Inorganic scale deposition is a ubiquitous challenge in oilfield operations due to the confluence of complex water chemistry and widely varying process conditions. When conditions become favorable, scale formation can be rapid, extensive, and lead to costly impacts to production (Kamal 2018). Given this risk, it is common practice for well operators to include scale inhibitors in their production chemistry treatment packages (Olajaire 2015).
The most common types of inhibitors are organophosphonates, anionic low-molecular-weight polymers, or combinations thereof. Mechanistically, scale inhibitors function by inhibiting the nucleation of scale crystals, retarding growth of the crystals as they form, or preventing deposition of precipitated solids onto downhole surfaces (SPE 87470).
Benefits of Slow Release
Most inhibitors are applied as liquids via either continuous, batch, or squeeze treatments (Kan 2020), but another option is to use a slow-release solid scale inhibitor. A variety of different options have been developed and tested over the years (SPE 134414; SPE 199255), and new approaches continue to be reported (Xiao 2024; Wu 2025).
Broadly speaking, these products are designed to provide extended periods of protection against scale deposition by slowly releasing an active inhibitor molecule into the well. The active molecules, mechanisms of retention and release, and timescales of protection vary widely and as such, one solid scale inhibitor may not be interchangeable with another.
Operators should carefully consider the characteristics and properties of the products they are considering to ensure they are compatible with the downhole environments being treated. Incorrect application may not only fail to achieve the desired scale-inhibition behavior, but also negatively impact well performance through additional formation damage and solids deposition.
Finoric has developed a family of slow-release solid scale inhibitors under the tradename of ScaleGone. Two versions of the product are currently available (Fig. 1), and additional variations are under development.
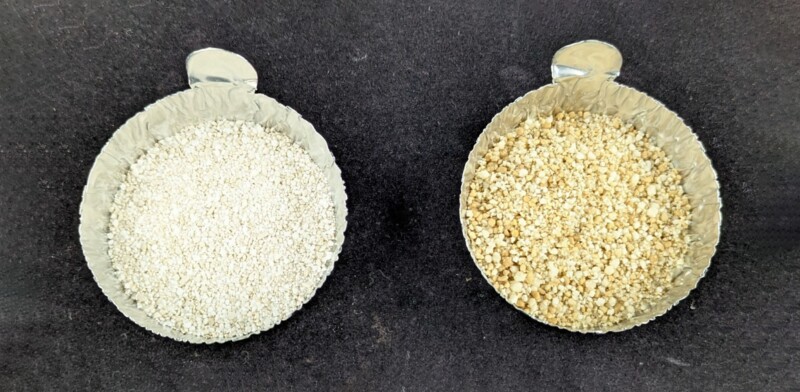
The base version contains a slow-dissolving active ingredient that is encapsulated by an inert polymer material; the polymer coating provides an additional barrier between the active ingredient and the fluids in the wellbore.
A second version contains the same slow-dissolving active ingredient, but does not have a polymer coating. Both formulations comprise high concentrations of the active scale-inhibiting ingredients, but the absence of the polymer coating in the uncoated version affords an even higher level of activity for that product.
While the encapsulated formulation has an activity level of approximately 85%, the uncoated formulation has an activity level of nearly 95%. High levels of activity are desirable because they lead to reduced dosage requirements to achieve a target scale-inhibitor concentration in the fluid. Both products are sized to approximately 14/40 mesh so that they blend well with the proppants used during unconventional well completions.
Scale Inhibitor Deployment in the Bakken and Permian
Exhaustive laboratory testing has shown that Finoric’s slow-release solid scale inhibitors are effective against multiple types of scale encountered in the oilfield environment and can exhibit release rates on the order of multiple months (depending on test conditions). Critically, however, these lab experiments have translated well into application of the product in the field.
The first field study highlights a six-well trial conducted in the Bakken Shale in 2023. Produced waters in the Bakken contain high levels of dissolved solids and are prone to forming a variety of types of scale, including calcite (CaCO3), siderite (FeCO3), and halite (NaCl) (SPE 174966).
Laboratory testing conducted with a synthetic brine and a liquid form of the solid scale inhibitor’s active ingredients indicated an expected minimum inhibitor concentration (MIC) of approximately 0.8 ppm. Above this concentration, the scale inhibitor is present at sufficient levels to prevent scale formation under the conditions used in the test. Below this concentration, the inhibitor is not able to prevent scale formation, and the risk for solids deposition increases significantly.
The encapsulated inhibitor was pumped at a rate of 0.3 lb/kGal of fluid through all stages of six wells. Aliquots of the flowback fluids were collected and analyzed starting approximately 45 days after completion.
An average active concentration of roughly 4.1 ppm was measured across all six wells for the first 9 months of production (Fig. 2). This was well above the expected MIC of 0.8 ppm, indicating that scale formation was not expected (and indeed was not observed) during that time frame. After 10 months of production, two of the six wells had fallen below the MIC, and by 12 months, all six had fallen below the MIC, indicating that the product had reached the end of its useful life.
