While renewable energy development continues to rise, the transition from traditional hydrocarbons is not progressing as rapidly as once expected, and oil and gas is still set to be a key player in the energy mix by mid-century.
There has been significant development of green technologies and increased investments in wind, solar, and hydrogen energy, but the demand for hydrocarbons continues to grow, driven by global energy demand and the complexities of transitioning entire energy infrastructures.
As the world aims to balance energy security with sustainability and affordability, it is clear hydrocarbons will continue to fulfil a critical role in meeting energy demand for the foreseeable future. It will take the next 27 years to move the energy mix from the present 80% fossil/20% non‑fossil split to 48%/52% (DNV Energy Transition Outlook, 2023).
Looming net-zero goals have placed operators under the microscope as they grapple with the challenge of maintaining profitability while adhering to environmental regulations. There are also increasing expectations from stakeholders and investors who are factoring environmental, social, and governance criteria into their investment decisions. Operators must now demonstrate not just financial viability, but also a commitment to sustainable practices.
The drilling landscape in particular faces more complex challenges than ever before as it contends with fluctuating oil prices, more stringent environmental regulations, and increasingly complicated wells. While advances in exploration and drilling technologies have transformed the industry, unlocking previously inaccessible reserves and increasing production rates, the risk and technical difficulties associated with drilling operations have also escalated. As the sector strives to reduce its carbon footprint, advancements in drilling technologies are not only helping to minimize environmental impact, but also enabling more-efficient operations in increasingly complex well conditions.
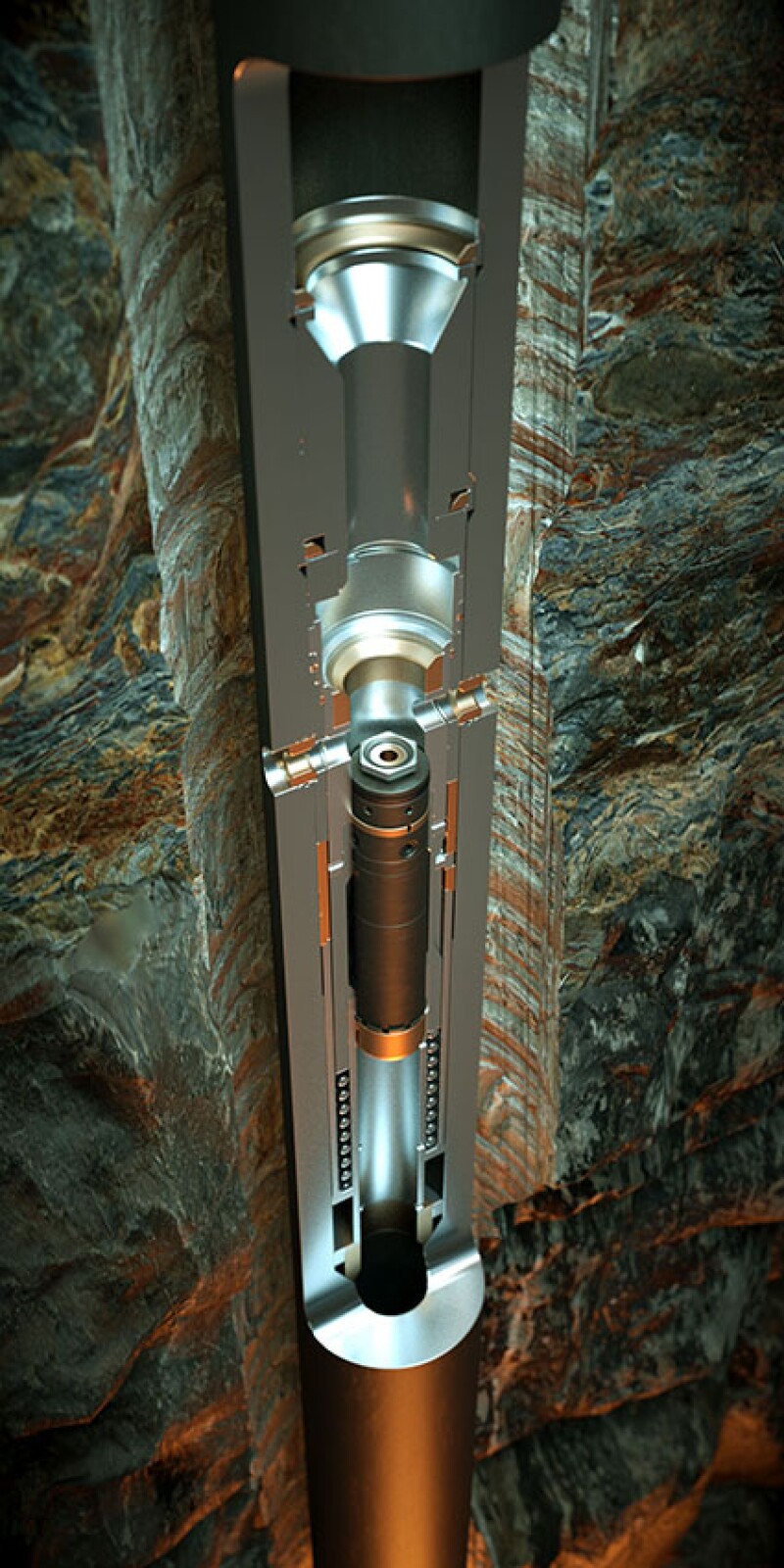
Understanding Stuck-Pipe Encounters
