As industry buzzwords go, “automation” has spent its time in oilfield vernacular climbing the ranks of widely used terms. It now resides as one of the go-to designations for signs of advancement in any number of disciplines. Its use has been tied most frequently with drilling operations as contractors look to keep employees out of harm’s way via a robotic takeover of most motion-intensive jobs on the rig’s drill floor—basically anything that grips, clamps, or spins. More recently, the term has moved away from the drill floor and into other well construction operations allowing for things such as remote, real-time measurements without the need for boots on the ground.
For areas like west Texas and the Permian Basin shales, having the option for remote readouts and a component of automation that can allow for corrective actions should the need arise can go a long way in terms of safety and efficiency gains as well as better manpower application. Unsurprisingly, the area has become a solid testing ground for new, expanding efforts in automation.
With dreams of new drilling-fluid-monitoring automation, Eric van Oort, a professor at The University of Texas at Austin and former Shell research scientist, and select students came up with a new way to automatically measure mud parameters such as viscosity without the use of a traditional viscometer.
“The fact that we still use manual measurements, some of them now 90 years old, is quite puzzling in this day and age,” van Oort said. “The Marsh funnel, for instance, was introduced in the 1930s, and other mud tests go back to the 1950s and 1960s. These API measurements have served us well, but the question is, can you do something more now with modern measurement techniques and sensors? So, I started working on new ways of measuring the viscosity and density, and then later fluid loss and even solids and salinity in muds. That proved to be all very successful and promising.”
Construction of a mud skid to house the equipment and sensors needed to conduct these tests in real time was the next step in the evolution of van Oort’s concept. That initial skid was a cannibalized and reworked version of a unit that was employed on Shell’s Rig 1, which the supermajor built for its in-house rig-automation research based in Pennsylvania. This early mud skid, considered the prototype of van Oort’s design, was abandoned before it was properly tested.
“We generated quite a bit of IP [intellectual property], my students and I at UT,” he said. “The Shell skid hadn’t seen a significant amount of service, and it had some nice components that we could reuse. We took that skid apart and reconfigured it and put it out in the field with Pioneer Natural Resources for a set of field trials in the Permian. Those went well.”
The field trial results were shared in a paper presented at the 2019 Unconventional Resources Technology Conference (URTEC 2019-964). The paper concluded that the pipe viscometer employed by the skid allows for the characterization of additional rheology parameters, which cannot be obtained with Couette-type viscometers, such as the critical Reynolds number, characterizing the transition from laminar into turbulent flow, and the friction factor in the turbulent flow regime.
It also found that a typical measurement cycle for obtaining basic fluid parameters took only 5 minutes, allowing for more than 10 independent updates each hour, whereas density and water-cut values are provided continually. The increased frequency allowed timely flagging of the overtreatment of the fluid and discrepancies with fluid weight during the trial.
After the initial work at UT, van Oort started an industry-sponsored automation consortium at the university called RAPID (Rig Automation and Performance Improvement Drilling) and set his sights on finding a partner and commercializing the fluids-automation technology.
“Although everybody was excited about it and kept telling me that this was great work, nobody stepped up to the plate to help commercialize it,” recalled van Oort. “Of course, this is around 2015, right? The downturn is happening, and I could find no takers. For several years, I was talking to companies to try and get this off the ground, with little to show for it, unfortunately.”
Enter former Shell colleague and friend Munir Aldin, owner and president of MetaRock Laboratories. The company would collaborate with SPYDR (Scientific Partnering Yields Drilling Revolutions), a company the professor would form to lead the commercialization efforts for the mud skid, to bring a fresh prototype to life. With a willing client waiting in the wings and under SPYDR’s direction, MetaRock built the new unit.
“The way it works is that we connect directly to the active mud tank and are continuously taking samples and conducting measurements on them,” explained Mohamad El Zein, senior project engineer with MetaRock. “The outputs are pushed to the rig’s data-acquisition software for use at the rig site or remotely. This is all fully automated. It doesn’t require any intervention. Health monitoring of the skid is also done fully remotely. All the skid requires is some maintenance once a week. There’s no need for a lot of manpower.”
The SPYDR/MetaRock mud skid is a fully automated standalone unit that measures mud properties with full temperature control, allowing it to measure parameters such as viscosity variables, friction coefficient, pressurized density, and oil/water ratio. The skid is roughly 4×11×8 ft. It weighs about 5,000 pounds. This footprint is considerably smaller than the original Shell skid prototype.
