Researchers at the University of Texas at Austin (UT) have set an audacious goal to halve the time, cost, and number of rig personnel required for drilling every type of well, from unconventional shale to ultradeepwater. The Rig Automation and Performance Improvement in Drilling (RAPID) research consortium is envisioned by its creators as an accelerator of technologies that can address “any and all” aspects of automated well construction.
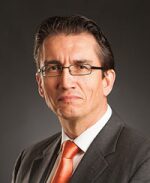
Launching a new research and development (R&D) group in the middle of an industry downturn may seem like bad timing. But program director and petroleum engineering professor at UT, Eric van Oort, emphasized that low oil and gas prices should serve as motivation, not trepidation.
“There is a big carrot out there. Operators have done everything to reduce cost, to reduce activity, to lay down rigs, to work with suppliers on price reductions,” he said. “The dust is settling on that, and the question now is what are you going to do to make these operations at [USD] 40, 50, 60 a barrel profitable?”
RAPID’s plan is to develop, field test, and assess the commercial viability of new technologies that deliver value for the companies who join the consortium and to get this done in a relatively short time. The far-reaching effort will leverage the experience of a multidisciplinary group of UT research scientists, talents of top engineering students, high-tech facilities, and mountains of drilling data from participating oil and gas companies.
The senior research team includes seven PhD-level engineers with extensive backgrounds in oil and gas, robotics, data analytics, and aerospace. Program director van Oort spent 20 years in various technical capacities at Shell before taking on his role at UT, and is a former SPE Distinguished Lecturer. In May, he addressed representatives from more than 30 upstream companies at a kickoff event on campus to make the case for why they should support RAPID.
To join the consortium and have access to its work, companies pay an annual fee of USD 75,000, prorated this year to USD 50,000. Once they become members, the hope is that the companies will provide critical drilling data and feedback on the direction of the research projects.
Aside from helping companies expand their profit margins, van Oort said automation will make drilling complex wells easier, improve safety, and help attract a new breed of engineers to replace those being lost through the recent layoffs, as well as those retiring amid the great crew change.
Another chief goal of RAPID is to enable true well manufacturing by evening out drilling performance across rig fleets to a level that is competitive with today’s best-in-class crews. Historically, operators have struggled to achieve such consistency.
“Just changing out a key individual—a key driller on one rig—could make a big difference, and what was once the best performing rig could suddenly become a very low performing rig,” van Oort said.
Low performers of the drilling sector bear a high cost on operators. It is estimated that most drilling operations suffer from an average non-productive time of about 20% per well. Exacerbating the problem is the inefficient work and poor execution of routine tasks that go unrecorded. Termed by the industry as invisible lost time, it can more than double the amount of actual time wasted on reaching a well’s total depth. When combining these metrics, van Oort said there is the potential to recover 50% of the cost of investment in most wells. “That is a big carrot for us to go after.”
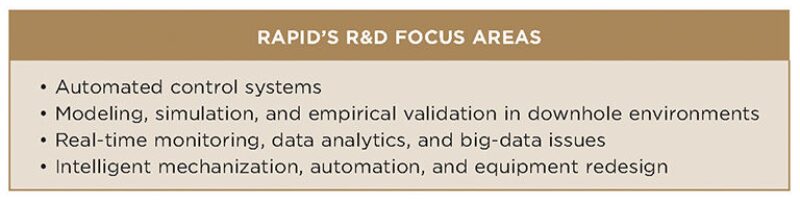
So far the program is confined to UT, but the intention is that other universities and research institutions around the world will become involved with RAPID. Van Oort said he has contacted another leading automation group, the International Research Institute of Stavanger in Norway, to open the door to collaborative projects. The RAPID consortium will also participate in SPE’s Drilling Automation Technical Section, which is one of the most influential advisory bodies in the field.
RAPID Developments
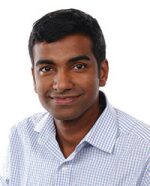
As integral members of the consortium, each of the senior scientists involved are bringing their own innovations to the table. Some of their latest work is expected to be presented at the SPE Annual Technical Conference and Exhibition in Houston this September, and some has already been published. Back in March, at the SPE/IADC Drilling Conference in London, several of the senior team members presented technical papers on projects RAPID is pursuing, including one authored by Pradeepkumar Ashok,one of the research scientists in UT’s drilling automation group.