Stuck-pipe incidents are a frequent challenge during drilling operations, often costing operators millions in remediation. The remediation process is complex, frequently requiring days or even weeks of nonproductive time (NPT) and resources that may not be immediately available. Such incidents can arise from various factors, including differential sticking which occurs when pressure differences between the mud column and formation fluids cause the drillstring to stick against the wellbore wall, creating a "stuck spot" that immobilizes the pipe. Packoff is also a common issue where accumulated cuttings, debris, or other materials around the drillstring create a blockage.
In any situation, even if partial movement is possible, circulation and rotation are often not feasible. As each stuck-pipe scenario is unique, resolving it often necessitates a customized approach. Operators frequently find themselves constrained by a lack of available solutions, limiting their ability to respond effectively to a stuck‑pipe situation.
Jarring is a traditional stuck-pipe recovery method that uses mechanical or hydraulic tools to deliver sudden, high-impact forces to the drillstring to free the stuck pipe. Though this method can be effective, it is expensive and can take days or longer, which results in significant NPT to the project.
If the stuck pipe cannot be resolved, the last resort is to perform a disconnect, traditionally requiring mobilization of a wireline crew to deploy an explosive charge, known as a backoff or string shot. The explosives must be detonated above the freepoint to sever the string and can leave an unpredictable fishing profile for future operation. This technique can be time-consuming, costly, and introduces a new set of risks into the operation by deploying third-party crews and transporting hazardous materials to the rigsite.
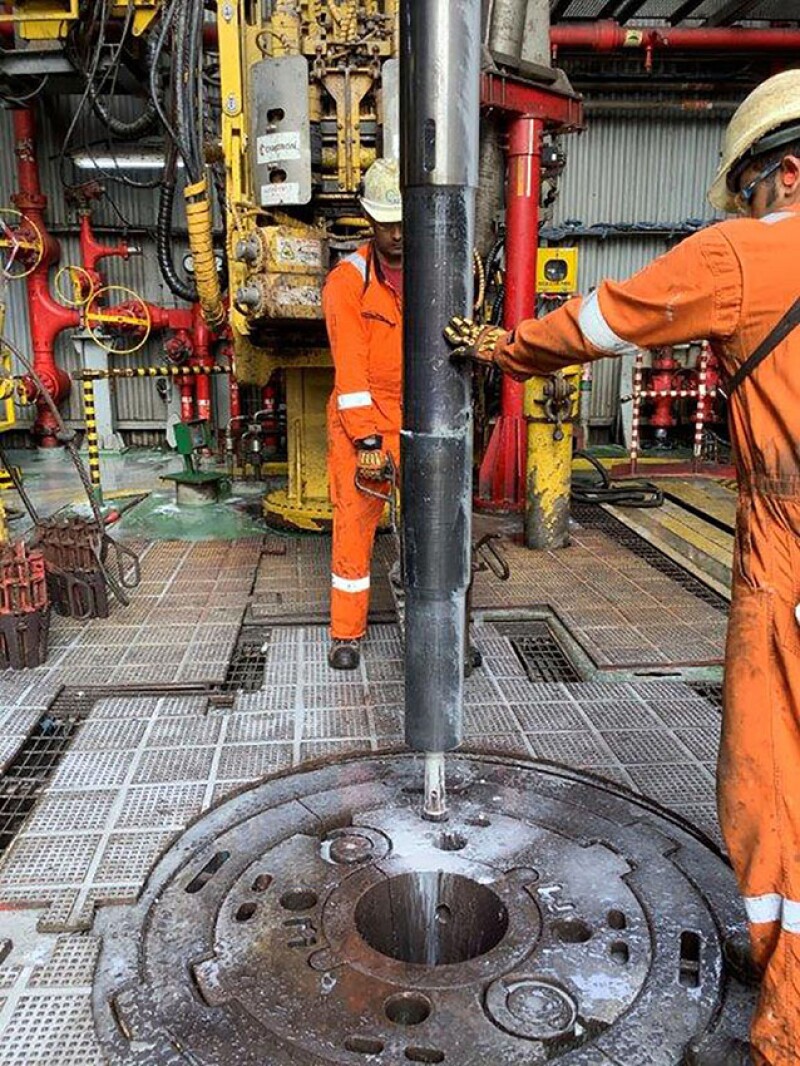
Innovative Circulation Technology Application
During a recent project offshore Azerbaijan, an operator’s drilling assembly became stuck when drilling an 8½×10¼-in. section of a well. Despite extensive jarring attempts, the operator was unable to move the string or circulate mud in the well. This meant that operations to sever the assembly to regain circulation were required.
