After the 2010 subsea blowout of the Macondo well that resulted in 11 deaths and the worst oil spill in US history, early kick detection technology found itself at the top of the wish list for regulators and offshore companies seeking to avoid similar accidents. The National Commission on the BP Deepwater Horizon Oil Spill concluded that the crew lacked both training and the technology to recognize the critical signs that a kick was occurring.
“If noticed, those signs would have allowed the rig crew to shut in the well before hydrocarbons entered the riser and thereby prevent the blowout,” the commission said.
Five years since the accident, there has been limited progress made in advancing kick detection for conventional, or open-to-atmosphere drilling. One reason is that kick detection is complicated, involving a mishmash of sensor readings that must be correctly interpreted. Because of this, many of the existing kick detection technologies suffer from a high rate of false alarms and only function under certain drilling conditions.
These issues prompted Shell to partner with National Oilwell Varco and Noble Drilling to create what it calls a “smart” kick detection system. Brian Tarr, a principal well engineer who leads the work on well control technology at Shell, discussed the project at the recent SPE Drilling Systems Automation Technical Section Symposium in London.
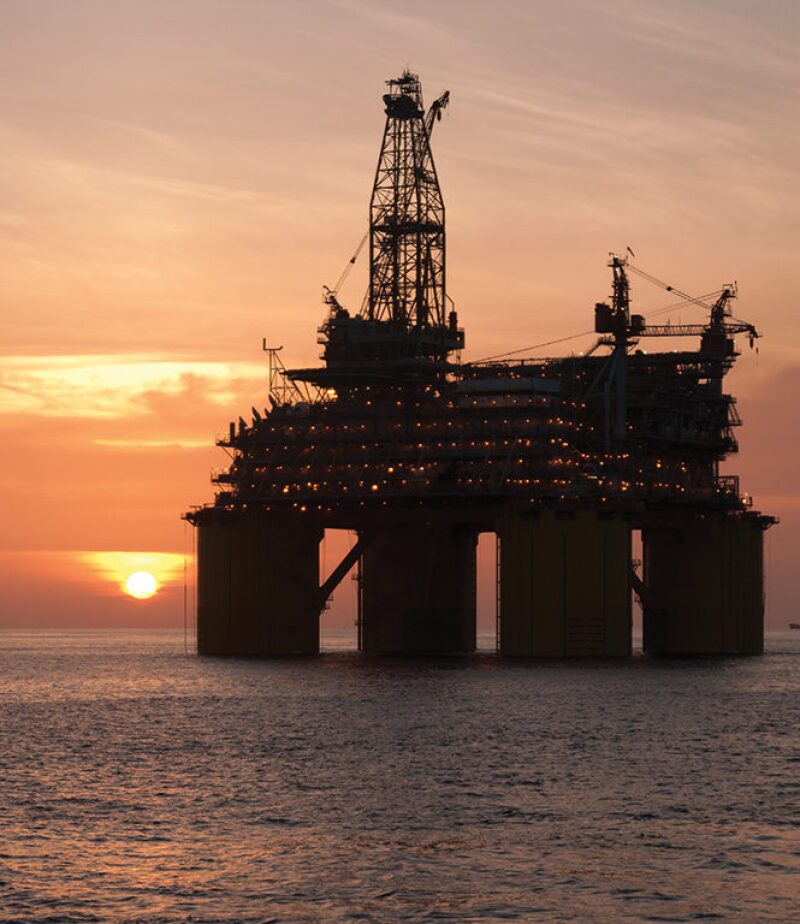
Shell thinks that improved reliability will lead to an automated kick detection and reaction system. But there is yet another problem with developing this type of technology. Despite the importance expressed by both industry and regulators, there remain no defined standards.
“We haven’t really focused on measurements associated with kick detection in our industry. If you go and look at industry requirements for kick detection systems, it basically says you have to have a measurement,” without spelling out the requirements for accuracy or redundancy, he said.
Those working on new detection methods point out that the status quo represents a large financial opportunity. Halliburton has reported that pore pressure and wellbore instability issues, which include kicks, cause as much as USD 8 billion in lost time each year for the offshore industry.
Kelly Rose, a research scientist at the US National Energy Technology Laboratory (NETL), has invented a new technology to detect kicks just above the drill bit. The idea came to her at a US government meeting that made 25 recommendations for improving the safety of offshore drilling. Early kick detection was No. 1 on the list.
Rose noted that aside from improving safety, detecting kicks both large and small can reduce the cost of drilling. “All kicks are not equal. Most of the time when industry is facing some sort of wellbore instability event, it is not nearly the magnitude of a Deepwater Horizon,” she said. “But even minor kicks lead to drilling challenges.”
