Large, unmanned floating facilities may be on course to become the embodiment of all that is promised by the oil and gas industry’s digital revolution.
Fewer people working in remote corners of the globe, leaving behind fewer carbon footprints. Thanks to the advent of the internet-of-things, all systems are monitored from the safety of an onshore center. In the background, a digital twin peers into the future for equipment failures.
Minor tasks, such as leak detection and corrosion monitoring, are done by a diverse cast of robots and fixed sensors. Bigger maintenance projects are performed by human crews who visit only once or twice a year via a service vessel—there will be no helipad. Also absent are any staff accommodations, cranes, or a control room.
This is a quick snapshot of Aker Solutions’ latest version of an unmanned floating production, storage, and offloading (FPSO) vessel. The Norwegian offshore engineering firm has been iterating on the idea since at least 2017 when it promoted unmanned FPSOs to drive down offshore development costs.
And while it remains today only an idea, there are just a few scalable barriers keeping an unmanned floater from being realized, according to Aker Solutions Senior Manager Anna Frostad.
“The unmanned FPSO concept improves both field economy and HSE—and I therefore think this is the design for the future,” Frostad said during an online presentation of a technical paper (OTC 30905) she coauthored for the 2020 Offshore Technology Conference.
In terms of savings, the paper suggests that the future owners of an unmanned FPSO will likely be oil companies that are committed to long-term results. To build one might only be 10% cheaper than to build a conventional FPSO. On the back end though, first adopters may see a reduction in typical operating expenses of up to 30%.
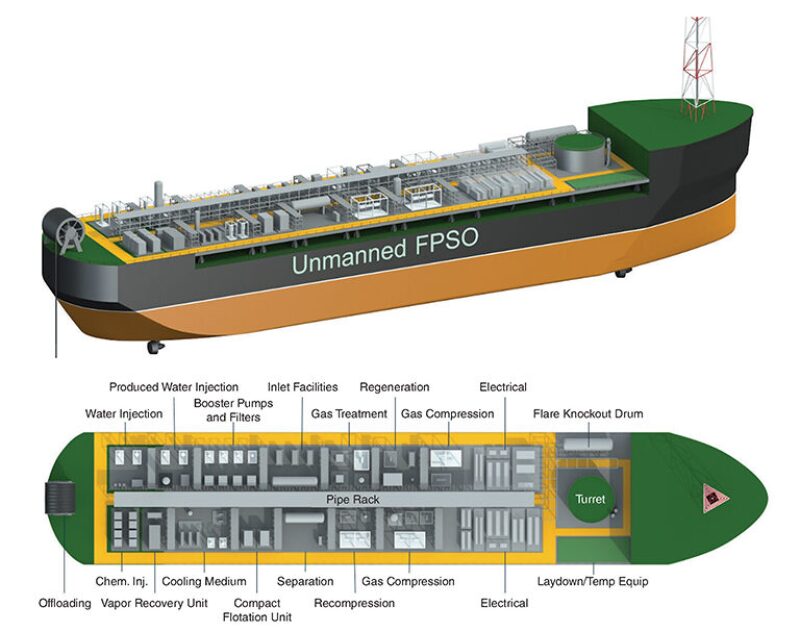
Frostad emphasized that whoever is first must also adopt a “subsea mindset” and a very large digital tool box. She outlined three key elements to the subsea mindset: design simplicity, high-quality equipment, and a modular layout that enables a “plug-and-play” approach to replacing critical systems.
Taking this approach conceptually also meant that the design engineers would need to forego the adaptation of existing FPSO designs. “The starting point was a blank sheet of paper,” with the overriding principle being that every system added to the design needed to be “justified in,” said Frostad. The result is what the company calls a lean design.
From the highest level, the lean FPSO she described shares many of the same characteristics of a typical manned FPSO, including a tanker-shaped hull.
The planned-for oil storage capacity is 1 million bbl, the maximum operating depth is 1000 m (about 3,280 ft), and its distance to shore is limited to 200 km (about 125 miles). As oil is stabilized on the topside, the natural gas is to be conditioned, compressed, and reinjected into the subsea reservoir.
But the broad similarities end there.
To achieve the highest order of reliability—arguably the biggest requirement for the concept’s economic feasibility—Aker Solutions contends that subsea processing technology must be leveraged. Notably, the firm is a pioneer in this arena, having installed the world’s first subsea compression system in 2015 at Equinor’s Åsgard field offshore Norway.
The firm has also designed several unmanned (or normally unmanned) fixed-leg platforms. While unmanned platforms have existed for decades, they are marked by a higher-than-expected number of maintenance visits, each one eroding their value proposition.
A new generation of more sophisticated unmanned facilities has attempted to shed this old reputation, however, Frostad explained that their scope in terms of crude processing remains highly limited. “As of today, offshore full-processing platforms are permanently staffed due to a large number of manual operations and maintenance tasks,” she added.
