The offshore oil and gas industry has always been cognizant of its impact on the marine environment. The choices that operators make in how they operate, including the disposal of drill cuttings, must address an increasing number of environmental and climate targets in addition to those related to health, safety, and cost. As a typical well will produce approximately 1000 metric tons of oil-based drill cuttings, quantifying greenhouse-gas (GHG) emissions associated with the disposal and treatment of drill cuttings has become an essential step to achieving net-zero ambitions.
Since 1991 (1993 for fields in production), strict regulations relating to the discharge of oil-based drill cuttings have been in force under the OSPAR (Oslo/Paris) Convention. Those regulations banned the practice of discharge to sea of untreated oil-based drill cuttings and led to a situation where they were generally shipped to shore for treatment and disposal.
In 2020, TWMA engaged DNV, the independent energy expert and assurance provider, to undertake a comparative study between the company’s offshore thermal drill-cuttings treatment solution and conventional alternatives including “skip and ship,” bulk transfer, and cuttings reinjection (CRI) used on the Norwegian Continental Shelf (NCS). It is the first paper to show a direct emissions comparison between offshore processing and alternative methods implemented.
The study assessed the carbon dioxide (CO2) footprint and nitrogen oxide (NOx) emissions for each of the different alternatives. The values were then used to create an interactive emissions calculator that can easily be applied to specific projects to clarify the actual potential for emissions reduction within the drilling waste management process.
Background
Technological improvements, as well as cost focus on existing solutions, have meant that offshore thermal drill-cuttings treatment has been widely adopted in many offshore basins as one of the safest and most cost-effective approaches. In Norway, which was the subject of the study, adoption of the technology has been slower than in other countries, with onshore thermal treatment of oil-based cuttings applied as the predominant technique, while some fields use offshore slurrification and injection into dedicated disposal wells.
However, the cost of drilling new disposal wells and the track record of successful offshore thermal projects in other countries have improved the frame conditions for the use of offshore thermal treatment of cuttings on the NCS. It has also been demonstrated, in an earlier independent comparative study by Carbon Zero (SPE 207519), that the carbon footprint of skip and ship to shore of drill cuttings is 53% higher than that of drill-cuttings treatment at the wellsite (SPE 202639).
Comparative Assessment Alternatives
The main options for oil-based drill-cuttings treatment are offshore thermal processing or cuttings reinjection, both at source, and skip and ship or bulk transfer to shore.
TWMA’s thermal processing unit, TCC Rotomill (Fig. 1) is used to process oil-based drill cuttings, drilling fluid, and sludge associated with oil- and gas-drilling activities.
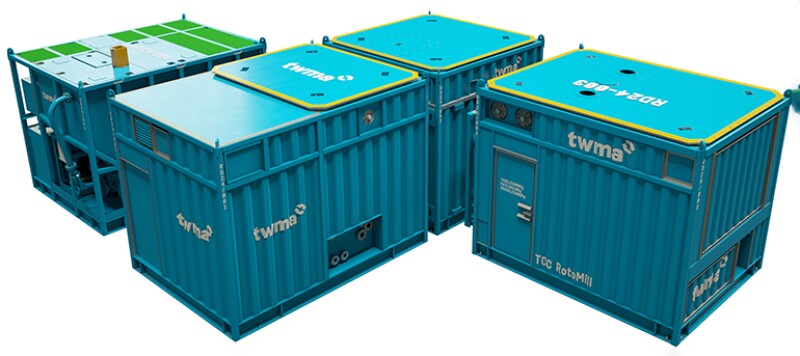
The technology uses a process of thermal desorption to separate drill cuttings and associated materials into their three constituent parts of oil, water, and solids for recycling and reuse or disposal. In an offshore environment, the hydrocarbon content in the recovered solids and water is well below most environmental limits for safe disposal and is therefore dischargeable to sea. Recovered base oil, which remains unchanged throughout the process, is reintroduced to the drilling mud system at source.
Cuttings reinjection is based on drill cuttings, slurrified with seawater, then injected under pressure into a dedicated drill-cuttings disposal well. Hence, one (or more) dedicated disposal well(s) is required.
Alternatively, skip and ship to shore is one of the most applied solutions in the NCS. Here, skips are utilized at the rig site to contain oil-based drill cuttings for transportation onshore. Typically, this could require more than 200 skips, each involving more than 12 crane lifts before reaching its final destination, amounting to more than 2,500 lifts per well. This activity also increases the likelihood of safety and environmental incidents.