Though many new systems remain untested in the field, the hope is that they will improve upon the current options and give crews more than enough time to address a potentially dangerous kick before it reaches the rig floor. The ultimate solution may be a bottoms-up approach, in which kicks are not merely evaluated using sensors on the rig floor, but are also tracked as they move past multiple points along the wellbore.
Eric Toskey of the Letton Hall Group, a Houston-based research and development firm, said the industry has “handicapped” itself by over-relying on measurements from the rig. He is working on a sensor that can be placed above the blowout preventer (BOP), which he said is a first step toward a networked detection system.
“The idea is that if you have information at the bit, then you can see influx of fluids from the zone right after you have drilled it, and that is really ideal” in order to enable the driller to balance the mud pressure, he said. “But we also want to see how it is moving up the hole of the annulus and riser, so it still wouldn’t be enough if you just had a sensor at the bit or the [bottomhole assembly]. You would want to have additional sensors higher up.”
New Rig-Based System
The first generation of Shell’s new jointly developed system was piloted on a Noble rig in the US Gulf of Mexico, where it detected its first kick only a few days after installation. The kick was also the only one detected during the 6-month trial and was covered in an SPE technical paper (SPE 173052).
Shell set out to create a new technology because the vendors of current rig control systems “have been slow to realize the desirability of automated kick detection systems that can alert the driller to a possible kick situation, regardless of the well construction activity being conducted,” the paper said.
Tarr elaborated and said many of the available systems fall short because they are focused exclusively on detecting events during drilling and circulating operations. But based on internal data from the companies involved in the project, only 25% of kicks experienced on deepwater floating rigs happen during drilling and circulating.
The 25% of the time when kicks are related to making connections and the 50% that are related to tripping the drillpipe in and out of the well were not covered. “That was a big gap to start with that we needed to fill,” Tarr said.
To enable the detection of kicks during each type of drilling operation, new algorithms were created along with “kick-specific” alarms that sound with a pop-up window on the driller’s control screen. The pop-up windows correspond to the type of drilling operation taking place, e.g., drilling, connections, or tripping, so that the driller understands why the alarm was tripped and has the information to decide what to do next.
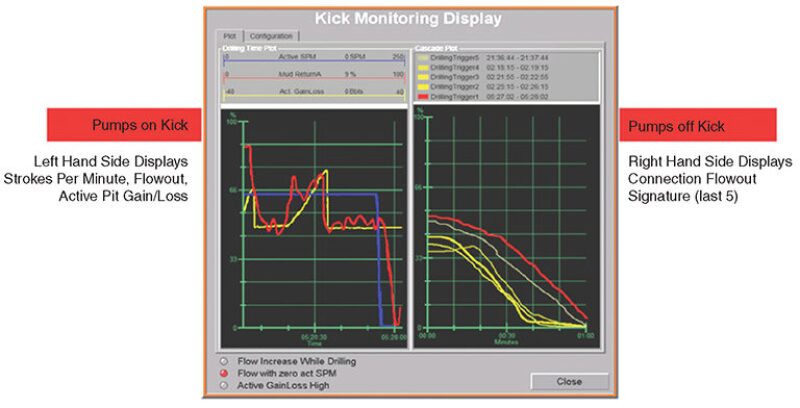
For instance, if a kick was to occur while the driller is making a connection, then the pop-up window displays the flow signature of the previous five connections to clearly show why the latest connection is cause for concern.
The alarms on the current kick detection systems can be set off too easily by routine actions such as starting and stopping the mud pumps, the SPE paper argues. This is why the Shell-led project had placed a heavy emphasis on reducing the potential to trigger false alarms.
“It has to be a system that only demands [the driller’s] attention when there is really an influx,” Tarr said. “If it just becomes an annoying nuisance, crying wolf too often, he is going to ignore it, turn it off, and it’s of no use.”
To reduce the number of false kick indicators, the best available sensor technology was installed in the rig’s flow systems and redundancy was built in by using different types of sensors to duplicate key measurements. The foundation for much of this part of the project came from the lessons shared by Shell’s downstream business, which has extensive experience with automated safety systems and sensor technology.
However, in the end, the system still experienced a high rate of false alarms of 35% for kicks and 65% fluid losses, which can be interpreted as a precursor to a kick. And just as with the commercial systems that Shell is seeking to replace, the main culprit for the false alarms was believed to be associated with the stopping and starting of the mud pumps. The company thinks this problem can be addressed in the next generation of its detection system.
