As production declines over time, the injection of fluids is required to enhance oil recovery and/or maintain the reservoir pressure. Whether applied at field startup or as a secondary recovery technique, waterflooding can boost oil recovery from less than 30% to 30–50%.
The common problems associated with waterflooding include loss of injectivity, premature injector failure, and injection conformance. This can also lead to issues around insufficient voidage replacement, which can result in lower reservoir pressure and the production of fluid with a higher gas/oil ratio. In total field recovery, this ultimately means lower production and oil left untapped in the well. To remediate the issue of conformance, costly and often complex interventions and re-drills were traditionally used to restore water-injection capability. Also, passive outflow-control devices have been used successfully to somewhat improve the fluid conformance from injection wells. However, they may fail in reservoirs with complex/dynamic properties including propagating/dilating fractures.
Advanced Wells in Injection Wells
There are a number of considerations when planning a water-injection completion, particularly around both the rock and fluid properties, as well as the credible risks that could occur, namely:
- Uneven displacement of hydrocarbon
- Fracture growth short-circuiting injectant-proximal wells
- Fracture growth breaching caprock/basement seal
- Crossflow, plugging, and solids fill
Advanced completion options include deploying passive flow-control devices. For example, inflow-control devices (ICDs) are unable to react to dynamic changes in reservoir/well properties. This often requires production-logging-tool (PLT) logs, distributed temperature sensors, and/or tracers to be run and, if available, to apply the sleeve option. Alternatively, active (intelligent) completions, such as inflow-control valves, can be used, but they tend to be expensive and complicated and are limited to the number of zones. This technique also requires frequent analysis of data from the well to perform such actions.
Tendeka, a global specialist in advanced completions, production solutions, and sand control, has developed FloFuse, a new and exclusively autonomous rate-limiting outflow-control device (AOCD) (Fig. 1).
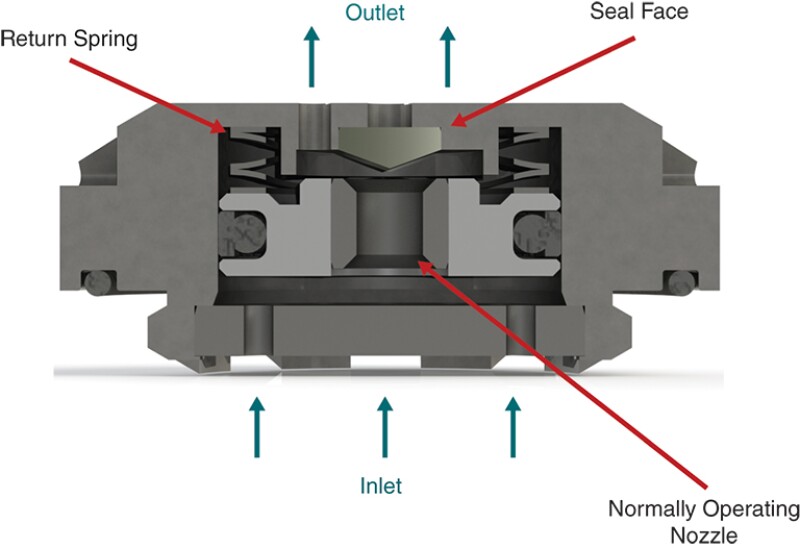
Using the analogy and inspiration of a home fuse box, which contains many individual fuses to control various parts of a building, the AOCD can control the excessive rate that passes through a specific section of a well, causing tripping once the threshold is reached. By almost shutting, i.e., significantly choking, the injection fluid into the fractures crossing the well, the AOCD autonomously prevents growth and excessive fluid injection into the thief/fracture zones and maintains a balanced or prescribed injection distribution.
Like other flow-control valves, this device should be installed in several compartments in the injection well. Initially, devices operate as normal passive outflow control, but if the injected flow rate through the valve exceeds a designed limit, the device will automatically shut off.
This allows the denied fluid to that specific compartment to be distributed among the neighboring compartments.
Under normal operating conditions, injection outflow passes through the “normally operating nozzle” into the housing and through the screen, where sand control is required.
