Flow-induced vibration (FIV) from high-velocity multiphase flow is a common source of vibration concern in process piping, potentially leading to fatigue failures and hydrocarbon leaks. A combination of computational fluid dynamics (CFD) and finite element (FE) modeling offers a potentially powerful tool for assessing and diagnosing multiphase FIV problems in hydrocarbon-production piping systems.
Global energy consultancy Xodus Group performed FIV studies on an Equinor-operated topside production system, carrying multiphase flow at high-pressure (approximately 69 bara) conditions, where significant vibration was measured. The study assessed different vibration-simulation methodologies, combining FE analysis with forcing functions based on both correlations and CFD simulations. The aim was to gain a better understanding of the accuracy and limitations of calculation methods typically used to assess fatigue.
Calculating Multiphase FIV in Operational Pipework
While CFD FIV modeling methods have been well validated against low-pressure water-airflow under laboratory conditions (Emmerson et al. 2016a and 2016b), little has been published to show how well these techniques perform for operational hydrocarbon-production systems. As these systems usually operate at higher pressures with complex, live hydrocarbon fluids and water, the process conditions are often not well defined. They typically incorporate several features that could complicate the vibration-generation mechanisms such as long upstream pipelines, chokes, and convoluted combinations of pipe bends with complex support arrangements.
As part of the development of a new Energy Institute guidance document for subsea pipework, the project with Equinor was instigated following a joint industry project (JIP) established by Xodus, in collaboration with TNO and funded by six major operators, to improve techniques for estimating forcing functions in liquid-gas flows.
Vibration measurements were taken at various locations on a section of piping carrying multiphase flow at high-pressure conditions (approximately 69 bara) (Fig. 1). The forces were applied in harmonic, transient, and fluid structural interaction (FSI) simulations (directly coupled FE and CFD).
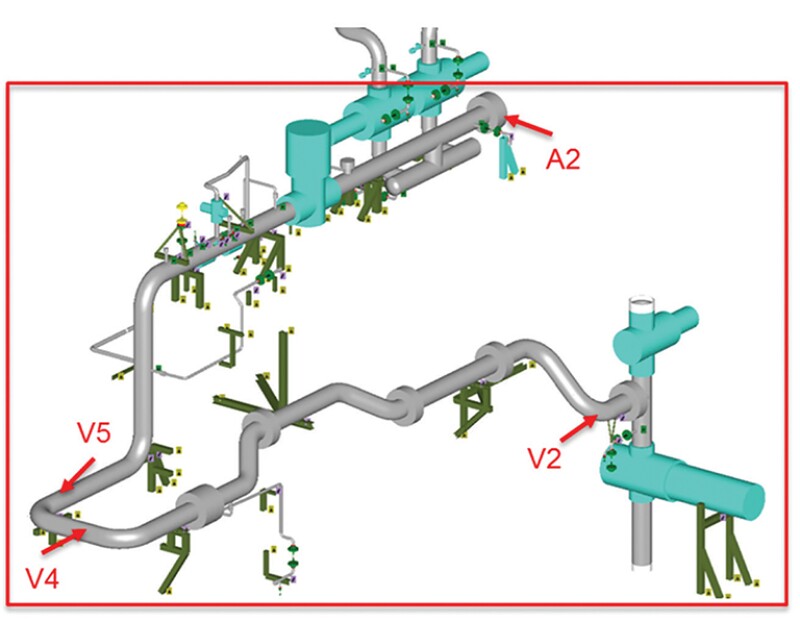
The topside piping arrangement consists of 16-in. schedule-100 piping, with a tee at the top of a riser section followed by six 90o and four 45o 1.5 R/D elbows and is reasonably well supported (as shown in Fig. 1).
The measurements provided the vibration velocity of the piping structure, and frequency spectra analysis was performed for comparison with the structural-response simulations. The main locations of interest are V4 and V5 as the measured vibration was the highest here. The peak vibration velocity at V4 is 4.7 mm/s and this occurs at 5.1 Hz in the EW-Y direction (Fig. 2), while at V5 the peak is 6.4 mm/s at 5.2 Hz.
