Industry proponents and many leading academic institutions agree that natural gas is the safest, cleanest-burning bridge fuel capable of heralding the alternative energy market of the future. One risk in the development of this resource involves the inevitable leakage of methane. As a greenhouse gas (GHG), methane is considered more detrimental than carbon dioxide (CO2).
In current field operations, the industry is working diligently to lessen the environmental footprint of CO2 throughout the development of shale gas facilities. Lower emissions, methane utilization, and profitability are driving new ways of handling natural gas at the surface.
A Question of NumbersSeveral recent studies have highlighted methane leakage as a major challenge for shale development in the US and abroad. Robert Howarth, David R. Atkinson Professor of Ecology and Environmental Biology at Cornell University, contends that this aspect alone makes both shale and conventional natural gas twice as harmful to the environment than coal for future greenhouse gas emissions. His opinion is contested by both academia and industry. A number of subsequent reports from institutions such as the American Petroleum Institute and America’s Natural Gas Alliance, IHS/Cambridge Energy Research Associates (CERA), Devon Energy, and from competing faculty at Cornell display numbers much lower than those espoused by both Howarth and the Environmental Protection Agency (EPA). At the root of this debate lies the EPA’s Greenhouse Gas Inventory published in 2010. The methodology used for the report inferred that each unconventional gas well completion emits an average of 9,175 Mcf of methane, of which 51% is flared with the rest being vented. The EPA estimated that, on average, 4,587 Mcf is produced during the completion of every unconventional gas well in addition to the same amount of gas vented for each unconventional gas workover. According to a report published by IHS/CERA, the EPA’s analysis bases assumptions on activity that conflicts with industry practice and standard health and safety considerations at the wellsite. Namely, the numbers associated with the EPA report reflected gas captured through several green completions. An assumption was made that this same amount would be leaked where green completions were not used. The real numbers are unknown because the lack of emission reportage, which is voluntary, prevents a detailed analysis. While many of these reports include wider sampling of well data, it may be some time before an actual number can be attributed to methane leakage. The rate of methane leakage is identified as being within a range of 2 to 8% of total production. Industry proponents assert that the 8% range is erroneous because of the use of extremely limited data within the EPA. Environmental proponents assert that the EPA numbers are low. Lawrence Cathles, a Cornell professor, came out against Howarth’s findings with his commentary on Howarth’s 2012 background paper. Cathles cites the Devon Energy report as one of the most significant sources of information for determining actual rates of methane leakage. The Devon Energy study surveyed eight companies and around 1,600 wells. The report assessed that, of 6.5% of the wells that were not green completed, approximately 54% were flared. Only 3% of the wells covered in this study vented any methane into the atmosphere. The report estimated the maximum venting rate on an average of 765 Mcf/well completion. “If you multiply that by the 3% of the wells that were venting at that rate, you get a leakage rate that is very similar to the leakage rate for conventional wells, and everybody agrees that leakage for conventional is negligible,” Cathles said. “A leakage rate between 1 and 3% total production is considered a reasonable range; although, the current leakage rate is unlikely more than 2.5%,” he said. |
The real question remains, “How will new technology play a role in facilities management to avoid the unnecessary leakage of methane during the development phase?” While flaring remains an efficient, low-cost method of mitigating methane gas, many operators are looking at utilization as a way to cut down on the overall environmental footprint of their operations and as a way to capitalize on a resource otherwise “wasted” through flaring. The debate continues as to the percentage of total production leaked during standard shale operations, although the impetus for the industry is to utilize gas rather than waste it.
Industry Perspective, Solutions
As a resource, methane has an economic value. Until recently, operators were limited to venting or flaring when drilling exploration wells in undeveloped areas. “In the data I have seen from Williams and others in the Piceance (not a shale), initial difference for the first few wells was around 8%; but, once the pipeline was in, the development wells settled in as 1 to 2% total losses with transmission included,” said George King, distinguished engineering advisor with Apache.
King added, “Many operators, like XTO in the Barnett, even reduced that by not flowing back fracs in some areas until tubing could be run and separators and pipelines were in place and hooked up.” Operators are driven to capture methane whenever feasible. The highest production rates of a well come in the first month or two, which is how the simulations in a shale area are designed (i.e., with consideration for a fast return on investment). According to King, “In pre mid-2008, the gas price was USD 8 to 10/Mcf. From an economic standpoint, would anyone waste 8% of a shale well’s average 2.5 Bcf by needless venting or flaring?” This number equates to roughly USD 2 million/well. “Even at today’s price of USD 2.50/Mcf, that’s about a half million dollars per well,” King said.
