Waste injection in shale, with matrix permeability in the nanodarcy range and without the presence of any permeable layers, has been performed on the Norwegian Continental Shelf (NCS) for more than 15 years. To avoid leakages to the seafloor using this method, techniques have been developed that allow wells to dispose of several million barrels into individual shale domains, with vertical propagation of the disposal domain less than 1,000 ft above the injection point. Recently, use of frequent 4D interpretations of seismic surveys shot over a permanent sensor array allowed detailed domain mapping and independent dynamic monitoring.
Historical Perspective
Changes of North Sea regulations in the mid- to late 1990s made the seabed disposal of oily cuttings and other waste from drilling and production impossible without the use of significant topside cleaning systems. Meanwhile, the development of fields required increasingly complex wells, resulting in the almost systematic use of oil-based mud for efficient drilling.
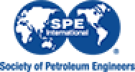