Three of Asia’s biggest upstream operators are now in the midst of full-scale digital adoption. The companies are beginning to see results, but none is counting on a “big bang” in development of the technology any time soon.
Over the past couple of years, Malaysia’s Petronas, Shell Malaysia, and Thailand’s PTT Exploration and Production (PTTEP) have each launched digital programs across their organizations in hopes of improving their exploration, development, and production workflows and results. The change has come with a number of growing pains and lessons learned through trial and error.
The leaders tasked with overseeing implementation, however, want to keep the growing pains to a minimum. For that reason, they are taking a deliberate and methodical approach to digitalization. This is especially true for Petronas, an integrated, state-owned firm that is both Malaysia’s main energy producer and chief revenue generator. Risk is not viewed favorably within the company.
Petronas officially embraced digital transformation in 2017 after Tan Sri Wan Zulkiflee Wan Ariffin, president and chief executive officer, made digitalization a key focus in the company’s growth plan.
As part of its implementation efforts, Petronas that year established the Center of Digital Excellence under the stewardship of Wan Shamilah Saidi, chief digital and information officer. With the integration of all digital initiatives under one platform, focusing project development, the company’s different units no longer work in isolation.
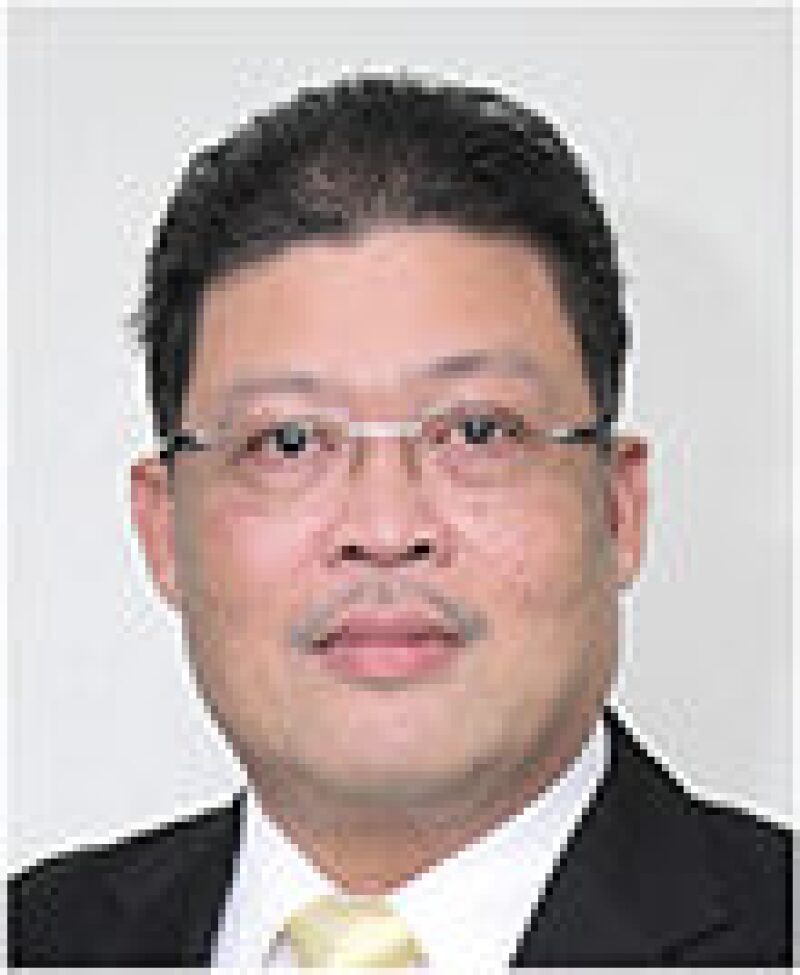
“We do not believe we have to develop everything ourselves from scratch,” said Nasir Hj Darman, Petronas chief technology officer of group research and technology, on the sidelines of a recent digitally-focused SPE executive forum in Kuala Lumpur. The company’s development program consists of a mix of internal incubation, external collaboration, and acquisitions.
