Mary Van Domelen makes two key points about using diverters in fracturing designs: “It is one of the useful tools in our unconventional stimulation tool kit,” and there is a good chance “you are doing it wrong.”
Those two observations motivated the engineering adviser from Continental Resources to write “A Practical Guide to Modern Diversion Technology” (SPE 185120), a 22-page overview on effectively using diversion to more effectively fracture a well by plugging the dominant fractures to divert the pressure further down the wellbore to ensure more perforations are effectively stimulated.
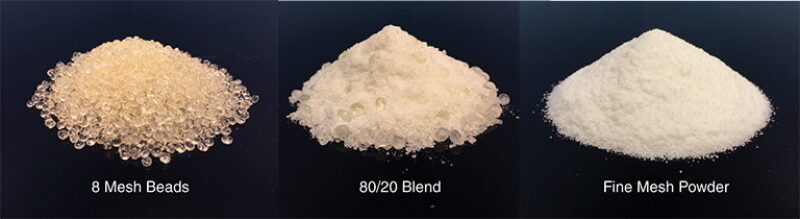
Van Domelen’s paper, presented at the 2017 SPE Oklahoma City Oil and Gas Symposium, is one of a spate of recent papers by operators that show diversion is becoming a widely used part of fracturing designs, particularly in the oil-rich Bakken. The papers are coming from unconventional pioneers such as Continental and Devon Energy, smaller operators such as Liberty Resources and Abraxas, and even Saudi Aramco. All report benefits from diversion, ranging from improved production and more productive fractures to cost savings.
Liberty reported (SPE 184828) that wells in the Bakken using diversion produced twice as much as offset wells using the old method, and “33% to 39%” more than predicted by a model that uses data from comparable wells in its database of more than 10,000 wells in North Dakota.
“We are excited about what we are doing,” said Paul Weddle, completion manager for Liberty, who presented the paper at the recent SPE Hydraulic Fracturing Technology Conference. “In the oil business, there are differences (of production) of plus or minus 10% to 15%” due to local geological variations. But with gains of more than 30%, “we may be on to something.” The earliest wells using diversion have been producing for a year and continue to exceed their expectations.
Diversion has been quietly used by early adopters—Devon’s recent paper was based on changes it made in its diversion method based on testing—but in the past year the number of companies trying and using it has grown substantially.
The rise has transformed the business of Jamplast, a private company that began selling degradable polymer particles for diversion back in 2005 when a large oilfield service company ordered some for testing, said John Moisson Jr., president and founder of the company.
It was a small line of business until 2014, when unconventional producers started using the material for refracturing older unconventional wells and completing new ones. Demand has grown so much in the past year that “today it is a major part of our business,” Moisson said.
For those doing the completions, diversion was added during a period of sweeping revisions in fracturing designs.
Many of the recent technical papers on the subject have been written by operators in the Bakken that used the drilling lull during the deep slump in early 2016 to totally reconsider how they complete wells.
A paper by Abraxas (SPE 184851) described how “a legacy Bakken completion design was set aside to make way for a ‘blank slate’ analysis.” Diversion was not on Abraxas’ initial list of possible changes. The process led to completions using significantly more water and proppant pumped at higher rates, sand instead of ceramic proppant, far longer laterals, and diversion to ensure that a dense array of perforations is stimulated more evenly.
Based on the reported results in SPE papers and in earnings presentations, the efforts have generally paid off, but change is often bumpy. “Early on we stubbed our toes a time or two and pressured a stage out,” because too much diverter was used, Weddle said. “But we are now seeing a lot of consistency and success.”
Improvements based on extensive reviews were “a silver lining” during a hard time, said Kyle Haustveit, a completions engineer for Devon, who was a lead author on a paper (SPE 184862) about how the company used an array of diagnostic tests to evaluate its completion designs, sometimes with surprising results.
By using multiple diagnostic tests it was able to improve its diversion by discovering that the diverter it was using was not diverting, and finding an effective alternative. The project demonstrated that there is a payoff for checking to see if you are doing something wrong.
Arguments over the value of diversion linger because it is hard to quantify its role in improved results. The problem is the many variables to consider and limited data available on production within stages.