Hand in Hand: MPD and Kick Detection Technology
Many of the kick detection technologies being developed today target traditional open-to-atmosphere drilling operations. However, another rising technology called managed pressure drilling (MPD), a closed-to-atmosphere system, has many built-in advantages for kick detection systems.
Designed by Weatherford, Microflux is one of the commercial kick detection technologies designed to work with MPD systems, and has been used for almost a decade in fields both onshore and offshore around the world.
This tandem of MPD and early kick detection was used in Canada to detect an influx of just 19 gal (less than half a barrel) that was automatically circulated to the surface without having to close the blowout preventer. It also helped shave 50 days off of the expected rig time in the North Sea in a harsh environment drilling program.
Neal Richard, an offshore account manager at Weatherford’s Secure Drilling Services unit, said many of the commercial kick detection systems meant for openhole drilling are not fully capable of delivering on their promise.
The main reason is that these technologies use information derived from the traditional, yet inexact, kick detection practice of monitoring the volume of the mud pit and paddle systems to measure flow. Richard, an engineer who has spent more than 9 years working on MPD projects at Weatherford, said those systems are inadequate for kick detection and rely too much on human interpretation.
“Normally, kicks are not detectable in less than 10-bbl increments using conventional equipment,” he said. “We are adding tools for measuring the flow-in and flow-out using instrumentation, such as the Coriolis meter, and we are looking for small changes in the flow trends.”
According to Richard, the early kick detection system can measure kicks with volumes smaller than 1 bbl. This method relies on key MPD systems such as a rotating control device, which diverts all the returning drilling mud flow away from the rig floor and through the MPD manifold. Inside the manifold, MPD chokes are used to pressurize the mud system and may be automatically controlled to respond to kicks.
Also inside the manifold, a Coriolis flowmeter measures multiple parameters of the returning mud flow in real time. The information is fed into a control unit that determines whether the changes in flow are due to an influx or another phenomenon such as wellbore ballooning, also called breathing. It takes the system about 20 to 30 seconds to make the right call.
“The most important thing is that you have detected the influx quickly and controlled it at a very small volume,” Richard said. Simply put, the smaller the kick, the easier it is to deal with.
Mudline Detection
Another approach to kick detection involves placing a sensor package just above the BOP. The effort is led by Letton Hall, with funding from the Research Partnership to Secure Energy for America (RPSEA), a nonprofit organization that has been developing new oil and gas technologies under a contract with NETL for the past decade. Cameron International, the world’s largest maker of BOPs, also participated by providing technical assistance and facilities.
The researchers concluded early in the project that a subsea system could be built and tested much quicker than a downhole sensor, which would have to overcome the complex issues of high pressures, temperatures, power supply, and communication to the rig or platform.
Placed inside the joint that connects the riser to the BOP, the proposed sensors would measure density to identify an influx. The developers believe that density is the key to detecting kicks because formation fluids, i.e. oil and gas, are lighter than the drilling mud.
Depending on the water depth, Toskey of Letton Hall estimates that between 20 and 40 minutes of warning time could be gained with the proposed sensor. He added that the end goal is not only to detect the differences in the density, but also to measure exactly how much mud, gas, and oil has flowed into the riser.
“That’s the thing that I’ve heard drillers say they are most excited about,” he said. “The confirmation that you have oil and gas at the mudline is extremely important, but moreover, can you quantify it? Can you tell me how much is there? Are we looking at 1 bbl, 10 bbl, or 100 bbl?”
If provided with these kind of numbers, the drilling crew can take more decisive actions on the rig floor to prepare for and mitigate the kick on its way up.
One of the two tested sensors is similar to the ultrasonic technology used in the advanced flowmeters that operators use to measure production on the topside of platforms. Ultrasonic sensors are highly sensitive to gas in liquid flow and there is a strong correlation between their response and fluid density. The other test involved a hydrostatic sensor that relied on pressure measurements to determine density.
