This paper describes the method developed to achieve underbalanced drillstem testing (DST) in a deepwater field offshore India. DST tools rated to 450°F and 15,000-psi differential pressure were configured to maintain integrity and successfully evaluate the well potential. By use of a multicycle DST tool string, the reservoir potential was tested safely and effectively with an underbalanced test fluid in two deepwater wells, achieving the desired test objectives.
Introduction
An operator in India needed to conduct high-pressure/high-temperature (HP/HT) drillstem testing on a deepwater well with low-density clear brine in the annulus. Performing DST was necessary to assess hydrocarbon potential in the deepwater block for further field-development plans.
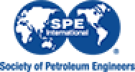