The purpose of acid stimulation of carbonate formations is to increase production. The essential component for these stimulation fluids is the carbonate-dissolving agent, which creates conductivity channels connecting the reservoir with the wellbore. Controlling the reactivity of hydrochloric acid (HCl), the most-used dissolving agent due to its high dissolving capacity, wide availability, and low unit cost, is the most viable approach to successfully stimulate a high-temperature carbonate reservoir.
It is essential to retard the HCl-carbonate rock reaction to achieve the optimum balance between total fluid used and enhanced well production. It is well documented that the conventional emulsified acid exhibits high friction pressure, is cumbersome to prepare, and performs with sensitivity to a multitude of parameters. These drawbacks have prevented the industrywide adoption of this method.
The recently developed single-aqueous-phase retarded acid (SAPRA) designed for primarily 15–25% HCl solutions represents a significant step forward. The first successful field implementation of SAPRA took place offshore the Malaysian state of Sarawak in early 2021.
At Sarawak, the HCl reactivity was regulated and retarded by a single potent low-dosage additive, which is compatible with selected acid corrosion inhibitors, nonemulsifiers, H2S scavengers, other commonly used additives, and if necessary, friction reducers.
Improving Acid Stimulation Efficiency
The technical approach behind SAPRA is based on chemical technology that enables the reduction of the reaction rate and allows the control of the diffusion/mass transfer mechanism. This is key in designing the acid treatment to optimize chemical program cost and well production and has been extensively studied (Al Moajil et al. 2020; Czupski et al. 2020; Daeffler et al. 2018; and Abdrazakov et al. 2018).
The technology was developed utilizing a surface barrier concept where transiently adsorbed retarder molecules adhere to a carbonate surface and thus, delay the hydrogen ion carbonate reaction over a range of acid concentrations and operating temperatures. Due to the complexity of the chemical interactions among all the additives in the acid fluid system, the selected additives must be screened to ensure mutual compatibility before conducting performance testing such as corrosion rate, calcite solubility capacity characterization, and coreflow measurements. Incompatible chemistry could lead to severe corrosion issues such as the examples shown in Table 1.
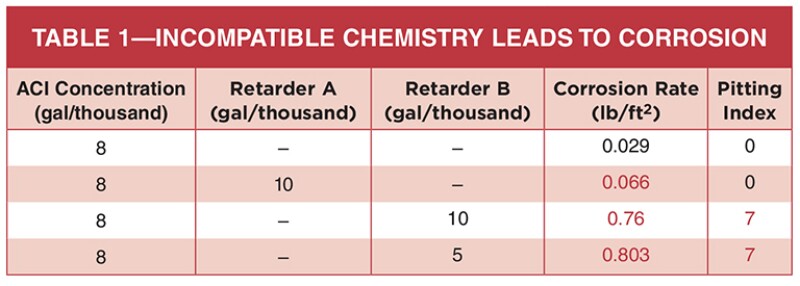
Experimental Materials and Procedures
The experimental acid fluid recipes comprise:
- HCl base solution
- Acid corrosion inhibitor (ACI) with an intensifier
- A water-soluble carbonate acid retarder
- H2S scavenger
- Nonemulsifier
- Iron-control additives
The test acid solution underwent a series of procedures to analyze package dispersibility, thermal stability, limestone acid digestion, and metal corrosion. This was followed by acidizing coreflood preparation and experiments. Indiana Limestone cores were used throughout the investigation.
Following successful determination of porosity and permeability, brine is injected at the desired rate until a steady-state pressure drop is reached. At this point, the acid injection is switched on and the acid begins to be pumped into the system. The pressure is recorded throughout the flood, and the pressure-drop data is used to determine the exact pore volume to breakthrough (PVBT) of the given coreflow. Once the formation of a wormhole is apparent through the pressure data, brine is again switched on and injected into the core to completely flush the system of acid.
All experiments are performed with the applied pressure of 1,000 psig and conducted at 127°C and 138°C with the injecting rates between 1 to 6 ml/min. The HCl strength is kept at 15 wt% and 25 wt%. X-ray computer tomography (CT scan) is used to examine the tested core for wormhole characteristics. In this work, 10 different ACI formulations were screened against three different retarder chemistries.
Results
Product compatibility. For both additives to function properly, an essential film formation at the molecular level on appropriate surfaces must occur. The ACI components must bind to negatively charged metallic surfaces, whereas the carbonate acid retarder must bind to a positively charged formation surface. Thus, the molecular properties of these ingredients are naturally opposed in their functions and must be carefully tuned in the overall acid formulation to preserve their individual action and efficacy.
