BP’s largest subsea development, PSVM, is the first ultradeepwater development in Africa and is the most expansive subsea development in the industry to date because of its water depth and geographical spread. It sits in 2000-m-deep water northwest of Luanda, Angola. This paper discusses the keys to the successful delivery and well productivity of the first seven of 40 planned wells of the development.
Introduction
The PSVM development is an ultradeepwater project offshore Angola (Fig. 1). The development will access resources from four fields—Plutao, Saturno, Venus, and Marte—which will be tied back to a single central floating production, storage, and offloading (FPSO) vessel. All 40 of the planned development wells are subsea, in water depths ranging from 1800 to 2050 m. Of the 40 wells planned, 22 are producers and 18 are injectors. All four fields produce from and inject into poorly consolidated Miocene turbidite sandstone reservoirs; consequently, downhole sand control is required for all development wells.
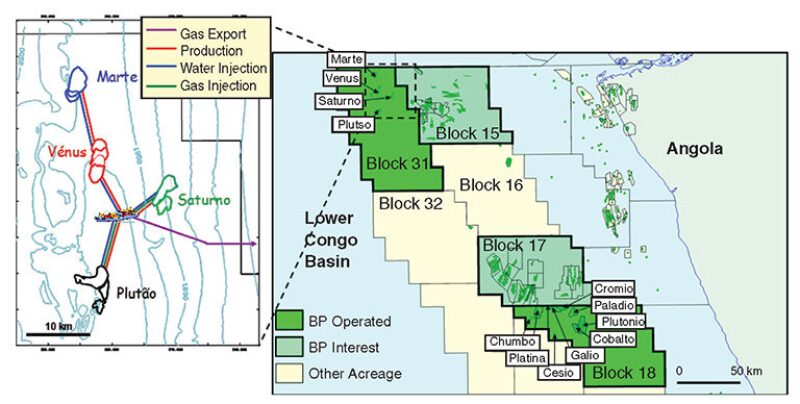
Sandface-Completion Design
The principal design objectives of the sandface completions for the development wells were
- Access all net sand across multiple units separated by long shale intervals in trajectories from 0 to 90° and openhole lengths from 100 to 600 m.
- Keep the formation sand in situ for producer wells, and design openhole water-injection wells highly tolerant of fines backproduction to the wellbore.
- Provide assurance of installing robust sand control, and limit solids production to target levels.
- Minimize equivalent circulating density for a low-fracture-gradient environment.
- Minimize formation damage and shale reactivity, thus providing maximum productivity and injectivity by achieving mechanical skin factors of less than +5 for producer wells and less than +7 for injector wells.
- Provide facility to incorporate downhole flow control or shale isolation through high-integrity openhole zonal isolation.
- Use equipment with a proven track record where possible, and verify equipment reliability and integrity for first-time correct operation and 20-year well life.
- Minimize losses to the formation while running the upper completion, and enable the completion to be landed, tested, and packer set without slickline or coiled-tubing intervention.
Producer-Sandface-Completion Basis of Design. The completion type assessed to be capable of meeting the design objectives for production wells was an openhole gravel pack (OHGP). Taking into consideration the properties of the rocks exposed in the long openhole sections and the operating environment, a viscous-gel-type gravel pack with alternative path functionality was selected over a circulating alpha/beta-type gravel pack, to provide increased assurance of installation success.
Water-Injector-Sandface-Completion Basis of Design. Limited aquifer support necessitated a significant number of water-injection wells for pressure support to the production wells at an almost 1:1 ratio. Also, aligned with an additional desire for reservoir sweep, the wells would be positioned on the periphery of the fields, predominantly below the oil/water contact (OWC). As such, the sands would likely be more marginal in quality. Given the producer/injector-pairing strategy, rigor in design and installation equal to that focused on the production wells was required.
Because of the stacked nature of the sands and their dispersion throughout the gross interval, injection conformance might be difficult to achieve along any completed interval, which could lead to a requirement for multiple wells injecting in individual zones and an increase in project costs. Allowing for the ability to include downhole flow control (DHFC) functionality where required would provide the opportunity to force injection conformance. Openhole standalone screens (SASs) were selected as the completion type for water-injection wells to best satisfy the objectives.
Gas-Injector-Sandface-Completion Basis of Design
The initial sandface-completion design chosen for the gas-only injectors was SAS completed above the OWC. The ability to inject sufficient gas into the reservoir was absolutely critical to achieving the desired PSVM oil-production profile. The gas-injection well completed to date is the only gas-injection well at startup; achieving its planned injectivity fundamentally underpins the delivery of the oil-production-profile ramp-up and early plateau period. However, because of the significant concerns of poor reservoir connectivity above the OWC, it was later agreed that there would be greater exposed net pay and a far higher probability of connectivity to support the producers if the completed section of the well was extended to below the OWC.
Upper-Completion Design
The upper completion was selected on the basis of some key considerations and design criteria, including
- Facilitate a common completion design with standardized completion components that will be aimed at minimizing pressure loss.
- Minimize ultradeepwater remedial interventions and workovers by selecting optimal, fit-for-purpose equipment that is designed for the environment and life of field.
- Use corrosion-resistant completion equipment, designed for maximum reliability and well integrity.
- Incorporate permanent downhole pressure and temperature gauges in all wells and downhole flow control in dual-zone injection wells.
- Install downhole chemical injection to reduce the formation of scale in the producers.
- Provide remotely operable downhole well-control barriers so conventional vertical trees can be run independent of a rig after the completion without having to run or retrieve workover risers and suspension plugs.