A statistical analysis of 14 wells by Halliburton (SPE 179167) in 2016 found that the impact of diversion did not reach the level where it was “statistically significant” but the result did indicate it was “helpful rather than detrimental.”
There is no way of knowing if the results in the ground look like drawings showing rows of even fractures. But Weddle said the diagnostic testing and production analysis show more clusters are producing more efficiently, and ultimately, “production is our strongest metric.”
Adding Finesse
As more water and sand are pumped at higher rates to fracture long wells, diversion is needed to add some “finesse,” Van Domelen said. The finesse is required to more evenly spread millions of tons of sand among hundreds of fracture initiation points. For example, Liberty’s high-density perforation designs can have up to 15 perforation clusters in each of the 50 stages over a 9,500-ft lateral.
Diversion is not addressing a new problem. As long as companies, such as Devon and Shell, have been reporting what they have observed using fiber-optic cables to monitor fracturing, they have reported that the lion’s share of the water and proppant regularly flows into the first perforation cluster within each stage.
Dominant fractures, such as the ones shown in Fig. 1 from Devon, are a problem on multiple levels.
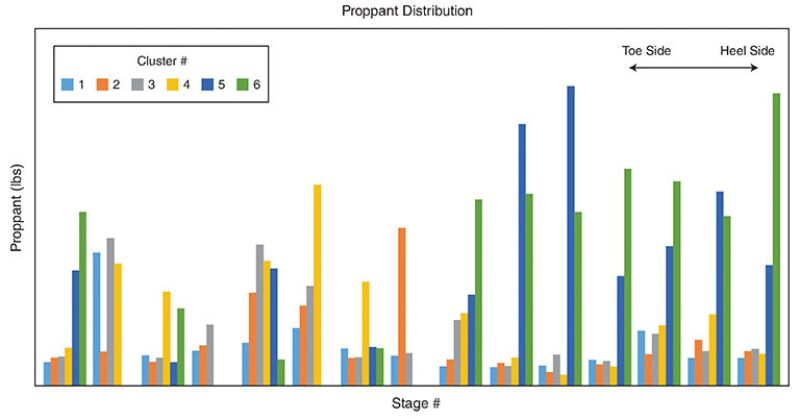
For one, the initial cluster takes in so much of the flow, it reduces the fluid to below the level needed to effectively fracture later perforations.
And a giant fracture is not likely to be a more productive one.
“I can’t get proppant that far out,” in a really long fracture to ensure it remains open and producing, said Clayton Smith, global director Research Development and Engineering for Pressure Pumping Services at Weatherford, adding that “there will never be any production from out there.”
Also, those long over-stimulated fractures are likely to extend to nearby wells, increasing the risk of damaging frac hits.
The most widely used hydraulic fracturing diverters finesse the problem by temporarily plugging dominant perforations by pumping pre-mixed volumes, or pills, of multisized grains of polylactic acid (PLA).
Relatively small volumes of diverter pills are dropped during short breaks in pumping proppant within each stage, The particles are supposed to follow the fluid flow into the dominant opening and form a plug that is strong enough to stand up to the hydraulic pressure—Weatherford has tested them up to 6,000 psi, and is pushing that higher—and afterward will go away by breaking down into a benign liquid.
Larger particles in the mix are designed to create a structure bridging the opening while mid-sized and smaller ones fill in the gaps. If the mix and the volume pumped are right, the diverter will block the dominant fractures sending the high-pressure stream down to undertreated clusters.
If the range of particle sizes is not right, it will not seal. If the total amount pumped is too low, it will fail to plug. Too much and it can block every perforation and stop the job.
One reason more companies are using diverters is that it costs a lot less than it used to. In recent years, the price has dropped by 80%, said Francisco Fragachan, director of sales and marketing for Weatherford Pressure Pumping Services.
Larger-sized particle types, such as flakes and pellets from Jamplast, are engineered to significantly reduce the volume of material needed in some openings, such as an uncemented well, Moisson said.
At this price point, Weddle said the additional time required to pump the diverter during each stage is the main cost consideration, not the cost of the material. He estimates the breaks added in the pumping for diverter drops adds about 6–9 hours per well. “It is still a very cost-effective way to drive performance,” he said.