Coretrax, an Expro company and global leader in oil and gas well integrity and production optimization, delivered its downhole circulation technology to remediate the issue. The company’s DAV MX and HyPR Holesaver had been deployed in the string as part of the customer’s wider risk assessment in case of a stuck-pipe incident. The solutions remain dormant in the string while still providing a contingency option if needed, providing an immediate remediation solution. The tools were selected as the narrow inner diameter of the drillstring components meant that traditional wireline-deployed tools were not suitable.
Ahead of deploying the tools, Coretrax provided standard operating procedure documents, which were tailored for the specific rig and well conditions, meaning no additional personnel were required on site to run the tools. This enabled the operator to start corrective operations immediately when the stuck pipe occurred.
Following considerable jarring activities, the operator achieved 50 gal/min of flow in the well. While this is a fraction of the circulation usually achieved, it was sufficient to enable activation of a 7-in. DAV MX circulation sub. Once activated, the sub allowed the operator to regain full circulation above the stuck point.
The versatile technology is largely immune to variations in angle, temperature, differential pressure, mud type, and mud weight and has a number of activation darts to support applications across drilling, completions, or plugging and abandonment. In this case, the tool was deployed with an emergency opening ball (EOB).
The EOB is used specifically for restricted circulation applications where it is not possible to pump or deploy darts to the DAV MX. The ball can be deployed in complete packoff or plugged‑string scenarios as long as the inclination of the well allows for it. The EOB was selected because the well angled at 68° which would allow the ball to gravitate down to the setting. After 2 hours, the ball successfully reached the circulating sub and full circulation was restored.
The operator then deployed the 2.405-in.-outer-diameter HyPR Holesaver with the fishing dart to sever the string. Unlike conventional methods, this tool requires no explosives or other high-energy sources to deliver significant safety and efficiency benefits. When activated, the flow of ordinary mud is redirected, creating a high-velocity radial jet of fluid to erode and cut pipe in just a few hours.
The fishing dart leaves clear and unrestricted access to the fish after it has cut the string free, enabling fishing of the bottomhole assembly (BHA) to commence almost immediately following cutting. Interference added to its tail also means that as the cut pipe is withdrawn it collects the fishing dart and carries it back to surface. After 30 minutes, the dart reached the HyPR sub and commenced with the hydraulic cut which was completed after approximately 10 hours of operation, and torque and overpull were applied to the string. Utilizing the technology, the team was able to successfully sever the stuck pipe, and the BHA above the severance point was successfully recovered to surface.
When compared to traditional wireline methods, the application of this technology saved an estimated 2 days of rig time which is generally required for techniques involving explosives while also eliminating the need for additional specialist personnel on board.
