It’s not exactly what the doctor ordered, but expired medications may help treat one of the oil and gas industry’s costliest ailments—corrosion.
This is according to a new study from Saudi Aramco and its EXPEC Advanced Research Center in Dhahran that put several common medications through standard industry corrosion testing.
Published this week at ADIPEC in Abu Dhabi, SPE 216036 shows at least one of the unnamed drugs passed those tests with flying colors and is being investigated by the national oil company as a possible alternative to conventional corrosion inhibitors.
The proposal comes as the oil and gas industry faces an annual corrosion bill of more than $1.3 billion, according to figures from the National Association of Corrosion Engineers.
The particular focus of the Aramco study was to identify medications that could be deployed downhole during acid stimulation treatments, a common technique in Saudi Arabia for enhancing permeability within deep carbonate reservoirs.
However, the challenge lies in the corrosive nature of hydrochloric acid, commonly employed in these treatments, which poses a risk to the integrity of steel casing and tubing.
Authors from Aramco explain in their paper that while conventional corrosion inhibitors are effective, they are also expensive and highly toxic. By contrast, they add that expired medications pose a lower environmental risk since they break down faster and “due to being expired and not fit for human consumption, the cost is inherently low.”
And though they are by definition past their prime, separate studies cited show that most expired medications remain effective beyond their expiration dates.
The paper also points out that only a third of the drugs prescribed are believed to ever be taken. Much of the world's pharmaceuticals are simply thrown out or flushed down the toilet, which the authors argue raises even bigger environmental concerns than oilfield chemicals since such disposal practices are more likely to impact plant and animal life as a result of landfill leaching or water pollution via sewage systems.
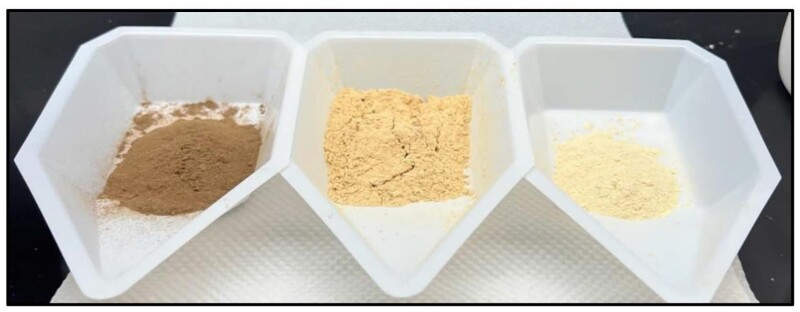
'Sample 7' Outperforms
The industry's desire to reduce its operational environmental footprint has driven the research of alternative corrosion inhibitors, many of which are plant-based. The Aramco researchers point out that these preceding studies showed successful plant-based candidates shared a common trait: they were made of alkaloid molecules.
Alkaloids are important since they adsorb to steel and also happen to be key components of many popular prescription drugs. Other drugs with various combinations of benzene, oxygen, and nitrogen are also capable of forming a thin protective film over metal.
While Aramco withheld the names of the drugs it tested, it gave examples of “high use” medications that demonstrate these attributes which include the painkiller morphine, the malaria drug quinine, and sildenafil—better known by its brand name Viagra.
The researchers ultimately selected nine medications that were collected from local pharmacies and hospitals and split them into three groups: herbal-based drugs, stimulants, and hormonal and immune system boosters for the third category.
After grinding the various pills down into a powder, they were mixed with the hydrochloric acid solution and the steel coupons were immersed for 6 hours at room temperature. The results showed that most of the medications demonstrated some level of corrosion inhibition while a few actually accelerated the damage.
In the end it was “Sample 7” from the third group that proved to be the clear standout, achieving a 99% corrosion inhibition efficiency rate at room temperature. This sample was selected for further testing at 150°F and maintained an inhibition rate better than 88%.
When the test was run at 200°F, the researchers said the control solution with no corrosion inhibitor “completely dissolved” after 6 hours. They did not report an inhibition rate of the winning sample for this third and final test but did share that the corrosion rate was nearly 30% below the industry’s maximum acceptable rate.
More Trials Needed
The Aramco research team plans to develop its medical-based inhibitor further using emulsified acid systems. Commonly used for high-temperature applications, emulsified acids are made using high-speed shear mixing to disperse acid droplets in either water or oil phases.
The Saudi oil company added that the research project's next steps also include assessing the risk of formation damage and precipitation by testing the medication’s compatibility with the different additives regularly included in its acid treatments.
Beyond that, the authors said more work is needed to isolate the exact molecules in the drug that are actively preventing corrosion with the intent of lowering costs by enabling smaller concentrations to be pumped downhole.
For Further Reading
SPE 216036 Expired Medications as Corrosion Inhibitors in the Oil and Gas Industry by T. Al Mubarak, F. Al Otaibi, M. Rafie, and A. Baiz, Saudi Aramco, EXPEC ARC.