This paper shares the engineering approach used to determine where and when sand control was needed in offshore Malaysia on the basis of geomechanical sand-free critical-drawdown-pressure (CDP) evaluation for the selected well type, configuration, and completion. The decision to implement a proper method of sand control can be made by comparing the CDP with the minimum drawdown pressure (MDP) required to meet the target production rate. Sand-control-method selection was based not only on the sand-particle-size distribution, well life, and mode of well production but also on maximizing oil and gas recovery per well.
Introduction
The challenge in Malaysia was to design and implement a sand-control completion that could maximize well productivity with a stable wellbore under perceivable changing offshore production conditions implemented at the lowest cost.
The objectives of setting up the sand-control benchmark for the Malaysian field were
- To reduce the sand-control completion costs by greater than 50%
- To drive a sand-control well-design culture change for developing cost-effective well completions for sandstone reservoirs
- To determine selectively where, when, and what sand control is needed in the developing reservoirs
- To enable well-placement and reservoir-penetration-trajectory design to maximize sand-free‑production drawdown pressure
- To optimize the use of expensive sand-control methods
- To estimate sand critical erosion pressure drawdown
Fig. 1 shows a carefully developed workflow.
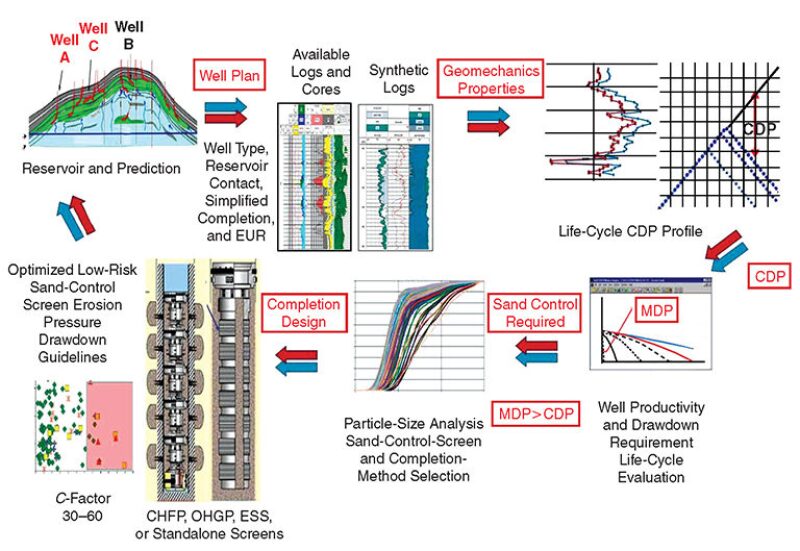
Maximizing CDP
For a well designed to penetrate target reservoir sand, the sand-free CDP should be evaluated for the entire potential producing interval following the designed reservoir-penetration trajectory. Because the geomechanical properties change with pore pressure, this evaluation must be conducted for the whole life cycle.
For cased-hole completion, perforation orientation and phase angle can be optimized to increase the CDP. More effectively, CDP can also be increased by increasing well inclination for the same sand.
In some sands, the CDP can be affected strongly by water production. After water breakthrough, the rock strength and friction angle that affect sand consolidation and stability of sand structure at and near the wellbore may be dramatically reduced. Moreover, when formation sands contain significantly high amounts of water-reactive shale, the whole wellbore can collapse. CDP can then become very small, or even zero. High pressure drawdown could cause wellbore and even completion mechanical failure.
MDP
The process of predicting the MDP should start with the prediction of well performance, which can be conducted analytically or by reservoir-model-simulation studies. Fluid rates, pressure, and key production ratios such as gas/oil ratio (GOR) and water/oil ratio (WOR) or water cut as a function of time should be predicted first.
Comparison of the MDP profile and the CDP profile should help determine the requirement for a sand-control completion by an obvious criterion of MDP>CDP. With all planned wells evaluated by this method, where and when the sand control is needed can then be determined technically for the developing reservoirs. Here is a summary of the workflow:
- Determine single or multiple reservoir-penetration strategy.