If the pressure drop in the formation decreases as a result of increased injectivity due to a fracture or high-permeability streak, the injection rate into that compartment will increase. The resultant increased pressure drop through the nozzle acts against the return spring until the flow area between the seal face and the nozzle becomes restricted and the valve triggers to the fused position, restricting the outflow into that compartment. In the fused position, some bypass is maintained to enable the valve to re-open should the conditions allow.
This valve is fully reversible and will reset if the rate becomes sufficiently distributed again. The target normal operating rates and degree of outflow control and trigger rates can be varied by application.
The performance enables the operators to minimize the impacts of thief zones on the injected fluid conformance and to react to a dynamic change in reservoir properties, specifically the growth of fractures/faults. By enhancing the sweep efficiency and pressure support, the device will mitigate reservoir uncertainties as it acts autonomously against any unpredicted circumstances like a fuse box in buildings.
Importantly, this technology removes the need and cost of running a PLT and the complex well interventions required to open/close the integrated sliding sleeves in traditional completions as it achieves the optimized well performance autonomously.
The results of several simulation studies, supported with several field application results, show that the AOCD reduces the injection cost and improves field net production value (NPV) and the reliability of injection-well systems. It also lowers the risk of poor conformance due to the development of complex fracture structures and any sort of exacerbated outflow balance, thereby minimizing the risk of out-of-formation fracturing. As the injection conformance control could be an issue in most CO2 injection wells, this could also be applied to losing containment control above the zones. Moreover, the AOCD can also be used as a mechanical diverter to manage and optimize matrix stimulations during well operations for improved injectivity.
AOCD Performance
To validate performance, full-scale laboratory tests on realistic injection conditions were carried out for a single bi-stable valve. Several single-phase injection experiments, including water and polymer, were also performed to define the characteristics of the valve using different sizes—2.2 mm, 3 mm, and 4.5 mm.
The characteristics are described by the differential pressure across the valve vs. flow rate through the device. After reaching a certain flow rate, the valve shuts off the water flow. The trigger rate outlined below is dependent on the nozzle size and spring constant.
- 2.2 mm valve triggers at (85 BWPD or 105 psi)
- 3 mm valve triggers at (135 BWPD or 135 psi)
- 4.5 mm valve triggers at (280 BWPD or 185 psi)
The flow performance of the bi-stable valve has been proven while the behavior of the flow can be simulated in the reservoir/near-wellbore model. The flow rate of the trigger point is an important parameter to calculate the number of devices in a completion. If a minimum flow rate is needed to be injected into the thief zone after AOCD shutoff, the AOCD can be paired with a bypass ICD to deliver the desired outflow. Pressure relief is accomplished by stopping injection and by the inclusion of one or more ICDs in the same zone as the device(s) in order to equalize pressure.
Example 1—Injection Rate of 8,000 BWPD
Using AOCDs in a vertical injection valve with the four perforations, the objective was to balance the outflow while minimizing injection through the thief zones, targeting an injection rate of 8,000 BWPD.
Appreciating that the outflow profile would change at different stages of the lifetime of the well, it was anticipated that even with the flow-control devices, the dispersal of the perforation may create a thief zone in the future. More than half of the water was expected to go through that zone when the fracture developed. An AOCD was designed to mitigate this likely occurrence, and several devices with set choke rates were distributed among the other zones. It was targeted that the maximum flow rate going through a zone is 3,500 STB/D. The AOCDs then trip and the injection going into that specific zone reduces significantly, almost by more than half. This helps prevent the excessive injection rate of the fluid into the thief zone and keeps a balanced outflow (Fig. 2).
