Heavy oils are characterized by high density, high viscosity, and high-heavy-fraction components. Because of high viscosity and lower API gravity than conventional crude oil, primary recovery of some of these crude oil types requires thermal stimulation of the reservoirs.
Most of the technologies that deal with heavy oil need to address the mobility ratio or viscous forces before any flooding. In general, poor recovery is caused by physical reasons or geological reasons. Physical reasons can be categorized as capillary forces (existence of the interfacial tension between oil and water, wettability) or viscous forces (high mobility ratio between water and oil). Geological reasons are heterogeneities in reservoir rock and exist in all petroleum oil systems.
In heavy oil reservoirs, enhanced oil recovery (EOR) intends to reduce the capillary forces and interfacial tension to improve microscopic displacement efficiency or improve the sweep efficiency (macroscopic) by reducing the mobility ratio between injected fluid and displaced fluid. Improving the mobility ratio is achieved by increasing the viscosity of water using polymers or by reducing the oil viscosity using heat. In general, all technologies need to address the capillary and viscous forces to improve oil recovery. Paper SPE 207361 discusses improving of the efficiency of the flood by near-wellbore conformance and improving the vertical sweep efficiency.
The use of fiber-optic sensors, as addressed in paper SPE 199023, is intended to gather better data and avoid misinterpretation during falloff tests and injectivity tests. Traditionally, for heavy oil EOR simulation, because of the addition of chemical species or heat to the flow equations as well as the need for a finer grid resolution, the use of the full-field model in most cases was limited and the use of sector models and local grid refinement to obtain a reasonable accuracy has been applied in the industry. Sector modeling conditions must be satisfied to establish the reliability and the trade-off between accuracy (sector models) and computational expediency (full-field model). Recent development of hardware and software [graphics-processing-unit (GPU) -based simulators] has provided the industry with the tools to achieve a full-field model simulation in most fields by taking advantage of GPU solvers and using a fine-grid model to predict full-field performance.
This Month’s Technical Papers
Autonomous Outflow Control Technology Used in Water/Polymer Injectors in Heavy-Oil Fields
Fiber-Optic Sensors Evaluate Well Performance in Polymerflooding Pilot
Electrical Heating Can Optimize Production in Heavy-Oil Fields With Intelligent Multilaterals
Recommended Additional Reading
SPE 200279 Field Application of the Autonomous Inflow Control Device for Optimized Heavy Oil Production in South Sultanate of Oman by Ali Al-Jumah, Petroleum Development Oman, et al.
SPE 203012 More Oil and Less Water: Autonomous Inflow Control Devices in New and Old Producers in Heavy Oil Fields From South of Oman by Ameera Al Harrasi, Petroleum Development Oman, et al.
SPE 207684 Game Changer in Dealing With Hard Scale Using a Slickline Torque Action Debris Breakerby Mahmoud Mohamed Koriesh, Dragon Oil, et al.
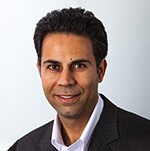
Mehdi Izadi, SPE, is a reservoir engineering authority in the Technology Department at Ecopetrol. Currently, he oversees the technical assurance of reservoir simulation and modeling activities, defining guidelines and standards for dynamic modeling, defining the technological route and training plans, and developing respective successors within the simulation discipline. Izadi holds PhD and MS degrees in petroleum engineering from the Colorado School of Mines and has more than 20 years of experience in classical reservoir engineering analysis, reservoir simulation, and enhanced oil recovery (EOR). He has been teaching industrial courses and providing onsite training on chemical EOR simulation and reservoir modeling and currently is an instructor at Ecopetrol University. Izadi is a member of the JPT Editorial Review Board.