The company’s digital strategy starts from the top with leadership directing development projects, while “bottom up” idea generation is encouraged from its engineers and scientists, Nasir explained. A ringfenced budget dedicated to technology development ensures those engineers and scientists are clear from the outset on the resources available to them.
To control the quality of its research, the company established the Petronas Technology Management System that determines how projects are developed. It evaluates all projects by employing the Technology Readiness Level system to gauge technological maturity. “That is one of the ways for us to reduce risk,” Nasir said. “We want to be No. 1, but we do not want to be guinea pigs.”
Khoo Choo Beng, Sarawak Shell Berhad general manager, business excellence, offered JPT similar views during the same gathering of Asia-Pacific (APAC) industry and tech executives. A regional unit of one of the largest multinational, integrated oil and gas companies in the world, Shell Malaysia, too, is a sprawling organization made up of many different divisions. Managing technology development can become unwieldy and requires structure and discipline, including in its upstream unit.
“We try very hard not to have the organization jumping on the digitalization bandwagon where it’s the buzzword of the day and everyone goes off doing their own digital projects within their own team or function or space,” said Choo Beng, Shell Malaysia Upstream is “not going for mass quantity” over quality.
“A lot of time we try to see if there are cheaper, simpler, quicker solutions that we can deploy,” he said. The business’s focus this year is to “digitalize the mundane,” removing much of the administrative-level work so that employees can focus on larger, more important tasks.
Last year marked the birth of Shell Malaysia Upstream’s digital journey as the unit came up with a “framework to govern how we want the organization to embrace digitalization,” Choo Beng said. It began by forming a Digitalization and Technology Advisory Board, a board of governors that screens and prioritizes the organization’s project wish list. Project approval depends on “sufficient value” and whether it is doable for the organization given available time and resources, he said.
The board interviews individuals or teams within the organization to understand their pain points and find opportunities to improve work through digitalization. It then focuses development under five digital areas: increasing production, improving safety, finding ways to “bring information to fingertips,” leveraging data as a strategic asset, and striving for simplification and automation.
Connecting Humans With Digital
