Despite multitier safeguards, blowouts occur. When such accidents happen, rate estimation is an important and daunting task. This study presents an analytical model coupling the flow in a reservoir/wellbore system of a gas well. The model considers flow in the tubing, annulus, and riser and the attendant heat transfer.
×
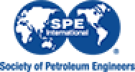
Continue Reading with SPE Membership
SPE Members: Please sign in at the top of the page for access to this member-exclusive content. If you are not a member and you find JPT content valuable, we encourage you to become a part of the SPE member community to gain full access.