As a field matures, there is a crucial need to focus on integrity-related issues such as hazard prevention and mitigation. During the initial field development of D field offshore Terengganu in Malaysia, the well design was fit for purpose to meet production needs. However, extension of production requirements contrary to earlier plans, a production-driven operational philosophy, and irregular well-integrity surveillance have compounded integrity issues. To rectify this trend, a field redevelopment was based on a number of concrete steps.
Field Overview
D field is an oil- and gas-producing field that saw its first hydrocarbon discovery in 1981. After a series of appraisal wells and the formulation of a field-development plan, the field’s first oil production was realized in March 1991. The field’s primary production is oil from multistack major reservoirs X1 and X2, with 30 to 70% CO2 concentration. D field has a total of four producing platforms, consisting of one main platform with three satellite platforms. The production streamlines from the satellites undergo separation processes at the main platform before collection at the floating storage and offloading facility.
Currently, the field is operating with a total of 218 completion strings. The main platform consists of a separation-process unit, a water-injection module, a gas-injection module, and a produced-water-treatment system. Dedicated gas and water pipelines run to each satellite platform, meeting the requirement of water and gas injection to the reservoir as part of the reservoir-management plan. In addition, enhanced-oil-recovery (EOR) implementation is being assessed as part of the effort to increase production.
Problem Statement
From 2010 to 2012, a 60% decline in daily production rate was observed, largely as a result of integrity issues. Operating under a wide range of CO2 concentrations in hydrocarbons poses a challenge in the initial material selection for well completion, which can in turn greatly affect well integrity and life span. Furthermore, the early-optimization philosophy for water and gas injection led to the use of one well slot with dual-utility well completion, which complicates well intervention and deteriorating well-integrity assurance because of the difference in operating temperatures between the two strings in a wellbore.
Extensive diagnostic surveys and well-integrity logging were conducted from 2010 to 2012 in order to determine the condition of subsurface well integrity and safeguard the production and reservoir-management-plan requirements for the EOR project. To ensure deliverables, the team has adopted a series of systematic guidelines to diagnose well integrity.
Subsurface Integrity Diagnostics
Rapid Increase in Water Cut. From the key observation wells, the team noted a steep increase in water-cut percentage; in one example (Well AA), this percentage rose from an initial 18 to 80% within 2 consecutive years of monitoring. From this observation, the team has initially estimated that leaks in completion strings most probably have occurred because of an operating strategy of simultaneous water injection and oil production in one well slot in most of the D-field wells.
Sudden Drop in Oil Production. In again considering the example of Well AA, the steep unexpected increase in water production has caused a significant reduction in oil production. This was believed to be caused by the increase in hydrostatic pressure in the annulus that significantly reduced the oil column in the production strings overtaken by water.
Abnormal Pressure Profile. Here we use the example of Reservoir X-3, which was simultaneously produced from the group of six observation wells that had shown a stable pressure profile in the course of 7 years of production. It is important to note that Reservoir X-3 is not the main producing reservoir in D field. X-3 is a natural-depletion reservoir, a term used by the team to describe a reservoir with no water-injection support from the injector wells to maintain the pressure. However, the reservoir pressure monitored from these six wells experienced a steady decline that ended in 1998, but in 2001, the pressure increased by 200 psia, with a steady increase until the end of 2007.
This phenomenon is probably caused by production-tubing leaks in single or multiple wells concurrently producing from and injecting to the other reservoirs in D field. The injected water, intentionally dedicated to support other reservoirs, has traveled to Reservoir X-3 because of leaks in completion strings, which in turn caused high water production recorded from the reservoir’s producing wells.
High Casing Pressure. Daily surveillance on well parameters such as flowing tubinghead pressure, production-casing pressure (PCP), intermediate-casing pressure (ICP), and flowing production-string-head temperature allows the team to identify anomalies in well conditions. Early signs of communication between casings can be detected if PCP (Annulus A) exceeds 2,000 psi and ICP (Annulus B) exceeds 300 psi. The communication between casings is further confirmed by bleeding off the pressure at the respective annulus and monitoring to see if the pressure builds up in the annulus by more than 50% within 24 hours after the attempt. Communication between casings is treated as a high health, safety, and environmental priority. Should the situation be encountered, the well is required to be secured and tested further to confirm the existence of leaks, and remedial action is to be taken.
Well Intervention
In place of the requirement to perform field-performance analysis and reservoir studies by operating per a consistently optimum-condition reservoir-management strategy, the D-field team has initiated and executed routine reservoir-data gathering in all of its 170 wells, which further confirmed the existence of poor well integrity after 20 years of production. For a detailed discussion of these findings, please see the complete paper.
Well Workover
Once the well-integrity condition is confirmed through surface data and well-survey data, the condition is then evaluated. If possible, internal patching (completion string and casing) will be conducted to rectify the integrity issues. However, in order to secure the well’s safety, ensure continuous production, and ensure reserves recovery, a workover is required should the well present conditions indicating that it is beyond rectification, such as multiple holes and leaks in the completion string, annulus communication, and packer leak causing crossflow between reservoirs.
