Electrification of critical drilling and production components is sweeping through the oil field, both onshore and offshore. As technology catches up with the energy storage requirements for given applications, service companies are introducing new electric-powered equipment to replace kit that has been historically hydraulically controlled.
One of the latest additions to this movement has been SLB’s EWC electric well-control technologies. EWC technologies replace hydraulics and its complex network of hoses, valves, and actuators with a simplified electric power system that provides real-time data insights and a continuous supply of on-demand power to well-control components under any operating conditions.
Electrically driven pumps deliver shear pressures up to 5,000 psi and the system’s lithium‑ion 10C battery backup system provides immediate response and full functionality when rig power is unavailable.
SLB’s EWC technology enables drillers to instantly and precisely control and monitor blowout preventers (BOPs) onshore and offshore, leveraging industrial internet of things components along the system architecture to provide instant pressure readouts, without the need for conventional pressure gauges. This is designed to help operators make better-informed decisions about the operation and maintenance of the well‑control system—reducing nonproductive time and minimizing operating expenses.

JPT sat down with Matthew Givens, a pressure-control equipment domain expert and 24-year veteran of SLB, to get the low down on this new EWC system and what it means for the industry.
JPT: Traditionally, well pressure controls are manipulated hydraulically and remotely operated. What made SLB look at this system as a prime candidate for electrification?
MG: Traditional BOP systems are hydraulically operated remotely, regardless of whether the BOP system is on land, offshore, or a mile below the surface of the ocean. Over time, these systems have become more complex, with hydraulics accounting for more than 60% of system failures. Industry standards and increased well depths require more hydraulic accumulation, increasing the size and weight of the BOP control system. We needed a way to improve performance, reliability, and monitoring of the BOP system while reducing the system’s overall footprint. Our EWC electric well-control technologies are simplifying the system architecture, transitioning from maintenance-intensive ‘stored energy’ of hydraulics to reliable, energy-dense, electric power sources that use data-based decision-making for maintenance.
JPT: How long was the new system under development at SLB and were there any significant changes made from the earliest days to Serial #001?
MG: Electrification has been a goal since the early 2000s, but stored-energy solutions just weren’t ready for our application. In the last 5 years we have accelerated our EWC developments, notably introducing the EWC pressure on-demand BOP control system. Initially, we aimed for full electrification of the BOP system. However, operational challenges made it apparent that some situations might still require hydraulically actuated equipment. Our EWC pressure on-demand system provides the end user with improved edge-based diagnostics and significantly reduces the footprint by using batteries as stored energy for existing hydraulically actuated equipment.
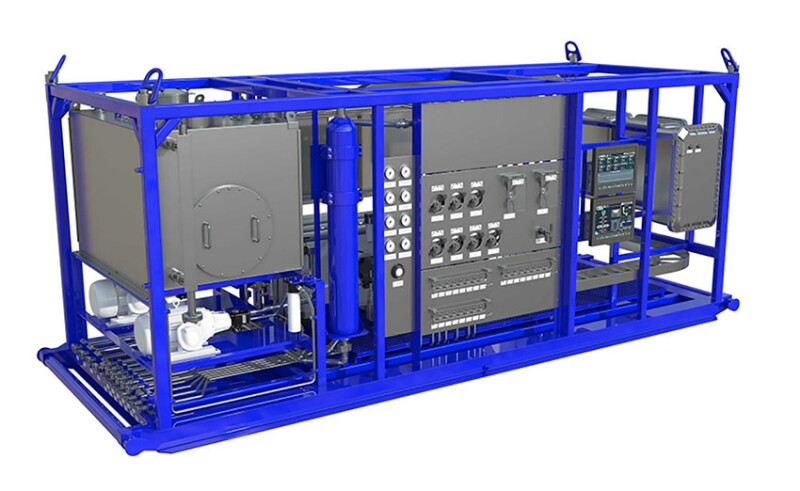
JPT: Can you talk about energy storage and the benefits of moving from fluid-based to battery-based?
MG: Traditional BOP systems use hydraulic accumulators (compressed gas over hydraulic fluid) to function the equipment. As fluid moves from the accumulator to the BOP, the gas chamber volume expands, causing a loss in system pressure and requiring more accumulators. So, you end up with a system that requires a lot of space on the rig or wellsite. Using batteries, we can provide more stored energy in about the space of a household refrigerator rather than the entire kitchen.
JPT: How does the new battery receive its power and how is that power transferred to well-control equipment, such as the BOP? Is the power system redundant?
MG: During project scoping, customers can choose how to deliver power to the compact, electric system. One option is to use the rig’s power system directly, with the battery serving as a secondary power source in the event of power dips or a rig blackout. The other option is to run the equipment directly from the battery, with the rig charging it when not in use. In both cases, the battery system is charged by the rig’s power system and includes redundancy in its architecture.
JPT: How does the electrification of the well‑control system impact the reaction time to a well-control event?
MG: Our EWC pressure on-demand system closes well-control equipment in the same or less time as traditional systems, meeting industry and regulatory requirements. For legacy BOPs, closing times match traditional accumulator-based system. Looking ahead, we plan to further enhance EWC technologies to deliver faster closing times and improved testing capabilities.
JPT: How much does the elimination of the hydraulic system impact maintenance on the well-control equipment?
MG: A reduction in maintenance time is one of the core benefits of EWC technologies. With the EWC pressure on-demand system, we are removing large banks of accumulators that require pre-charge adjustment and routine bladder maintenance.
Traditional systems rely on time-based maintenance. Our EWC technologies were designed with a focus on data from day 1 of the development. This includes edge-based diagnostics that log all functions, track the performance of each function, and make informed decisions on where maintenance is truly required.
JPT: Weight and size are important factors for consideration for most oilfield equipment, especially offshore. What benefit do electric well-control systems bring on that front?
MG: Our EWC technologies offer significant weight and footprint reductions. Removing accumulators greatly reduces the size of the overall BOP control system. The EWC pressure on-demand control system saves about 40% of the space for a largebore four-cavity BOP stack. We are actively planning for the future and working to optimize the weight and footprint of components currently under development.
JPT: What can you share about the FEED in the North Sea for a custom electric well-control BOP system?
MG: SLB launched the EWC pressure on-demand BOP control system at the IADC/SPE International Drilling Conference and Exhibition earlier this year. We are engaged with our customer in a front-end engineering and design (FEED) project to remove risks associated with the use of batteries in a well-control system on an active drilling and production facility in the North Sea.