Here we go again. A series of unexpected circumstances have intersected to drive oil markets down, causing myriad challenges for operators and service companies alike.
A virus pandemic erupts, shutting down global economies and thus the demand for oil. Ongoing disagreements between OPEC, Saudi Arabia, and Russia on a response strategy and increased production sees global crude prices drop to the $20 range, something we have not seen in decades.
Compounding the crisis in North America is the market influence over the past few years, which drove operators to focus on cash flow and profitability over production and capital discipline with limited access to equity and additional debt. Operators will need to work closely with service providers to once again make step changes in optimizing value, improving efficiency, and eliminating downtime and wasted resources.
The New Normal
Speculation as to the duration of this crisis is just that: speculation. The macro forces fueling it, the COVID-19 pandemic, and the price war between OPEC and Russia are beyond our control. In terms of business, it is wiser and more prudent to focus on what we can control.
Even before the recent events, most operators and service providers had already been revising their strategies, shifting from production growth to profit growth, in response to dwindling investment. We can expect that trend to intensify. There will be an increased emphasis on making operations more efficient and leaner with fewer resources and less susceptible to incidents and interruptions that lead to downtime. Further, investors are continuing to prioritize ESG factors (environment, social, and governance) alongside profitability. The room for error and cost overruns just got a lot smaller.
It is a well-worn cliché but perfectly apt right now: When life gives you lemons, make lemonade. As challenging as the current market climate is, it nonetheless presents us with opportunities to adopt more sustainable and more efficient solutions; among them is better water management.
Given the ratio of produced water to oil—up to 10 bbl for every 1 bbl of oil—development of unconventional assets has required increasing the focus on water management operations. To hydraulically fracture a single well requires millions of gallons of water, water that is frequently sourced elsewhere and transported to the fracturing site via truck.
Hydraulic fracturing produces millions of barrels of water from the reservoir in addition to the oil. The produced water, along with any recovered frac water (flowback), contains sands, salts, and metals that make it challenging to reuse directly in fracturing or otherwise.
The more sustainable and more efficient solution is to recycle the flowback and produced water. It entails desanding, filtering, and treating the flowback and produced waters, blending it to applicable specifications, safely storing it, and finally transferring the recycled water to the wellsite for use as a fracturing fluid.
A comprehensive, integrated, and automated closed-loop water management system can render flowback and produced water into a suitable base fluid for fracturing. Such a system not only brings more sustainability, accuracy, and efficiency to water management, it is cost-effective, especially now amid this volatile market.
More Sustainability
What to do with all the produced water generated from high-water-cut unconventional wells has proved to be a vexing question. According to an article in February JPT (https://pubs.spe.org/en/jpt/jpt-article-detail/?art=6469), in North America roughly 90% of onshore produced water is disposed of in saltwater disposal (SWD) wells, also called injection wells. As production slows in this current crisis, the demand for water disposal will go down, but in the long run, such disposal is simply unsustainable. Existing injection wells are filling up fast, and in some basins, they are now linked to increased seismicity, which has drawn the ire of the public and regulators. Moreover, trucking huge volumes of waste water to SWD wells often miles away is costly and requires time, trucks, drivers, and increased logistical and environmental risks, all of which up the odds of roadway accidents, spills, and higher emissions.
Recycling reduces the need for both disposal and sourcing fresh water, and advances over the past few years in technology have resulted in cost-effective options. Additionally, in water-stressed areas such as New Mexico, regulators and industry experts have recognized the need to reduce dependence on fresh water for fracturing and evaluate technical, economical, and sustainable methods to treat produced water for reuse.
As an example, a recycling installation in west Texas cut the operator’s freshwater sourcing by 50%, lowering overall operational costs and eliminating the need for wastewater disposal. In less than 2 years of operations, the system has recycled roughly 900 million gallons of water for use in fracturing operations.
Recycling the flowback and produced waters is more sustainable and cost-effective in the long run.
More Accuracy
Effective recycling requires analysis of the flowback and produced water composition to determine the proper chemical and filtration treatment. Manual or piecemeal water management, where technicians crunch numbers on calculators and basically mix the chemistry by hand, is labor intensive, time consuming, and prone to error.
Accurate analysis and chemical treatment can be achieved using a proven, advanced water treatment system. One such technology is the TETRA Swiftwater Automated Treatment (SWAT) system. It uses a chemical to oxidize the heavy metals and eliminate bacteria; coagulants to neutralize negatively charged suspended particles and cause them to clump; flocculants to promote the particles to clump; clarification to remove the clumps; and filtration to remove any remaining super-small particles.
