Two alkali/surfactant/polymer (ASP) floods became operational in the Taber area of Alberta, Canada, in 2006 and 2008. Throughout the course of both projects, extreme scale deposition was observed. Scale-inhibition and -remediation strategies were developed that included a comprehensive monitoring program, chemical scale inhibition, and mechanical scale-prevention techniques. From the large amount of data gathered, models were created to predict scale severity and content and to develop specific mitigation plans.
Introduction
In southern Alberta, the Mannville B Taber South (Warner) pool was discovered in 1963 and has been under waterflood since 1967 and the Glauconite K Taber (Crowsnest) pool was discovered in 1943 and has been under waterflood since 1971.
The Warner ASP flood was the first fieldwide ASP flood in Canada and began injection in May 2006. The Crowsnest ASP flood began injection in January 2008. Both floods used a 0.75-wt% concentration of NaOH as the alkali and continue to use recycled produced water for injection.
Scale and its associated problems and mitigation strategies have evolved over the course of these projects.
Scale Problems
Scale problems started at Warner toward the end of 2006, approximately 8 months after the start of ASP injection. During the next 12 months, it became evident that run life of pumps had significantly decreased on some wells. Scale was building up at the pump intake or inside the pump and reducing the flow of fluid into the pump. Most pump failures were preceded by the rapid loss of pump efficiency, combined with a high producing fluid level and increased torque on the rods. Most wells with failures did not have a significant buildup of scale outside of the pump.
By the end of 2007, it became clear that reduced run life was a full-field problem. Some wells were experiencing extremely short run life, with pumps lasting less than 1 month. As the ASP flood progressed and more wells experienced increased pH and other conditions favorable for scale formation, the pipelines and the facility also started to see scale problems. Pipelines had been accumulating scale slowly, and the rate of scale deposition increased as more wells started to scale. Toward the end of 2007, the gathering-system pressure had increased substantially and, in one instance, flow through the pipeline was completely blocked (Fig. 1 above). At the facility, various valves and meters failed because of interior scale buildup. The injection pumps also failed because of scale on mechanical seals.
Scale Mitigation
Mechanical Inhibition. To avoid significant scale buildup in the facilities, all piping and equipment that had scale buildup was internally coated to prevent scale from adhering. Pipelines were replaced with coated piping where flow restrictions could cause a pressure change that would initiate scale deposition. In an effort to reduce deposition in these areas, valves and header systems were coated internally. Finally, an aggressive and frequent pipeline-pigging program was put in place to keep production lines free of scale buildup.
Chemical Inhibition. Initial analysis of the scale showed that a significant portion was calcium carbonate based. