The author outlines current decommissioning guidelines and typical practices and explores cost-effective ways by which companies can navigate this multifaceted process. The complete paper provides a case study that illuminates an optimal, cost-effective decommissioning methodology for offshore facilities and structures, which is closely aligned with emerging decommissioning guidelines and regulations and with industry best practices.
Introduction
Decommissioning of offshore facilities will become increasingly important in Southeast Asia. Therefore, the promulgation of standard practices jointly developed by regulators and operators are key to the best outcomes for the environment, affected communities, and owner/operator economics.
Three well-known global conventions address broad guidance of decommissioning activities: International Marine Organization Resolution A.672, the United Nations Convention on the Law of the Sea, and the Oslo-Paris Convention. The coastal state having jurisdiction over the installation or structure should ensure that it is removed in whole or in part in conformity with these guidelines and standards once it is no longer serving the primary purpose for which it was originally designed and installed, or serving a subsequent new use.
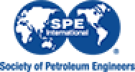