In my 30 years in the energy industry, I don’t think I’ve seen anything capture our collective imaginations quite as much as digital has—not only in our industry, but also in our personal lives.
We’re surprised—and often amazed—by the way digital has changed our lives with smart phones, streaming, and online connections. We’ve seen the medical industry transform patient well-being and retail supply chains become vibrant when they’re underpinned by strong digital tools.
Irrespective of what’s happening elsewhere, however, we must admit that the oil field is still in the early days of its digital journey. There are many reasons for our slow start, of course, and the intention of this editorial is not to belabor them; instead, I want to provide a good dose of pragmatism as we consider what’s next for digital in the oil field.
At this juncture in our journey, it’s time to give serious thought to the expectation/reality gap, the cultural differences between the way we’ve always done things in the oil field and the way that digital is changing us, and the pain points that may trip us up unless we’re careful.
Data, Digital, and Expectations
In oil and gas operations, we collect enormous amounts of data—and we should expect that this data contains insights to help us streamline operations; orchestrate activities across multiple stakeholders; deliver more efficient, consistent outcomes; and maximize recovery.
The challenge is that data doesn’t mean much by itself. I agree with mathematician Clive Humby, who referred to data as the “new oil.” Oil must be refined into products—such as gasoline or plastics—to create value. The same is true of data which, when refined, can be used to understand reservoir characteristics, calculate nonproductive time, and myriad other things.
But unlike oil, data is a renewable resource—which enables it to create additional value on new and different levels. We can use refined data to make decisions, refine it again to make different decisions, or even go back to the original data and reprocess it to gain new insights. We can apply data to models repeatedly as they evolve, improving clarity around particular challenges, or finding new ways to solve problems.
But, in the end, data is still only data. And that’s why we’re so focused on digital.
Digital gives us the tools to do something with the data.
There’s an interesting construct here. Just as data can’t do much by itself, digital is simply a box of tools—data analytics, visualization, the internet of things (IoT), machine learning, digital twins, cloud capabilities, and more. The relationship between data and digital is necessarily symbiotic—and we will do well to remember this when we set expectations for what digital can and cannot do.
For illustration, let’s consider one of today’s most talked-about digital tools—artificial intelligence (AI)—and its role in our industry.
Many people in our industry view AI and its variants as a panacea for everything that ails us, no doubt in some part due to recent examples of how AI can diagnose illness, write term papers—the list goes on. In truth, these examples are among the easier problems for AI to solve; essentially, they’re lists of problems that fit AI’s strength in finding answers to complicated problems by drawing on a massive library of existing solutions.
But in our complex industry, things are not so simple. First, there is no massive library of existing solutions because we’ve historically kept our proprietary data locked in our respective companies. In addition, many energy companies have grown by acquisition—resulting in various types of data, structures, and repositories that aren’t easily integrated.
Second, the cyclical nature of the oil field doesn’t foster stability, so the interaction among critical elements—known and unknown—varies. Because of this complexity, practical challenges become much more difficult to solve, and our ability to draw meaningful correlations requires a new way of working. Solutions call for a collaborative, innovative partnership between the AI tool and the person who knows how to apply the tool’s results to build something meaningful and lasting for our industry.
Here, AI extends, but doesn’t replace, what people can do, so they can handle more complex tasks, or more tasks in the same amount of time.
We need to recognize that there is still much to learn about AI—and this is a critical point as we map out our digital journey. We need to have an honest understanding of the data, the tools, and the relationships with experts that are available to us, as well as what they can deliver.
Physical and Digital
When I started my career, the term “oilfield technology” almost always referred to designing, developing, and deploying physical tools. In this time- and labor-intensive process, operators and service companies identified a challenge, collaborated on the technology that would solve it, and prototyped and tested many times, both in technical centers and the field. We did so because the perceived cost of failure was simply too high.
It was also fairly common for individual companies to request “one-off” tweaks to standard solutions in order to address their specific needs. The result of this practice was that, while the problem may have been solved for the respective operator, the enhancement wasn’t applied to the wider industry (remember, we keep our data tight in this industry). Continuous improvement on an industry scale became a rare commodity.