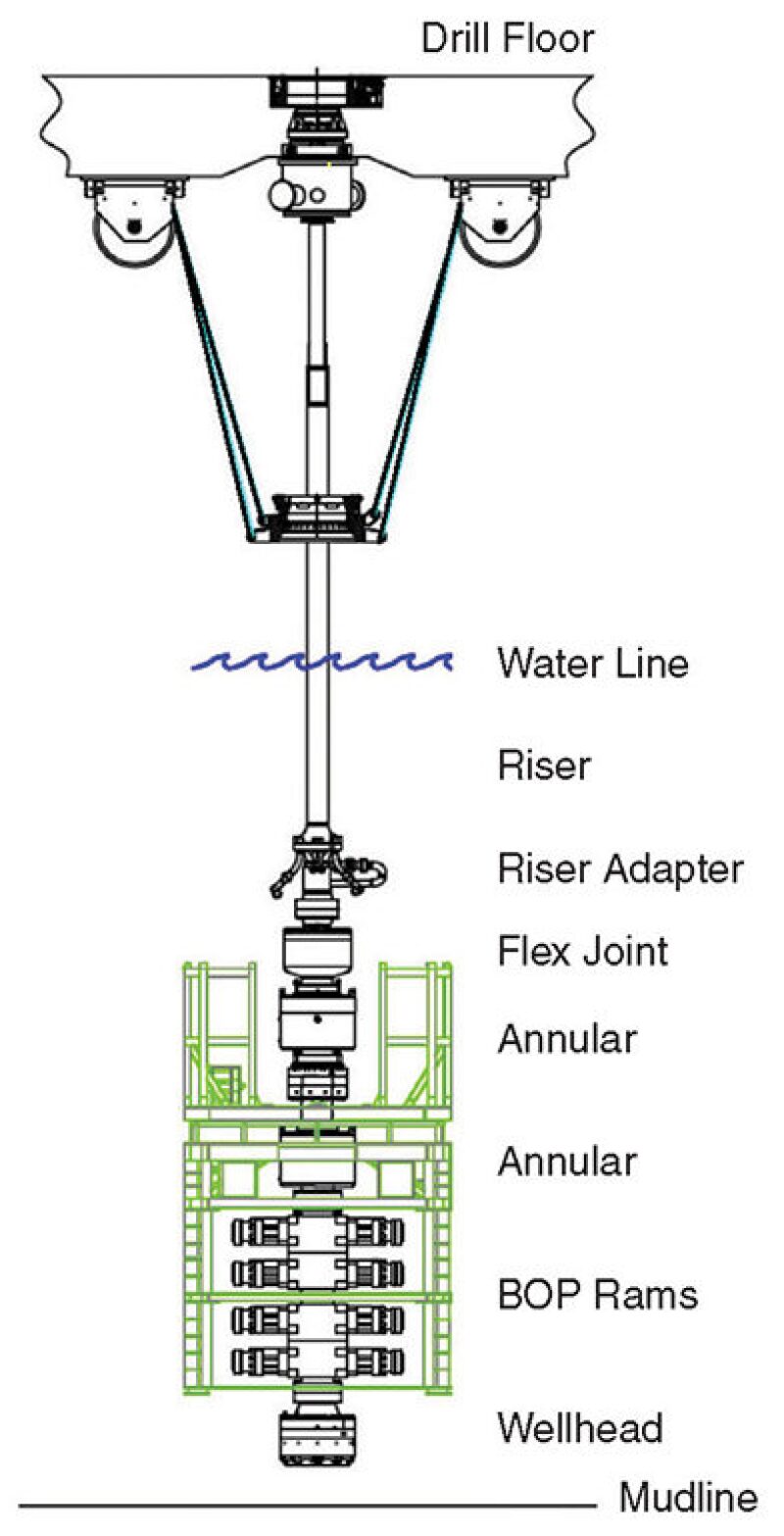
Due to budget constraints, polyvinyl chloride (PVC) pipe was used to run the simulation of flowing fluids and gas instead of steel. Despite not being able to use steel, Toskey said the testing proved the feasibility of the sensor package, but more research will be needed to design a device that can actually be tested during drilling offshore. Last year, the US government rescinded any future funding of RPSEA. Toskey said that for the research to continue, operators will need to step in to form a joint industry project.
He added that detecting kicks at the mudline should not be seen as a standalone solution, but as a piece to the bigger puzzle of how to detect and track kicks. He believes that a robust system will include a “multiplicity of measurements” that ranges from the bottom of the hole all the way up to the rig. Letton Hall has begun to develop a downhole sensor that it hopes to test for mud density measurement.
Kicks at the Bit
The kick detection system being developed by the NETL scientists would rely on logging tools, such as measurement-while-drilling or seismic-while-drilling, which sit just above the bit and therefore require no installation of additional hardware. Once a kick is detected downhole, the driller would receive a warning on his control screen a few seconds later.
All these “while-drilling” tools collect large volumes of information as they travel down the borehole and are also routinely used offshore, especially in challenging wells, to characterize the formation or geosteer the bit to the pay zone.
