Australian technology developer MezurX is touting its newly introduced flow, density, and mud monitoring system as a significantly better alternative to the widely used Coriolis meter. Using an advanced set of sensors, the X-Omega provides real-time information that can be used on rigs for early kick detection and managed pressure drilling (MPD).
ruce Henderson, president and CEO of MezurX, claims the technology involves “a completely different way of measuring density and flow” while offering more reliability and a smaller footprint than Coriolis-based systems.
And despite the current price environment, Henderson said several service companies and offshore operators are showing interest in the X-Omega system and work has already been awarded. “It’s an interesting time for us,” he said. “I think that during a downturn in the industry, new technology is always attractive to keep costs down and make things more efficient.”
MezurX is listed on Chevron’s website as one of several firms the oil and gas major is funding through its venture capital division to promote the development of emerging upstream technologies.
The X-Omega was created by integrating the company’s proven flowmeter and pressure sensor technologies, along with software to interpret the data.
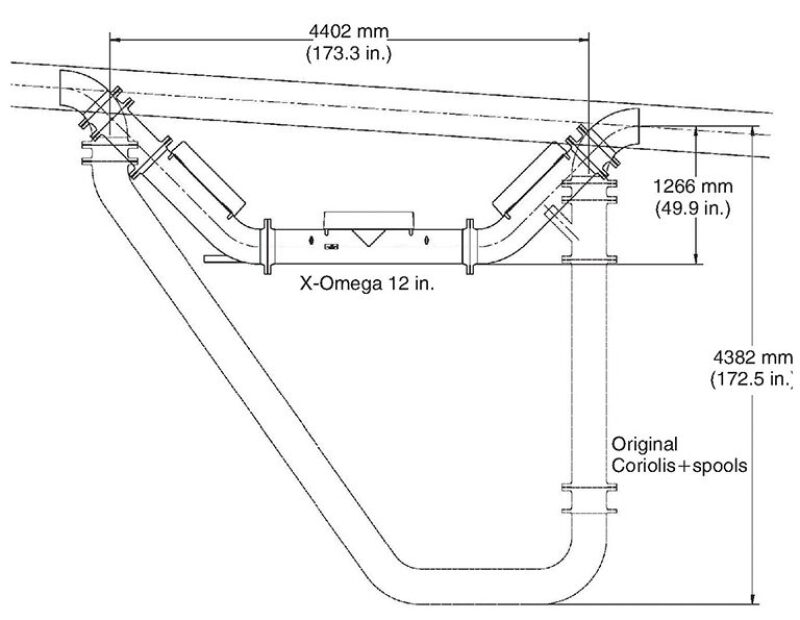
As drilling mud enters the system through a return flowline, the fluids are first measured by a density module that contains a pressure sensor, then a wedge-meter analyzes the flow velocity, and a second density module on the back end takes another pressure measurement. This simultaneous measurement of two parameters delivers real-time flow data required for MPD operations, as well as early kick detection, and reduces nonproductive time.
Coriolis meters used on offshore rigs typically require height clearance of about 14 ft vs. the 4 ft needed to install the X-Omega. The modularity aspect of the X-Omega system means it can be configured horizontally, vertically, or at right angles to address rig design. One benefit of this nearly-in-line capability is that the pressure drop in an X-Omega meter is about 35% less than a Coriolis meter of equivalent capacity because the internal passageways of the X-Omega have a larger diameter and have less obstruction, Henderson said.
The new system has yet to be used in the field, but Henderson said the company’s confidence relies on the established track record of its individual components, which have been used on rigs for various applications in identical drilling environments. The flow sensor has been used on offshore rigs to measure both oil- and water-based drilling muds. The pressure sensor technology has also been used offshore for early kick detection and undergone extensive testing at the company’s flow loop simulator in Brisbane, Australia.