There is a limit to disruptive innovation in oilfield technology. Blowout preventers (BOP) show how hard it can be.
A decade ago on 20 April 2020, the Macondo disaster made a powerful case for change when this last line of defense failed to stop a blowout that caused explosions and a fire that killed 11, destroyed the Deepwater Horizon drilling rig, and set off one of the largest oil spills ever in the Gulf of Mexico.
Scathing reports from investigations and staggering payouts from lawsuits against BP and other companies highlighted the shortcomings of machines that failed to serve as the last line of defense when natural gas surged onto the drilling floor, setting off a series of explosions.
The investigations highlighted a long string of errors that led to the avoidable crisis. There was a failure to verify the cementing, missed signs of gas building up in the well, and a delayed decision to activate the BOP until the explosions already may have severed the hydraulic lines to the wellhead.
But the simple explanation for it all: The shear rams failed to sever the pipe and seal the well.
In the aftermath, well-control standards and regulations were rewritten and expanded. The changes required that old recommendations became requirements, and new ones were added, including a strong push toward real-time monitoring.
The reports did not propose fundamentally redesigning BOPs.
But for engineers with an inventive streak, this looked like a call to rethink the driving force behind these hydraulic devices where the fundamentals have changed little since the first patent was issued nearly 100 years ago.
The arguments for rethinking BOPs included a 2003 study by West Engineering Services that found shear rams failed 7.5% of the time based on an estimate of the typical force required to cut pipe at the time. The force needed rises as casing gets tougher, water depths deeper, and well pressures higher, according to the study funded by what is now the US Bureau of Safety and Environmental Enforcement (BSEE).
A Det Norske Veritas study for Transocean completed before the Macondo blowout found 11 situations where a BOP was activated in an emergency among the 15,000 wells drilled from 1980 to 2006. The BOPs only worked six times during that period, according to a story in The New York Times published in June 2010—while the industry was scrambling to find a way to stop the Macondo leak.
Different Perspectives
The innovators range from startups to major offshore drillers.
A Norwegian engineer started a company to sell a design for all-electric BOP stacks and an offshore drilling contractor developed an electric motor to retrofit into a BOP body.
Engineers with military and space experience created cutting devices powered by gas generators using solid chemical propellants that send out high-pressure streams of gas when ignited by an electrical signal, similar to the deployment of an airbag or the thrusters on the Space Shuttle (this technology has been around for a long time).
Transocean incorporated one of those devices, made by Kinetic Pressure Control, as part of its redesigned BOP system. The K-BOS—Kinetic Blowout Stopper—is billed as being able to cut anything that goes through a BOP. It will be the last line of defense—the deadman autoshear.
As part of the redesign, Transocean developed an electric pumping station that will seal the well and cut anything left in the way. This subsea pump, which sends out a high-pressure stream of fluid, is combined with a fluid reservoir and a closed-loop system of hoses connecting it to the BOP and allowing it to use the fluid over and over.
The pumping system, which is battery-powered and made from proven off-the-shelf parts, closed and opened a shear blind ram 100 times at its maximum operating pressure in a deepwater test last summer.
Transcocean said at the end of the test, “The K-BOS cut a 16-in. heavy-wall casing with a 6⅝-in. landing string inside it simultaneously (a previously unshearable tubular combination), after which the blind shear ram closed and sealed on the bore.”
It is an example of a Transocean strategy to use innovations to gain a competitive edge. Darrell Pelley, director of technical marketing for Transocean, said the company holds 17 patents related to the pumping system.
Earlier this year, Transocean’s Chief Executive Officer Jeremy Thigpen announced that the company was talking to regulators and customers in hopes of testing the system on several working rigs this year.
That was before the COVID-19 pandemic triggered global reactions that killed both oil prices and predictions of a comeback for offshore drilling.
“We were talking to customers when everything changed here last month,” said Pelley.
He added, “I am excited by the technology. I am frustrated by the market conditions. We thought we were on the cusp of breaking out.” He still sees testing ahead, but it will take longer than expected.
Who Pays?
Ten years after Macondo inspired a spate of novel ideas, none of them has been tested on a working drilling rig.