While not their primary function, these tools also collect data about the dynamics inside the wellbore. However, this information is often unused by service companies or operators. “They are throwing that out, kind of like when you make cookies and you throw the scraps out around your cookie cutter. But there is still meaningful information in those scraps,” said Rose, a former exploration geologist at Marathon Oil. “I thought, why can’t we recycle this data?”
To do that, the information is processed through a suite of filters and algorithms that assess the wellbore condition mathematically. If a kick happens, the numbers in the data should change accordingly and trigger the alarm.
While NETL’s results have so far been positive, they are limited in scope. To date, only one operator has shared its logging-while-drilling data with NETL for testing the algorithm. The data set was provided by a Middle East operator on a drilling operation that experienced four documented kicks at different intervals.
When the NETL approach was used, each of the four kicks was positively identified, said Brian Tost, a wellbore geophysical researcher at NETL. “That was really encouraging for us and if anything, it helps develop a thirst for more data,” he said. “You get a hint that it works and you want to see it in other data sets.”
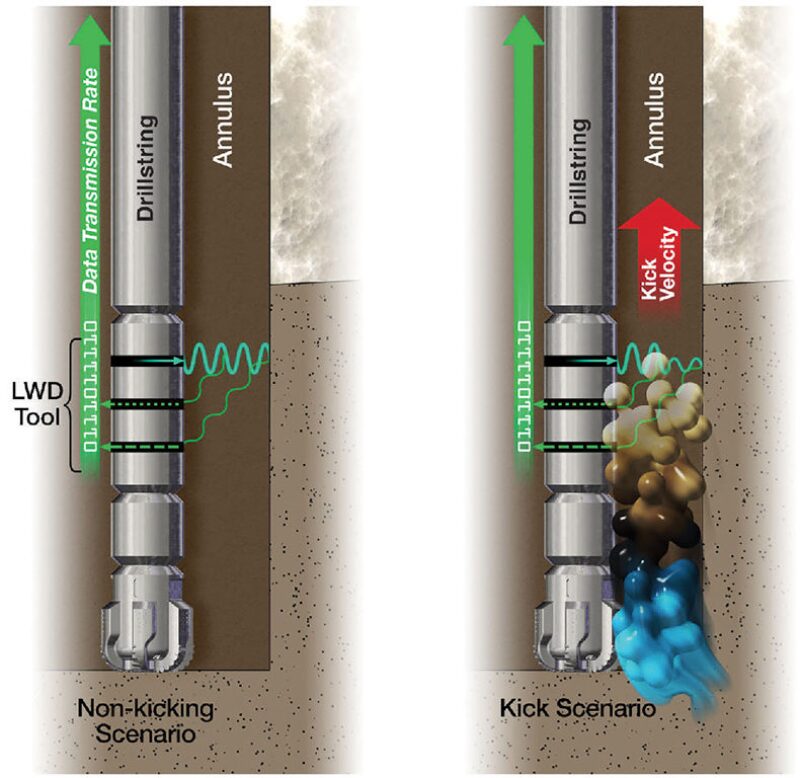
In most cases, downhole tools communicate up to the rig using mud pulse telemetry that transmits information at the speed of sound. In a well with a total depth of 10,000 ft, it would take just under 2 minutes for the signal to reach the driller. And the NETL team predicts that in the worst case scenario where kick is rapidly traveling up the riser, its approach could provide about 15 minutes of warning time for the crew to react.
The deeper the well and the slower the kick is moving, the longer the warning time provided by the system. Research on how kicks move has only recently begun. Some kicks remain static, while others migrate upward at rates that span minutes and hours.
With math and physics on their side, finding operators to provide more data has become the hard part for the NETL researchers. Historically, the industry has shared very little about the prevalence of kicks and does not document these events systematically. Rose said she believes that if companies open up more, they would benefit by advancing the development of new ways to address kicks.
“There is a treasure trove of data and information that operators could be collecting and disseminating” about kicks, Rose said. “But because of their commercial perspective, they tend to ‘tight hole’ that information.”
Moving forward without kick data from the operators, the next step for NETL is to create experimental data to play “what if games” to further validate and refine its approach. The team also wants a final product that not only detects a kick, but also identifies its makeup in terms of gas, oil, or water and then quantifies the volume, something the team calls kick fingerprinting.
For Further Reading
OTC 25847 Kick Detection at the Subsea Mudline by E. Toskey, Letton Hall Group.
SPE 173052 SMART Kick Detection; First Step on the Well Control Automation Journey by J. Brakel and B. Tarr, Shell, W. Cox, Noble Drilling Services et al.