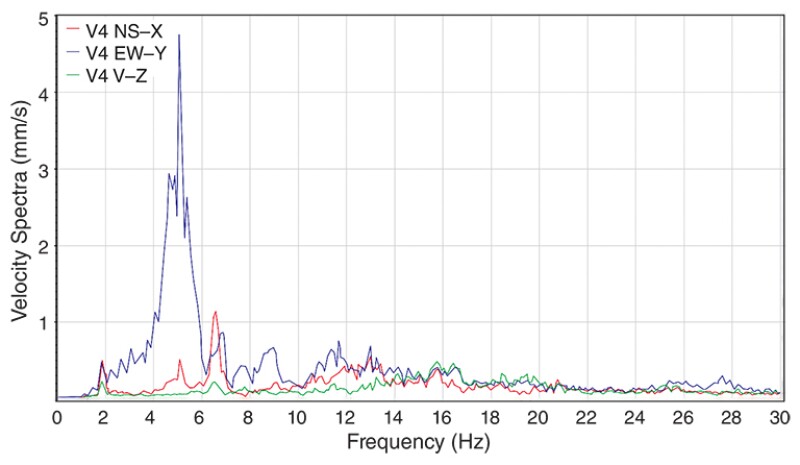
Method
Fluid forces based on either correlated test data or those calculated in the CFD simulations were used as inputs for FE simulations to predict the structural response of the pipework. These vibration predictions were then compared to the vibration measurements.
Fluid forcing predicted using CFD analysis. Siemens PLM STAR-CCM+ was used to perform all the CFD simulations. The geometry was split up so that the forces on individual bends could be calculated. The volume of fluid (VOF) multiphase model was used for all the simulations, and the resolution of the interface between the liquid and the gas was improved by the high-resolution interface capturing (HRIC) approach.
The gas phase was modeled as compressible using the ideal gas equation, while the liquid phase was modeled by combining the hydrocarbon liquids and water into a homogeneous mixture with a constant density and viscosity. The fluids were modeled as isothermal, i.e., temperature changes were assumed to be negligible. The simulated time period was 30 seconds to give enough data on which to perform the analysis.
Fluid-forcing approaches. The approach for applying fluid forcing varied depending on the type of FE modeling.
For the harmonic FE analysis in the frequency domain, forcing functions were applied as two-slope power spectral densities (PSD), which were based on correlated test data developed as part of the JIP work (Belfroid 2016 and 2019). These forcing functions were also modified based on the CFD-predicted forces, and both of these approaches were investigated.
There is a range of possible ways to adjust a typical two-slope forcing function to approximate the CFD predictions. It is clear that, regardless of the chosen fitting parameters, the two-slope method does not replicate the CFD predictions very well below approximately 8 Hz (Fig. 3). This is important, given that the first two Eigenmodes of the pipework are 4.5 and 5.8 Hz. The JIP correlation gives considerably higher forces below 2 Hz, as is borne out by the relative PSD values at f0, which are three and six times greater than the CFD-fitted curve.
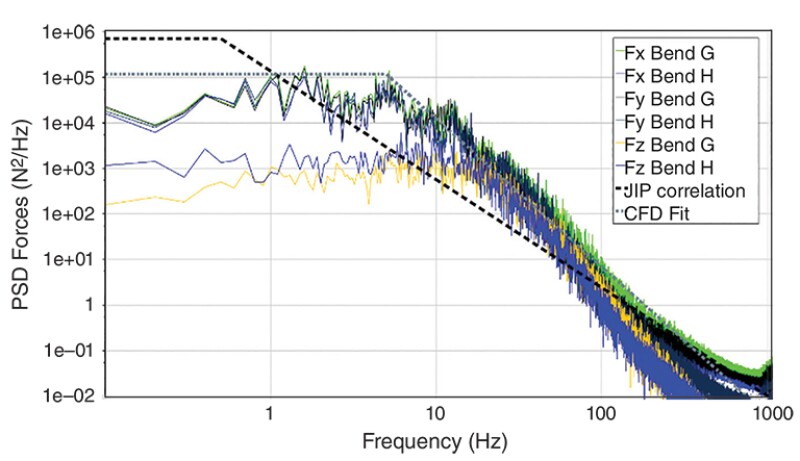
FE modeling. The objective was not to produce a highly accurate FE representation of the as-built pipework. Instead, it aimed to get the frequency response of the structure about right compared to the frequency spectra of the vibration measurements.
FE models were built using both ANSYS mechanical and STAR-CCM+, using piping elements and solid elements respectively to represent the piping system. The extent of the FE domain was the same as the CFD domain. As a starting point, a modal analysis was performed to quickly investigate structural frequencies using different representations of the supports. The piping-element model was run in two ways, with the fluid forces applied in the frequency or time domains.
The Rayleigh damping approach was used with coefficients, which give a damping ratio of approximately 2% at 5 Hz (first Eigenmode).