By adapting recently proved up subsea equipment for use on the topside, she argued that operators can reliably stretch out both the failure rate of equipment and physical inspections. Her paper highlights that Åsgard’s subsea compressor has a mean-time-before-failure rate of 7.9 years “which is significantly higher than for conventional, topside compressors.”
The study’s ideal target for planned production downtime is just 16 days annually (14 days for manned inspections and 2 days for shutdown and startups), which would allow it to maintain the same availability rate of top-tier manned FPSOs.
To aid in the effort of keeping people off the vessel for as long as possible, fixed cameras, drones, and crawlers will be given the job of inspecting platform conditions autonomously or remotely controlled by inspection teams onshore.
While presenting, Frostad shared that the overall unmanned concept could be applied to other types of platforms and offshore conditions.
In a related development not covered in the paper, Aker Solutions was awarded in March 2019 the front-end engineering and design contract for a Chevron-operated gas field offshore western Australia.
If commissioned, the project would involve installing the first subsea compressor outside of the North Sea and the building of an unmanned power and control semisubmersible floater—representing a potential stepping stone to the more complex unmanned FPSO concept.
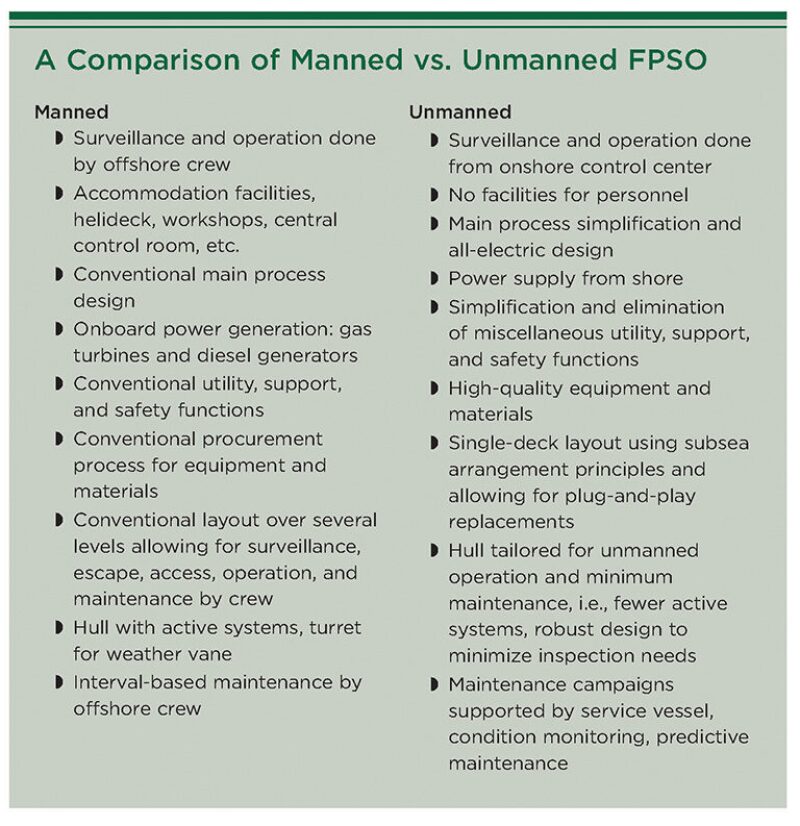
The Cost of a Subsea Mindset
The estimated cost of Aker Solution’s unmanned FPSO is about $1.8 billion—or about 10% less than a manned unit of similar capabilities. At first glance, the concept’s capital savings may be considered relatively small considering that the topside of an unmanned FPSO would weigh just half that of the manned variety.
According to Aker Solutions, the big savings comes from a lower overall cost of ownership. In its study, the firm found that operating expenses on an unmanned FPSO would be reduced by 25 to 30%.
“The decrease is dominated by the reduced cost for offshore personnel,” said Frostad, adding that the unmanned concept targets a requirement of about 7,000 offshore staff hours annually compared with the 260,000 staff hours consumed by a typical FPSO crew of 60 people—a reduction of 37-fold.
Several millions of dollars a year will be saved by eliminating helicopter transports. This simplifies the construction process too, but it also removes a major safety concern for offshore operators since over the decades helicopter crashes have claimed the lives of dozens of oil and gas workers.
The FPSO’s slimmer profile is achieved partly by using a single-deck layout vs. the traditional double-deck seen on many FPSOs today. In addition to achieving the reduced-weight goal, a single-deck facilitates the installation of topside equipment with the systems most likely to be replaced located on the edges of the FPSO for easier access.
Hundreds of more tons are removed from the equation by negating many otherwise ubiquitous elements of a crewed FPSO. In line with the elimination of staff quarters and workspace, there is no need for hot-water or air-conditioning units.
Maintenance-intensive emergency preparedness systems are gone too—including lifeboats and fire water pumps. Chutes will replace the lifeboats, though the main route of escape for any visiting personnel is to be a motion-compensated bridge attached to the service vessel.