Likewise, the overall dispersion of the formulation must be tuned such that these essential solute-surface interactions are maintained so that the mixtures are stable over a protracted time, with good thermal stability and absence of significant phase separation or precipitation.
Taken together, the exercise of creating an effective total package is a challenge; essential properties of the acid fluid must be tested with all elements of the package present. The ACI-retarder pair that was selected had the least problematic interactions and maintained overall functionality.
Dispersibility and thermal stability. Fig. 1 shows the general appearance of the additive package system as dispersed into 20% HCL. A very minimal separation of an oily material occurs without any substantial solids, yielding an exceptionally clean system overall.
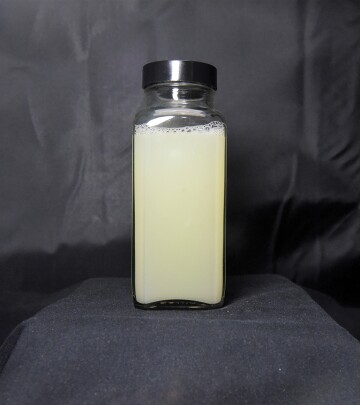
Thermal stability tests of the package were run in 15 wt% HCl at 138°C and filtered through a 100-mesh screen. Insoluble residue was neither observed nor produced from the thermal stress testing.
Limestone acid digestion. Acid-digestion tests of the total acid package were typically run in 15 wt% and 28% HCl solutions. The dissolution results reveal that SAPRA has significantly less weight loss in comparison with the neat acid HCl system, suggesting a slower carbonate surface reaction rate of SAPRA. Tests were run with freshly prepared and dry-aged solutions and showed no diminution of performance after aging.
Corrosion-rate testing. Acid corrosion tests were run using a variety of metallurgies, over temperatures ranging from 116°C to 138°C and between 6 to 8 hours exposure time. Excellent corrosion control was achieved with rates below the industry threshold of 0.05 lb/ft2. No pitting was observed using the base and modified packages. Separate tests confirmed that limestone digestion rates were unchanged using the modified system compared with the base system. Selected results of corrosion testing are shown in Table 2.
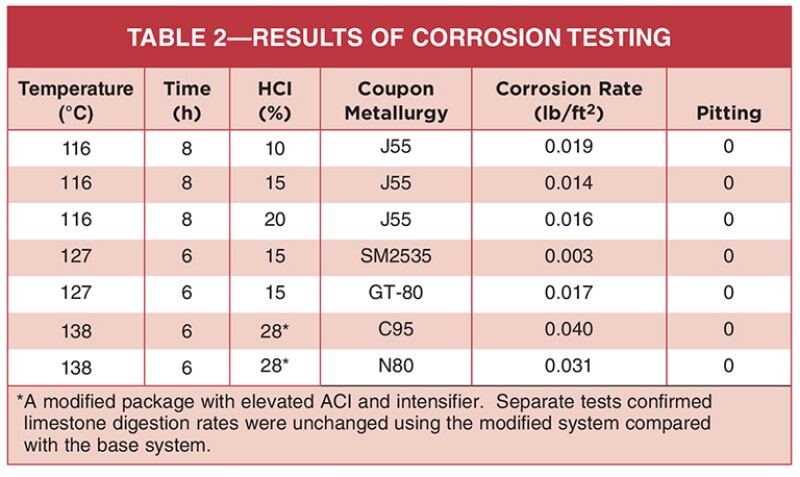
Coreflow testing and CT imaging. At the initial injection step, the acid is moving through a dead volume (volume inside the tubular part of the equipment, mainly the heating coil) where the pressure drop is relatively constant over the injected volume. When the acid reaches the core inlet, the pressure-drop signal rises and then drops after the acid breaks through the core. Flattening of the pressure-decline curve is confirmation that the acid has broken through the core.
Of all the coreflow experiments, the examiners found no premature reaction behavior. Fig. 2 above shows the typical CT scan of the core tested with the SAPRA system: a narrow wormhole with a few branches along the main path. The core inlet on the left and outlet on the right indicate good wormhole propagation throughout the core.