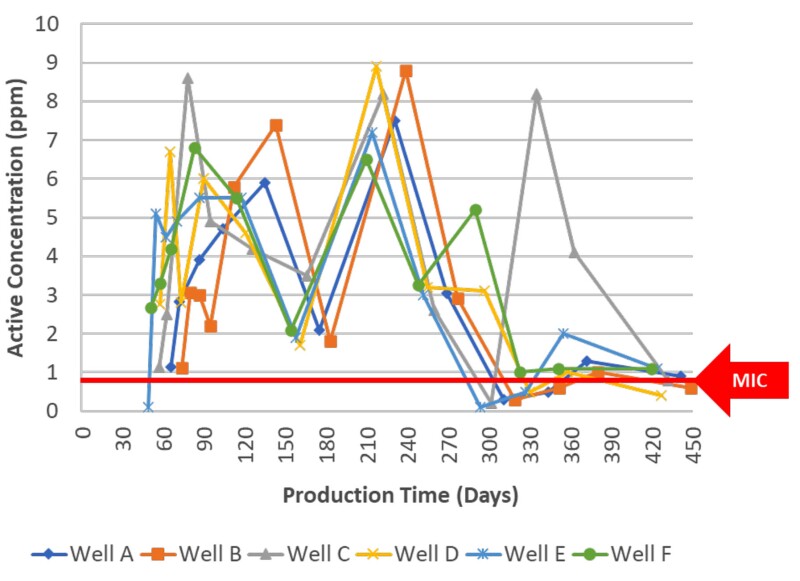
At this point in the well’s production cycle, scale control would need to be achieved using a conventional liquid inhibitor or via reapplication of slow-release solid scale inhibitors in a workover or remediation procedure.
In a separate ongoing study in the Permian Basin, a combination of the coated and uncoated inhibitors has also proven effective at preventing scale formation. Incorporation of the uncoated inhibitor into the treatment package provides an initial spike of scale inhibitor during the early phase of production, and then the slower-dissolving encapsulated inhibitor combined with the inherently slow-release properties of the common active ingredient provides an extended period of protection.
Before beginning the Permian treatment program, the operator had been experiencing frequent scaling of their subsurface electrical submersible pumps (ESPs), leading to costly interruptions and pump replacements every 3 to 4 months. Since beginning the treatment program, flowback monitoring has shown ppm‑level concentrations of the active ingredient, and no scaling has been observed on the ESPs after at least 10 months. Residuals monitoring in the flowback fluid is scheduled to continue until the concentration becomes too low for detection.
Conclusions
In summary, this study shows that solid slow-release scale inhibitors can be very effective treatment options for wells that are expected to exhibit scaling issues during their production life. By applying a solid treatment during the well’s initial completion, it is possible to provide protection against scale formation from the outset of production.
In addition to maximizing uptime during the well’s initial high-volume production phase, solid scale inhibitors can delay the need for costly liquid inhibitors that require additional equipment such as capillaries and metering pumps.
Every operation is different and as such, treatment strategies such as product selection, dosage, and placement location will likely change from well to well, but in most cases, it is possible to design a viable strategy.
For Further Reading
SPE 174966 Scale Squeeze Fractured Reservoirs in the Bakken, North Dakota by S. Cook, H. Lu, J. Cutler, C. Haugen, L. Cenegy, and C. McAfee.
SPE 134414 A 5-Year Survey of Applications and Results of Placing Solid Chemical Inhibitors in the Formation via Hydraulic Fracturing by D.V.S. Gupta, J.M. Brown, and S. Szymczak.
Oilfield Scale Formation and Chemical Removal: A Review by M.S. Kamal, I. Hussein, M. Mahmoud, A.S. Sulton, and M.A.S. Saad. J. Petrol. Sci. Eng. (2018).
The State of the Art in Scale Inhibitor Squeeze Treatment by A.T. Kan, Z. Dai, and M.B. Tomson. Petrol. Sci. (2020).
SPE 199255 Case Histories of Extended Scale Prevention from Single Treatment of Chemically Infused, Slow-Release Media by J. Leasure and M. Marotz.
A Review of Oilfield Scale Management Technology for Oil and Gas Production by A.A. Olajire. J. Petrol. Sci. Eng. (2015).
SPE 87470 How Scale Inhibitors Work: Mechanisms of Selected Barium Sulphate Scale Inhibitors Across a Wide Temperature Range by K.S. Sorbie and N. Laing.
Encapsulated ATMP Microspheres with Slow-Release Scale Inhibition Function by C. Wu, K. Li, Q. Li, H. Yuan, L. Yang, Z. Dai, and J. Wang. Energy Fuels (2025).
Study on the Sustained Release Behavior of a Slow-Release Scale-Inhibiting Material by Y. Xiao, R. Hao, and S. Zhao. J. Polym. Res. (2024).
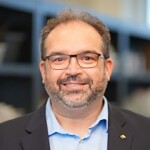
Daniel R. Dreyer is a corporate scientist at Finoric, where he develops and supports small molecules and polymer materials for use in the energy sector. He previously served as a staff scientist at Nalco Water and as director of chemical research at Graphea. His background includes oilfield chemicals, synthetic materials chemistry, polymer synthesis, and carbon nanomaterials. Dreyer began his research career at The University of Texas at Austin (UT Austin), where he focused on heterogeneous catalysis and advanced energy materials. He holds a PhD in chemistry from UT Austin and a BSc in chemistry and physics from Wheaton College.