Something that struck Brian Price as odd when he started selling chemicals to shale producers a few years ago was how few of them were thinking about whether the fracturing additives they pumped might cause trouble downhole.
The man who is now vice president of technology and strategic optimism at Rockwater Energy Solutions—yes, it is optimism—had spent years working offshore. Engineers working in the Gulf of Mexico worried about the possible impact of chemicals pumped into highly permeable sandstone reservoirs made up of minerals such as quartz and feldspar. Both are fairly inert compared to the highly reactive mix in shale formations.
While the job of offshore teams is to methodically consider how to maximize production from a few high-cost wells that are expected to produce for decades, those in the shale business have used standard designs to mass-produce wells in bad-quality rock, with a goal of maximizing production in year one.
“There are some things they overlook, that they do not think are detrimental because for them it is all about the front-end production” in shale, said Paul Carman, completions fluid specialist for ConocoPhillips.
That focus has allowed shale producers to steadily push up the first-year production over time, but the decline rate remains uniformly steep.
Fast-falling production is to a large extent a given in shale-oil wells. Liquids are pushed out by natural gas escaping from solution. As the pressure drops over time, the gas flow increases, and the oil flow drops.
But there is growing evidence that the chemicals used to complete these wells could be adding to the losses. Researchers have found in laboratory testing that interactions of chemicals used downhole can block production pathways in these reservoirs, which at their best are nearly impermeable.
Those problems are easy to miss because they happen after year one.
“Initially in the Eagle Ford, where conditions are fairly harsh with temperatures of 325°F and lots of water, we did not have a scaling problem. Now we have a scaling problem,” Carman said.
The word “initially” in that comment means about 5 years ago. And it didn’t surprise him.
“It is water and rock. You’re going to have certain temperatures and pressures downhole. You dissolve some things. You produce something out of hole. The pressure drop and saturation will cause scale. You cannot get around it, it is in the water,” he said.
What makes shale different from conventional wells, and more difficult, is the rich array of ingredients available that can create problems.
“Shales are among the most reactive surfaces in the Earth’s crust. We need to pay a lot of attention to the composition and chemistry of fluids we are injecting,” said Anthony Kovscek, professor of Energy Resources Engineering at Stanford University. (This year, Kovscek was recognized with SPE's John Franklin Carll Award for his contributions of technical application and professionalism in petroleum development and recovery.)
He made the comment while presenting one of the papers that outlined research backed by the US Department of Energy (DOE) investigating the potential damage caused by chemical interactions in shale at the recent Unconventional Resources Technology Conference (URTeC) conference (URTeC 5640).
He reported on work where a core was repeatedly flooded with a cocktail of 15 chemicals drawn from a design used to fracture a well at a test site. The result was a major reduction in permeability due to chemical reactions in the three cores tested.
Reactions during flooding drew iron out of pyrite in the clay-rich rock sample, creating iron hydroxide, which resulted “in dramatic detrimental changes in the fracture and pore network systems,” the paper said. Barium in the water pumped combined with sulfates released with the breakdown of the ammonium persulfate breaker and created barite (barium+sulfate) buildup in that core.
Lab studies backed by the DOE suggest the blockages can significantly reduce the flow through shale.
“In every case if it (the reservoir) is sulfate-rich, there is a big drop of over 50% of permeability of the rock from these reactions,” said Adam Jew, an associate research scientist at the SLAC National Accelerator Laboratory.
The Altered Zone
An URTeC paper presented by Jew used ultra-powerful synchrotron-based imaging devices at SLAC (more information at https://www-ssrl.slac.stanford.edu/content/) to observe the blockages created by a variety of chemical reactions involving injected chemicals, brines, and reactive substances in and around the fractured rock (URTeC 5231).
The paper began by listing risks associated with fracturing a shale well.
- More additives are required for the intensive fracturing required in shale than in conventional wells, where if fracturing is required, it is small in comparison.
- There is more time for reactions to occur because it takes weeks to fracture laterals running a mile or more.
- Many of those chemicals remain in the ground because much of the fluid never flows back.
Pioneer Natural Resources backed the work reported in that paper, which used cuttings from key plays in the Midland Basin—the Wolfcamp A and B plus the Spraberry—as well as water with the same makeup as the produced water and treated sewage the oil company pumps there.
“The altered zone of the shale in the stimulated reservoir volume is fairly thin, centimeters deep, but mineral scale that affects hydrocarbon flow from the matrix to the fractures is occurring both in the matrix of the altered zone and on the fracture surface from different processes,” according to the paper.
The paper described laboratory testing that identified chemical reactions that could free the reactive ingredients that can lead to scale deposits.
Pumping hydrochloric acid to soften up perforations—known as an acid spear—can cause reactions that free reactive elements, including iron, calcium, and barium.
The chemicals used to break down a friction reducer—pumped to reduce the risk that the polymer causes damage—include ammonium persulfate, which is a rich source of sulfate. That, plus sulfate from other sources, can combine with other reactive elements to create scale in and on the rock.