- Single-reservoir-target well on the basis of estimated-ultimate-recovery (EUR) gain per well optimization.
- Commingled well for multiple stacked reservoirs on the basis of total EUR gain per well optimization.
- Optimize sand-free maximum drawdown pressure (CDP).
- Optimize CDP for each reservoir-penetration interval.
- Optimize single or commingled well by maximizing CDP life-cycle profile.
- Determine MDP.
- Determine MDP per well to match the predicted fluid rates, GOR, and WOR.
- Generate MDP life-cycle profile.
- Sand-control completion criterion: MDP>CDP.
- Determine where and when sand control is required in the developing reservoirs.
Selection of Sand-Control Methods
After deciding that subsurface sand control is required to ensure wellbore sand stability and to ensure that the predicted EUR can be achieved by the wells, the nature and properties of the sand should be revisited and the particle-size distributions of sands in the producing intervals should be measured by either sieve or laser analysis. A plot of cumulative percent of particles vs. the particle size expressed in microns is used to inspect the nature of sand sorting and content of fines, silts, and clays.
In essence, when the sands are well sorted and uniform, a standalone screen with laboratory-tested screen design should be applicable for downhole sand control. When the sand sorting is good and the fines content is significant but relatively low, a more elaborate woven-mesh screen design can be used without gravel pack. When the sands are poorly sorted and nonuniform with a significant amount of fines, the selection of sand-control methods should focus on either gravel-pack or gravel-packed/fractured completions.
Fines Control With Gravel Packing
Gravel can be packed inside the cased or openhole annulus between the formation and sand-control screen. The methods are referred to as cased-hole gravel pack (CHGP) and openhole gravel pack (OHGP). Gravel can also be packed into the reservoir formation by a controlled hydraulic-fracture pack (CHFP). Completion implementation methods and technologies of these sand-control completions have been improved significantly. In comparison, CHFP has progressively become the standard strategy for sand control because of its ability and reliability to control more fines and yield better production performance.
The selection of these methods should be based on the following long-term production-enhancement life-cycle considerations:
- Optimizing of well productivity
- Minimizing of well mechanical skin
- Optimizing drawdown pressure
- Erosion risk
Maximizing Well Productivity
In Malaysia, all reservoirs are offshore and can be structurally and dynamically classified into three main types: thin oil rim, compartmentalized, and multiple stacked thin-bed reservoirs. Adding to their complexity, sands in those thin-oil-rim and compartmentalized reservoirs can also be multiple stacked.
For each sand, the optimum drainage and injection points should be determined on the basis of mobile hydrocarbon density, rock quality and productivity, flow connectivity, pressure distribution, and the potential of producing excessive water and gas, in addition to borehole and sanding stability. Connecting the selected drainage points from stacked target sands will constitute the basis of well reservoir-contact trajectory. Although, for a single sand, the well productivity may not significantly increase with increasing well-deviation angle, if the vertical- to horizontal-permeability ratio is very low, coupling more sands will certainly increase the well productivity index (PI) and recoverable-reserves EUR per well and, more importantly, increase the CDP of the well.
Minimizing Well Mechanical Skin
Theoretically, CHFP with a carefully designed fracture, avoiding fracturing into adjacent weak zones and implemented successfully by achieving a good control of fracturing propagation as shown by having a good tip screenout, should have the lowest mechanical skin when compared with other sand-control methods such as OHGP and CHGP.
Among all gravel-placement sand-control methods, CHGP has been recognized as the completion that potentially yields the highest mechanical-skin values. When reservoir permeability is relatively low, CHFP can even have a negative total skin, also reflecting good reservoir stimulation, in addition to having the benefit of a more reliable and efficient sand- and fines-control completion.
However, at high well-deviation angles, fractures may not effectively connect with the wellbore. Reservoir fluid then can flow either through the fracture or directly into the adjacent gravel-pack (CHGP) intervals. The fraction of fluid flow through the fracture dramatically reduces with increasing well-deviation angle. This induces high mechanical skin, and the skin could increase further with time.