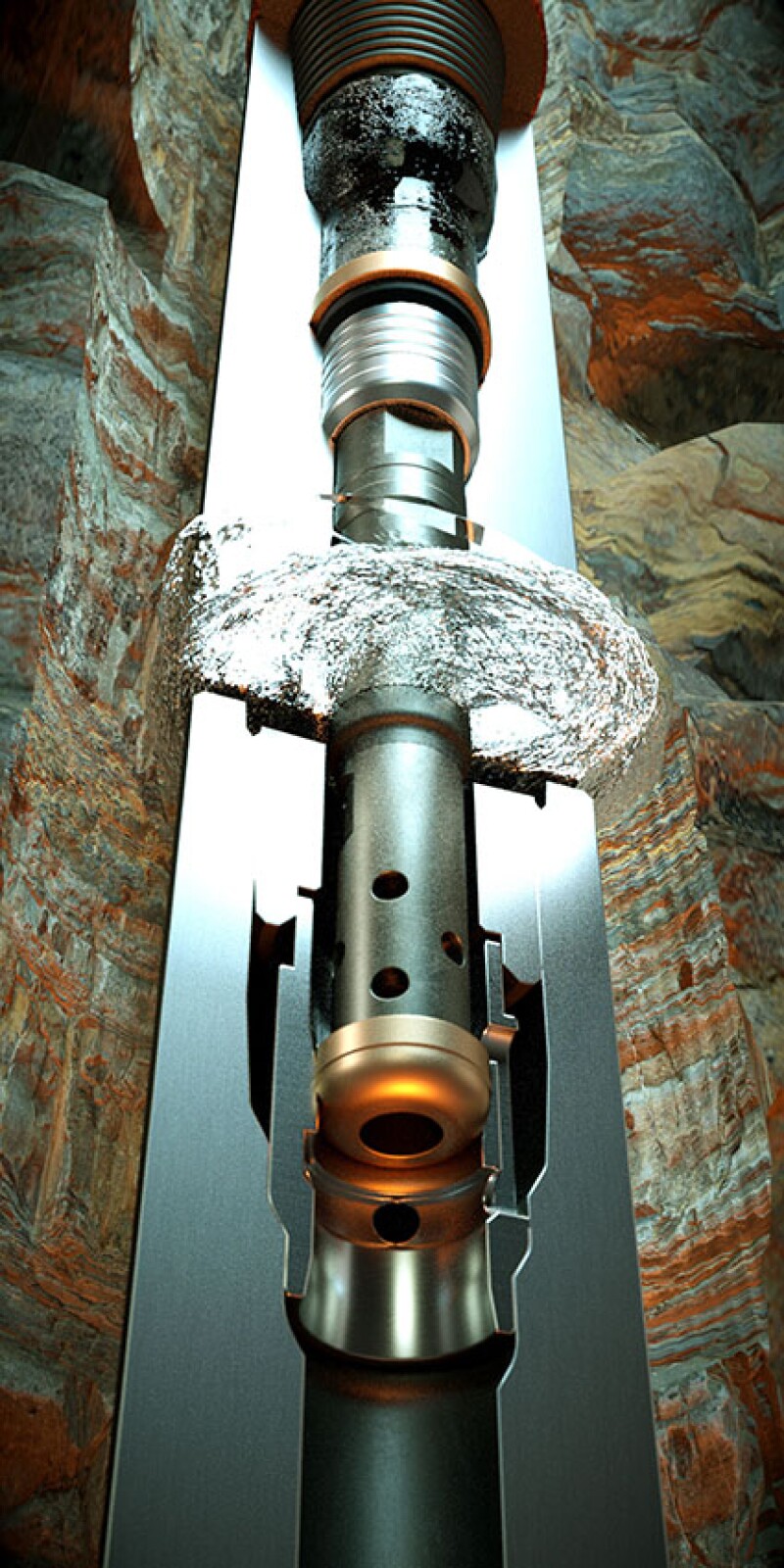
Driving Efficiencies in Drilling
As the energy transition continues to evolve, the oil and gas industry faces an intricate balancing act: meeting global energy demands while adhering to increasingly stringent environmental regulations. This challenge is particularly evident in the drilling sector, where the complexities and risks are higher, and the margin for error smaller. Innovative technology is essential in overcoming these hurdles to enable operators to address the most-challenging drilling situations safer, faster, and more efficiently.
The application of Coretrax’s circulation technology demonstrates the opportunities which can be garnered from having advanced contingency tools integrated into drilling operations. By allowing the operator to regain circulation and successfully sever the stuck pipe without the need for explosives or additional third-party crews, these technologies delivered significant time and cost savings while mitigating operational risks.
By embracing technological advancements, operators can not only optimize their current practices but also contribute to the broader goals of reducing the carbon footprint and supporting a sustainable energy future.
Reference
DNV Energy Transition Outlook, 2023

Operations coordinator Bartosz Lisiecki joined Coretrax in 2013 and is responsible for leading its Caspian and Sub-Saharan Africa operations. Based in Aberdeen, he has extensive operations and technical sales experience. He works closely with Coretrax customers to understand their challenges and ensure the right technology is delivered to support their needs.