This work is a study of collapse pressure of perforated pipes to evaluate the effect of lateral perforations on the radial resistance of pipes under external pressure. These types of pipes represent a simple and economical technology widely used as sand-control meshes or perforated liners.
Introduction
One of the most common challenges to high flow rates in mature fields is the migration of sand to the well. High rates of oil production together with maximum sand retention is the optimal result. In accomplishing this complex goal, perforated pipes play a vital role because they are a simple and inexpensive application, and they are widely used in the industry.
×
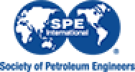
Continue Reading with SPE Membership
SPE Members: Please sign in at the top of the page for access to this member-exclusive content. If you are not a member and you find JPT content valuable, we encourage you to become a part of the SPE member community to gain full access.