When Nazareth Bedrosian was told last year that an engineer liked his BOP design, the director of oil and gas for Bastion Technologies commented, “He may like the idea but that is a whole lot different story than spending money on it.”
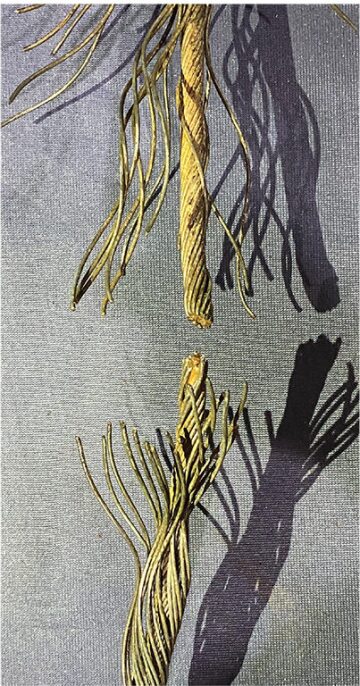
That in a nutshell is why Bastion, whose prime business is space engineering, has moved on to other paying projects, as have others who tried to disrupt the BOP sector.
“I applaud innovators; we backed some in the past,” said Bob Judge, director of drilling products for Baker Hughes. “The issue, the problem they have found is it is like pushing a rope. It requires that something be required by regulators, or there is a standard.”
An example is the BSEE’s requirement after Macondo that blind shear rams be capable of cutting wireline.
BOPs are similar to a home insurance policy. They are a necessary expense to protect against something you hope never happens, whether that is a tornado or a blowout.
Innovators promise to shave cost and weight and reduce the risk of a BOP not performing on the rare incidents when it is needed. But operators with a widely accepted solution in hand have been reluctant to consider changing to something new.
Change will require an operator willing to pay to support testing and, if all goes well, agree to a drilling contract that will allow a driller to bear the cost of buying, installing, and training crews to use a novel technology.
New BOP sales have been rare for years because the market has been glutted with nearly new equipment ordered back when oil was selling for $100/bbl.
The big three BOP makers—Baker Hughes, NOV, and Schlumberger—have mostly been paying the bills by selling parts and maintenance. “We have relied on spare parts and services and we had the odd stack order,” Judge said.
Their reliance on maintaining the status quo presents a sticky situation for innovators like John Dale, the chief executive officer for ESD, a Norwegian company he founded to sell a design for an all-electric BOP stack.
He is one of the BOP innovators selling working designs. For his all-electric BOP stack to become a well-control reality, he needs an experienced company in the deepwater business to make, market, and support his disruptive plan.
Convincing a service company to get into this moribund product line would be a longshot. Partnering with an equipment maker could get awkward.
To explain, Dale describes his fantasy of becoming the head of the BOP division of one of the big three companies and insisting that they go all electric. That would lead to executives asking how he would replace the revenue from all the hydraulic parts and services no longer needed in his all-electric future. Given his stubborn belief in electric power, Dale sees himself seeking a new job soon after.
Change can only happen if operators with deep pockets decide there is enough value to go to the trouble of creating a coalition including contract drillers, equipment makers, and regulators.
Judge said there are interesting ideas out there but wonders if in this depressed economic environment there are any significant innovations that operators, drillers, equipment makers, and regulators are all willing to support. His answer is “probably not.”
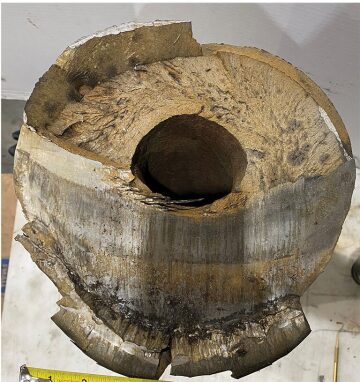
The Macondo Plan
The evaluations by regulators after the Macondo disaster were brutal, but over the past decade appear to have helped big BOP makers adapt to hard times.
They led to changes that expanded BOP makers’ parts and services business just before new sales vaporized after the 2014 oil-price drop to $50/bbl.
The required focus on increased data collection and monitoring helped reduce the time lost due to BOP downtime and set them up for the rise of data-driven analysis and services.
