An obscure issue emerged onto the subsurface engineering landscape a few years ago. Not long after, it became recognized as one that affected operators of unconventional developments across the globe. Now, one of the largest shale producers in the US says it has found a solution.
The big problem appears to involve fracture plugs that are not holding in place, or that are allowing for high-pressure fluids to bypass them. From deep within the lateral sections of horizontal wells, new imaging technologies have revealed in stark detail to the industry the casing erosion that results. But this effect may be just a symptom.
The true concern for operators should be that of overcapitalizing on a poor stimulation.
“When a plug fails, your treatment isolation is lost,” explained Blake Horton. “The whole treatment is going down into the previous stage, and you are never going to get the resource out of the stage that you are supposed to.”
Horton is a completions engineer at Ovintiv who helped lead the operator’s root cause analysis effort. Just over 2 years ago, the Denver-based shale producer became one of the first in the industry to realize its plugs were failing at an uncomfortably high rate during hydraulic fracturing.
Since then, the company says it has overcome the issue and is confident that its newest wells are seeing few if any plug failures. This comes after it has adopted two key understandings: solving the problem takes an enhanced diagnostic effort, and the results from that should be the ultimate driver behind buying decisions on plugs.
When the problem goes unnoticed, this philosophy is not obvious, or necessarily considered good business.
This is because as the shale sector added more feet and more stages to its wells over the years, so grew the amount of money being spent on fracture plugs and the time it took to remove them before a well could begin flowback. This opened the door for a few new technologies, namely composite-plastic and dissolvable plugs.
The former were brought to the market to reduce the time and cost of milling plugs out. The latter were designed to eliminate milling altogether, saving operators days of rental costs on multiwell pads.
With such direct lines to lower well costs and greater efficiency, both innovations have enjoyed widespread uptake in the shale sector. However, Ovintiv’s data and recent findings from other operators suggest the trend has led to diminishing returns.
Faster drillouts have come at the sacrifice of plug reliability, and therefore well productivity. Ovintiv reports stages that suffer from a plug failure will see an average of 30% lower perforation growth, a strong indicator of diminished stimulation effectiveness.
What Ovintiv is arguing is that less priority should be placed on plug cost and more on striking a balance between a plug’s ability to seal and its ability to be drilled out. A Goldilocks zone does exist, said Horton. Finding it, though, requires some homework.
“You don’t want to chase the cheapest plug,” he said, offering one rule of thumb on the matter. “You have a multimillion-dollar well, and this is one of the most important pieces of it. The entire stimulation depends on the plug.”
Do Not Rely on a Single Data Set
The first order of business is to diagnose the problem. To that end, Ovintiv developed a work flow that is more in-depth than its past approach, but notably, requires no advanced software.
The operator previously relied on two primary data sets to determine plug effectiveness: surface treatment pressure from the fracturing job and coiled tubing (CT) data that were also recorded on the surface while plugs were being drilled out later. This combination is now considered unreliable.
Starting with surface treatment pressure data, which are available on every job at virtually no cost, Ovintiv found that using this information by itself paints a fuzzy picture at best.
While some are trying to refine this data set with analytics, the operator's experience underlines the challenge. Ovintiv has observed stages that experience substantial pressure drops during the stimulation, which, at first glance, resembled the signature of plug failures. Then, during the drillout phase, it found that some of those suspect stages still had plugs in place.
“We have also seen the opposite too, where there is no change in surface pressure, but then we go [in the well] and find a massive, eroded section of casing where that plug was set,” shared Horton.
Though the risk for mixed signals is there, a large-magnitude pressure drop is not to be ignored and can be the result of a plug failure. Horton said if companies see such drops in more than 10% of a well’s stages, their next step should be to invest in some type of downhole visual diagnostic. The three technologies that fit the bill are video-based systems, ultrasonic imaging, and caliper tools that generate 3D renderings of the wellbore.
These ground-truth delivering technologies are most important, though, because they unmask the truly ambiguous cases. Those include instances where a plug holds in place, but partially fails, allowing a jet of sand and water to eat away at part of it and part of the steel casing around it. In that event, relatively small drops in treating pressure may be observed, but because they are small and slow to evolve, they do not often raise red flags for completions teams.
Horton recalled a stage that by looking at the treatment pressure could not have been distinguished from the rest of the stages immediately before or after it. It was by all indications “a normal stage.”
