Automating well downtime detection helped ExxonMobil identify wells that were open but not producing so engineers and production technicians could work to bring priority wells back online.
The supermajor developed its Downtime Advisory System (DTAS) to improve well production uptime tracking in the Permian Basin to better respond to large variations in daily production volumes that resulted from unrecorded downtime, Yan Wang, production engineer for ExxonMobil Upstream Permian Business Unit, said during a 25 September technical session at SPE’s Annual Technical Conference and Exhibition in New Orleans.
A limited number of production engineers and lease operators were responsible for monitoring many wells in the Permian which made it challenging to accurately record volume losses. As such, it was difficult to identify and act on production optimization opportunities, according to “Production Optimization through Operate by Priority: The Development and Deployment of Downtime Advisory System to Permian Wells” (SPE 221082).
For the purposes of the DTAS, Wang said, ExxonMobil defined downtime as when a well was not producing its primary production fluid, which would be oil for most wells in the Permian Basin. ExxonMobil considered a well to be underperforming, on the other hand, when it was still producing its primary commodity but at rates lower than expected due to an operating condition such as reduction in gas lift, pinched choke, or higher than usual flowline pressure.
Increasing instrumentation and communication makes production data more readily available, particularly in offices far from the field. But all that data could overload a production engineer, Wang said, so the idea of using that data and algorithms to automate detection of nonproductive wells was considered.
Doing so had a number of benefits, Wang noted, including improving accuracy of downtime data, saving travel time, and enabling the identification of the highest-volume wells that could be prioritized to return to production.
One of the first steps in automating downtime detection was establishing a good baseline of what the flow condition looks like for the well, Joshua Kaus, production engineer at ExxonMobil Upstream Integrated Solutions Company, said during the presentation.
Some of the data used in the DTAS is from steady-state production well tests, in addition to data from 2-minute intervals related to downhole pressure and temperature, casing pressure, artificial lift measurements, emergency shutdown (ESD) signals, and more.
But because “we do get faulty data sometimes,” Kaus said, the rules-based system cross-validates the results to determine if a well is shut in or underperforming (Fig. 1).
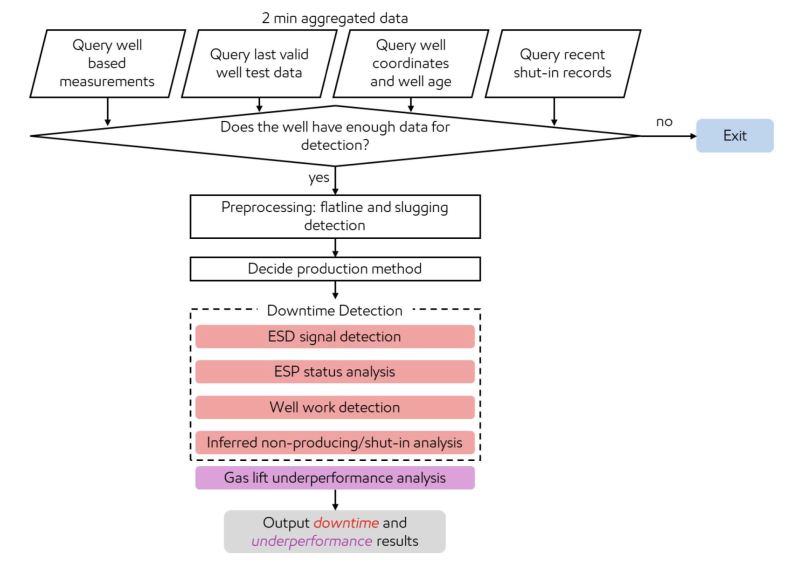
Kaus said ESD shutdowns were fairly simple for DTAS to detect. It can also detect autochoke events, in which wells are often still producing but at lower rates, and liquid-loading events, he noted.
DTAS can determine whether signals from a well’s electrical submersible pump (ESP) are in line with or lower than well test data to determine if the well is producing. For most ESP wells, if current values are much lower than test data, the paper noted, the ESP would be considered to be shut down or idle, which would typically translate into production downtime.
In addition, DTAS has an inferred shut-in algorithm that can identify other situations in which wells were not producing, Kaus said.
DTAS can also identify when gas lift injection rates are reduced, and it works with a gas lift optimization workflow in the Permian Basin to quantify the impact on production, according to the paper.
When DTAS infers downtime for a well, it notifies lease operators with an explanation of the downtime, which allows the operator to review and approve or reject an automated recommendation, according to the paper (Fig. 2).