The starting point were investigations that concluded that Transocean had failed to ensure the Deepwater Horizon BOP stack was maintained according to the recommendations set out in API Standard 53 Blowout Equipment Systems for Drilling Wells.
The Macondo report from the US Bureau of Ocean Energy Management (BOEM) said the BOP had not had a “major inspection” within the previous “3 to 5 years of service” as recommended in the standard. The driller also failed to show evidence it had consulted with the maker of the BOP—Cameron, which is now part of Schlumberger—about modifications using parts from other companies.
Those shortcomings were not the cause of the BOP failure, which was caused by a buckled pipe so off-center the rams could not cut it. This led to a change in the well control regulation that resulted in BOPs that could cut offline pipes and other components which they previously could not cut.
Nonetheless, maintenance rules were stiffened by turning recommendations into a requirement. That change led to mass inspections of BOPs and guidelines requiring them to be broken down and rebuilt every 5 years, typically with parts from the original equipment maker.
Stepped-up maintenance work and parts became a steady source of income for BOP makers, whose relationship with customers grew because of the rules requiring real-time monitoring and information sharing.
One of the changes has been the addition of more sensors to gather data, and PLCs (programmable logic controllers) make it possible to automatically respond to the data. All that data created an appetite for analytical tools needed to comply with regulations requiring remote monitoring.
Those changes were embraced because they were needed to reduce the high cost of downtime by identifying and fixing many small problems before they developed into something that stopped drilling.
Judge said a “primary thing is the creation of RAPID-S53 database” where failures of parts or bugs in digital systems are reported by operators and drilling contractors and shared with original equipment makers. It serves as a reliability and performance information database based on API Standard 53.
Reducing downtime for BOP control units was a priority. These complex mechanical-electrical devices had long been known to be the biggest source of downtime by far.
BOP maintenance data through 2016 showed well-control equipment on drilling rigs resulted in more than half the downtime, with leaks in the BOP control system representing about two-thirds of those problems, according to the 2016 SafeOCS Annual Report prepared for US regulators.
Before the Macondo blowout, the BOP control unit was relying on its backup pod. Problems in that pod led investigators to question whether it was fully functional.
Since these studies were done, pods have been redesigned to increase their reliability, and Judge said they are constantly working to improve them.
“The biggest issues are in the control system. When we drill down further, the overwhelming majority of those issues are due to leaks,” Judge said.
Pelley at Transocean acknowledges these systems have become more reliable. Supporting that is a measure called revenue efficiency, sometimes referred to as operational utilization, reported by Transocean and other drillers.
Over the past 5 years, the score has risen from around 95% in 2014 to 98 to 99% in recent reports, Judge said.
It is intended to measure the percentage of time a drilling rig is earning money compared to the maximum amount that could have been earned if, for example, there had been no equipment breakdowns resulting in downtime. It is not a direct measure of BOP downtime—and far higher than industry estimates of nonproductive drilling time—but the number suggests downtime has been reduced.
Innovators say new technology can do even better. Transocean’s goal is to increase the revenue efficiency to nearly 100% by simplifying the hydraulic power supply with the subsea pumping system and by ensuring the K-BOS will cut whatever is in the well.
Is that potential gain enough to justify the cost of trying something new?
Despite claims by innovators that their systems will offer a more effective last line of defense than conventional systems, they have no operating history on working rigs, even though Macondo occurred a decade ago.
Judge said, “The safety record for offshore drilling, with a couple of notable tragic exceptions, has been pretty stellar.”