Low-Pressure vs. High-Pressure Prediction of Fluid Forces
The CFD analysis was repeated at 1 bara with the same mixture velocity and liquid-volume fraction. Except for the change of pressure and inlet-flow conditions, the CFD setup was identical to that used for the high-pressure analysis. The PSD of the forces on the bends are plotted in Fig. 4.
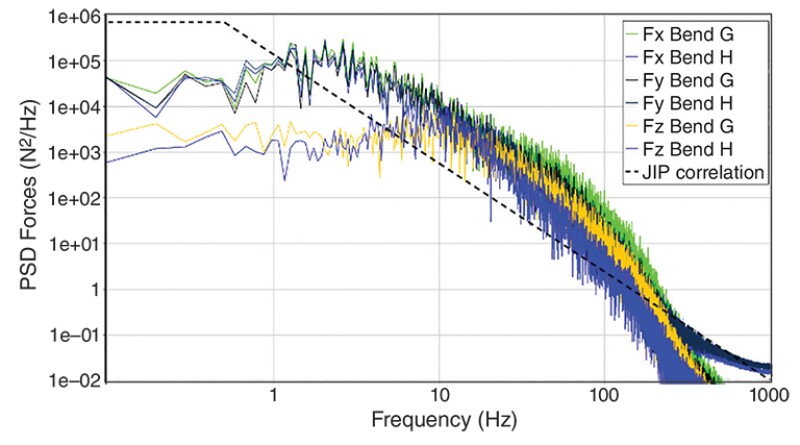
The frequency spectra for the low-pressure results is more focused on the low frequencies, with one main peak at 2 Hz compared to several peaks for the high-pressure results at 1.5, 5, and 9 Hz. The correlation based on the multiphase FIV JIP experimental data are independent of pressure, only depending on the gas-void fraction, mixture velocity, and pipe diameter; so in this case, the peak f0 value is 0.5 Hz at both low and high pressure.
Detailed comparison of the gas-volume fraction through planar sections indicates that the wisps of liquid are generally a bit larger and sparser at low pressure, with more of them hitting the bend walls as shown in Fig. 5.
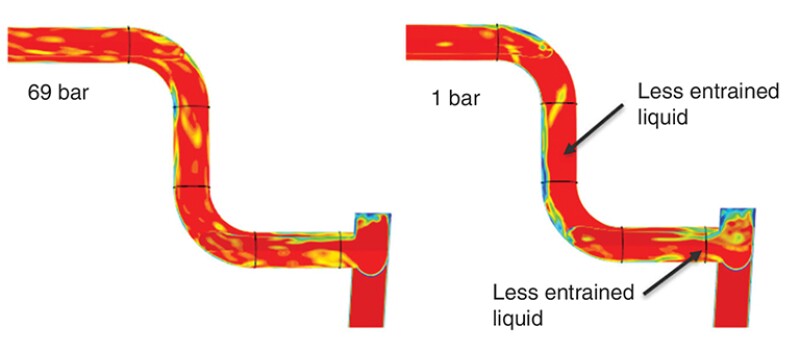
The high-pressure results indicated relatively small wisps of liquid, many of which did not have sufficient momentum to hit the walls of the pipe bends and are simply transported with the gas. The density difference between the gas and liquid is reduced compared to low pressure. A simulation without the riser showed that this stripping behavior influenced the higher-frequency content in the force spectra.
At high pressure, the momentum of the gas is increased relative to the momentum of the liquid (due to a reduced density difference). This tends to generate smaller liquid droplets and a more homogenized multiphase mixture that behaves more like a single-phase fluid. The JIP correlation does not account for this effect.
The detailed results comparing the measured and predicted vibration at V4 and V5 locations on the pipework with regards to the following criteria are provided in the full technical paper:
- Structural-response analysis
- Time-domain analysis
- Fluid forcing
- Structural response
In summary, using different forcing functions for a harmonic FE analysis produced very similar predicted vibration-spectra shapes, which compared well with measurements, but the magnitudes varied significantly depending on the shape of the forcing PSD. The measured peak velocity at location V4 was slightly over-predicted for the JIP correlation forcing function, but significantly over-predicted for the CFD-fitted forcing PSD. The magnitude of the predicted vibration depends on the forcing magnitude close to the dominant structural frequency; and this explains why the forcing function with a peak frequency closer to the structural frequency (the CFD-fitted forcing PSD) produces larger vibration.
When forces calculated in the CFD simulation were applied to the transient FE model, the predicted peak-vibration velocity was over-predicted by about three times compared to the measured vibration.