Accuracy is also needed to regulate the flow of water into the treatment system, so the chemical treatment corresponds to the volume and composition of the water. A smart system, ideally an integrated closed-loop (self-contained) system, will monitor and regulate the inflow and adjust the chemical treatment accordingly: a sudden drop in wastewater coming into the system is met with an adjustment of the treatment process to ensure the resulting fluid remains up to specifications.
Blending the treated fluid with fresh water also requires accuracy, as does monitoring storage levels to prevent tank or pond overflow, which is an avoidable risk with the potential for costly cleanup. Mitigating that risk is best done with automation.
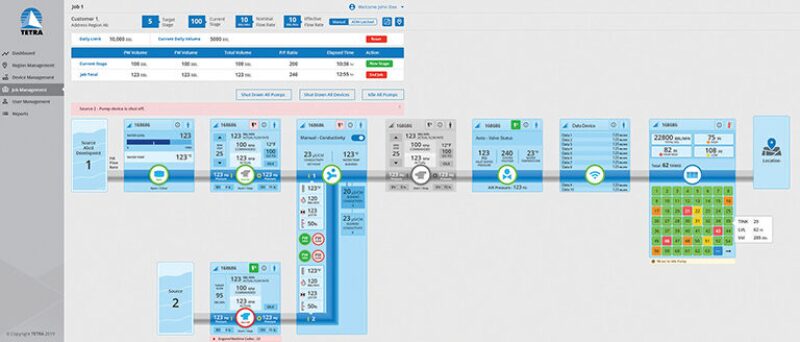
More Efficiency
Greater efficiency has been an industry mantra for decades. It became a major concern during the 2014–2016 downturn. Now, it is critical to the viability of every project, regardless of scope. One way to achieve the greatest efficiency possible is through automation. Automation means fewer workers on the jobsite, which means less exposure to risk, less travel, less fuel consumption, and lower costs.
Automating a water management system entails installing sensors on the various components: the flowlines, valves, tanks, pumps, desanders, treatment equipment, blender, and distribution manifold. The sensors are then connected to programmable logic controllers (PLCs), each calibrated with settings determined by operational design. With an integrated system, the components are linked together so they can communicate with one another. Such an approach delivers more efficiency than a collection of discrete components, each operating independently. That said, projects of limited scope may have only enough resources to automate key components such as the pumps or tank-monitoring systems.
An automated system can also be connected via cellular or satellite to the big data cloud, allowing technicians to remotely monitor and control each component as well as overall operations. If connectivity to the cloud is interrupted, the on-site PLCs keep operations running smoothly.
An automated, intelligent system can regulate pump speed for optimal performance, maximizing fuel efficiency and reducing wear on pump engines. Lower fuel consumption also reduces refueling trips to the site as well as the associated emissions.
Automation is also helpful should something go wrong. If, for example, the system detects a sudden drop in pump pressure due to a leak in the flowline, it will automatically shut down that pump and close the appropriate valve to prevent an unsafe or costly leak.
Logging into the system using a computer enables users to remotely view digital twins of the components, whether from their office, home, or the wellsite. They can monitor parameters and adjust pump pressure, chloride ratios, tank levels, and other settings.
Automation via the cloud also enables users to generate detailed reports on a number of metrics and timeframes such as volumes of water treated per hour; volumes of sand removed for a given volume of water; pump-engine fuel consumption per day; trends in pump pressure; and trends in chemical composition. As the critical benchmarks of operational success become efficiency and cost control, such reporting will provide quantification to enhance existing operations as well as plan and budget future projects.
Automation also can reduce the number of personnel needed on-site to operate and monitor equipment to as few as two workers, offering an advantage when a pandemic restricts movement and demands social distancing.
To illustrate the value of automation, an operator in the Appalachian Basin (northeast US) implemented the TETRA BlueLinx automated control system to automate water extraction from a nearby river for fracturing operations. Using a real-time data stream from the US Geological Survey website monitoring the river, the system automates the diesel pumps extracting the water. When river level drops below a specified threshold of cubic feet per minute, the pumps stop automatically, limiting the extraction volume so the operator avoids regulatory penalties and fines.
Adjusting to the New Normal
Unprecedented might be the best way to characterize the current oil market combined with the social and economic chaos wrought by the COVID-19 pandemic. For many of us it is uncharted territory. Oil trading for weeks in the $20 range is something we have not seen in decades.
We learn from these crises and adapt, grow stronger, and look for ways to improve what we assumed was already best practice. It is an opportunity for creative innovation as the industry strives for new levels of efficiency, remote work, and optimization.
In oil and gas, we are already seeing operators and service providers cut their workforces and scale back production. Although it is uncertain how the next several months will unfold, what we can be reasonably certain of is that hydraulic fracturing and unconventional development will continue to be part of oil and gas extraction, and with them high ratios of water to oil. In fact, that ratio will likely move in only one direction: more water.