Editor’s note: Professionals in the oil and gas industry often receive questions about how industry operations affect public health, the environment, and the communities in which they operate. Of particular concern today is the impact of hydraulic fracturing on the environment. In this new column, JPT is inviting energy experts to put those questions and concerns about industry operations into perspective. Additional information about the oil and gas industry, how it affects society, and how to explain industry operations and practices to the general public is available on SPE’s Energy4me website at www.energy4me.org.
There are headlines every day that discuss the ethics and safety behind oil and gas operations, particularly hydraulic fracturing. According to the media, hydraulic fracturing can cause earthquakes, contaminated water, and even deformity in animals (if you believe the movie Promise Land). The truth behind the headlines is that hydraulic fracturing is a safe way to get natural gas out of the ground. What makes it a safe practice is solid well construction.
The evolution of oil and gas well construction has passed through many frontiers with each new foray into the next “unconventional” hydrocarbon resource generating the needed technology to keep pace with the immediate needs. In light of more than 4 million wells drilled in North America over the past 194 years, it is somewhat surprising that the industry has been successful so many times, and what we have done with lessons learned from the relatively few failures.
Wells are designed from the bottom to the top and from the inside outward, but they are drilled and constructed in exactly the opposite manner—often by practitioners with metrics different from the initial design principles. The fundamental objective that must shape every action along the way is that the final product of well construction must be a highly durable pressure vessel, albeit one that is composed of hundreds of threaded connections with a variety of seals and with a long coat of cement. Few other engineering disciplines operate in this highly cloaked area, in which the final engineering product, the downhole section of the well, cannot be conventionally seen, heard or touched, and produces a product that no one really wants to smell or taste.
The birth of the US gas industry was ushered in by William Hart’s shale gas well in Fredonia, New York, in 1821. He encountered flowing gas at 28 ft and, consistent with the technology of the time, cased it with wood and flowed shale gas through wood and early steel pipes to light the streets and buildings previously illuminated with lamps filled with whale oil.
Both Hart and Edwin Drake, with his 1859-era oil well, made use of one of the earliest hydrocarbon prospecting tools by locating their wells in areas of natural gas and oil surface seepage. Both wells hit natural flows of hydrocarbons in the same depth range as freshwater wells; it is a small wonder that fresh water, gas, and oil cohabitate the same strata today. Present on every continent, in every ocean, and above virtually every oil and gas producing area, natural seeps of oil and gas are indications of overfilling of some conventional reservoirs or natural geologic structure interruptions such as faults and natural fractures. The appearance of oil and gas seeps is evidence of oil generation potential below.
The early oil industry was undeniably a highly polluted place in time. Although well construction moved forward to steel casing, artificial lift pumps, and the first steel pipeline for oil transport in 1879, the first use of cement to seal and reinforce a well’s steel pipe was not seen until 1903. This fledgling cementing technology took a significant jump in 1915 with Almond Perkins’ two plug cement system, which Earl P. Halliburton purchased and pushed into worldwide use. Although the first widespread use of cement was undoubtedly a significant pollution control step, it is difficult to say whether that accomplishment was its main intent.
As other forms of technology moved forward, related advances quickly followed. Rotary drilling made possible dynamic pressure control feasible and blowout preventer technology gave rise to kick control; a technology combination that gradually replaced the gushers that came after oil strikes by cable tool drilling. The advances in cementing, drilling muds, pumps, corrosion control, and various stimulation mechanisms in the 1920s to 1940s ensured that the protection of hydrocarbon resources and the environment were not mutually exclusive. Significant regulation and enforcement on all phases of well construction in the oil and gas industry varied for years in different regions of the country, particularly in the early boom areas drilled in 1859 to the 1890s.
The first unified approach to effective resource conservation rules and practical enforcement came in 1935 with the establishment of the Interstate Oil and Gas Compact Commission (IOGCC), the oldest and largest interstate compact in the US that now represents governors of 30 member and eight associated states. The goal of the group is not only to conserve resources, but also to protect the public. Their survey work on idle and orphaned wells has been the driver for most of the well construction and abandonment rules that states have adapted to fit the needs of local geology (Thomas 2001).
The advances and some of the problems that drove the technology development are shown in Fig. 1.
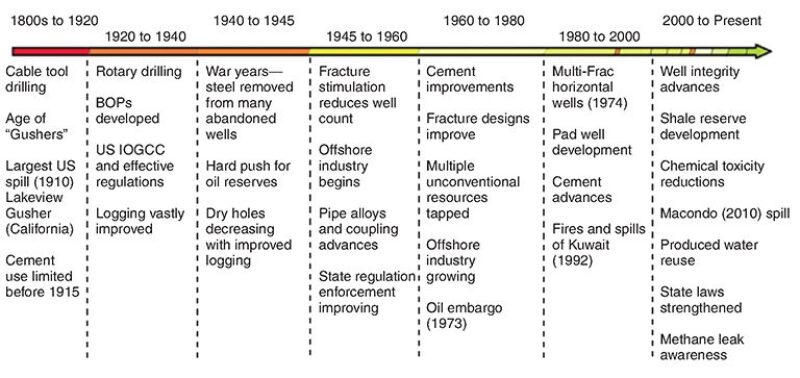
The fact that disastrous failures have driven the development and evolution of every field of technology, from medicine to space trips, should not be forgotten, although much of the public seems blissfully unaware of the trial and error journey that all technical disciples have taken.
