Brant Bennion, in the Journal of Canadian Petroleum Technology Distinguished Authors series, titled his 1999 article on formation damage “The Impairment of the Invisible by the Inevitable and Uncontrollable, Resulting in an Indeterminate Reduction in the Unquantifiable.” This is a brilliant definition of formation damage because it reflects very well the lack of relevant data (in particular, permeability data) that are essential for adequate design of drilling and completion fluids. In addition, the opening sentence in Bennion’s article is as relevant today as it was in 1999: “Formation damage is a hot topic these days—with justifiable reason as we move to the exploitation of more challenging oil and gas reservoirs in tighter, deeper, and more depleted conditions.”
In order to avoid some of the detrimental effects of formation damage, a key aspect is laboratory testing of representative core material under representative downhole conditions. Thin sections, dry scanning electron microscopy (SEM), cryogenic SEM, and X-ray diffraction have been used for a number of years to identify the main damage mechanisms, mechanical or liquid, contributing to the observed returned permeability measurement from coreflooding. High-resolution images can be obtained from dry and cryogenic SEM, but they offer only a limited view at any one time. One technique that has been applied recently to identify and quantify potential formation damage is that of microcomputed tomography (CT). This provides high-resolution scans of whole plugs and allows, for example, the identification of changes in pore structure because of fines mobilization, and the visualization of the filter cake after cleanup, depth of mud solids, and filtrate invasion. The combination of micro-CT with techniques previously used for formation-damage analysis is providing new understandings in the interaction of drilling and completion fluids with core material.
One of the more frustrating aspects of coreflooding has been how to relate the results obtained to potential well-inflow performance. Computational fluid dynamics is one technique that appears to have bridged this gap. This technique incorporates the data obtained from coreflooding into a model that recreates the actual well geometry, depth of formation damage, mud thickness, and distribution of restrictions in the tubing, such as safety valves. With this approach, production rates can be obtained that provide useful insights into selecting appropriate drilling and completion fluids, for example.
Enjoy the papers selected. Formation damage is still a “hot topic.”
Additional Reading
SPE 165092 Case-Study Analysis of Formation Damage Induced by Brine Workover Fluid on Burcioaia Reservoir (Romania) and Research on Damage-Removal Methods by A. Dragomir, OMV Petrom, et al.
SPE 165169 Formation Damage and the Importance of a Rigorous Diagnostic: A Case History in Nigerian Deep Water by Jean-Noël Furgier, Total, et al.
SPE 169435 Integrated Analysis To Identify and Prevent Formation Damage Caused by Completion Brines: A Colombian Field Application by M.G. Jaimes, Ecopetrol, et al.
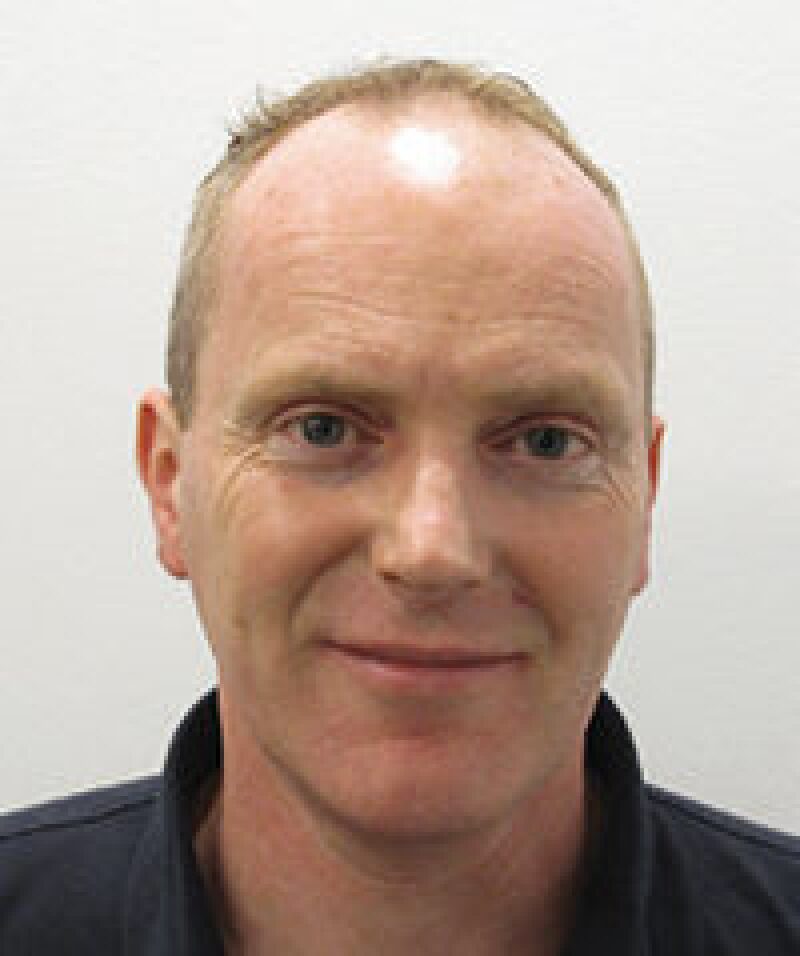
Niall Fleming, SPE, is the leading adviser for well productivity and stimulation with Statoil in Bergen, Norway. He has previously worked as a production geologist, chemist, and engineer. Fleming’s main interest is within the area of formation damage from drilling and completion fluids and from wells in production. He holds a PhD degree in geology from Imperial College London. Fleming has authored several SPE papers, is an associate editor for SPE Production & Operations, serves on the JPT Editorial Committee, and has been a member of the organizing committees for several SPE conferences and workshops.