“Turns out, though, that was our worst example of erosion,” he said, sharing that this stage came early in the learning process and the team only spotted it since a downhole imaging run had been pre-planned. Otherwise, he added, “we would never have thought that there was an issue with that stage.”
CT data can be used to either confirm or disprove what the pressure data indicates, but Ovintiv has concluded that it must be collected downhole to be trusted. Operators rely on CT to drill out the plugs and in theory the data collected during this process would show when the bit hits, or tags, the plug and starts to drill it away.
The problem has to do with the fact that many horizontal wells today stretch about 10,000 ft down and another 10,000 ft out. Horton said at these extremes, CT tends to act like “a big spring” during drillouts, which sends “the data bouncing all over the place.”
Further complicating things, today’s smallest and lightest-weight plugs take less than a minute to drill out, leaving not much confirming data to collect in the first place. That short span combined with the noise generated by the spring effect drove Ovintiv to start taking downhole measurements with memory tools attached to the coil so it could capture torque readings during drillouts.
With the downhole data, Ovintiv was better able to confirm whether a plug was where it was supposed to be, or if it had disappeared. It also gained more certainty over how long the plug took to drill out, providing some insight on its post-stimulation condition. However, even the downhole memory tool sometimes falls short of giving engineers the full story.
This is why the other big element to Ovintiv’s quality assurance strategy is to visually check for casing erosion periodically. Its primary diagnostic for this application is an ultrasonic imaging tool from DarkVision Technologies, a relatively new oilfield service company that was acquired by a unit of Koch Industries last year.
Some of the first images Ovintiv obtained from DarkVision—and that were the first to reveal the problem to the operator—were featured in a JPTreport published in January 2020. (Subsequent JPT reporting provided updates on industry thinking around casing erosion, which in addition to plug leaks, includes other issues.)
The imaging tool was initially deployed as part of a study on perforation erosion, but ended up surprising both the technology developer and its operator client by uncovering the existence of large casing breaches where a number of plugs had been set.
In contrast to those first images, Ovintiv’s latest run with the tool last month delivered a far less dramatic, but arguably just as compelling, of a downhole picture. The ultrasonic scans of the newly completed well showed zero evidence of plug failure or erosion.
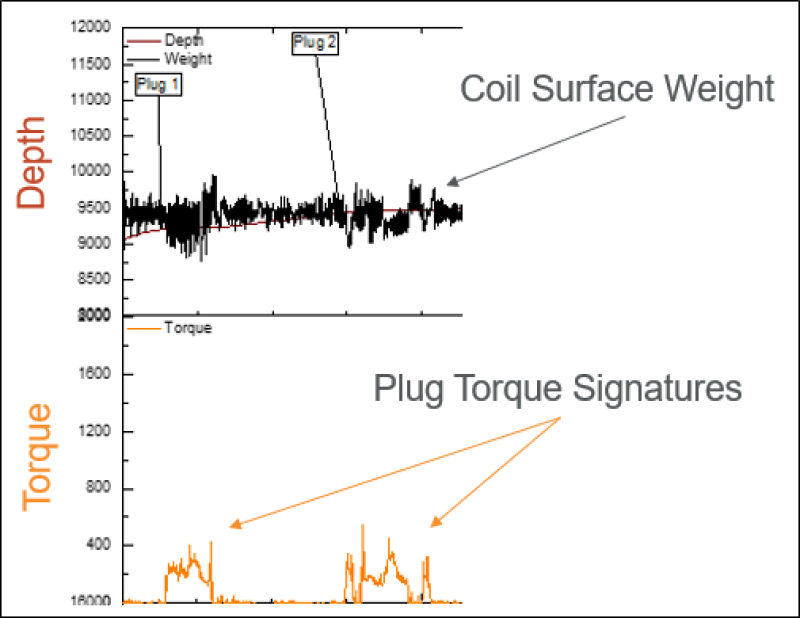
Choosing the Right Plug
The diagnostics alone did not result in the erosion-free success of that well.
Once Ovintiv became certain that the issue came down to its plugs, it spent an entire year looking at different versions to identify one that met both its sealing needs and its drillout speed wants. It found what it was looking for and has been using the same plug in every new well for over a year.
Ovintiv is not promoting its selection here, but rather how it arrived at its decision.
Sitting on Horton’s desk at work are half a dozen different plugs that for various reasons had to be brought back out of a well. His eye is trained to them in a different way now.