Saudi Aramco is interested in using diversion as a way to stimulate significantly more perforations per stage, and saving money by reducing the number of stages per well. “It is more efficient and cost-effective to have more clusters per stage,” said Kirk Bartko, a senior petroleum engineering consultant for Saudi Aramco, during a presentation at a conference.
Unexpected Observations
When Devon Energy evaluated three different diverters in combination with different fluid formulas last year, it found that one option was often doing the opposite of what it was supposed to do by frequently accelerating the growth of the dominant fracture, one had no impact on the growth of the largest fracture more than half the time, and one was far more likely than the rest to control the growth of the biggest fractures (Fig. 2).
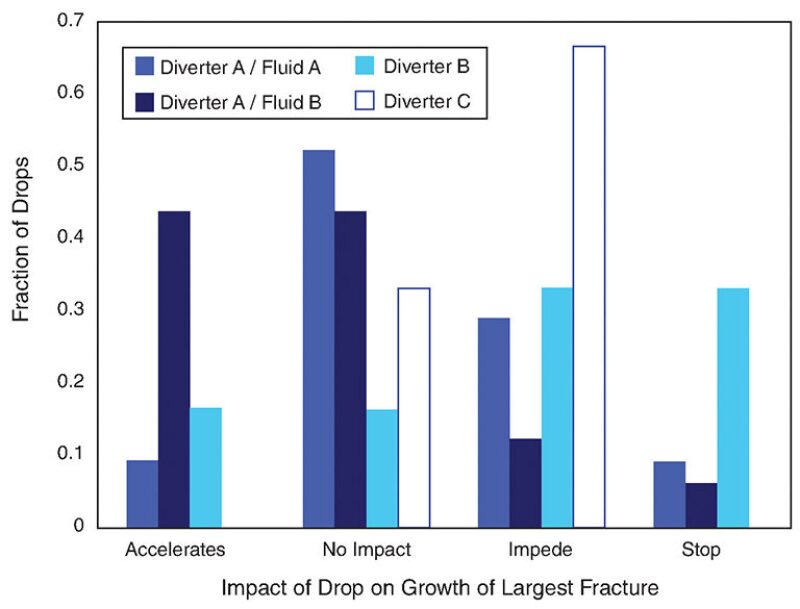
The combination of fluid and diverter most likely to halt growth, which is now regularly used, was identified only as diverter C, Haustveit said.
Details like that can be hard to find. Operators do not want to reveal anything that gives them an edge, and service companies are trying to sell their proprietary expertise.
“The design needs to be tailored to the need, to the conditions in the well. It is an engineering process, not a rule of thumb,” Fragachan said. He said the failure to think through a diversion design can be poorly performing wells, time and money wasted on added drops of diverter, or delays when too much diverter blocks all fracturing, forcing work to halt until the blockage clears.
Operators agree that some engineering is required, but it can be largely done in-house.
Based on experience and some calculations, Weddle said Liberty commonly uses a 50/50 mix of coarse (8 mesh)- and medium (20–70 mesh)-sized particles. Van Domelen suggested a mix of 25% coarse particles, 50% medium, and 25% fine PLA grains could be a good starting point.
Weatherford and the two biggest service companies, Schlumberger and Halliburton, have long sold diverters for acid stimulation and have made substantial investments in developing hydraulic fracturing diversion methods. While they are all selling diversion services and supplies, no company owns the PLA market, where there are multiple PLA particle-makers, some of which claim their version is superior for reasons that cannot be disclosed.
As someone who once worked for a service company developing diverters, Van Domelen appreciates the desire for a competitive edge, but the secrecy in this area casts a “veil of mystery over diversion.”
One key to creating a good seal is using a wide range of particle sizes in the mix, and Van Domelen’s paper offers a formula for that.
It is based on the method used to determine the mix of grains sizes needed to create a gravel pack that is permeable enough to allow oil to flow but not formation sand. She lays out a variation that inverts the formula to calculate the specification required to create an impermeable plug.