Getting people to embrace digital is one of the biggest challenges faced by organizations implementing the technology at a wide scale. On one hand, rapid uptake is needed for employees to keep pace with quickly evolving digital technology. On the other, many employees are concerned about how digital will affect their day-to-day work—and employment as a whole. Can they trust the technology?
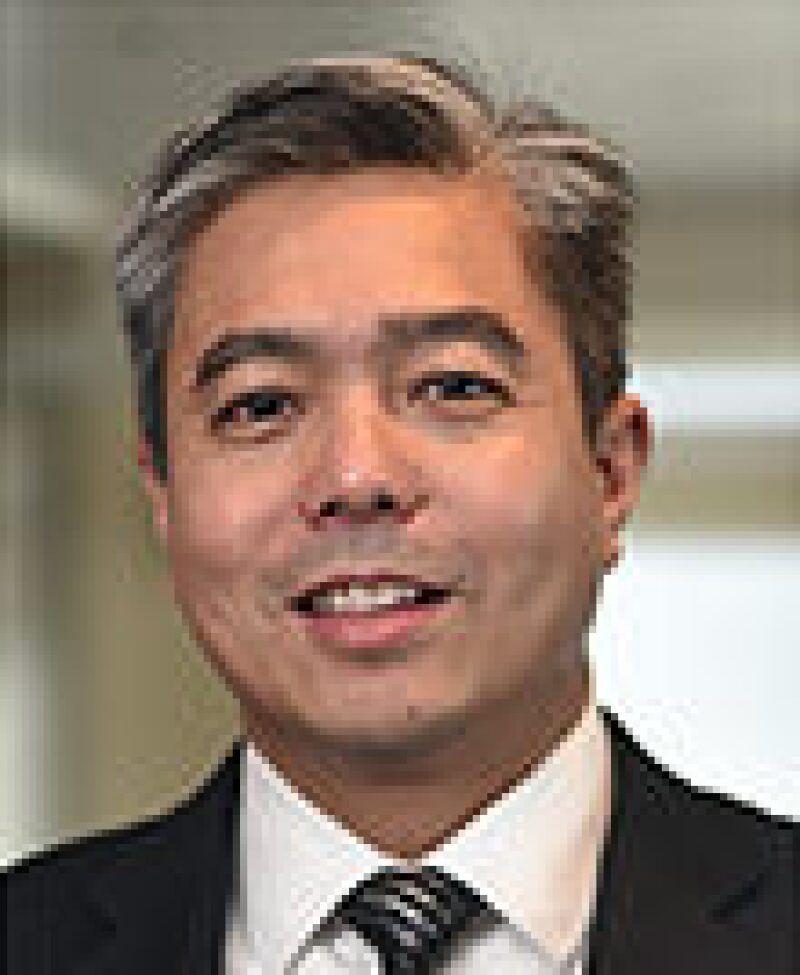
The first task of Petronas’ newly minted chief digital and information officer should be to “propagate digital across the whole organization,” said Adif Zulkifli, Petronas executive vice president and chief executive officer of gas and new energy. “It is all about trying to educate the people on what digital means and what we can accomplish with it.”
To that end, Petronas has developed a smartphone app called Switch for employees that covers a variety of digital topics from both a broad level and company context. The app is populated by videos in which leadership—Adif included—explains the virtues of digital technology and highlights Petronas’ digital initiatives. “When you have leaders on board, it’s much easier for you to get the whole staff on board,” he said. It also features speakers from outside the company ranging from an Amazon executive to a Formula 1 driver.
Digitalization is starting to spread to many different parts of the company, all the way down to talent development and succession planning, Tan Sri Wan Zulkiflee said during the March CERAWeek conference by IHS Markit in Houston. He said that the company is using an algorithm that helps match open positions within the company with employees who are the best fit for those positions. “But it’s just an input. It’s still being decided by humans,” he noted.
When it comes to developing the skillsets of the future, he said, “We have a fairly rough idea, but no one knows for sure what those will look like.” However, certain attributes are important for Petronas’ workforce, including passion for the work and a lifelong dedication to learning, necessary in a world of evolving digital technology.
“For the organization,” said Tan Sri Wan Zulkiflee, “we need to have platforms where we can retrain people, conversion programs [for] the various required skillsets, we need a recertification program—it’s a multipronged approach to ensure that we have the required skills going forward.” Along those lines, Petronas has a data science academy that certifies data scientists.
Choo Beng said there are many employees at Shell Malaysia Upstream, namely engineers, who have a natural inclination toward digital technology and are interested in contributing to that area in the company. The company internally is working to grow its digital skillset by training in analytics platforms such as Power BI and Spotfire.
