.
“There is a point where it will accelerate. Delay continues to happen, but how much longer can it go on?” Stokes said.
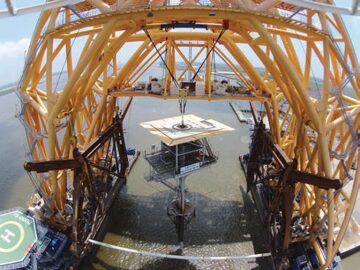
Under Development
The North Sea and the Gulf of Mexico are recognized as proving grounds for dealing with aging oil and gas fields because, among other things, those offshore fields are among the oldest. Many fields are at the stage where they require expenditures to extend their life or end it. There is a growing number of cooperative industry efforts to share information on how best to manage aging properties, including a push by SPE to expand its efforts in this area.
There are common ideas behind what works in the North Sea and the Gulf of Mexico, but applying those ideas differs significantly because of different climates: physically, economically, and politically.
The most obvious difference is the harsh conditions in the North Sea. They shaped the design of enormous production platforms built to develop reserves in the deeper waters of the central and northern North Sea. Those dwarf most of what is found in the Gulf of Mexico, making it difficult to transfer equipment and technology developed in the Gulf.
“The designs need to be fully workable for the North Sea. It is a more difficult environment,” said Twomey. “The Gulf of Mexico is a duck pond compared to where we work in the North Sea.” The experience in the North Sea has been harsh as well, with the few large platform removals costing far more than budgeted, he said.
In a recent SPE paper, Stokes offered an example of where the cost of shutting down and removing an aging North Sea platform swallowed about 80% of the cash flow accumulated over the field’s 20-year life. A government subsidy payment pared the bite to about 65% of the total.
“Our decommissioning costs are affecting our net present values,” said Stokes, adding that the case from 2000 cited in the paper is relevant today.
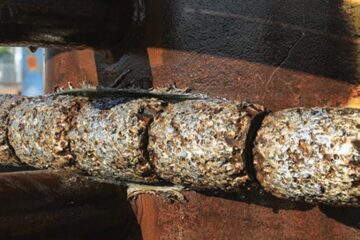
Regulators in the United Kingdom are not pushing for platform removals, as have their US counterparts, whose “idle iron” rule increased removals by eliminating ways to delay the work. A recent study commissioned by British regulators on maximizing production from the North Sea, known as the Wood Review, made a case for procrastination. The recommendations in the study included promoting increased work to maximize ultimate recoveries from older fields, and carefully considering whether structures can be reused, perhaps as a production hub for smaller fields nearby.
“Infrastructure in mature areas of the North Sea is under increasing commercial pressure as maintenance costs increase and throughput diminishes,” the report stated. It cited a study that “estimates between 0.5-2 billion BOE are at risk from the early decommissioning of existing infrastructure.”
This may add another argument in favor of delay. “In the post-Wood Review environment in the North Sea, there is very much of a regulatory shift upcoming. This is an entirely different kettle of fish,” said Philip Chadney, project director for Decom World, a business information firm providing decommissioning data and conferences.
But there are natural limits to how long fields can produce. There are growing efforts in the United Kingdom, with much effort by organizations such as Oil and Gas UK and Decom World’s UK unit. “The only way you can make money on decommissioning is to drive the cost down,” Twomey said.
Off Peak
Platform removal activity in the Gulf of Mexico has slowed as it moves past the events that spurred a previous flurry of activity and change. BSEE reported that 93 offshore structures had been removed through 19 September this year, about half of which were platforms. That is about half the 12-month total of 222 in 2013, which was down 22% from 2012.
Most of the salvage work from structures damaged by a series of four hurricanes in the Gulf of Mexico from 2005 to 2008, and the push by operators to work off a backlog of work created by the change in regulations, may be winding down. Few hurricanes have occurred in the Gulf since then.