Flame-resistant materials, firewalls, and service vessels equipped with water pumps will be relied upon in the event of a fire. Lacking its own cranes, the vessel will similarly rely on those found on attending service vessels.
With many more systems no longer needed and other key functions shifted elsewhere, the estimated weight of the unmanned FPSO topside is 10,000 tons compared with 20,000 tons for a manned FPSO.
Historically, topside weight is a reliable indicator of cost, but as Frostad pointed out, the subsea mindset introduces new tradeoffs which limit the ability to save on construction costs.
Chief among them is the fact that an unmanned process facility of such magnitude would require the most- robust equipment and materials available. For Aker Solutions, this means using “subsea-derived” technology that includes modular pumps, compressors, and scrubbers.
And to keep personnel costs to a minimum, these modules are to be replaced with new spares instead of repaired—another factor driving the overall capital cost closer to that of a manned FPSO. Aker Solutions expects that over a 20- to 25-year lifespan, the unmanned FPSO would see 35% of its topside systems ripped and replaced.
Another cost consideration involves powering the FPSO from shore. While removing the power plant means shedding more than 500 tons of weight, delivering electricity from shore to an FPSO is likely to be more costly (both from a capital and operating cost perspective).
Moving the power supply onshore may become more attractive and economic depending on how CO2 emissions are priced in the future, the paper points out. Aker Solutions calculated that doing so would cancel up to 240,000 tons of CO2 emissions annually, but only if the power source were to be “green,” implying that it must be from hydroelectric, wind, or solar generation.
And though the topside is significantly smaller, the other half of the FPSO, the hull, must be less prone to fatigue than the hull of a conventional FPSO to reduce the need for inspections. As a result, the hull provides no savings to the owner of an unmanned FPSO.
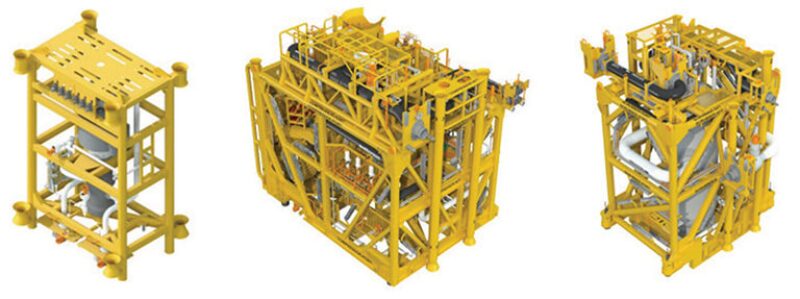
Some Missing Pieces
Frostad noted that while the study found “no particular showstoppers,” there are several areas that need to be further developed before the unmanned FPSO concept is brought to the shipyard. For instance, she said improvements to certain topside equipment is still desired.
The other side of the equipment problem involves awareness. To solve that, the unmanned FPSO must be replicated in the form of a digital twin—a popular, but still-emerging software solution used to simulate the operating conditions of large offshore assets.
As a feature of the digital twin, predictive maintenance programs will help onshore operators anticipate failures or take actions to delay them. “To enable this, it is crucial that all equipment is sufficiently instrumented, and that reliable, fairly long-term prediction algorithms are in place,” said Frostad, adding that improvements in this digital arena are needed as well.
The design of the unmanned FPSO will also need more tweaking so that it can better accommodate its crew of inspection robots which will have different mobility requirements than humans. Innovation is also required to advance the capabilities of remote intervention. While drones and crawlers are proving themselves to be reliable inspectors, they are not yet fixers.
Cargo offloading is yet another unassuming area in need of maturing.
Traditionally, moving the crude re-quires personnel on both the FPSO and a shuttle tanker to work together. To offload oil without anyone on the FPSO, Frostad said the study considered two options: the use of an offloading buoy or a tandem system.
In the interest of keeping costs down, the latter was favored; however, a system designed to be controlled from only the tanker does not yet exist—presenting a two-pronged problem.
First, current tandem systems involve physically mooring a tanker to its host FPSO. To circumvent the mooring process, the unmanned version will instead rely on dynamic positioning to maintain a safe distance from a tanker.
The second issue involves getting the product off the FPSO without anyone onboard. To do that, Aker Solutions said it is working with equipment makers to devise a way to move all aspects of connecting and disconnecting the flowlines to just the tanker. The idea is considered feasible, Frostad said, but she added that it would require retrofitting tankers and then field testing the new connection systems.
Perhaps the final missing piece to realizing the dream of the unmanned FPSO are the regulations concerning such a vessel. On this point, Aker Solutions acknowledges in the paper that the unmanned FPSO concept “is considered undefined by governing rules and regulations and may require discussions and clarifications towards authorities for approval.”
A likely sticking point, if there is one, is the absence of typical safety systems, particularly those related to firefighting.
The engineering firm is reasonably optimistic that the unmanned concept would pass muster in both Norway and Australia—home to two of the world’s strictest offshore regulatory regimes—but because it has never been done, “it may be considered a risk for the project that the safety system design will not be approved by the authorities.”