Venting vs. Flaring
The industry has moved away from venting methane in its raw form in exchange for flaring, which transforms the gas to CO2 with a 98% efficiency. King said, “From a quick survey of flow tests on exploratory wells, the amount of flaring from a shale gas well prior to pipeline contracting and construction is perhaps between 0.5 and 1% of total gas produced.” He adds, “The gas lost from a development well is very roughly between 0.1 and 0.5% of the gas in place.” The lower number is attributed to the availability of facilities and pipelines for transmissions. In addition, development wells often have the highest potential flow because the estimated ultimate recovery is often four to six times more gas than exploratory wells before completions application.
“The main losses in development wells are from gas in the circulated fluids and water while drilling out plugs and in the slug flow of gas and produced water in the first 2 to 5 days that would overwhelm a separator,” King said. These gas losses can be minimized once the well flow can be turned to the separator. “Portable separators and gas busters in combination with low-pressure recovery systems, especially in a pad development, can make significant reductions in the true lost and unaccounted for gas volumes,” King said.
According to King, “One problem that the industry does need to address is the venting of methane caused by blowing down a well or rocking a well to remove water that condenses from the gas during production or moves into the wellbore with the gas flow.” This process is standard for both conventional and unconventional wells. It is especially common in older conventional well completions with very low flow rates. As gas flow rate declines, the gas is no longer moving fast enough in the well to lift the water out of the well. As this water level builds, it holds a backpressure on the formation, further decreasing gas flow. Opening the well at the surface for a short time decreases the built-up pressure at the surface and enables a sudden flow of gas, which forces the water out of the well and returns it to production. The gas is often vented. “Equipping these wells with small, specialized, intermittent low-flow-rate lift systems would prevent the need for blowdown,” King said. “Horizontal wells will be more difficult to lift, and this requires work to find an optimum lift system,” he added.
Flaring is the preferred method for mitigating methane during the well testing phase. Although this method is less detrimental from a GHG perspective when compared with venting, it has fallen under scrutiny in many of the US shale plays. Flaring is a loud process. In addition, the abundance of flame often brightens the night sky. In urban areas, visibility of ongoing flaring can incite a negative public perception and brings safety concerns to local communities. As identified by a recent American Petroleum Institute report, areas such as liquid unloading and flowback after completions and refracturing are unlikely candidates for flaring. The industry is currently moving toward advanced technologies that promise to mitigate methane venting, reduce flaring, and utilize gas on site as a means of lowering both emissions and operating costs.
Flaring vs. Utilization
With flaring under more scrutiny both politically and publicly, more operators are finding ways to use flare gas rather than waste it through burning. While flaring remains an efficient mitigation strategy against releasing methane, it adds nothing to the bottom line for ongoing operations. Developing localized processing plants, capturing the gas during flowback, and using flare gas to offset diesel usage or to generate electricity are just some of the options applied by operators to prevent methane release and to lower overall emissions. This is leaving a smaller net resource of waste gas to contend with in facilities.
Green Completions. Reduced emissions completions (REC), or green completions, is one of the fastest growing technologies in shale development. As pointed out by several studies now available, liquids unloading is one the biggest contributors to methane release during unconventional resource development.
New wells and workovers are completed by producing fluids at a high rate to lift excess sand to the surface and to clear the wellbore to increase gas flow. Typically, the gas/liquid separator installed for normal well flow is not designed for this high-rate, three-phase (gas, liquid, and sand) flow. A common practice for the initial well completion has been to produce the well to a pit or tanks where water, hydrocarbon liquids, and sand are captured and slugs of gas vented to the atmosphere or flared. Completions can take anywhere from 1 day to several weeks, during which time a substantial amount of gas may be released to the atmosphere or flared.
Since 2000, a number of operators have deployed REC technology as a means for lowering emissions and capitalizing on early production. REC uses portable equipment specially designed and sized for the initial high rate of water, sand, and gas flowback during well completion.
Sand traps remove the finer solids present in the production stream. Plug catchers are used to remove any large solids, such as drill cuttings, that could damage the other separation equipment. A critical aspect includes the piping configuration to the sand traps. Abrasion from high-velocity water and sand can erode steel pipe elbows, creating a washout resulting in water, sand, hydrocarbon liquids, and gas in an uncontrolled flow to the pad.
Depending on the system, dehydration may be a necessary step before the produced gas enters the pipeline. The gas can be routed to a permanent glycol unit for dehydration or a portable desiccant/glycol dehydrator used for dehydration during the completion process.
