Sour gas is being produced from a number of carbon-steel-completed wells in the US, Canada, France, and Saudi Arabia. The gas stream contains various levels of hydrogen sulfide and carbon dioxide (CO2) and is produced from high-temperature reservoirs with temperatures ranging from 160 to 410°F. The combination of hydrogen sulfide with high temperatures introduces challenges related to corrosion and iron sulfide (FeS) scale formation.
FeS Scales
FeS is found naturally in different forms. The gas-production systems studied in this paper have large concentrations of hydrogen sulfide, so iron is a limiting reactant in these systems. FeS formation is favored thermodynamically.
×
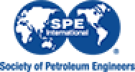
Continue Reading with SPE Membership
SPE Members: Please sign in at the top of the page for access to this member-exclusive content. If you are not a member and you find JPT content valuable, we encourage you to become a part of the SPE member community to gain full access.