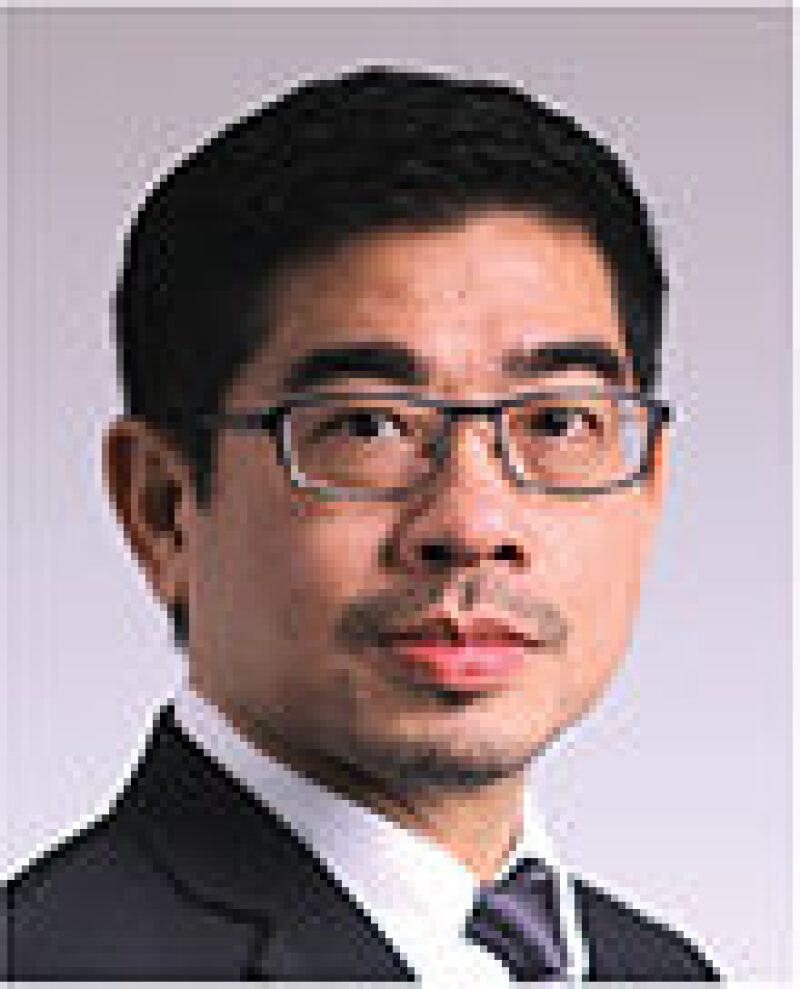
PTTEP has a mix of newly hired data scientists and its own veteran engineers experienced in digital technology. “However, in Thailand in particular we really lack these digital skills in personnel because we don’t have adequate data scientists in the country to supply the multiple industries competing for digital talent,” said Chayong Borisuitsawat, executive vice president of PTTEP’s business and organization transformation group and acting vice president of the company’s own Digital Center of Excellence.
For now, the company is offsetting the deficit by reaching into other APAC countries and the US to find talent. PTTEP is also building a digital academy within the company to ensure it can develop people who both know the industry and can take ownership of data.
Using Digital in the Real World
PTTEP launched its digital transformation program last year. The company currently has 31 digital initiatives spanning exploration, drilling, production, and the supply chain covering technologies such as data analytics, data visualization, cloud computing, and process automation.
While it’s still “very, very early” in the company’s digital journey, PTTEP is piloting predictive maintenance projects, working to improve tripping time and predict nonproductive time in drilling, and using advanced analytics to optimize production and processing from its gas fields, Borisuitsawat said.
The company is using a well-known cloud platform to store, compute, and analyze its exploration and production data but is still in many ways reliant on standard software from vendors. However, Borisuitsawat said he expects that those and similar software platforms could become open source or open standard so that operators like PTTEP would be able to add their own applications.
Petronas’ upstream business is currently focused on digitizing its data—some 70 petabytes that include seismic, geoscience, and well data—and keeping up with information and computing technology, Adif said. For example, the company is investing in cognitive capabilities for subsurface and field development planning. “We are already working with leading cloud and analytics partners on this and looking into establishing long-term and collaborative partnerships for co-creation and the exchange of knowledge between the oil and gas and tech industries,” he said.
The goal is to make data more accessible and valuable to its employees while increasing workforce efficiency. The company’s alpha well advisor tool, for example, collects hundreds of well reports via mobile devices and structures the data so that when an engineer prepares a well report, he or she can easily find characteristics, trends, and challenges from a collection of previous wells.