Another concern is that free iron in a well can react with the polymer in a friction reducer—polyacrylamide—significantly reducing its performance, based on lab testing. In extreme cases, these reactions create black gunk, known as gummy bears.
Unlike scale hidden deep in the fracture network, black gunk was the basis of a horror story shared among operators in the Woodford Formation located in Oklahoma whose surface equipment was fouled by gummy bears.
A solution to the mystery was offered a year ago in an URTeC paper by Mark Van Domelen, vice president for technology at Downhole Chemical Solutions, who said there is more to the problem than meets the eye in a recent interview (JPTstory, URTeC 2487).
“That gunk can go anywhere it can form in the proppant pack, the choke, a gas lift nozzle. It can be problematic anywhere,” he said.
Making Gunk Matter
The presentation about black gunk at URTeC and the JPT cover story that featured blobs of gunk that looked like a prop from a horror film, made Van Domelen kind of famous.
A friend asked him if that was a good association for someone in the friction-reducer business.
He recognizes the problem and prefers calling the bad stuff gummy bears. And he would rather talk about how the company can reduce truck traffic by delivering dry friction reducer to fracturing sites and mixing it there. Still, Van Domelen said it has generally been a plus. “It raises awareness of the issue and there has been a lot of followup,” he said.
Customers wondering about chemical interactions are sending in drilling cuttings for analysis to see if component in them might affect the additives being pumped.
There is greater awareness, but it is far from universal. “Many operators are going in blind. They pump the cheapest friction reducer they can find and suffer the consequences if the conditions are not right,” said Van Domelen.
He added that when it comes to damage due to chemical reactions, “it is so much harder to fix than it is to prevent.”
Other experts interviewed all agree with that sentiment. The hard part is identifying the right friction reducer to use, but there is no buyer’s guide or industry standard to guide the evaluation of friction reducers.
Ideally, the completion engineer would have chemical testing data on each well and an understanding of how friction reducers are likely to react in that environment.
The reality is there is no quick way to answer those questions, so completions engineers have to make some educated guesses. Chemicals suppliers talk about the need for a well chemistry database allowing engineers to make reasonable assumptions about the chemistry of the fracturing water and geology in an area with other wells.
On the chemical side, Rockwater turned to Interface Fluidics to develop what they say is a faster, cheaper, more accurate testing method for chemicals used in fracturing.
They adopted Interface’s testing technology to consistently simulate chemical reactions in propped fractures that is faster and cheaper than the available standards.
The Interface Fluidics device combines a silicon wafer with features added to the surface to simulate flow through a porous media—a proppant pack with a range of sand grain sizes (40/70 mesh). It is topped by a sheet of glass which is bonded to the silicon, sealing it and allowing observations during testing.
The small flow-through units allowed the testing of multiple friction reducers, brines, and reactive chemicals. They could see changes in the virtual proppant pack and also measure changes in the resistance as they pumped fluid through the unit at reservoir temperatures and pressures.
“Interface can run a wide range of fluids and fluid combinations to understand fluid-fluid interactions in the reservoir,” said Stuart Kinnear, chief executive officer for Interface Fluidics.
Rockwater made that effort because it is looking for evidence to convince skeptical customers that they need to select friction reducers based on the chemistry of fracturing water and the well.
“The industry wants to know what are the two products that do everything. The reality is we have 28 products in our line,” Price said.
Based on their testing, chemical reactions can obstruct the flow through propped fractures.
“These issues due to incompatibilities can occur even if the friction reducer demonstrates an ability to suitably perform its primary role of reducing pressures” during fracturing, Price said.
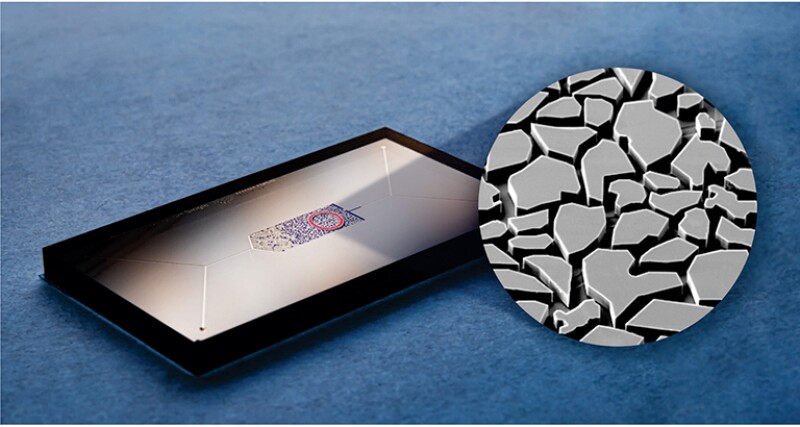
Consider Doing Less
A lesson from the DOE-Pioneer research project was: “The big thing is simple is better,” Jew said.