The results (Fig. 3) of the calcite-dissolving-capacity study and PVBT measurement indicate SAPRA effectively reduces the HCl reaction rate with the carbonate rock while retaining the dissolving capacity. The degree of reaction-rate retardation appears to be comparable to the equivalent emulsified acid system (acid strength) based on published data (Panga et al. 2005; Bazin et al. 1999).
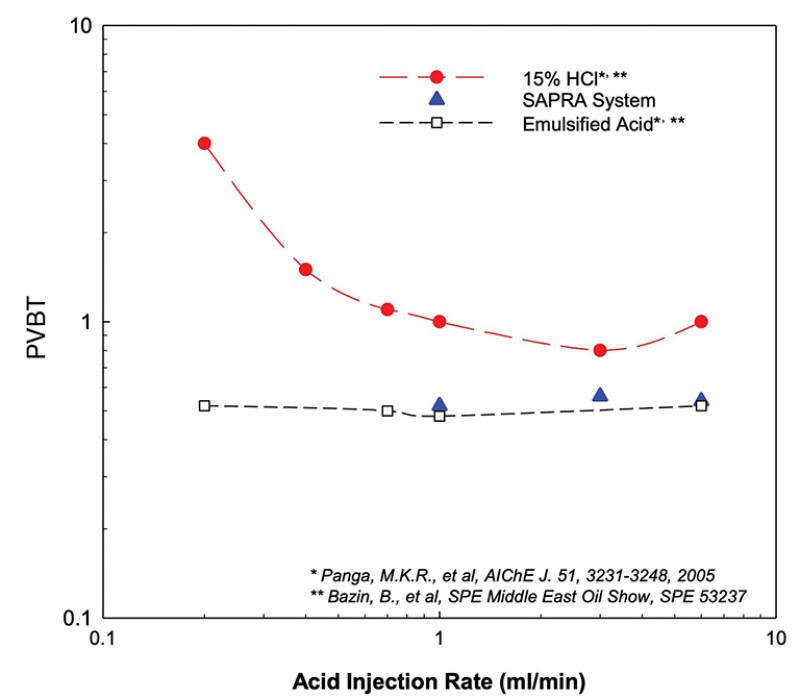
Wormhole patterns show that most of the retarded acid flows through the core sample. The wormhole structure at the lower flow rate and a more-branching wormhole structure at the higher flow rate. This characteristic may suggest the mass-transfer dependance of SAPRA. The behavior suggests the retardation mechanism is not temperature- and acid-strength dependent but rather injection-rate (diffusion-rate) dependent.
The main advantages of SAPRA over the emulsified-acid system are the following:
- It is a water-based system that eliminates the use of diesel, and thus minimizes environmental footprint.
- It can be mixed and pumped on the fly and therefore reduces surface equipment requirement and footprint.
- The fluid exhibits low Newtonian-like viscosity and compatibility with the acid friction reducer, which facilitates high rate or coil-tubing operations.
- It does not contain emulsion, thus has higher carbonate-dissolving capacity per unit volume of fluid compared to emulsified acid.
- It shows consistent performance throughout wide ranges of reservoir conditions due to the emulsion-free fluid architecture.
Further work is required to improve the fluid performance and features, for instance, how best to incorporate friction reducer and to quantitatively understand how the key mechanism controls the retardation of the system.
SAPRA is constructed from the molecular level up. Therefore, not only does this approach mitigate the risks associated with chemistry uncertainties, but more importantly, it provides a well-understood platform for continuous improvement.
Conclusions
Incomplete understanding of the exact nature of the chemical components in the acid system, for example, compatibility and reactivity among molecules themselves and with rock fabric, formation fluid, and downhole hardware, represents one of the main barriers preventing the industry from further advancing and improving the retarded acid system.
This study has demonstrated the importance of ensuring the mutual compatibility between all these molecules to achieve fluid robustness and consistent performance under a wide range of reservoir conditions.
For Further Reading
SPE 206363 New and Improved Single-Aqueous-Phase Retarded Acid SAPRA—Performance, Pore Volume Breakthrough, and Wormhole Characterization by J. Wu, ChampionX; M. Monette, The University of Texas; and J. Sickorez, ChampionX, et al.
SPE 203122 Performance Comparison of Retarded Acid with Emulsified and HCl/Formic Acid Recipes for Carbonate Acidizing by A. Al Moajil, N. Aljuryyed, S. Alghamdi, and S. Caliskan, Saudi Aramco.