- Clean up and test all production wells from the rig before first oil; thereafter, only the first producer in each field or in a new segment of an already drilled field will be cleaned up and tested from the rig; all other wells will be cleaned up to the FPSO vessel.
Producer-Upper-Completion Design. After establishing PSVM field production parameters and in conjunction with tubular-vertical-lift-performance analysis iterations, 5½-in., 13% chrome, 800-ksi-yield-strength tubulars were deemed the most versatile option for the completions. The completion-equipment components feature similar metallurgical properties, which assisted with equipment standardization.
Water-Injector-Upper-Completion Design. The water-injection wells were required to inject a mixture of treated seawater and produced water, so the additional implication of carbon dioxide corrosion needed to be addressed. Thus, the minimum metallurgy required for life-of-field integrity was determined to be 25% chrome. The upper completions are also designed with the ability to incorporate DHFC equipment and zonal isolation by making the interface between the upper and sandface completions compatible for intelligent-well requirements. A schematic of a typical DHFC water injector is shown in Fig. 2.
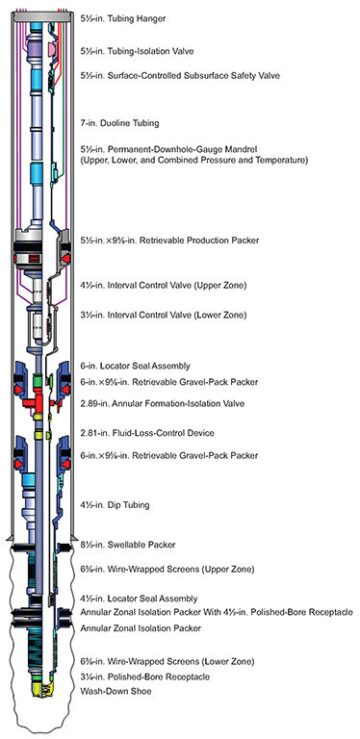
Gas-Injector-Upper-Completion Design. The tubing metallurgy requirement for dry-gas service is carbon steel; however, for PSVM, the gas injectors use 1% chrome carbon steel to align with the water-injection base tubing and allow synergies in supply chain.
Drilling- and Completion-Fluid Design
The reservoir drilling and completion fluids used for the project underwent a detailed laboratory assurance assessment that requires testing of all fluids to confirm compatibility between each fluid with fluid/fluid-interfacing tests, and fluid/reservoir compatibility by coreflood return-permeability testing. Following drilling of the reservoir section, the fluids program required the use of conditioned drilling fluid, various pills and spacers, completion fluids with various chemical additives, and a gravel-pack-carrier fluid. All of these were thoroughly tested in the fluids laboratory to confirm that they demonstrated low skin or no formation damage potential.
Completion-Installation Results
Well Productivity. Four of the six OHGP wells completed to date have been connected to the subsea flowlines and are producing back to the FPSO, with two still suspended while waiting on tieback to the FPSO subsea infrastructure. After the upper completion was installed, the wells were initially flowed back to the drilling rig for cleanup. After the cleanups were complete, the wells were tested and shut in for a pressure-buildup survey.
The four PSVM OHGP completions installed and tested to date have achieved an average of 80% completion efficiency compared with the reported average of 62% in analogous offset wells completed in the same geographical basin.
Well Injectivity. To clean up PSVM water injectors, a filter-cake breaker is circulated into the openhole section during the lower-completion installation, which is designed to water-wet the mud solids and then break down the carbonate solids. It is not possible to backflow the water-injection wells to the FPSO, so, after installing the upper completion, the openhole and tubing contents are bullheaded to the formation above sand-fracture pressure, followed by a seawater-injection test from the rig.
Keys to Success
Knowledge Sharing. Throughout the design, planning, and execution stages of the project, the best practices and lessons learned from the BP Greater Plutonio development and other operating partners in Angola were reviewed and incorporated as appropriate. Continuity of the team throughout the various stages of the project was also a big factor in program success.
Equipment Design and Qualification. The aim of the project was to minimize the time spent on detailed design reviews and failure-mode-effect and criticality analyses where possible by selecting equipment with a proven track record in relevant operating environments.
Equipment-integrity assurance is key to successful first-time installation and longevity of a completion. Therefore, before equipment manufacturing, a rigorous quality-control plan was established with each of the service providers.
Rigorous Planning. Rigorous planning from the design phase through the execution phase was necessary to successfully install completions to meet the stated objectives, maintain full sand-control integrity, and provide full functionality of installed completion equipment, all without damage to the environment or people.
Equipment design reviews and qualification testing, audits, quality control during equipment manufacturing, peer reviews, system-integration tests, and complete well-on-paper exercises are a few examples of the meticulous planning that was required to make the PSVM completions successful.
System-Integration Testing. The first of two system-integration tests was performed at the primary completion vendor’s test-well facility, which mimicked an onshore drilling rig.
In a benign, freshwater environment, the test facility was optimized for capturing downhole and surface data, while also serving as an enabler to run, set, test, and retrieve completion components.
This article, written by Special Publications Editor Adam Wilson, contains highlights of paper SPE 166257, “Angola Ultradeepwater Development: Pinnacle Completion Designs Deliver Prolific Production,” by J.F. Peña, A.Q. Joseph, N. Oakey, B. McNerlin, SPE, and S.A. Ralph, BP, prepared for the 2013 SPE Annual Technical Conference and Exhibition, New Orleans, 30 September–2 October. The paper has not been peer reviewed.