Sand is mined. It is washed. It is dried. Then it gets wet again.
Such is the unassuming life cycle of most every grain of sand ever pumped down a horizontal well along with millions of gallons of water and into the freshly opened fractures of a tight-rock formation in the US.
But what if the sand never had to be dried?
To start with, the unconventional sector could save tens or hundreds of millions of dollars a year, simply by cutting out the capital-intensive drying process.
That might mean mines of the future could be made small enough to follow operators as they sail slowly across their vast acreages.
Wet sand also lends itself to safer and more regulatory-friendly worksites, an important consideration given that more-stringent air-quality standards are coming into effect in the US next year.
A wet-sand revolution may also represent a major boon for the industrywide effort to reduce CO2 emissions—making each horizontal well completed with wet sand a bit greener than one that used dry sand.
This is all according to a newly shared case study (SPE 199975) from sand supplier PropX and US shale producer Ovintiv. Since the highlighted field test was completed last year, PropX has pumped more than 1 billion pounds of wet sand down wells in Texas and Oklahoma.
“What we propose in this paper is the next logical step in the supply-chain reduction,” of the unconventional sand sector, said Brian Dorfman. “That is, the removal or the significant scaling down of the drying facility.”
Dorfman is a business development manager at PropX and one of the authors of the whimsically titled paper, “Can Wet Sand Be Used for More Than Building Sand Castles on the Beach?”
On a multiwell pad in Oklahoma, Ovintiv found that wet sand—defined as having a moisture content of 1–10%—could be used to stimulate more than a hundred fracture stages in under 2 weeks. Addressing any concerns over efficiency, the operation saw an average of nearly 4 million pounds of wet sand pumped downhole each day—well within shale-sector norms.
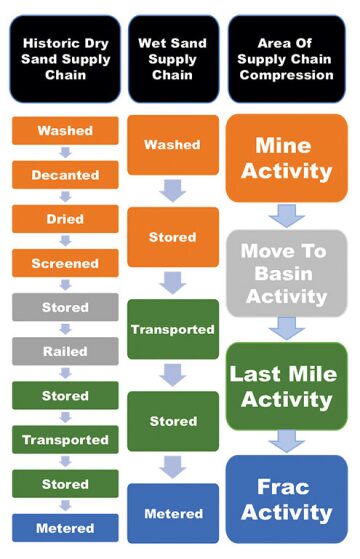
Sand is washed to remove contaminants. It is then run through industrial-sized kilns because dry sand flows from a hopper and into a train car or a truck far easier than wet sand which clumps together, as any child at the beach knows well.
To solve for clumpiness, PropX built new sand containers that load easily, and to load the sand, it adopted vibrating sieves used in heavier mining sectors.
Sand pricing is done by the ton, so with water added to the product, PropX also had to develop a new metering conveyor system that weighs the sand moments before it is blended with fracturing fluids.
The savings for operators who opt out of dry sand can have a wide range, from $2 to $10 per ton, according to PropX. Based on total proppant demand in 2018 and assuming a median savings of $6 per ton, the company estimates operators in the most active play in the US, the Permian Basin, would have stood to save more than a quarter-billion dollars using wet sand.
The Next Step in US Shale’s Big Sand Switch?
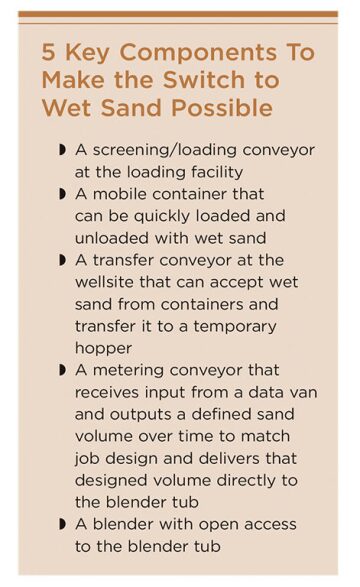
If wet sand becomes the new norm, Dorfman noted it will represent just the latest shift in a sand market that has already undergone one of the shale sector’s biggest transformations. Since 2017, when up to 90% of the sand used across all US shale basins came from three non-oil-producing states of Minnesota, Illinois, and Wisconsin, operators in the southern US have transitioned to sourcing almost all of their sand from in-basin mines.
Though the “Northern White” sands are stronger than those produced at in-basin mines, and therefore believed to better withstand the crushing forces of tight-rock fractures, they are far more expensive. Northern sands are mostly transported by rail—nearly doubling their cost by the time it reaches producers more than 1,000 miles away in Texas.
Producers have fully reclaimed that rail surcharge, and then some. The regional sands being delivered to wellsites by truck from a mine 50 or 60 miles away cost less than half of what was paid 4 years ago for the premium variety. Because of this sand switch, Dorfman said these companies have spent an average of $300,000 less on each well since the end of 2017, netting a collective savings of $2 billion.
Ridding dryers from the sand supply chain won’t save billions each year. But it might save just enough for it to become a trend.
The authors from PropX and Ovintiv found that the average capital requirement of the more than 50 in-basin mines that were built in the Permian over the past 3 years was around $181 million. Eliminating the drying units (along with the need for storage silos and conveyers) would trim this sum by 40 to 60%.