Energies 2020. Development of Selective Acidizing Technology for an Oil Field in the Zechstein Main Dolomite by M. Czupski and P. Kasza, Oil and Gas Institute—National Research Institute; and L. Lesniak, Brenntag Polska.
SPE 189540 Improving Wormholing Efficiency in Carbonates with a Novel System Based on Hydrochloric Acid by C.S. Daeffler, J.F. del Valle, J. Kariampally, et al., Schlumberger.
SPE 189559 New Single-Phase Retarded Acid System Boosts Production After Acid Fracturing in Kazakhstan by D. Abdrazakov, M. Panga, and C.S. Daeffler, Schlumberger; and D. Tulebayev, Emir Oil LLP.
Two-Scale Continuum Model for Stimulation of Wormholes in Carbonate Acidization by M.K.R. Panga and M. Ziauddin, Schlumberger, and V. Balakotaiah, Dept. of Chemical Engineering, University of Houston.
SPE 53237 Experimental Investigation of Some Properties of Emulsified Acid Systems for Stimulation of Carbonate Formations by B. Bazin, Institut Français du Pétrole, France, and G. Abdulahad, Homs University, Syria.
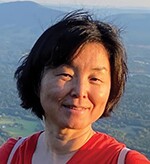
Jing Wu is a staff scientist in the reservoir group for ChampionX. She has 15 years of experience in the oil and gas industry working on research and product development for several product lines. She holds a master’s degree in chemistry from The University of Texas at Arlington.
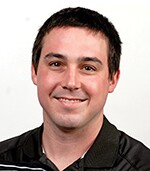
Jeffrey Sickorez is a senior chemist at ChampionX. He has more than 9 years’ experience in the oil and gas industry and has worked with several different product lines, primarily focused on acidizing and well stimulation. He holds a BSc degree in chemistry from the University of Houston.

J. Paul Street is the research and development director of the reservoir group for ChampionX. He joined ChampionX in 1992, working in both downstream and upstream applications areas for the oil and gas industry. He has led research for the ChampionX reservoir group for the past 15 years. He holds a PhD in chemistry from the University of California–Davis and performed his post-doctoral work at the University of Alberta.
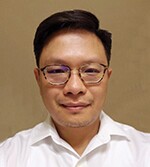
Peng Tonmukayakul is a senior marketing manager at ChampionX. In his current role, he manages, positions, and delivers new technologies for the company’s acidizing portfolio. He has 17 years’ experience in the oil and gas industry, particularly in well stimulation. In his previous roles, he worked in remedial treatments research, and engineering. He holds a PhD in chemical engineering from The University of Adelaide.
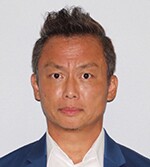
Jesse Lee, SPE, is a marketing technology director at ChampionX. For 21 years prior to joining ChampionX in 2018, Lee held several marketing and research, development, and exploration managerial positions with Schlumberger in the US and internationally. He has also previously served as a member of the JPT Editorial Committee. He holds a PhD in chemistry from Yale University and conducted his post-doctoral research at the Massachusetts Institute of Technology.
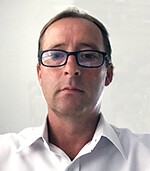
Steve Craig, SPE, is the business manager for the Eastern Hemisphere reservoir group at ChampionX. He joined ChampionX in 1994 and has held several Europe and Middle East technical and sales management positions within the production chemicals sector of the oil and gas industry. Craig began working in the reservoir chemical technology group of ChampionX in early 2020. He holds a PhD in chemistry from Strathclyde University.
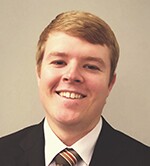
Matthew Monette is an engineering research scientist in the Hildebrand Department of Petroleum and Geosystems Engineering at The University of Texas at Austin. He holds BS degrees in both geological engineering and geology and geophysics from the University of Wisconsin at Madison and an MS in petroleum engineering from The University of Texas at Austin.
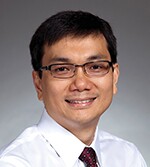
Quoc Nguyen, SPE, is a professor in the Hildebrand Department of Petroleum and Geosystems Engineering at The University of Texas at Austin. His current research interests include complex fluids, petrophysics, and subsurface transport processes related to hydrocarbon recovery. Nguyen holds a PhD in petroleum engineering from Delft University of Technology. He has published more than 220 journal and refereed conference papers, is an SPE Distinguished Member, and received the 2017 SPE Lester C. Uren Award.