Combining fracture and reservoir diagnostic analysis with integrated geomechanics and reservoir simulation is an efficient and cost-effective approach to generate realistic fracture geometry, understand fluid flow behavior, and define fracture-conductivity distribution in unconventional reservoirs. The complete paper presents a case study of integrated geomechanical and reservoir simulation with a developed fracture-conductivity-calculation work flow that was validated with diagnostic results to evaluate well spacing and completions design.
Introduction
This study extends that of previous authors by matching field fracture diagnostics and reservoir simulation using variable fracture conductivity. In the example used by the authors from the Hydraulic Fracturing Test Site 2 (HFTS-2) development, multiple fracture diagnostic methods were used to calibrate hydraulic fracture models. Once the model was calibrated, a new proppant-conductivity algorithm assigned conductivity values along the hydraulic fractures based on a physics-based model calculation of proppant concentration.
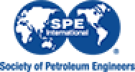