Digitalization and automation have delivered step changes not only in technology, but also to process in the oilfield industry. Instead of making small incremental shifts in well construction operations, our industry can now make disruptive shifts for tangible performance gains in efficiency, safety, and well integrity. Indeed, many of those changes will enable fully automated drilling and are either in their nascent stages or already here. Operators and service companies that intend to remain competitive in this context must accelerate their own digital transformations going forward.
Digitalization and automation make existing processes or technologies more efficient and less error prone. Some examples of technologies which have been improved by digitalization and automation include automated tubular makeup and connection integrity management, intelligent managed-pressure drilling (MPD), and well-construction optimization software. These automated technologies enable working with fewer personnel, managing from a distance, reducing operational costs, and making better, more consistent decisions.
Automation in Tubular Running
Automated tubular-running technology is changing well construction as the industry knows it. The technology uses artificial intelligence to control both connection makeup and torque evaluation to replace the inherent flaws of human judgment and inconsistency of human behavior. The result is validated well integrity with certainty, minimized safety risks, improved reliability, and substantial cost savings.
Since the inception of this technology 2 years ago, it has delivered measurable value to producers on every continent in over 150 runs and nearly 50,000 tubular connections. It has helped to eliminate more than 20,000 hours of personnel exposure to rig-floor safety risks and yielded millions of dollars in validated savings.
One example of that value was in offshore Australia for a major oil company, where this technology enabled reduction of onboard tubular-running personnel by 33%. Fewer personnel also reduces the operational carbon footprint, helping to achieve another important goal shared by the industry. Another was in Argentina where a customer saved 24 hours of rig time through delivery of more than 1,000 connections with zero damaged joints in three wells. The value generated from rig-time savings alone often far exceeds the actual cost of the service.
In offshore Azerbaijan, a client ran seven completions with more than 2,900 connections and zero connections damaged. An operator in the United Arab Emirates achieved 30% faster run rates and zero rejected joints. And in offshore Qatar, the technology helped to eliminate connection damage while pulling completion strings from two wells, making it possible to reuse 75% more of the high-cost chrome tubing from automating the connection breakout process.
Applying artificial intelligence from pipe manufacturing to well installation improves efficiency and eliminates human errors during the connection process. This minimizes the chance of catastrophic well failures associated with leaking connections, significantly reducing risk and the total cost of well ownership.
Intelligence for MPD
The next generation of MPD technology represents the culmination of more than a half century of MPD results for faster drilling and completion, lower costs, and improved production. It incorporates decades of knowledge from the world’s most comprehensive database of tens of thousands of wells into one advanced artificial-intelligence-driven algorithm that drives a unique automated control system. This technology integrates rig equipment for machine-to-machine communication, real-time analysis of downhole conditions, and rapid automated responses. The result is well pressure, volume, and flow detection at levels which no human can perceive, controlled at a frequency which no human can sustain. This will become a core requirement in automated well drilling.
The MPD intelligent, automated control system provides real-time information to take the precise action at the right time and to maintain constant bottomhole pressures under any range of conditions or operations—from drilling, to completing, to cementing wells on land or offshore. A rotating circulating head in an automated riser also changes the game for floating drilling vessels by utilizing an integrated, robotically enabled, compact design to reduce installation time from days for legacy systems to minutes for the new automated systems.
Whether drilling in deep water or on land, automated MPD systems have solved challenges for operators and drilling contractors everywhere. In onshore Saudi Arabia, MPD helped to save 20,000 bbl of mud. In offshore Egypt, it enabled circulating out two influxes in hours while continuing drilling operations. And in deep water in the Gulf of Mexico, it saved a large operator more than $90 million on a six-well campaign.
Digital Well Delivery
Digitalization has already revolutionized the way operators manage and optimize production; now it is time to advance the drilling space. For decades, the industry has demanded a holistic approach to managing complex wellsite operations digitally. Now, a newly developed well-construction optimization software platform answers that challenge.
Giving operators every piece of mission-critical data all in one place, the platform is a key enabler for any oilfield company on a digital transformation journey. As an all-inclusive, real-time solution, it does more than transfer data between the rig and office. It combines planning, data management, visualization, real-time engineering capability, and facilitates execution, all from a single intuitive package.
The state-of-the-art platform seamlessly integrates the operator’s well data, so global team members can access, share, and store all vital project information to facilitate collaboration anywhere, anytime. It makes consolidated data available in real time, enables advanced domain viewing and live analytics, and leverages competency by giving a single engineer the analytical capacity of an entire team. It is based on more than a decade of delivering data services with 99.9% system uptime for more than 110 companies worldwide.
Digitalization and automation successes are accelerating and here to stay. The productivity gains that the industry will recognize as a result are apparent. As an industry, if we have the courage to eschew the old and embrace the new, our transformation will accelerate through better, faster decision making, improved operational efficiency and productivity, and reduced risk to people and the environment.
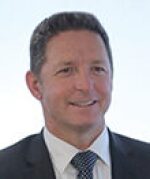
Dean Bell, Weatherford president of drilling, evaluation, and intervention, joined the oilfield service company in 2016 as vice president, intervention services, and drilling tools. Previously, he was vice president of drilling tools and remedial services for Europe and Africa at Schlumberger based in Paris. After time as a field engineer in MWD/LWD/directional drilling, his career spanned operations management positions in Central Asia, Latin America, and the Gulf of Mexico, as well as general management roles in Saudi Arabia, Mexico, and Indonesia.