Good or bad, we still work the same way today. All of us know it and expect it—because we’ve always done it this way.
But digital enters the oil field in a completely different way.
Digital allows us to turn the improvement loop—measure, analyze, act (to improve), and repeat—faster. IoT and digital hardware enable faster measurement, and cloud and advanced computing provide faster analysis. It’s the human element, in choosing when and how to act, that now determines how fast we can turn the loop. And each time we turn it, we can do it a bit better. To some in the oil field, though, that’s a bit like building the airplane while we’re flying it.
There’s also some evidence that the traditional oil field is a little mistrustful of the value of digital technology. Today, more than 40% of production management decisions are still made using spreadsheets; in fact, a 2022 study found that the most common piece of software used for managing field production is Microsoft Excel! And it's estimated that about 70% of producing wells aren't digitally connected at all.
Of course, some of this situation is driven by simple economics. Why would we, in the 750,000‑plus stripper wells that produce fewer than 5 B/D, outfit a rod pump with digital bells and whistles?
The answer is, we wouldn’t. And we won’t.
A Modest Proposal for the Journey Ahead
As we go forward, digital will go beyond efficiency and automation to help us reduce business uncertainty and costs, improve financial stability, and meet our decarbonization goals.
Clearly, we need to reevaluate our options as we take the next steps on our digital journey.
This isn’t to say that we haven’t been making important progress; in fact, we’ve been doing that in well construction for a while. Automated control systems drive better efficiency and safety of rig operations. Solutions that integrate surface and subsurface systems with automated processes manage everything from monitoring drilling fluids to automatically steering well paths to the most-productive zones. Remote drilling, which now comprises a majority of well construction activities, lowers carbon footprints while boosting operational consistency.
By the way, this growth in remote operations was accelerated by a global pandemic that challenged us to work differently. We need to be much more proactive in driving change, rather than having disruptive events do it for us.
These days, big opportunities lie in production, where the focus is on recovering the myriad barrels left unproduced from existing wells. Solutions for this challenge will need clear rationale for decision‑making, better data visualization, monitoring, alarms, and recommended actions—all masterfully orchestrated. To be successful, we’ll need to partner with companies outside our traditional network, bringing in experts in cloud services; data access, analysis, security; and AI—to name a few.
Of course, these are just the latest challenges for our industry. Throughout my career, we’ve met our challenges with a combination of skill, innovation, and commitment—and I’m certain that the digital journey won’t be any different.
But as I’ve outlined here, this particular journey is going to call on all of us to be pragmatic, patient, and collaborative in ways we haven’t been before. For now, I suggest that we turn our focus to
- Clarifying what we truly need from digital—and recognizing what it can and cannot reasonably deliver—while not giving up on the journey.
- Envisioning the path but understanding that the journey may change faster than we’re used to—so we’ll need to balance short-term outcomes with long-term benefits.
- Developing methods to scale up data for the mutual success of the industry while still maintaining data privacy around our most critical assets.
Now is the time for us to get ready for whatever happens next. It’s time to join forces, with our traditional networks and with new partners, with a common goal of meeting our net‑zero commitments, keeping our industry resilient, and making sure that we are always taking energy forward.
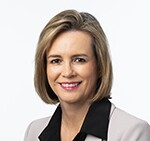
Maria Claudia Borras is executive vice president, Oilfield Services & Equipment (OFSE), at Baker Hughes, where she sets business and value-creation strategies for the 35,000-employee OFSE organization. A 30-year veteran of the oil and gas industry, she served in senior executive roles at GE Oil & Gas and Baker Hughes Inc. prior to her current position.
Borras serves on the boards of directors of Tyson Foods Inc. and Baker Petrolite Saudi Co. Ltd., and served on the ADNOC Drilling board of directors from 2019 to 2022. She is a member of the University of Houston Energy Advisory Board and the Energy Advisory Council of the Federal Reserve Bank of Dallas.
A native of Colombia, she holds a degree in petroleum engineering from the Universidad de América, Bogotá.