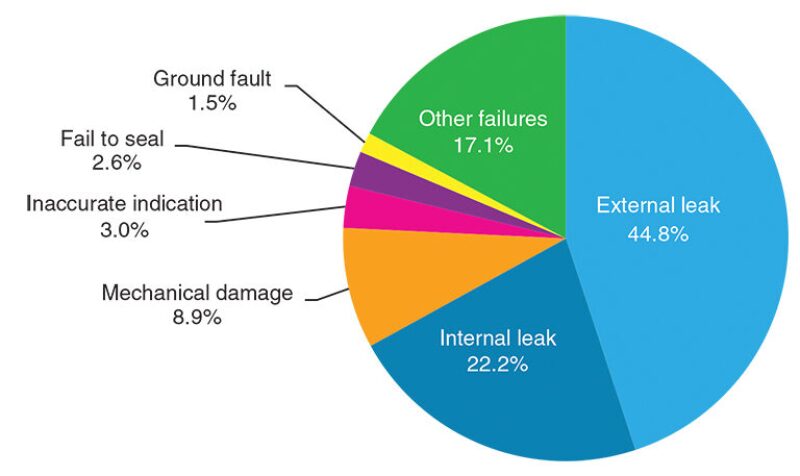
Growing Problem
When it came time for investigators to bring the BOP from the Deepwater Horizon on shore for analysis, the BOEM report said they required a “test pad capable of supporting an approximately 325-ton BOP stack.”
Since Macondo, the weight of BOPs stacks has ballooned. After the one blind shear ram on the Macondo failed, regulators required two of them to ensure the well is shut off even if one fails. That pushed the number of rams commonly found on stacks to seven and the weight to around 450 metric tons, according to a chart from Dale.
To ensure a comfortable margin for shearing, more racks of accumulator bottles, which store fluid under pressure, were added to the stack to ensure it had enough power to consistently shear tougher drillstring components.
As drilling moved to deeper water, more bottles were required because the higher water pressure reduces the output of each of the tall, heavy bottles. None are needed in the Transocean system or for electric BOPs, which eliminate other hydraulic components on the rig and subsea.
The next generation, built to shut off a 20,000-psi well (20K), increases the weight another 50% to 680 metric tons.
Dale uses those numbers to argue that new technology is needed to reduce the weight of BOPs working in deeper, more hazardous environments. An electric design that is the equivalent of a sixth-generation 15,000-psi stack would weigh about half as much, around 225 metric tons, with an umbilical providing power to a battery and a fiber-optic line for data and communication, he said.
The fact that the alternative power systems weigh less could become a motivator of change because BOP stacks as as tall as a suburban office tower stand on a wellhead.
Two companies are selling a tethering system to reduce the risk of wellhead stress—Oceaneering and Trendsetter Engineering—while a third is offering a foundation around the wellhead for greater support—Neodrill.
“This wellhead is already screaming for help. I have heard of 20K BOPs close to 700 mm metric tons, that is 1.4 mm lbs. It is saying help!” Dale said.
Dale’s 20K weight estimate is close to the one offered by NOV, which has sold the first 20K BOP. But Bob Cowan, the product technical manager at NOV who answered a question about weight after a presentation at the 2020 IADC/SPE Drilling Conference, suggested it was a manageable concern.
He said they will be monitoring wellhead fatigue and the BOP’s position to see if the added weight is having an effect.
Shearing and containing pressures and temperatures that high require increased equipment size. The weight of the rams alone will rise from 350 lbs in the 15K BOP to 1,200 lbs in the 20K model.
Still, the power source behind the K-BOS is tiny in comparison. Bobby Gallagher, the CEO of Kinetic Pressure Control, showed the cylinders, not much bigger than a large can of juice, used for the propellant.
The startup has a collection of huge hunks of steel cut. Last fall and winter Kinetic held monthly demonstrations for prospective users. They watched the K-BOS sever hard-to-cut items, from wirelines to a thick-walled 6.9-in. (OD) landing string pressed to a wellbore wall by 130,000 lbs of pressure, Kinetic said.
It was all done in less than a second using a device Gallagher described as a gate valve. Transocean’s Pelley said, “The K-BOS machine is an emergency device that allows operational benefits in the form of longer, heavier casing strings, for example, while also mitigating the risk associated with a loss of well control.”
Regulators who have seen the machine work in deep water will need to write new rules to test whether it is ready to go.
BSEE has long required BOPs to be function-tested every 14 days by closing and opening the rams. The Kinetic unit is like an airbag: once it has been fired, the charge has to be replaced.
The agency declined to comment on whether it will adjust regulations to suit these new technologies. Offshore regulations allow alternative equipment and procedures if they can meet or exceed the required level of safety and environmental protection.