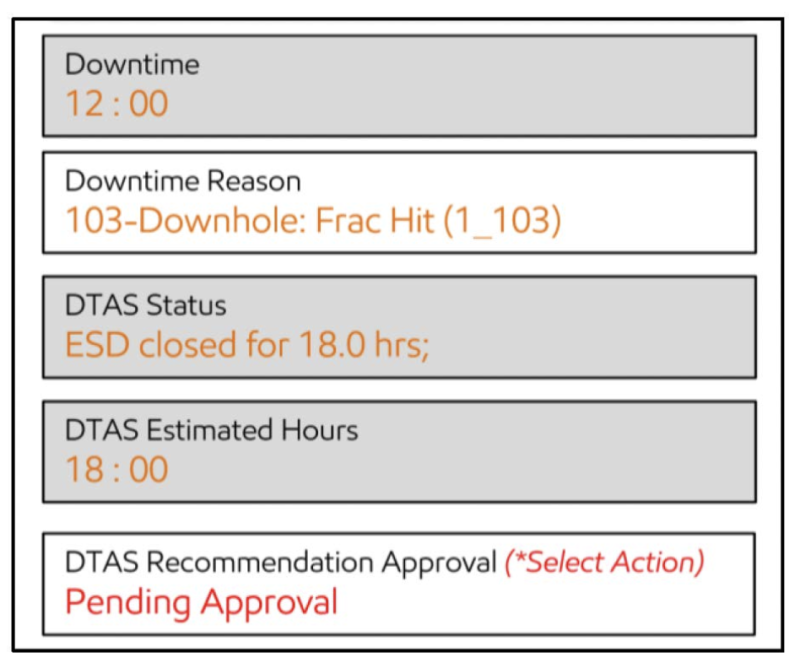
Kaus said DTAS helps to prevent unrecognized downtime from being missed (Fig. 3) and in one case identified 18 hours of an ESD being closed, alerted the appropriate lease operators of the event within 24 hours, and “provided recommendations to make their lives easier.”
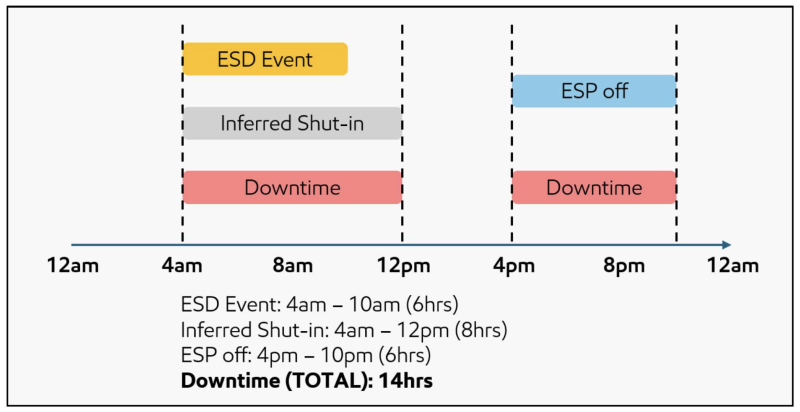
The system has been deployed across about 2,500 wells in the Permian and has resulted in a notional 5% improvement in the accuracy of downtime reporting, Kaus said. He noted that the amount of downtime reported is not necessarily higher, it’s just a more accurate reflection of production downtime.
That increased accuracy has helped ExxonMobil better concentrate its efforts on gaining extra uplift, he said.
The system has also made it possible to improve use of the lease operator’s time, he said.
With the development of DTAS, ExxonMobil was also able to break down the different categories of production downtime by volume (Fig. 4).
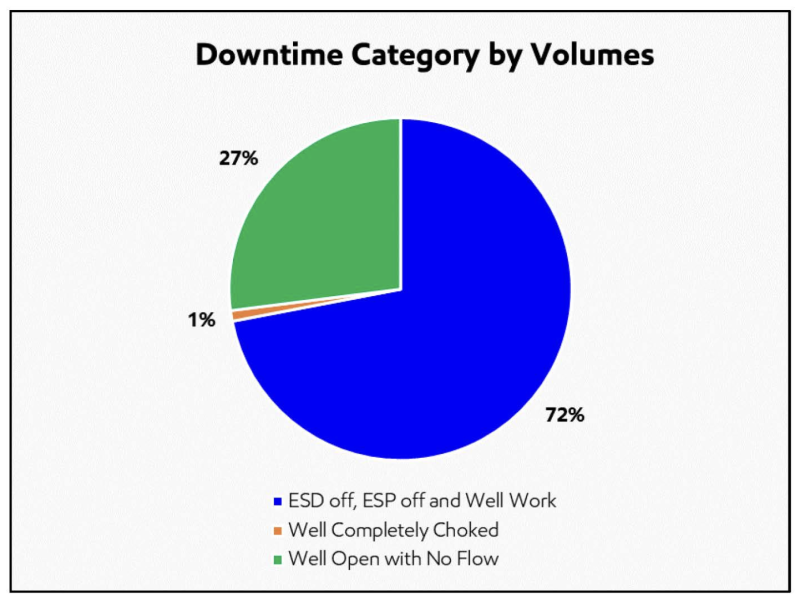
Kaus said the automated advisory system is one more step on the road toward a more digital oil field.
For Further Reading
SPE 221082 Production Optimization Through Operate by Priority: The Development and Deployment of Downtime Advisory System to Permian Wells by Y. Wang, J.E. Kaus, E. Karantinos, and Tuan Thanh Phi, ExxonMobil Upstream Integrated Solutions Company.