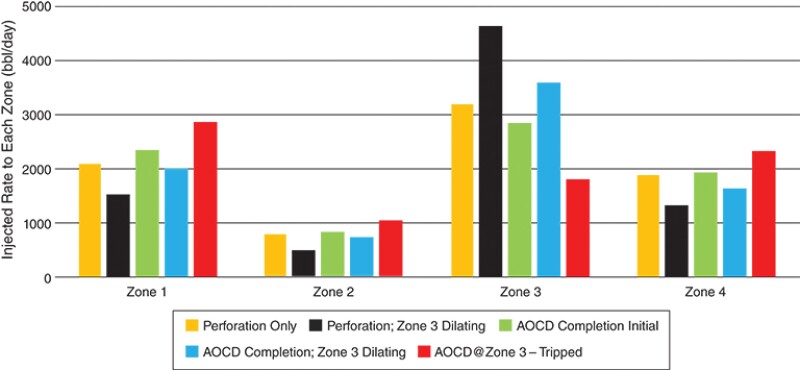
Example 2—Injection Rate of 2,000 Sm3/D
Another example is a well in the Gulf of Mexico with five completion zones. The well itself was passing through four layers. It was expected that the top layer would take the majority of the fluid as this was the environment for which initiation and growth of thermal fractures were expected. The objective here was to control the impacts of thermal fractures. A simulation study showed that the AOCD completion could supersede other options due to the AOCDs’ managed outflux to the well, as less water would be injected while producing more oil from producers. In terms of NPV, it shows that the devices would also bring much better output compared to alternative technologies, as shown in Fig. 3.
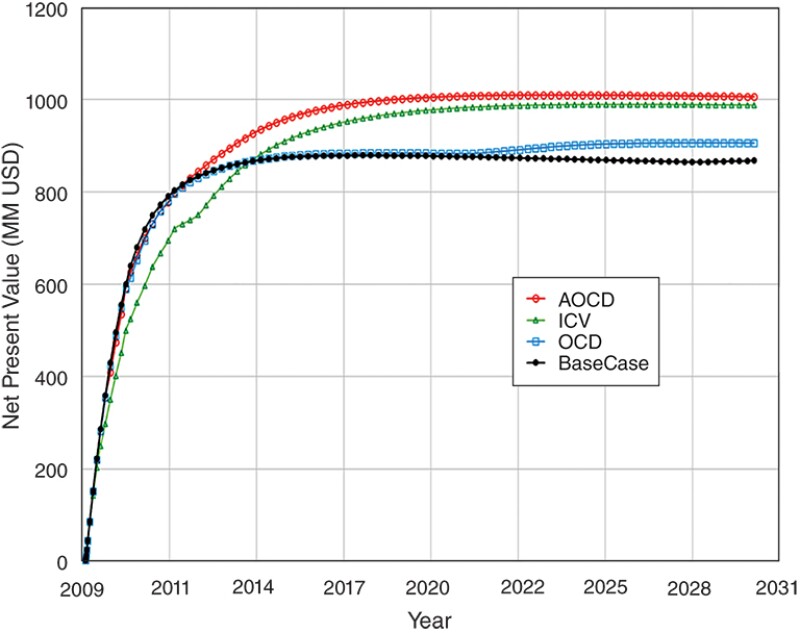
AOCD and Uncertainty Management
It should be recognized that the reservoir and nearby well properties may change significantly over time, especially in injection wells. Such a dynamic system requires autonomous devices to act accordingly against unprecedented conditions, as passive ICDs are unable to react. The design of advanced well completions is normally based on log data such as permeability; this may result in uncertainty in the well performance. In essence, using an autonomous device would mitigate this risk because the valves are active and can autonomously react to changes in the properties of the nearby wells and/or the reservoir performance.
AOCDs can choke excessive injectant into thief zones, dilating or propagating fractures. They can be used in water, polymer, water-alternating gas, and CO2 operations. They could be also deployed in a horizontal well or in a vertical well. The valves reduce the risk of poor conformance, and with the lower imposed initial pressure compared to the conventional ICDs, the AOCDs could manage the water injection much more efficiently to achieve the desired sweep and ultimate recovery.
References
SPE 93564 Designing Effective Sand Control Systems to Overcome Problems in Water Injection Well by H. Sadrpanah, Schlumberger; R.D. Allam, BP; A. Acock, Schlumberger et al.
SPE 197612 A Game Changer for Injection Wells Outflow Control Devices to Efficiently Control the Injection Fluid Conformance by I. Mohd Ismail, M. Konopczynski, and M. Moradi, Tendeka.
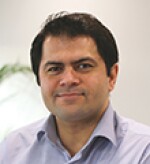
Mojtaba Moradi is a reservoir engineer with Tendeka. He has more than 10 years’ experience in the oil industry and has published more than 25 technical papers. He has extensive experience in well/field performance optimization with a focus on advanced well completions.