As bottomhole-assembly and drill-bit design and operation have embraced new technologies such as artificial intelligence, new materials and manufacturing techniques, and improved design software, the industry continues to research methods of optimizing delivery and understanding of already globally used technologies. It is this approach that has long allowed service companies, operators, and drilling contractors alike to improve drilling performance, as highlighted in the papers summarized here.
In the first of these papers, paper SPE 210723, finite element fatigue simulation has been used to minimize the risk of twistoffs in jars, something that many of us in the drilling community have experienced. This paper can help us reduce those unplanned events and lost time.
Many rigs worldwide have moved to using autodriller-type control systems, and, in many cases, these systems have shown improved performance. In the second paper, paper SPE 214997, the optimization of these systems is discussed in the review and modification of driller procedures to minimize damage to bottomhole assemblies and the drill bit during drilling.
Finally, while many papers have discussed high-frequency torsional oscillations and their effect on the bottomhole assembly and drill bit from an operational or a theoretical view point, the final paper, paper SPE 212566, discusses full-scale laboratory experiments to qualify the drill bit’s influence on this effect.
All three of these papers highlight increased understanding in the operation and evolution of existing technologies to improve drilling delivery. In the evolving world of drilling where the final objectives and uses of wells are changing—whether for repurposing; carbon capture, use, and storage; or geothermal uses—these approaches to optimizing existing technologies in conjunction with the introduction of new technologies can help oilfield drilling teams pivot into this adjacent energy environment to deliver successful wells.
This Month’s Technical Papers
Improvement Plan Using Fatigue Analysis Minimizes Jar Twistoff
Autodrillers, Rig-Control Systems, Driller Procedures Reduce BHA Failures
Laboratory Experiments Qualify Bit Influence on High-Frequency Torsional Oscillations
Recommended Additional Reading
SPE 212438 Building a System To Solve the Challenges of Drilling Hot Hard Rock for Geothermal and Oil and Gas by Anthony Pink, NOV, et al.
SPE 212559 Machine Learning-Based Drilling System Recommender: Toward Optimal BHA and Fluid-Technology Selection by Gregory Skoff, SLB, et al.
SPE 212109 World’s First Application of Steel Body Bit in High-Chloride Formation With Water-Based Mud by Bekbolat Uandykov, Zhigermunaiservice, et al.
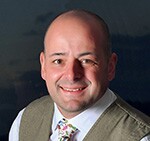
Martin Hayes, SPE, is a senior drilling engineer for Dragon Oil. He holds a BS degree in applied geology from the University of Leicester and is recognized as a Chartered Engineer and Chartered Petroleum Engineer by the Energy Institute. He has spent more than 25 years in the drilling industry, working with in drilling design, operations, and training for companies including Schlumberger, Black Reiver Consulting, Stanfield Consultants, Merlin ERD, Tullow Oil, WellSafe Solutions, Bedrock Drilling, and Gulf Keystone. Hayes is a member of the JPT Editorial Review Board.