Innovators say they can do that, though it will require a different approach to verifying something is ready to go.
Dale said the traditional function test would be like testing a car’s airbag by going out and slamming the steering wheel with a sledgehammer.
Gallagher has spoken to regulators about using reliability measures applied in the aerospace business to show these devices are “orders of magnitude” more reliable than the current shearing devices. The device meets military-grade reliability standards. (1 in 10,000 chance of failure).
There is no equivalent measuring system for BOPs. Traditional hydraulic systems do not provide the same level of real-time data as electrically controlled ones.
Ensuring the propellant is ready to trigger the gas generator is the critical question, Gallagher said. That can be checked every second. Based on experience, when that much force is applied, the likelihood the rams will close is high.
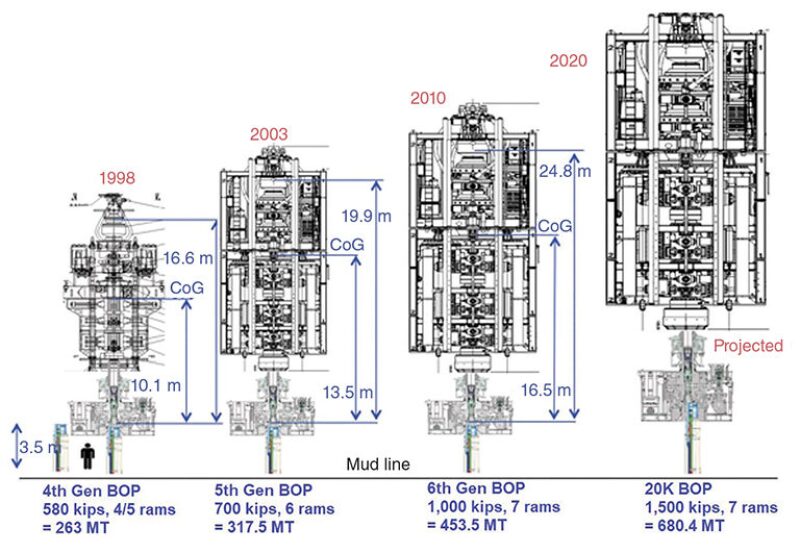
Process of Elimination
Kinetic and ESD are two of the surviving members of a group of six startups working together to find ways to commercialize well-control innovations. This subcommittee, which is part of SPE’s Drilling Systems Automation Technical Section, has been paused, said Trey Mebane, a consultant involved in the subcommittee who was formerly vice president of innovation at NOV.
Bastion stopped working on its BOP idea in favor of working on paying oil technology projects, Bedrosian said. Another innovator decided it was time to take an engineering job to support his family, said Mebane.
The barriers to entry to the well-control business include the glacial pace of change. BOP product development timelines are long enough to kill most startups.
During his talk at the IADC/SPE Drilling Conference, Cowan said, “15K BOPs were designed when I was a young man.” For those wondering how long ago that was, he added, “I have had 45 years in the business.”
Like NOV, Baker Hughes and Schlumberger put in years to develop a 20K subsea BOP, but so far only NOV has sold one.
With no sale in sight, Dale uses his income from another subsea engineering project to design a subsea rotating control device to pay the modest overhead at ESD, which is looking for someone to build the design acquired from MHWirth in September 2017.
He predicts he will prevail because “I am a believer, number one. The next thing is I never give up; that is important.” He strongly believes that the economic and safety benefits of electric BOPs will be essential in the future, both onshore and offshore.
While Kinetic and ESD have tried to sell their BOPs to onshore users, no sales have been made so far.
A rare public sign of industry interest was an item in Equinor’s proposal for a rig of the future that said its drive to electrify subsea operations includes considering an electric BOP.
The technology risk is limited because these alternative power sources have been proven to be reliable in other subsea applications, said Pelley.
The bigger barrier is psychological. Hydraulic power has been at the heart of BOP design for longer than most engineers have been alive.
Pelley said decision makers are reluctant to take a “step into the unknown” because “consequences of failure are very high.”
But that could change if someone began successfully doing something different. “Once you prove to the players in this market you can make that change, that psychological lid will crack. They will become less fearful,” Mebane said.