The “idle iron” rule in 2010 tightened enforcement of a lease contract provision requiring removal of nonproducing equipment within a set time period by eliminating provisions that allowed operators to delay action. For example, Stone Energy, whose backlog rose as high as 105 idle structures, sliced that total to 9 over a 2-year period, said Gary Siems, decommissioning manager for Stone.
For Stone and Chevron, the need to deal with a lot of facilities quickly inspired them to make changes to reduce risk and cost. Both companies took advantage of new equipment but followed different approaches. Stone built its method around a large new, self-elevating barge with a 500-ton capacity crane that allowed it to bring in experienced crews with a range of skills able to concurrently handle the many stages of a decommissioning job in a compressed period of time.
“If you look at each step on an individual basis, it may be possible in some cases to do some things cheaper with conventional methods. But across the entire campaign, on average we did the work in half the time for one-third less money,” Siems said.
The biggest promoter of new technology in the Gulf was Chevron, which systemically examined the process used to squeeze out costs as well as safety and environmental risks. It has worked with service company partners to create new equipment to put its observations into practice.
One of those was reducing the risks for underwater demolition work by lifting large pieces, reducing the number of cuts needed. It also promoted new cutting methods, reducing the risks of underwater work, or eliminating the need for divers altogether.
Chevron found that bigger lifts save money, but there are other criteria that have to be met. “Projects are measured in terms of cost, safety, and whether it affects your reputation,” said Stokes.
Paying a higher day rate for single rates was preferable over the “stick-by-stick approach” requiring multiple small lifts because it “had the smallest cost per unit and the least risk” of worker injuries or environmental damage, said Don Stelling, president of Chevron Environmental Management Co.
Transferring new ideas to the North Sea will require major modifications. The difference is starkly obvious when comparing the capacity of the best-known heavy lift device built for the Gulf of Mexico with one soon to arrive in the North Sea.
In the Gulf of Mexico, the VB 10,000 made by Versabar used an arching truss supported by two barges to do lifts as heavy as 6,000 tons. That is a fraction of what the first vessel designed for North Sea work, the Pieter Schelte, can lift. It was built by Allseas Group to lift topsides weighing up to 48,000 tons on its front end, and structures weighing up to 25,000 tons on the deck at the stern. In between are crew quarters offering accommodations for 571 staff on the twin-hulled ship that is 1,250 ft long and 406 ft wide.
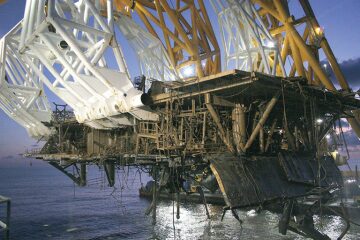
Single lift removals in the Gulf of Mexico save time and money. “I am a big fan” of Versabar, said Robert Byrd, vice president for consulting at TSB Offshore, adding that “it has introduced new types of equipment that have reset the price mark for certain types of operations.”
Stokes said the Pieter Schelte could also “change things dramatically” by removing enormous structures in a single lift. Allseas said the new lift boat will begin working in the summer of 2015. Its first job will be removing Talisman’s YME platform in early summer, followed by a job laying pipe in the Black Sea, and then it plans to begin removing three platforms for Shell from its Brent Field beginning late next summer or in 2016.
When asked about the likely cost of using its big new vessel, a spokesman for Allseas said: “Pricing for Pieter Schelte is of a different nature than for regular heavy lift vessels. The duration of the operation is short, so the cash expenses are limited; but the depreciation element in the price is considerable because of the huge investment in the vessel. As a result, pricing of a job executed by Pieter Schelte may be higher or lower than when done by a semi-submersible crane vessel.”
Those in the industry are waiting to see what the numbers will look like in practice. Stokes said he is optimistic that industry cooperation and innovation in areas such as cutting and planning and managing complex jobs will result in significant savings over the next 10 to 15 years. “The prize in front of us is reducing decommissioning costs,” Stokes said.