From the study of forces of ruin (wear, corrosion, erosion, decomposition, weather, cyclic loads, etc.) that degrade all things natural and manmade, engineers describe behaviors that will destruct and design counteractions that will preserve or extend. An engineered structure, perhaps “perfect” at the time of construction, remains perfect only for a period of time. For example, we “risk” our lives with the use of skyscrapers, ships, airplanes, cars, and bridges, but still trust them to perform safely over an expected lifetime. They are designed to have an acceptable, although nonzero, risk level, as they age or when weather or load conditions change.
All these lessons must enter into both design and maintenance to reduce risk. In engineering design, multiple fail-safe principles and redundant systems that both warn of a potential problem and prevent an immediate one are used. For the oil and gas industry, redundant barriers in well design perform this purpose with great reliability.
From early failures to “old age” wear, time is portrayed as the enemy of any engineered structure, regardless of the engineering discipline. Time has four major influences in our operations as follows:
- Time affects the knowledge available at the time of well design and construction. This in turn must reflect a knowledge of materials available at the time for the construction, and the knowledge-based regulations that governed construction at that time. Failure rates of wells in a specific time period are artifacts of that period; they should not be reflective of wells designed and completed later. In well construction, the past 15 years have arguably brought more advances (e.g., new pipe alloys, better pipe joints, improved coatings, new cements, and subsurface diagnostics by seismic and logging delivering a better understanding of earth forces) than the previous 15 decades of oil and gas operations.
- Early time failures on new wells reflect both the quality of well construction and general early component failure (similar to items on a new car that must be repaired in the first few weeks of operation).
- Time reflects the potential for natural degradation of materials and changing earth stresses, both natural and manmade. The aging of structures is inescapable. The effect of aging, however, is highly geographically variable and controllable to a degree with maintenance. Structures in dry climates and soils often age slowly, while structures in wet areas, salt spray zones, acid soils, and tectonically active areas may be degraded and even destroyed in a few years. The oldest producing wells, for example, are more than a century old and many have not leaked, while high-pressure/high-temperature, thermal-cycled, and corrosive environment wells may have a well life of a decade or less before permanent plugging and isolation is required.
- Time has also recorded changes in energy source availability from the easily obtainable conventional reservoir petroleum resources to dependence on and development of resources that are much more difficult to access. This, in turn has created technology-driven approaches that have been difficult for some, both inside and outside the industry, to learn and accept.
Hydrocarbon-producing wells are a nested collection of pipe, cement, seals, and valves that form multiple barriers between produced well fluids and the outside environment. The concept of a well design ensured that if the inside barrier fails (e.g., a leak in tubing allows a sustained pressure in the annulus), the next barrier will prevent leakage outside of the well—essentially a barrier-within-a-barrier-within-a-barrier. A modern well design favors more barriers at the surface and across protected water zones and fewer barriers toward the bottom of the well, where the perforations and fractures are placed to encourage oil flow into the well. For a well to pollute, a leak path must form and extend from the inner hydrocarbon flow path to the outside environment.
A well’s barrier system begins during drilling as each depth is drilled and each casing string of the well is put in place. The completed well is a system of interactive barriers with the number of barrier sets matched to the needs of isolation.
Once the hole has been drilled to depth for a segment of the well and a casing string has been run to the bottom of the section, cement is pumped down the casing and up the annulus between the casing and the drilled hole. Once set, cement has similar compressive and tensile strengths to the rocks through which the hole has been drilled (in the range of 5,000 psi to 10,000 psi unconfined compressive strengths). Monitoring and evaluating cement quality, bonding, strength, and durability is a science itself with more than 1,000 publicly available, presented, and published technical articles and studies (www.OnePetro.org).
Although the 50-year-old cement bond log (CBL) is often touted as a quality check, the best indicator is often the cement pumping record, which should be available for every well. An experienced engineer or foreman can often forecast the quality of a cement isolation step from the cement pump chart’s recording of density, pump rate, pressure, and returns. This type of evaluation is immediately available, requires no added equipment or cost and is superior to most cement monitoring methods or tools on the market. The only proof of isolation continues to be a pressure test, commonly required for all surface strings in areas where fresh water or the surface must be protected.
There is no such thing as every inch of the hundreds or thousands of feet of cement in a well’s various annuli being perfect; and there is no need to have every bit perfect, only to have 100% isolation over a long enough annular interval to provide a seal to the fluids that must be isolated. A length of 25 ft of “perfect” cement will hold over 10,000‑psi pressure differential (King and King 2012).
References
King, G.E., and King, D.E. 2013. Environmental Risk Arising From Well-Construction Failure—Difference Between Barrier and Well Failure, and Estimates of Failure Frequency Across Common Well Types, Locations, and Well Age. SPE Prod & Oper 28 (4): 323–324. SPE 166142-PA.
Thomas, K.T. 2001. Produce or Plug? A Summary of Idle and Orphan Well Statistics and Regulatory Approaches. Presented at the SPE/EPA/DOE Exploration and Production Environmental Conference, San Antonio, Texas, 26–28 February. SPE-68695-MS.
George E. King, SPE, is Distinguished Engineering Advisor at Apache Corp. He is a registered professional engineer in multiple states with 42 years industry experience in completion, well construction, and well failure analysis. His work has focused on unconventional formations, sand control, perforating, fracturing, and well construction risk analysis. King earned a degree in chemistry from Oklahoma State University and in chemical engineering and petroleum engineering from the University of Tulsa, where he was an adjunct professor. He has written more than 60 technical papers and was awarded the 2004 SPE Production Operations Award and the 2012 Engineer of the Year award from the Houston Region of the Texas Society of Professional Engineers.