A three-phase separator is used to remove free water and condensate from the gas. Condensate is collected during the completion process and sold for additional revenue. Temporary piping may be used to connect the well to the REC skid and gathering system if the permanent piping is not yet in place.
Green completion equipment is only necessary for the time it takes to complete the well. Operators typically transport this system from site to site to be used in a number of well completions, often on a truck-mounted skid.
Depending on the basin and the operator, some companies have opted to build their own units while others prefer to use a third-party service provider. Devon Energy has used REC voluntarily since 2004. The company has since reduced methane emissions in its Barnett shale operations by 25 Bcf of gas. The company uses the same process to complete wells in New Mexico, Wyoming, Oklahoma, and south Texas. The company reports that it has completed more than 2,000 green completions to date.
Encana uses green completions around 90% of the time, even in areas where the technology is not mandated. According to Doug Hock, Encana spokesman, “In areas where there isn’t sufficient infrastructure, we would utilize flaring.” He added, “Green completion technology is required in Colorado and Wyoming, and, although it’s not required in Texas and Louisiana, we do it there as well.”
REC is fairly standard for many unconventional plays. As the technology becomes more available, it will continue to bring gas to market and lower emissions. This technology is not a viable solution for exploration areas with limited infrastructure, but, in developed areas, it has grown to be an efficient means of mitigation (Table 1).
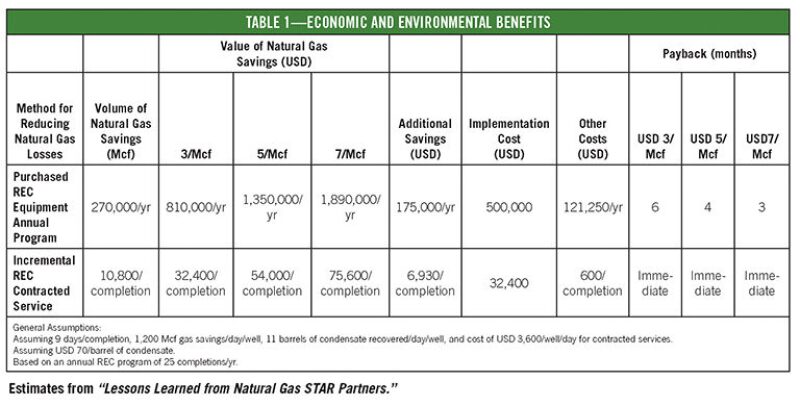
Bi-Fuel Systems. Another technology that has affected the use of flare gas is the use of natural gas in standard diesel generators. Bi-fuel systems are rapidly expanding in areas such as the Bakken where Statoil currently runs 10 of its rigs with bi-fuel generators. Continental Resources and ConocoPhillips have also committed to bi-fuel systems.
The bi-fuel system is a retrofitted design that allows a standard diesel generator to operate on up to 70% natural gas (Fig. 1). “With diesel costing an average of USD 4/gal, these operators in the Bakken are using 60% natural gas at around USD 0.40/gal equivalent,” said Jeff Anderson, regional manager at Eco AFS, a distributor for the GTI Altronic technology.
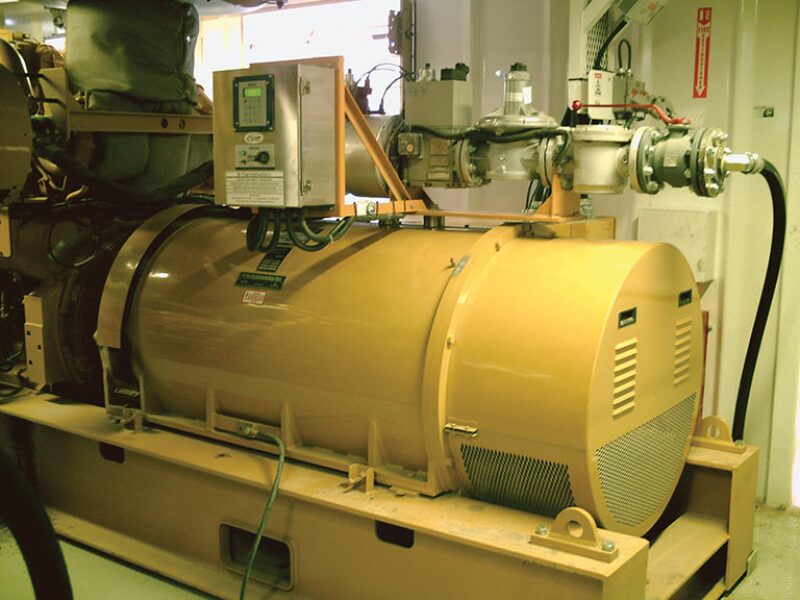
“There are multiple reasons for using a bi-fuel system,” said Lance Langford, vice president of Bakken, Statoil. “In most of these resource plays, gas pipeline capacity is an issue,” he added. Statoil’s gas production in the Bakken has grown rapidly, even though it is an oil field. “We’ve been pretty fortunate; we have pipeline capacity,” Langford said. “Even if you have plenty of capacity, a bi-fuel system does two things: it saves you money, and it lowers emissions,” he added.
