The planning process for developing a well-specific subsea-capping contingency plan involves assessing the feasibility of deploying a capping stack from a floating vessel, determining the weight and stability of the capping stack to overcome the force of the blowout jet, and performing dynamic-flow simulations of closing the capping stack outlets without loss of well integrity. This process not only assesses the feasibility, complexity, and risk exposure of the capping operation but also may justify further planning, studies, or expenditure.
Introduction
Blowout-kill techniques can be classified as either surface-intervention or relief-well methods. Relief wells aim to kill a blowout from the bottom by injecting fluid into the wellbore until the influx of formation fluid is stopped and the well is static when pumping stops. In many cases, a relief well will be the safest intervention and have the highest likelihood of success, and often it is considered the last line of defense against a blowout.
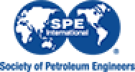