In general, bulk transfer of drilling cuttings is similar to skip and ship. The main differences are that oil-based drill cuttings are pumped between storage tanks on the rig, vessel, and quayside rather than contained and lifted in individual skips.
With both skip and ship or bulk transfer operations, onshore treatment of oil-based drill cuttings is required and as such, emissions related to this must be considered.
Emissions Identification, Evaluation, and Conversion
To establish an emissions calculator and achieve an objective, fair, effective, and accurate way of assessing the emissions footprint of the different alternatives, several assumptions were made by DNV before boundaries were defined:
- All solutions would utilize a similar process for handling cuttings and fluids from the well prior to processing; therefore, emissions associated were neglected.
- All rig-site solutions would use rig power except for the thermal processing unit which has its own power-generation system.
Having established a scope and identified activities, emissions data for the different processes involved in each method were collected and reviewed. Key sources of data were literature and guidelines for emission studies, as well as specific emission and energy consumption data from primary sources.
Identified Relevant Operations
Data related to the emissions of each of these operational stages came from multiple sources such as rig contractors, onshore treatment suppliers in Norway, TWMA process data, and research institutes.
On- and Offshore Power Generation
Emission factors for power generation for offshore operations were obtained for different rig power sources. This included values in kg CO2/NOx per kWh generated. Different options for power source offshore were included; gas turbine, marine diesel engine, power from shore (EU), and power from shore (Norway).
Emissions for operations onshore are linked to the energy sources that are being utilized. Therefore, the model includes different emission factors for variable energy sources. These include the EU energy mix, Norway energy mix, UK energy mix, and on-site diesel.
To calculate emissions for all alternatives to assess the different alternatives comparatively, all emissions were calculated as kg CO2 or kg NOx per tonne of cuttings treated/handled. Input data and emission factors for different activities and operations were also identified, evaluated, and converted for use in the model. Where possible, specific NOx factors have been used. Otherwise, activity-based NOx factors were used (for example, general rig factor or general supply ship factor).
Comparative Assessment
To compare the emissions of the different drilling-waste-management applications, a comparative assessment was performed using an emissions calculator, developed in Microsoft Excel to ensure user accessibility. This had two main functions: the baseline emission factors for different activities and the variable parameters for which the user can add project-specific data.
Three different scenarios were chosen for a comparative assessment of the emissions footprint for different alternatives. The comparative assessment focused on the total emissions of each alternative and on identifying main contributing activities of emissions for each alternative. The total emissions of the alternatives for treating/handling cuttings were then compared using parameters from the three different scenarios.
- Scenario 1: Same scope and parameters as used in a UK-based study from 2019 (SPE 207519)
- Scenario 2: Cuttings from the Ekofisk field with onshore treatment in Tananger
- Scenario 3: Cuttings from the Troll-field with onshore treatment in Ågotnes
A marine diesel engine is applied as the offshore power source for all scenarios, “EU power mix” for onshore, and a generic drilling rig for the CRI alternative in all scenarios, with 35 days for drilling an injection well with a capacity of 10000 tonnes of cuttings.
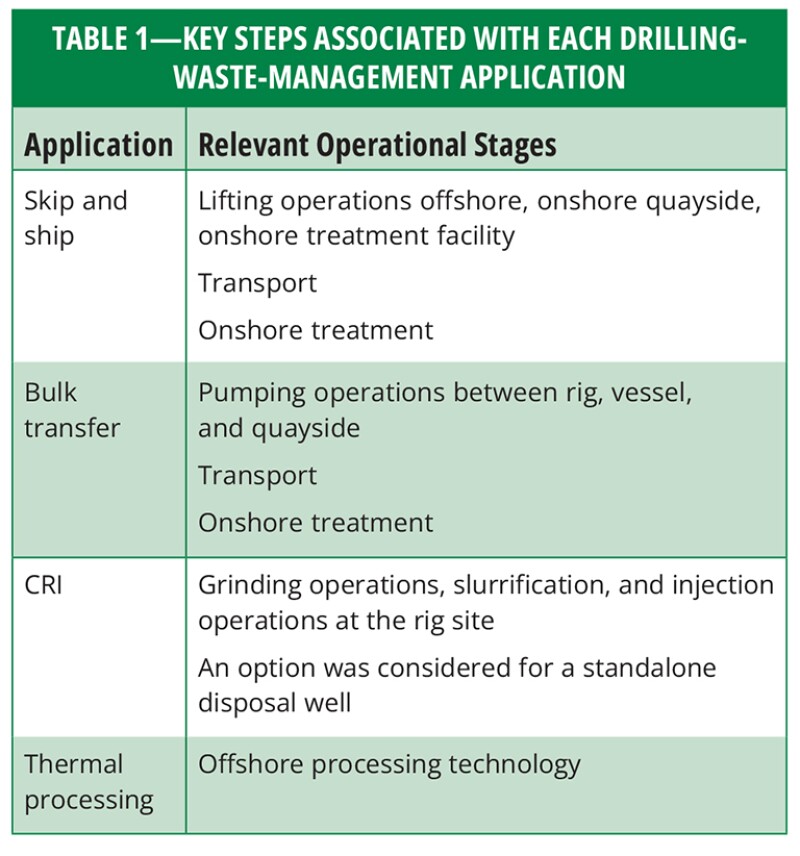
Summary of Results
The comparative assessment showed that the alternatives involving onshore treatment of drill cuttings were highly influenced by the distance to an onshore treatment facility. For all scenarios, onshore treatment activity contributes a significant amount of the emissions for these alternatives.
