Network simulation and optimization are a well-established methodology for the operator in increasing and sustaining production capacity. To improve existing workflows, the operator has enhanced its previous petroleum- and process-engineering-focused toolkit and has deployed globally a production system that uses digital twins from end to end for model-based surveillance and optimization. The cloud-based production-system digital twin connects sensor data from each asset’s data historian to an equipment-data model and first-principle steady-state simulation tools to create a reliable status of the well network and processing facilities.
Integrated Production-System Digital Twin
By applying cloud computing technology in the proposed system, all complex calculations are executed on the virtual machines and users can access the digital twin with a Web-based application. Comprised of two subsystems—well network and processing facilities—the end-to-end production-system digital twin began with a focus only on the subsurface well-production network.
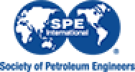