Ashok is working with graduate students to make wellbore manufacturing a literal reality, as opposed to just a shale industry catchphrase. “People have been talking about it for a long time, and some people have been doing automation here and there in a very one-off manner,” he said. “What we want to do is set up a framework that unites everything.”
And that involves transforming disparate sets of drilling data into look-up tables to achieve safe and optimal drilling parameters. These tables are to be presented visually to the driller in a format similar to a heat map, or as a color-coded guide that can be easily interpreted. An automated control system will act on these tables to perform various routine drilling operations such as tripping, casing runs, and even managed-pressure drilling.
The table methodology simplifies the complexity involved with using rig and drilling data generated by multiple systems and in conflicting formats. Ashok said offering the driller a visual version of the tables will foster trust between man and machine because the tables make it easy to understand why the automated system is doing what it is doing.
On the front end of this process, everyone involved in drilling must be brought together to provide the data that will be used to generate the tables. This includes personnel representing the operator, drilling contractor, service companies, and the original equipment manufacturer. From there, a control algorithm designer can build the tables and then install them on a rig within a couple of hours.
Regardless of rig design, the model being used to generate the tables will, for the most part, be the same. Ashok said that means the automated processes on different types of rigs should be very similar.
The goal of this approach to automation is not to break drilling records, at least not for a while. Ashok argues that to achieve wellbore manufacturing on the scale of several thousand wells in the same field, first the industry must build the assembly line, i.e., a fleet of automated rigs running on programs that are rapidly customizable. Once that fleet is up and running, then companies can focus on rolling new wells off the line faster and faster.
This vision is at odds with what some in the industry want, which are systems that will outcompete even the best human driller as soon as they are introduced. But doing that involves creating very complex control algorithms which would delay development of automated wellbore manufacturing systems in the near future. The name of the game for now is not perfection; it is consistency.
“If you see how rigs operate today, there will be one rig which is always the best and the other rigs will be somewhere along the spectrum and what we want to do—through automation—is to bring all of the rigs to a consistent performance,” Ashok said.
And this is not to say that in the years to come, the type of complex algorithms needed for world-beating automation technologies will never be developed. They will be. But because automated drilling remains a nascent technology, Ashok said it needs a bridge to the future, which is what he hopes his model becomes.
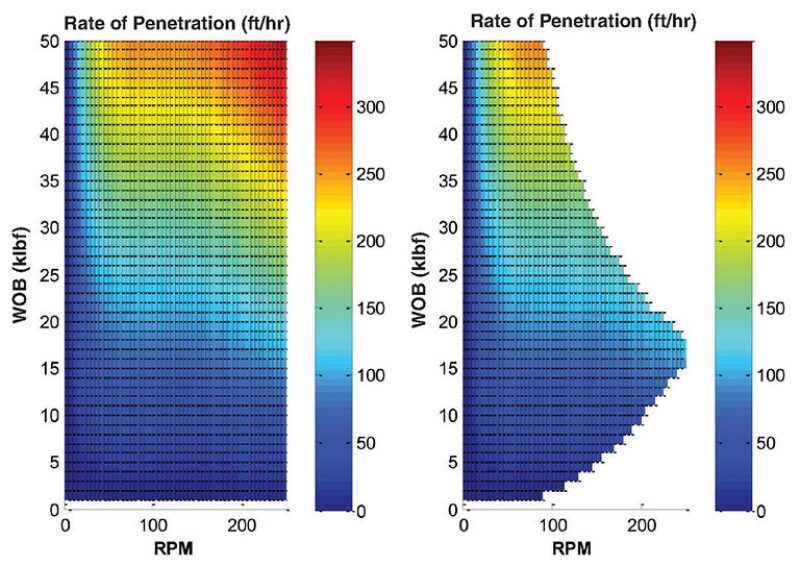
The more complex a model the less adaptable it is, Ashok said. The look-up table model will improve its performance through adaptive learning. As live drilling data come in, the tables adjust in real time and become more refined. Then those data can be used to drill the next offset well more efficiently. This approach to automated drilling is still in the early development stage and Ashok hopes to be able to test the model on a working rig by the end of this year.