Therefore, with multiple wells experiencing severe well-integrity issues beyond rectification and in preparation for a future EOR program, a massive workover campaign was carried out between 2009 and 2012 in D field. In the course of the workover campaign, the downhole condition was confirmed further on the basis of the completion string and well accessories retrieved to surface from various wells (Fig. 1). Internal and external corrosion can be detected on the major completion accessories.
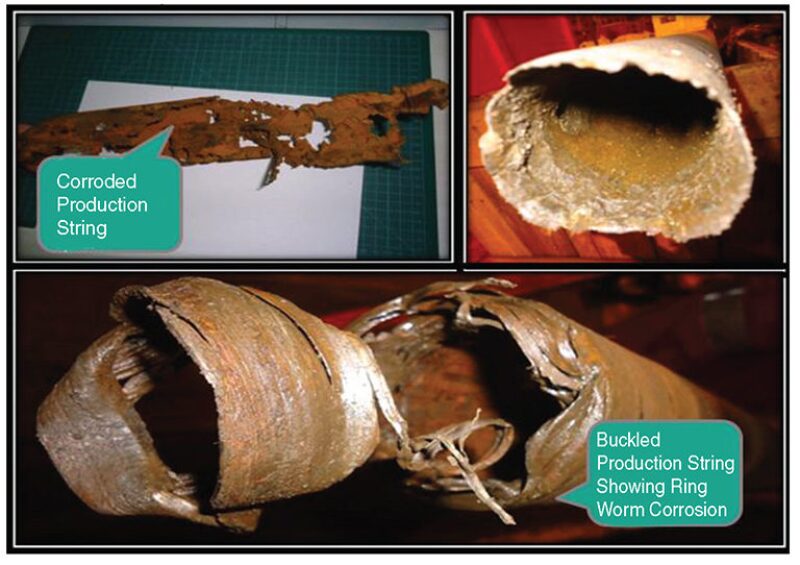
Casing Integrity
On the basis of the severely corroded condition of the completion string retrieved during the workover activity, the casing integrity becomes suspect. The team has initiated and executed a series of casing-integrity tests to ensure the ability of the casing to withstand pressure during production with no potential hazard to the environment. In addition to the casing-injectivity tests that were performed to ensure casing reliability, a series of cased-hole logs with sonic and ultrasonic capabilities was executed to ascertain not only the integrity of the casing but also the bonding quality of the cement behind the casing.
In one example from Well DD, the interpretation result of the survey’s corrosion mode was able to show a significant degree of metal loss ranging from 30 to 50%, mostly located near or between the fluid-entry points at the perforation area. In an instance from Well EE, the ultrasonic interpretation of a significant portion of the casing revealed the disturbing occurrence of a microannulus filled with gas (from the reservoir secondary gas cap) in the cement above the main production zones. To ensure the safety of the environment with respect to the hazards caused by a potential leak of production fluids, the team decided to perform a remedial squeeze cementing on Well EE, resulting in a major improvement in the cement-bonding quality.
However, the poor casing condition in Well DD made that well particularly hazardous for a new recompletion in the same slot. Hence, the team put forward a plan to reuse the slot by performing a plug-and-abandon operation in the existing wellbore, starting from the poor-casing section and extending to the bottommost depth of the original slot, followed by a sidetracking of a new target above the abandoned section to secure and deliver the remaining reserves of the well.
Controlling the Corrosion Rate
Corrosion is inevitable. Therefore, the only possible control that can be applied in a completion string is control of the corrosion rate. The corrosion rate increases as the temperature, pressure, and stress increase during production. Corrosion will occur with the appearance of an anode, a cathode, and an electrolyte, which promote the oxidation and reduction processes of metal.
A high concentration of carbon dioxide, together with high-water-cut production, promotes the formation of carbonic acid. The acidic substance will then react with iron to form sidetrite scale, forming a protective film on the walls of the completion string because the scale is nonconductive in nature, thus preventing galvanic corrosion occurrence. However, crevice and pitting corrosion will occur when carbonic acid is formed. Additionally, the presence of CO2 will cause embrittlement, which in turn results in stress-corrosion cracking, causing mechanical failure of the completion string (Fig. 1).
There are also biological factors to consider in corrosion-rate control. Injection-water quality should be monitored for the presence of sulfate-reducing bacteria (SRB). SRB metabolize sulfate ions of an organic carbon source, thus introducing hydrogen sulfide (H2S) into an H2S-free system. This will then accelerate the occurrence of crevice corrosion in the completion string. Furthermore, other factors can influence the corrosion rate, including an erosive production environment and the selection of completion metallurgy.
This article, written by JPT Technology Editor Chris Carpenter, contains highlights of paper SPE 165634, “Mature-Field Subsurface Integrity: Formulation of a New Paradigm Through a Holistic Diagnostic Approach for D Field, Malaysia,” by Wan Rokiah Ismail and Almag Fira Pradana, Petronas Carigali, prepared for the 2013 SPE Latin American and Caribbean Health, Safety, Social Responsibility, and Environment Conference, Lima, Peru, 26–27 June. The paper has not been peer reviewed.