After looking at a plug and picking it up, he can predict whether it has a good chance of withstanding a modern hydraulic fracturing treatment that can reach upwards of 12,000 psi.
While holding a composite-plastic plug that is about 5 lbs. and less than a foot long, Horton said it would always deliver fast drillout times, “but the problem is this may also be gone during the frac—it’s not going to last, and that’s the whole point of a plug.”
Another plug behind his desk is made of steel, weighs about 30 lbs., and is almost 3 ft long. This heavy-duty variant shouldn’t have any trouble withstanding the pressure pumping, but it may also take half an hour to drill out.
“If you have 50 of those in the well, you could be adding some serious time to the to drillout,” Horton said, reminding that the trade-off between cycle time and completions effectiveness remains an important consideration.
These instincts were sharpened through a number of experiments that Ovintiv ran to qualify its plug candidates. The operator began with independent tests run on the surface to see if the prospects could hold up to a shot of high-pressure water while placed in a piece of casing.
If they failed there, Ovintiv knew they stood little chance against much harsher real-world conditions. The top candidates were then taken to the field for their final exams—downhole stimulations that were monitored using the multidiagnostics approach outlined above.
In addition to the hard data, Horton advises to pay attention to physical characteristics of the locking and sealing mechanisms. Some systems rely on cast iron slips and others on ceramic buttons to hold them against the casing. Some plugs have a backup sealing ring, some don’t, and others use a different method to squish material against the casing to isolate the flow.
Depending on each operator’s stimulation design and geologic properties, which are not covered here but play a role in the matter, the best option may be different. Horton noted other caveats that impact a plug's ability to set correctly, including their placement in deviated sections, on casing connections, or in an area of the wellbore where there is too much sand.
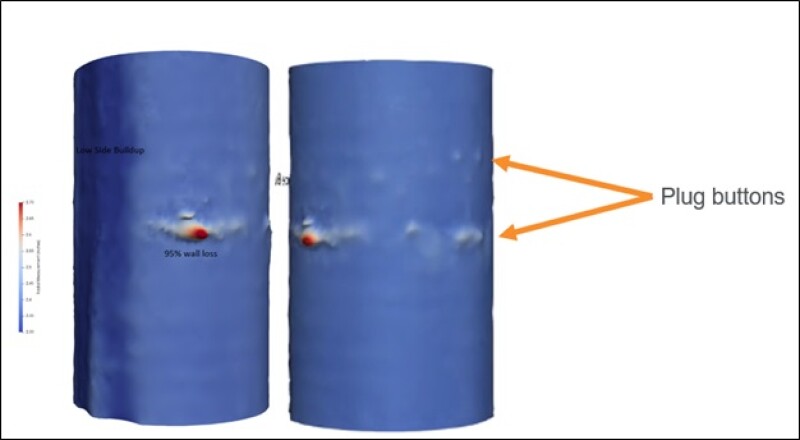
Renewed Scrutiny on Dissolvable Plugs
Operators may be seeing the biggest problems on this front when using dissolvable plugs. This has been true for Ovintiv, causing it to reconsider its views of the technology.
“We have a lot of evidence that shows [dissolvable plugs] failing during a stage,” said Horton. He was speaking to downhole imaging data acquired by multiple operators in the US and Canada that found around three-quarters of stages isolated with dissolvable plugs had casing erosion.
Included in Horton's personal collection at work are the remains of a dissolvable plug that, like the others on his desk, was pumped back up to surface. What stands out most to Horton about this plug is that it was inside a well only for an hour, and yet its locking and sealing mechanisms had fallen to pieces. Most fracturing stages take at least twice as long to complete as it did for this plug to dissolve to a point where it could not effectively isolate the stage.
In a 2020 peer-approved paper (SPE 201734), ConocoPhillips also raised concerns over the performance of dissolvable plugs. The operator's study centered on the causes of casing erosion and emphasized that deformed casing sections, which are often the result of weak rock layers, appear to exacerbate plug failure rates.
On dissolvable plugs, specifically, the operator found that large-diameter types had a bypass, or a leak, rate of 50%. Smaller, high-expansion dissolvable plugs had a 100% leak rate.
ConocoPhillips recommended that operators and manufacturers collaborate on ways to qualify dissolvable plugs "against realistic downhole conditions."
This is not the first time that dissolvable plugs have faced scrutiny since they were introduced to the shale sector several years ago. However, in the early days of the technology, a more common complaint from operators was that they did not dissolve quickly enough.