Student Involvement Is Key
One of the central components of RAPID are students who take an active role in the research projects. As automation technology makes its way deeper into the industry, a guiding principle of the consortium is that it must be accompanied by people who know how to use the technology to the highest benefit and will serve as its champions.
To educate and train up this so-called “automation generation” for the industry, a new multidisciplinary track for graduate students has been created that deviates from the traditional petroleum engineering course work. Aside from courses related to drilling and completion, graduate students in the RAPID program will get knee deep into other automation-related areas such as digital signal processing, design of electrical machines, and advanced robot dynamics.
Among undergraduates, RAPID will take advantage of UT’s freshmen engineering research program which promotes highly qualified students to build robots that perform industrial tasks. Recent examples include a student-designed robot to handle radioactive materials in the nuclear industry and an automated pipe-doping system for the drilling industry that sought to reduce rig crew needs by one while improving quality assurance.
Mitch Pryor, one of the consortium’s senior research scientists and a UT lecturer with a background in robotics and automation, highlighted just how successful the freshman program has been and believes that if the oil and gas industry wants to fill the ranks with the most talented young engineers, then it ought to embrace robotics in a big way. “The robotics investment has paid off,” he said.
Of the 47 students who applied to the dynamic systems and controls graduate program in UT’s mechanical engineering department, 45 listed robotics as their number one area of interest—including the 28 who were eventually accepted.
Pryor noted that the overwhelming interest among students for robotics has presented a recruiting challenge for non-robotics professors. Down the road, the oil and gas industry may face an analogous situation whereby an increasing number of engineering graduates will pursue careers in industries that have better adopted robotics.
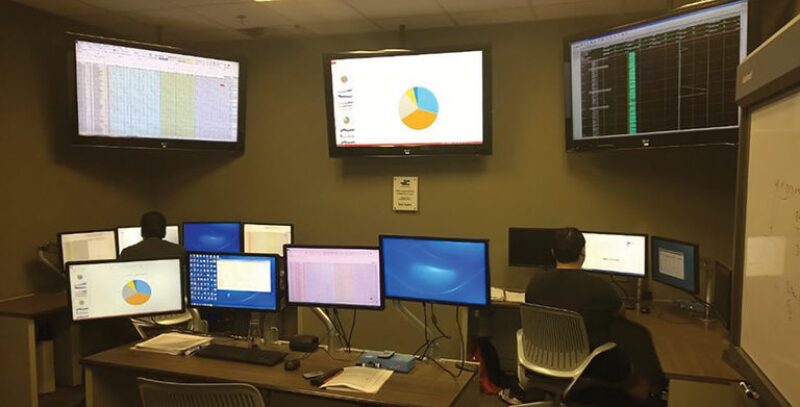
Aside from robotics, RAPID has several other tools at its disposal that will be used to run data analytics research, simulations, and modeling. One of them is a real-time operations center that has access to working rig data. Students with access to the monitoring center, which was funded by Baker Hughes, use industry software to evaluate performance trends and look for other useful patterns as rigs in the field drill their wells.
This offers the students a chance to learn well engineering as it happens, and puts another set of inquisitive eyes on the rig data for the operators. This setup has already delivered significant value for an operator when a group of seven students used the center to analyze drilling data from 200 wells. The inefficiencies identified by the students, if resolved, stood to save the company USD 57.5 million over a 3-month span.
For Further Reading
SPE 173164 Overcoming Barriers to Adoption of Drilling Automation: Moving Towards Automated Well Manufacturing by Adrian Ambrus, University of Texas at Austin, et al.
SPE 173085 Automated Drilling Fluid Rheology Characterization with Downhole Pressure Sensor Data by Ali Karimi Vajargah, University of Texas at Austin, et al.
SPE 170324 Automated Well Control Decision-Making during Managed Pressure Drilling Operations, by Ali Karimi Vajargah, University of Texas at Austin, et al.
SPE 170955 Pure and Coupled Drill String Vibration Pattern Recognition in High Frequency Downhole Data by Theresa Baumgartner, University of Texas at Austin, et al.