Petronas also is using robotics and automation in its research center to handle hazardous chemicals such as mercury, hydrogen sulfide, and carbon dioxide. Petronas also is using robotics and automation in its research center to handle hazardous chemicals such as mercury, hydrogen sulfide, and carbon dioxide. Nasir noted that similar technology can be used in the oil field. In labs where the company works with high-pressure/high-temperature equipment, robotics and automation have reduced manpower by 40–50%.
The technology has “opened up a lot of other things that we can do with existing manpower, and not a single person was made redundant. We do not believe in that,” Nasir said. “So, at the end of the day, when we measure efficiency per capita, we can do a lot more with the same number of people.” For example, “we did not do prototyping—we outsourced it previously. With these extra people now, all the prototyping is done internally. And that is saving costs. That is saving time.”
When a project is outsourced, the manufacturer produces the prototype and sends it back to Petronas for testing, taking about a year given the tender process. “And if it fails, you have to go through that cycle again,” he said. “That makes people scared of failing,” and the company “becomes fat with projects.”
Shell’s digital focus areas revolve around “making processes more and more efficient” so that they improve frontline productivity, Choo Beng said. On the subsurface side, Shell uses what it calls a “fault crawler,” a form of artificial intelligence that canvasses subsurface data modeling to predict where faults are located, allowing for better decision-making when planning a well.
Because of limited gas-handling capacity during oil production at one of its facilities, Shell set up a real-time optimization tool that keeps a well’s gas/oil ratio (GOR) in check. Previously, a production engineer had to manually inspect GOR on a daily basis and take action when wells were showing higher GOR, but now it is done automatically in real time.
Shell’s use of a smartphone and tablet app called ProntoForms has tripled submissions under the company’s accident control technique thanks to the ease of reporting incidents. In the past, “hundreds and hundreds” of hours were spent digitizing and analyzing the reports each week, Choo Beng said. ProntoForms allows workers to input a report on the fly, digitizing their submissions. The next step will be to use machine learning to automatically search through millions of words to find insights on safety performance.
Shell has also used ProntoForms in inspection reporting. Manual inspections and reporting offshore previously took weeks. Inspectors would jot down notes, take countless photos, and return to the office to prepare a report, which itself could take weeks. With the app, all of this is done immediately on site.
Petronas’ Digital Case StudiesPetronas has published several digitally-themed papers since beginning its organization wide digital strategy in 2017, sharing its learnings and experiences in applying the technology. In OTC 28591, the company outlines how to become a “data-driven organization,” emphasizing the importance of having the “right” data as opposed to merely hoarding petabytes of data that are mostly indecipherable. Data collection methods should be determined—ideally most would be automated—and data should be easily shared and searched by selected parties within an organization, the paper said. When paired with the appropriate domain experts, this will drive better insights from analytics. Through an ideation workshop, the company came up with the Petronas Remote Monitoring & Predictive Diagnostics Centre (PRMPDC) to monitor, perform analytics, and offer solutions for its plant assets. Four plants were incorporated into the RMPDC pilot, including its 30-million tonnes/annum Malaysia LNG complex and facilities serving three offshore oil fields. Predictive failure models and prescriptive analytics helped improve asset performance, resulting in more than $20 million in value created in just 4 months vs. less than $1 million spent. Quality sensor data were critical in Petronas’ implementation of a method to measure well activity performance, detailed in SPE 192835, supplementing the Petronas Digital Collaboration Centre, a decision-support platform for monitoring operational and safety issues during drilling. The company developed an artificial intelligence tool to assess performance in near-real time, allowing for adjustments to be made as a well is drilled. Petronas also reported cost savings in SPE 195064 through deployment of its Virtual Workstation (VW) that improved the performance of petroleum engineering technical software, namely for the Petrel platform, in the company’s subsurface department. The VW brought together software and data into a single data center, allowing engineers virtual access through the company’s intranet. Following a proof of concept phase in which static model compatibility tests were conducted in Petrel, the organization scaled up the program to 40 users. As a result, the company was able to hold on to around $280,000 previously dedicated to IT infrastructure. |