Use of offshore thermal processing technology showed the same level of emissions in all three scenarios, with 95 kg CO2 and 0.09 kg NOx emitted per tonne of cuttings treated. This method had the smallest emissions footprint and was based on the offshore power source; the alternatives have a fixed power demand per tonne of cuttings treated. The results yield an emission reduction of 14 to 48% compared with onshore alternatives.
It was also shown that emissions from skip and ship and bulk transfer procedures were highly dependent on sailing distances, as well as the power source for the onshore treatment facility and road transport distances.
The CRI alternative had the highest emissions of CO2 of all the scenarios—double that of the offshore thermal processing unit—with the majority of these emissions originating from drilling the disposal well. This related mainly to the number of days spent drilling, as well as the injection capacity of the disposal well. This method emits 205 kg CO2/tonne of cuttings to be injected. The emission of NOx was also relatively high for this alternative, with 1.92 kg NOx emitted per tonne of cuttings.
The results are examples only and will change among the alternatives depending on the actual project and the corresponding values applied in the variables function in the emissions calculator.
This case study is based on SPE 207519, which was presented at 2021 ADIPEC in November.
For Further Reading
SPE 207519 A Comparative Emissions Assessment—Drill-Cuttings Treatment Alternatives by G. Innes, TWMA; S. Nesse, DNV GL; and J.T. Eia, TWMA.
SPE 202639 Reducing Carbon Footprint Through Wellsite Processing by G. Innes and A. Morris, TWMA.
SPE 61262 Environmental Priorities of Re-Injection and Land-Based Handling of Drilled Cuttings and Affiliated Fluids by A. Saasen and J.E. Paulsen, Statoil; and K. Holthe,Norwegian Building Research Institute.
Low-Carbon Drilling—TCC RotoMill Wellsite Processing vs. Skip & Ship by M. Eadie, CarbonZero.
Norway. 2020 National Inventory Report. United Nations Climate Change.
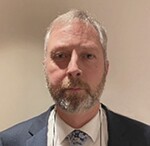
Steinar Nesse is vice president, environmental risk management, energy systems, at DNV. Previously, he worked with the Norwegian Environment Agency; however, he has been with DNV as an environmental consultant for the past 27 years. He supports national authorities and energy companies in Norway and abroad with impact assessment work and management of environmental aspects of offshore industry activities such as oil and gas, offshore wind, and deepsea mining. Nesse holds an MSc degree in marine resource development and protection from Heriot-Watt University and a BSc in environmental technology from the University of Stavanger.

Gareth Innes, SPE, the chief engineering and commercial officer at TWMA, joined TWMA in 2018, bringing with him more than 20 years’ experience. He leads TWMA’s technology development and sales and marketing strategy globally. Over his career, he has worked for large international service companies where he successfully managed a number of oilfield technology businesses.
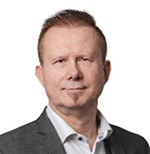
Jan Thore Eia, SPE, general manager for TWMA Norge AS, works with oil and gas operators to plan and execute safe, cost-effective, and environmentally beneficial drilling-waste- management programs. He is responsible or the operational performance, business strategy, and business development for the company’s Norwegian business.