The complete paper describes piloting the collection and analysis of distributed temperature and acoustic sensing (DTS and DAS, respectively) data to characterize flow-control-device (FCD) performance and help improve understanding of steam-assisted gravity drainage (SAGD) inflow distribution. Fiber-optic-based instrumentation was deployed within FCD-equipped active wells using permanently installed coiled tubing. Logs were performed on multiple wells during stable and transient flowing conditions. Additionally, acoustic recording using flow-loop testing was completed with accelerometers, geophones, and fiber-optic cables during FCD characterization.
×
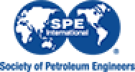
Continue Reading with SPE Membership
SPE Members: Please sign in at the top of the page for access to this member-exclusive content. If you are not a member and you find JPT content valuable, we encourage you to become a part of the SPE member community to gain full access.