The operator hopes to have all 16 of its rigs running on bi-fuel systems by the first quarter of 2013. “We’ll replace about 60% of our diesel with natural gas, which is around 1,800 gal/rig,” Langford said. This will equate to a savings of around USD 3,000/rig/day, with an expected gas price of around USD 3 to 3.50/Mcf.
“On top of the savings, you also reduce emissions,” Langford said. The company has reduced its emissions on bi-fuel rigs in the Bakken by half by substituting diesel with natural gas. “In lots of these areas, when you have all these new wells coming on, you have limited capacity, so you are flaring a portion of your gas,” Langford said. Rather than flaring, Statoil is using the gas, which is providing a substantial savings for the company. “That is additional savings because you’re paying yourself back plus the mineral owners on that gas that might otherwise be flared,” Langford said. For each rig, the bi-fuel system burns approximately 250 Mcf/day. In all, when Statoil has outfitted its 16 rigs, it will achieve a daily cost reduction of USD 48,000/day.
“In the Bakken, there are thousands of diesel engines running 24/7. I would be less concerned about the flared gas than the diesel emissions,” said Anderson. Bi-fuel systems are a small but important way that operators are preventing methane emissions.
“I think we’ll do away with flaring in the Bakken,” Langford said. Pipeline and gas plant construction will eventually offset this process. “It makes sense economically to switch to bi-fuel systems even if you are not flaring gas,” Langford added. The company plans on expanding its bi-fuel use to other equipment, such as fracturing pumps, when the technology becomes available.
Electric Generating Turbines. Another element that is relieving facilities pressure in the unconventional market is the process of burning flare gas to generate electricity. King said, “Apache is contracting with an operator of electric generating turbines powered on field gas to generate power for some of its drilling rigs in Oklahoma and is looking at it for other areas as well.”
Statoil is also using this technology in its Bakken operations. “We have a pilot program where we can’t get pipelines into the city limits in Williston, North Dakota.” The operator is using microturbines to generate and sell electricity back to the grid and to use on site. “In addition to bi-fuel systems, we are looking at the possibility of going 100% electric for operating some of our rigs,” Langford said.
Generating electricity from natural gas that would normally be flared is an efficient way of mitigating emissions, but the technology is marginal. “I think it’s going to be more about reducing emissions and, if we are lucky, maybe some profit,” Langford said.
Capacity is an issue for the microturbine as setup requires some foreknowledge of available resource. A typical gas field will have both strong and light production. Mobilizing the proper number of microturbines could prove difficult with varying production levels.
Many operators are looking for ways to decrease their environmental footprint. “I think we’re all working hard on a multiple of fronts,” Langford said. “We are all looking at technologies from both directions, lowering our cost structure, and reducing emissions,” he added.
Looking Ahead
The release of methane is an economic waste for most operators. With current efforts to continuously improve and innovate the process, best practice operations are reducing gas loss, especially in pad developments, to about <0.1–0.5% of total production, although this still needs improvement. “The technology for sharply reducing methane losses is known—every issue about methane release can be handled with technical solutions, and innovation in the field will improve it if the operator is a learning organization,” King said.
For Further Reading
IHS CERA. Mismeasuring Methane: Estimating Greenhouse Gas Emissions From Upstream Natural Gas Development by L.M. Barcella, S. Gross, and S. Rajan.
API, ANGA. Characterizing Pivotal Sources of Methane Emissions From Unconventional Natural Gas Production by T. Shires, URS, and M. Lev-On, The Levon Group.
Geochem. Geophys. Geosyst. Assessing the Greenhouse Impact of Natural Gas by L.M. Cathles.
National Climate Assessment. Methane Emissions From Natural Gas Systems by R. Howarth, Cornell University, D. Shindell, NASA, R. Santoro, Cornell University, et al.
EPA. Lessons Learned From Natural Gas STAR Partners: Reduced Emissions Completions for Hydraulically Fractured Natural Gas Wells. http://www.epa.gov/gasstar/documents/reduced_emissions_completions.pdf
Estimates from “Lessons Learned from Natural Gas STAR Partners.”