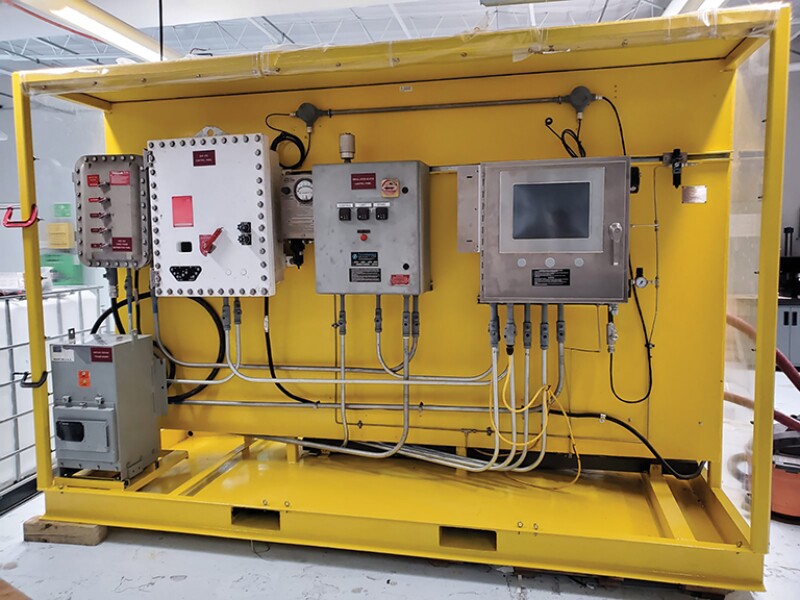
The willing client? Pioneer Natural Resources—the host of the field tests of that original, modified skid. The biggest draw of the mud skid to any would-be client may be the promise of less nonproductive downtime while drilling, a recurring bugaboo for operators since humans started drilling for hydrocarbons in the mid-1800s. As the old saying goes: Time equals money. And that is never truer than in the business of drilling oil and gas wells.
“This is not necessarily meant to replace mud engineers, but it allows for new ways for them to work,” explained van Oort. “You get a continuous readout of important properties like viscosity, density, oil/water ratios, and so on. You can use that information to avoid drilling-fluid related nonproductive time. If you let density slip, you could get into well control problems, borehole instability problems, or lost circulation problems. If the viscosity of the fluid climbs too high, you could get yourself into lost circulation situations with high ECDs (equivalent circulating density). We have just seen during the trial, that maintaining low-end rheology is particularly important for maintaining good horizontal hole cleaning and avoiding stuck-pipe incidents.”
Continuous monitoring also allows for optimization of fluid treatments, minimizing dilution and maximizing solids control. Today, solids control is still worked by the mud engineer at the rig site. The skid’s automation allows the mud engineer to step away from duties like a routine mud check and work on more value-added activities such as optimizing solids control.
“You could also think of a mud engineer in the future as a roaming asset, servicing a number of different rigs at the same play,” van Oort said.
One of the most important applications for the mud skid is its use in managed-pressure drilling (MPD) operations. All MPD control systems rely on hydraulics models. Today, they are fed the information from an infrequent manual mud check.
“Those control systems are important, and they need really accurate rheological data,” said van Oort. “You can now feed it real-time viscosity and density data, and we can measure properties at elevated pressures and temperatures. We can measure at standard API temperatures and at more realistic downhole temperatures.”
The automation of these processes also eliminates safety concerns that can arise when taking manual measurements, such as with high-pressure/high-temperature testing or working in a slippery environment for mud measurements and treatment.
The skid can be used effectively with both water-based and oil-based muds. The only thing that changes is the model used to interpret the data.
Beyond the current scope of the skid, SPYDR and MetaRock are keen to integrate additional sensors of interest, which can measure pH, conductivity, emulsion stability, solids, and salinity.
“We are using a combination of newer technologies with off-the-shelf instruments,” explained Aldin. “However, a key differentiating factor here is knowledge and experience. Eric came in with a wealth of knowledge and experience of how he wanted to do it, including the flow loop configuration, as well as the mathematics and modeling that is behind the parameter derivations, for example. At MetaRock, what we offer is engineering solutions, choosing and combining the right components. You combine all of this and deliver what is true innovation.”
The path to commercialization of the SPYDR/MetaRock mud skid has to come to terms with an industry that historically embraces the status quo, especially when it comes to technology. In a world of “if it ain’t broke, don’t fix it,” the contractors must win over new clients with their product and both parties hope the Pioneer field trials go a long way toward achieving that goal.
The contractors are high on the skid’s capabilities, but coy when it comes to talking about costs. While SPYDR wants to keep that information close to the chest for now, they have been told by would-be clients that quotes from larger services companies regarding comparable services have come in prohibitively expensive—many thousands of dollars per day.
“What we’ve done is build something that can be more competitive in terms of pricing, such as it can even be deployed on an unconventional land rig in the US and Canada,” van Oort said.
The current pilot with Pioneer began in February 2021 and is set to run for 5 months. Early word is that the client is happy with the performance.
“They understand the value of the information,” said Aldin. “They’re taking the data and comparing it to the manual measurements, and now we’re gaining trust and confidence.”
According to van Oort, SPYDR is talking to several American/Canadian operators and service companies about a potential future for the mud skid. There are also contacts in the Middle East and elsewhere, raising the hope for a fast deployment of the unit around the globe.
For Further Reading
URTEC 2019-964 Automated Surface Measurements of Drilling Fluid Properties: Field Application in the Permian Basin by S. Gul and E. van Oort, The University of Texas-Austin; C. Mullin, Pioneer Natural Resources; and D. Ladendorf, Royal Dutch Shell