And from day one, the drying units are the mine’s largest operating expense, demanding up to a third of the entire workforce. Add to this the high maintenance costs that come with running what Dorfman described as the “most complex” system found at a sand mine.
“The infrastructure is large and susceptible to breaking down,” he said of the drying units. “Eliminating or reducing the drying process would increase the plant uptime, it would eliminate the bottlenecks at both the dryer and the vertical storage, and finally, it would allow for the inventory to flex much easier with the sporadic nature of frac sand demand.”
PropX is also pushing for the next generation of sand mines to go from regional to hyper-local with mobile mining systems that can be installed as close as 10 miles away from a wellsite. Coupling a wet-sand system with such a last-mile advantage would “supercharge” the combined savings, Dorfman said.
There is a noteworthy downside of wet sand. Another reason sand is dried after washing has to do with so much of it coming from those northern states, well-known for their long and frigid winters. If wet sand becomes freezing sand, a big problem is posed for those trying to load or unload it.
This means wet-sand completions are a warm-weather affair and likely not a viable option for operations in places such as North Dakota or Alberta.
More Moisture, Less Emissions
The sand-drying units found at most mines are gas guzzlers—natural gas, that is.
“When I say drying frac sand is an energy-intensive process, I mean it,” Dorfman assured.
“Assuming it takes 300,000 to 400,000 BTUs to dry one ton of frac sand, we estimate close to 1 million tons of CO2 was emitted in 2019 in the Permian Basin alone—just to dry frac sand, only to mix it with water and get it wet again.”
Preventing these emissions would be the equivalent of taking close to a quarter-million cars off the road every year, he added.
Based on an average price of about $2.50/Mcf of natural gas, the PropX and Ovintiv team estimate the Permian sector may have spent over $38 million to fuel the drying process in 2018.
If the US were to adopt a carbon tax, a possibility long discussed and expected by many in the US oil and gas business, this issue of gas usage becomes even more pressing.
Using the Permian figures from 2018 once again, a tax of $20 per ton of CO2 emitted would have added up to almost $20 million in additional costs to running natural-gas-powered drying units. If a stiffer tax of $40 per ton were applied to this scenario, operators of these sand-mining facilities would have shouldered up to $47 million in costs that ultimately would have been passed down to end users.
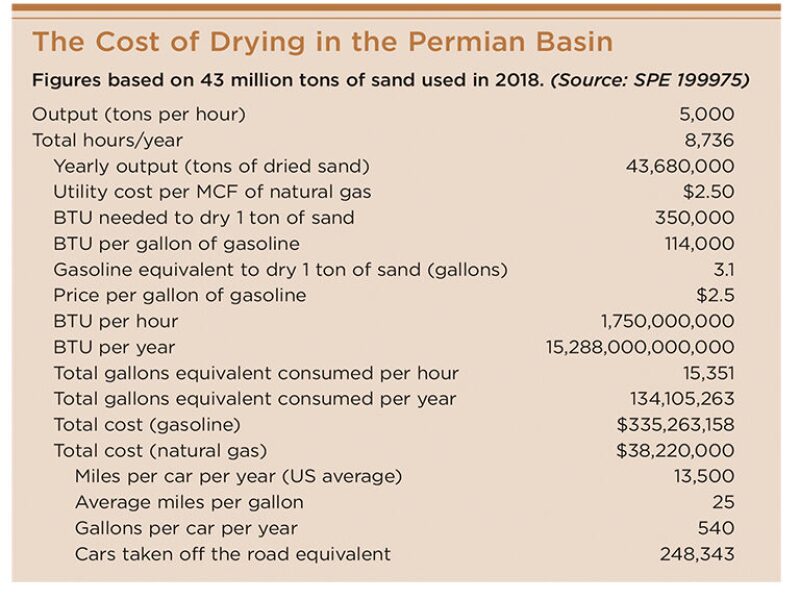
From Dust to Damp
If nothing else convinces operators and sand suppliers to displace dry sand with wet sand, then it may be air-quality regulations that prove to be the ultimate driver.
Silica dust is a well-known hazard and anyone who has visited an onshore completions site in recent years has known to avoid entering the area where sand is unloaded into blenders without a tight-fitting mask. This is because inhaling too much silica dust while breathing can result in a chronic lung disease known as silicosis.
In 2016, US federal regulations were introduced to put strict limits on the amount of dust that can be in the air at worksites. Companies have been given a grace period to become compliant, but that time runs out in June 2021. By then, companies must comply with most aspects of the regulations, including a limit on the presence of silica dust in the air of no more than 25 micrograms per 8-hour working shift.
Dorfman offered perspective by explaining that this “is the equivalent of a spoonful of sand spread out across an entire football stadium—that air has to be near perfect.”
Dust-management technologies exist, but with wet sand they are not needed since its added weight and clumpy nature prevent sand particles from floating into the air when agitated.
In the Permian study, PropX and Ovintiv used fixed air monitors and attached others to personnel to verify the claim. The air-quality data, which is shared inside the paper, showed not only were wet-sand operations compliant, but that dust levels were below the sensor’s detectable limits. “Damp sand eliminates respirable silica dust, period,” said Dorfman.
For Further Reading
SPE 199975 Can Wet Sand be Used for more than Building Sand Castles on the Beach? by B. Dorfman, M. Oehler, and K. Fisher, PropX; I. Wilson, EnCana Corporation, Ovintiv.