It is important to understand that the vibration predictions in this study are made using a combination of both CFD and FE models, and both need to be accurate to provide a good result. The key findings of this work include:
- It is important to model pipe supports accurately. It should be appreciated that, in a real-life offshore piping system, some supports may be ineffective, damaged, missing, or modified.
- In this study, solid-element and piping-element FE simulations produced similar results, with piping-element models requiring considerably fewer computing resources. However, in more general applications, piping elements should be used with caution, as they might not predict local stresses to a sufficiently high level of accuracy.
- Frequency-domain analyses tend to assume identical forces on all bends, with no phase relationship. This study has demonstrated that the phasing of forces and the variation in forces between bends can be important.
- Given the advances in computing power, these types of calculations can be carried out in reasonable timescales.
Conclusion
A combination of CFD and FE modeling offers a potentially powerful tool for assessing and diagnosing multiphase flow-induced pipework vibration problems in hydrocarbon-production systems. Previous work has shown that CFD simulations can predict fluid forces in low-pressure water-air flow loops under laboratory conditions. This work has shown that, for a real-life piping system operating at elevated pressures with a complex mixture of hydrocarbon fluid and water, the various simulation methods considered compare reasonably well with measurements. All methods over-predict vibration while reasonably accurately estimating the peak vibration frequency.
Care is required when undertaking this type of analysis. It has been shown that it is important to have an accurate FE model of the as-built pipework and supports. Equally important is the forcing function which is applied to the FE model, which should accurately represent the fluid forces on the bends. In this case, the magnitude and peak frequency of the forcing function had a significant influence on the response of the structure.
Forcing functions based on correlated data from tests at low pressure should also be used with caution for high-pressure systems because multiphase flow behavior differs depending on the gas density. In addition, the inclusion of phasing of the forces at each bend can have an effect on the structural response, and simulations performed in the frequency domain do not consider this.
The consequences of inaccurate predictions of piping vibration vary, but for a fatigue assessment it could significantly affect life estimates (and hence operational safety), or production-rate limits (which may significantly impact operational profitability).
References
Emmerson, P.R., Lewis, M.J., and Barton, N.A. 2016a. Slug Flow JIP. Presented at the 11th International Conference on Flow-Induced Vibration, The Hague, The Netherlands, 4–6 July.
Emmerson, P.R., Lewis, M.J., and Barton, N.A. 2016b. Influence of Multiple Bends for Multiphase Flow-Induced Forces in 6” Piping: Measurements and CFD Analysis. Presented at the 11th International Conference on Flow-Induced Vibration, The Hague, The Netherlands, 4–6 July.
Belfroid, S.P.C., Nennie, E., and Lewis, M. 2016. Multiphase Force on Bends—Large-Scale 6” Experiments.Presented at the ATCE, Dubai. SPE 181604.
Belfroid, S.P.C., Gonzalez-Diez, N., and Pereboom, H. et al. 2019. Multiphase Flow-Induced Forces on Bend Structures. OMAE2019-96387.
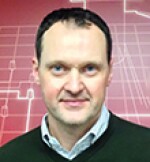
Paul Emmerson, principal consultant at Xodus Group, has 26 years of experience applying analytical and CFD modeling skills to solve complex fluid and thermal engineering problems. He is an expert in CFD, flow modeling, and piping vibration and has published numerous papers at conferences and in technical journals. He can be reached at paul.emmerson@xodusgroup.com.
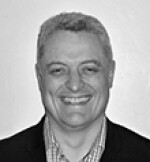
Mike Lewis, global lead CFD at Xodus Group, is a recognized expert in the field of CFD, finite-element analysis, and vibration-mitigation engineering with over 25 years’ experience. He can be reached at mike.lewis@xodusgroup.com.
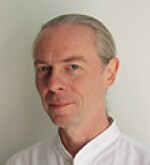
Neil Barton, consultant engineer with Xodus Group, is an expert in multiphase flow and CFD flow modeling, with specialties in pipework vibration and sand-particle erosion. He began his career at British Gas, moving to the National Engineering Laboratory, and then Xodus. He can be reached at neil.barton@xodusgroup.com.
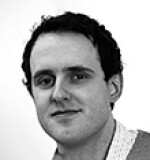
Steinar Orre, principal researcher in flow technology at Equinor ASA, has worked in the oil and gas industry for more than a decade and specializes in fluid-flow modeling, analysis, and piping vibration. He can be reached at storr@equinor.com.
Knud Lunde, advisor, flow technology, at Equinor ASA, is an expert in multiphase flow and piping vibration, having worked for Equinor in the oil and gas industry for several decades. He can be reached at knudl@equinor.com.