That translates into changing or eliminating chemicals or approaches likely to cause problems.
Breakers made with persulfate are effective over a wide range of well conditions—a paper by Carman concluded as much in 2007—but when it breaks down, it releases sulfates, providing a building block for scale formation.
If the amount of friction reducer used is low, a breaker may not be required, Carman said.
Jew also advises against acid spears—pumping hydrochloric acid to soften up the reservoir rock before pumping a fracture. In the process, it can release multiple reactive chemicals that may cause problems such as iron from pyrite, barium from drilling mud left after cleanup, and calcium from carbonate rock.
All can contribute to the amounts of those elements in the produced water. In the coreflooding experiment, the Marcellus water included barium, strontium, iron, calcium, and magnesium.
The industry is split between those who insist on doing acid spears and those who do not. Derek Hina, technical service manager for Reliance Oilfield Services, said a customer who read an SPE paper advising against acid spears told him, “that’s not an option.”
Since acid has proven to be a useful treatment for downhole scale issues, Jew suggests substituting sulfuric acid for hydrochloric acid as a way to significantly reduce sulfate releases, plus some other steps to deal with related reactions. Oil companies considered the idea, but ultimately said no.
“They are afraid of changing the chemistry” in a well that costs millions to drill and complete, Jew said.
The result is an unanswerable question. “When they ask if it will it work, I cannot answer without doing the field test,” he said.
Another question they face is: How does scale development in fractures compare to what they have found in coreflooding experiments? There are going to be differences. As the name implies, coreflooding is designed to ensure the injected fluids flow through the rock, which is far from assured in nature where the pace of change is slower.
Collecting data on how fractures change over time due to chemical reactions in the well presents enormous challenges. The cost and risk of developing methods to identify where, and how much, chemical reactions are reducing permeability would be high. It is the sort of big problem best addressed by an industry- and government-supported partnership.
No one knew what fracturing looked like in the ground until there were test sites paid for by companies—beginning with ConocoPhillips—and often government that dug up fractured core samples and conducted many other tests to see where they grew and interacted.
What they found was the fractures are propped sporadically and the sand found in those cracks does not resemble the uniform proppant packs used for testing. This led Carman to wonder how much the chemical reactions change proppant conductivity and how it may affect flow. Another question on his mind: Does an acid spear release enough reactive stuff to have a significant impact?
The hard part about selling a downhole chemistry test site is that unlike fracturing, which has been recognized as an essential tool for shale production, there are a lot of people who wonder if downhole chemistry matters that much in large fracture networks.
“There is some work saying frac surface damage is not so critical,” said Alexandra Hakala, a senior fellow for geologic and environmental systems, who is the Onshore Unconventional Resources Technical Portfolio Lead at the National Energy Technology Laboratory in Pittsburgh, Pennsylvania.
She countered that work by noting that production pathways in fracture networks converge at critical spots and those “pinch points are critical.”
For Further Reading
URTeC 5640 Coreflood Effluent and Shale Surface Chemistries in Predicting Interaction Between Shale, Brine, and Reactive Fluid by A.S. Gundogar, SLAC National Accelerator Laboratory and Stanford University Energy Resources Engineering; J.L. Druhan, University of Illinois at Urbana-Champaign; C.M. Ross, Stanford University Energy Resources Engineering; and A.D. Jew, SLAC National Accelerator Laboratory, et al.
URTeC 5363 Rethinking Mineral Scaling: What, Where, and Why Is It Occurring in the Stimulated Rock Volume by A.D. Jew and J.R. Bargar, Stanford Synchrotron Radiation Lightsource ; J.W. Brownlow, Pioneer Natural Resources; and M.M. Laughland, Stratum Reservoir.
URTeC 5231 Controlling Strontium Scaling in the Permian Basin through Manipulation of Base Fluid Chemistry and Additives by Eleanor Spielman-Sun, SLAC National Accelerator Laboratory; A.D. Jew, SLAC National Accelerator Laboratory; J.L. Druhan, University of Illinois at Urbana−Champaign, et al.
SPE 106162 Successful Breaker Optimization for Polyacrylamide Friction Reducers Used in Slickwater Fracturing by P.S. Carman, and K.E. Cawiezel, BJ Services Co.
URTeC 5391 Characterization and Remediation of Scale in Three Horizontal Wells in the Point Pleasant Appalachia, PA by A. Roberts, E. Fonseca, and T. Tekavec.
URTeC 5179 Optimizing the Selection and Application of Chemical Additives in Shale Reservoirs by J. Yan, W.i Wang, W. Wei, and G. Winslow, Chevron Corporation.
URTeC 5524 Hydraulic Fracturing Geochemical Impact on Fluid Chemistry: Comparing Wolfcamp Shale and Marcellus Shale by W. Xiong, J. Moore, D. Crandall, C. Lopano, and A. Hakala, National Energy Technology Laboratory.