Introduction
The subsurface safety valve (SSSV) is an emergency fail-safe flow-controlling safety device (API Specification 14A, Subsurface Safety Valve Equipment, 2015). However, it is not considered a well barrier because of its allowable leakage rate (Roth, et al., 2017).
Different countries have different mandates governing its installation. Some jurisdictions stipulate a requirement to have an SSSV in an offshore operating environment or when operating in close proximity to populated areas. Others leave the decision to the field operators.
When installed, SSSVs need to be regularly function-tested to ensure that they will correctly operate when required. It is often the case that an SSSV will fail prematurely— before the end of the life of well. In this case, an intervention is required to restore a functioning safety valve before production can be resumed. Until this intervention is planned, and depending on the regulations in place, a well could be shut in for a lengthy period of time, which in turn will impact the production levels. The intervention to reinstate a functioning SSSV can range from a relatively quick, rigless operation, to a full workover.
Some SSSV providers offer rigless remedial tools to aid salvaging their faulty SSSVs. However, these are valid options only if the failure was related to the valve functionality. However, if the failure was due to a damaged or corroded sealbore, or to a leaking capillary control line, TAQA is the only company offering a rigless solution to remedy and restore the SSSV.
Ways To Identify SSSV Sources of Failure
Effective troubleshooting is critical to find out what the problem really is and where it lies. Only then can we decide on the best course of action for the situation at hand. If however, conventional techniques have failed to resolve the SSSV issue, then most likely one of the two issues addressed in this article exist.
There are many ways to find the cause of an SSSV failure. One method is to plug the tubing below the SSSV or SSSV landing nipple: pressure-up the string while closing the control line manifold on surface and monitor for either pressure stability or consistent leakage. This will help define the condition of the control line. Further investigation could be conducted for the sealbore condition such as using an impression block.
Damaged Sealbore SSSV Failures and TAQA’s Remedy Approach
The focus of this article will be on a couple of unique and universal rigless solutions that can be attempted in any SSSV as a last resort when other conventional rigless options have failed and before preparing for an inevitable workover. These two technologies (PulseEight Secure & SwellStack) specifically address two SSSV failure modes: one internally in the tubing, and one externally on the outside of the tubing.
The first deals with damaged or corroded sealbores as shown in Fig. 1 where a regular insert SSSV cannot achieve a seal in either the tubing SSSV or SSSV landing nipple.
The second failure mode is when a failure occurs in the capillary/control lines where it is not possible to maintain or to apply pressure to keep either the tubing SSSV or insert SSSV open.
Another advantage of these technologies is that they can be simultaneously deployed if both failure modes take place concurrently.
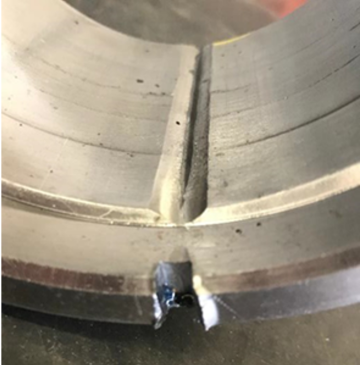
Typically, sealbores have the smallest internal diameter in a device. It is also where they accommodate regular packing seal stacks, mounted on a mating tool to retain the seal. These regular o-rings can only seal in well-polished sealbores. It is often the case that over time, these sealbores can get corroded or damaged by wireline and/or coil tubing runs which will eventually render them unusable.
The solution is to use proprietary swellable o-rings in custom-designed packing seal stacks to enable the continued use of the defective sealbores which have previously been scarred. An example of this is shown in Fig. 2. This solution has a quick turnaround and can be implemented on any insert SSSV from any provider. It is a relatively simple but effective method that has proved to work in numerous cases to revive the SSSV back to normal working conditions without the need for any workover or major well intervention.
PulseEight Secure—TAQA’s Unique Solution to Damaged Control Line SSSV Failures
The second common failure mechanism deals with the capillary line which is considered to be the artery of the SSSV system. It contains and allows the transmission of pressure via hydraulic fluid from the surface down to the SSSV. Operating the SSSV is accomplished by pressuring up or bleeding off the control line liquid. When out of service, the SSSV system as a whole becomes unresponsive.
The solution is to run TAQA’s propriety SSSV technology which functions completely wirelessly, thus eliminating the need for a control line or capillary tube. There are alternative insert safety valves on the market; however, these are passive tools—they do not facilitate maximum production rates and require frequent resetting and pressure calibration.
As shown in Fig. 3, TAQA’s PulseEight Secure technology entails a standalone piece of equipment with a self-contained battery pack that powers the SSSV. In addition to this, the tool has a variety of programmable commands and safety triggers that allow it to exceed the functionalities of a regular SSSV.
PulseEight Secure employs Fluid Harmonics, TAQA’s proprietary wireless production telemetry that puts produced fluids to work as a two-way channel for data and tool commands. Using Fluid Harmonics, the wireless intelligent SSSV will send a daily signal assuring its health so there’s no ambiguity on its readiness to respond in the case of an emergency situation. Accordingly, there’s a reduced requirement to schedule regular function tests and hence compromise well performance. On receipt of the daily signal, the operator will have full confidence that the valve is functional. The signal will also have embedded several other pieces of information, most importantly how much life is left in the battery and tool performance. This will enable the operator to plan ahead of time to replace the wireless intelligent SSSV with minimal disruption to other activities.
Utilizing this technology can help save the operator a substantial workover investment as well as delayed production revenues that could result from having to shut in the well for prolonged periods of time.
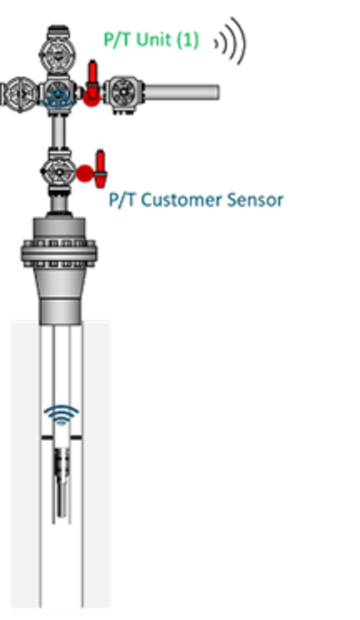
In conclusion, TAQA’s proprietary PulseEight Secure technology in combination with SwellStack can offer a unique and robust rigless solution to any SSSV failures, minimizing well intervention cost and time as well as reducing the risk of locked production.
REFERENCES
API Specification 14A, Subsurface Safety Valve Equipment (2015).
Xiao, D., Abdulaziz, M., Mack, J., Sarawaq, Y., Reid, R., and Helvenston, A. (2017). Field Deployment of a Rigless, Cable-Deployed ESP Using a Vertical Wellhead. The Saudi Aramco Journal of Technology.
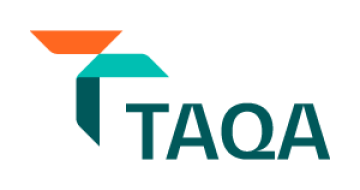