Skin decrease with time may not be entirely from higher influx because of dominated flow into the CHGP intervals. Formation and fracture compaction in some overpressured reservoirs could result in decreasing porosity and permeability that could show increasing skin. Fines migration, particularly at higher drawdown, could also result in exhibiting a similar trend, especially at higher well-deviation angles. The key parameter is the inflow velocity, which must be kept low.
Critical Erosion Drawdown Pressure (CEDP)
It has been suggested that the method of sand-control-completion potential erosion evaluation be based on analyzing the historical data correlating the drawdown pressure with the C-factor. The C‑factor was defined as the product of fluid velocity at the perforations (CHFP) or at the screens (OHGP) and the square root of downhole-fluid density. In general, C-factor can be regarded as the square root of the kinetic energy of fluids.
Because the high fluid velocity can cause high fines movement in the reservoir, which could cause high sand and fines production and increase the downhole-fluid-mix density, it is the governing factor. Then, the only way to minimize this erosion potential is to reduce the drawdown pressure. Therefore, there should be a CEDP below which erosion potential can be kept low. Velocity can be kept low to produce the desired fluid rate when the well PI is high.
Sand-Control Well Design for a Deepwater Reservoir
A Malaysian deepwater field has been producing enormous amounts of sand at the surface because of a series of well failures from expandable-sand-screen (ESS) completion wells (Fig. 2). All sands contain fines larger than 15%, as determined by laser particle-size analysis. According to the suggested sand-control-method selection guidelines, the control should be either CHFP or OHGP with a good screen design by laboratory flow tests rather than a screen-alone method such as ESS.
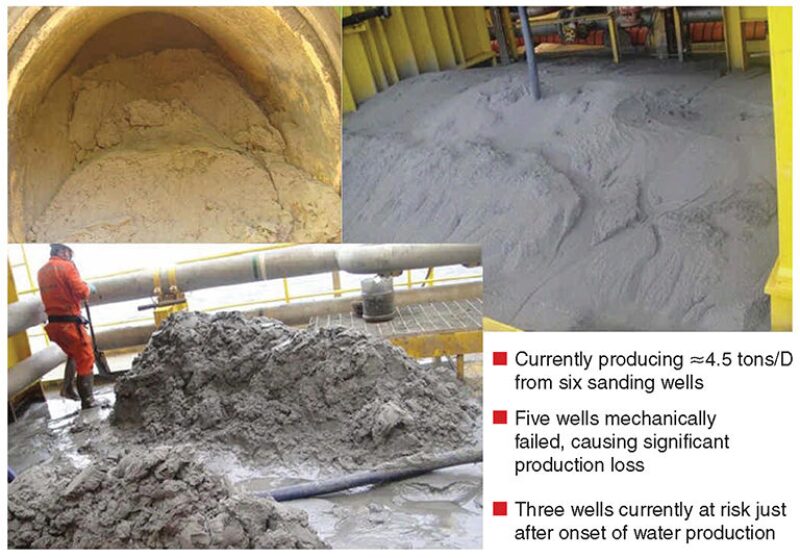
To achieve the targets of field development from multiple sands in this reservoir, wells should penetrate and contact more sands with high-deviation-angle trajectories.
For the same completion cost, OHGP can produce more because of commingled production from many sands. To minimize the risk of fracturing into the adjacent weak sands, the fracture half-length for CHFP could not be optimized to gain significant PI increase for the target high-permeability sand. More than 13 wells in this field have recently been drilled and completed to reverse the dramatic production decline from the failed sand-control wells. For high-deviation-angle-trajectory wells, it seems the OHGP completion was more appropriate, meeting the goal of high PI and EUR at the lowest cost.
This article, written by Editorial Manager Adam Wilson, contains highlights of paper IPTC 16449, “Production-Integrated Sand-Control Benchmark for Field Development,” by Keng Seng Chan, SPE, Danny Chong, SPE, Rahim Masoudi, SPE, Mohamad B. Othman, SPE, and Norbashinatun Salmi Bt M. Nordin, Petronas, prepared for the 2013 International Petroleum Technology Conference, Beijing, 26–28 March. The paper has not been peer reviewed. Copyright 2013 International Petroleum Technology Conference. Reproduced by permission.