Diverter Design Guidelines
Source: SPE 185120. |
Pressure Test
There are databases to mine for diversion information, including FracFocus where companies disclose the chemicals used for fracturing, but ultimately each operator has to adapt what others have done to the well at hand.
The variables range from how the well was drilled and completed, to variations in the rock properties and stresses along the wellbore.
Liberty uses from 2 lb to 30 lb of diverter per stage, which is far less than it thought would be needed when it was researching how others did diversion.
The prime measure used to see if a diverter is actually diverting is the pressure change after a pill is dropped. If there is a sharp increase, it suggests the particles have blocked off the flow into the dominant fracture and the flow is now being directed elsewhere.
An example of that was in the Abraxas paper, which said “treating pressure data indicate that PLA granular diverter was highly effective,” in a wellbore that had not been cemented. That observation addressed a significant concern: Could the diverter particles create a plug if the space between the casing and reservoir rock has not been cemented?
Pressure response interpretation is not an exact science. During the fracturing conference, the pressure responses mentioned by presenters ranged from around 200 psi to well over 1,000 psi, leading to pointed questions about whether those readings really indicated the diverter was working.
Based on Devon’s work, pressure monitoring could be something people are getting wrong.
“So many times people are defining the effectiveness of diverters based on surface treating pressure alone,” Haustveit said.
The problem with that, as Devon has observed when using fiber-optic monitoring, are the instances when the pressure rises because diverters are doing the opposite of what they were supposed to do: “They screen out smaller fractures and accelerate the already dominant ones.”
“One of the first learnings was that fiber showed that surface treating pressure increases alone is not a good indication that the fluid flow was diverted away from the dominant fracture,” he said.
Weddle has studied those papers for the insights they offer, but the million-dollar cost of those sorts of studies is not in the budget yet for smaller operators like Liberty.
By using production analysis and radioactive tracers, Liberty concluded it significantly increased the efficiency of its perforation clusters considerably, he said. Tests showed efficient production from 12 to 13 clusters out of 15. That is better than average both in terms of the percentage producing, and the number because it stimulated more than twice as many clusters as many widely used designs.
Van Domelen agrees the surface pressure response alone is not definitive, but companies have to work with the data available. That includes monitoring nearby offset well pressures while fracturing. Those levels can indicate if diversion is helping to manage fracture growth within the limits of the completion design, reducing interactions with nearby wells.
Devon is also using lower-cost diagnostics that can be widely used. One promising option tested by Devon used pressure readings from multiple nearby wells to predict fracture growth.
Extreme fracture growth is increasingly being recognized as a problem as the industry works to reduce damaging frac hits among tightly spaced wells.
Continental’s completion supervisors log the pressure response after each diverter drop, with a goal of an increase of about 500 psi, which is the maximum. These observations are stored in a database that is used to analyze diversion performance, and compared with PLA particles from competing suppliers, Van Domelen said.
“Based on the data we look at, they are not all equal. You get different responses with different diverters,” she said.
Further Reading
SPE 185120 A Practical Guide to Modern Diversion Technology by Mary Van Domelen.
SPE 184828 Mining the Bakken: Driving Cluster Efficiency Higher Using Particulate Diverters by Paul Weddle, Larry Griffin, and Mark Pearson, Liberty Resources.
SPE 184840 Innovative Diversion Technology Ensures Uniform Stimulation Treatments and Enhances Gas Production: Examples From Carbonate and Sandstone Reservoirs by Zillur Rahim, Adnan Al Kanaan, Sayd Taha, Saudi Aramco, et al.
SPE 184862 New Age Fracture Mapping Diagnostic Tools-A STACK Case Study by K. Haustveit, K. Dahlgren, H. Greenwood, Devon Energy, et al.
SPE 184851 Re-Designing From Scratch and Defending Offset Wells: Case Study of a Six-Well Bakken Zipper Project, McKenzie County, ND by Peter Bommer, and Marc Bayne, Abraxas Petroleum; Michael Mayerhofer, Liberty Oilfield Services, et al.
SPE 179167 Improving Hydrocarbon Recovery in Sliding Sleeve Completions Utilizing Diverters in the Wattenberg Field by Jessica Fry, Halliburton; Erick Roach, Brett Kreyche, PDC Energy, et al.