Jar twistoff is a well-known service quality issue for some applications, especially in relatively large borehole sizes such as 22 and 16 in. The jar is one of the weakest points in the drillstring because of moving parts, which include complex shapes, resulting in stress concentration. The complete paper presents results of a study focusing on placing the jar in the bottomhole assembly (BHA) to reduce bending moments and bending stresses on the jar connections. As a result, the risk of twistoffs during drilling is minimized, while the effectiveness of the jar is maintained if a stuck event occurs.
Introduction
Jars traditionally are placed between drill collars in the applications described in this study.
×
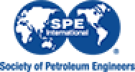
Continue Reading with SPE Membership
SPE Members: Please sign in at the top of the page for access to this member-exclusive content. If you are not a member and you find JPT content valuable, we encourage you to become a part of the SPE member community to gain full access.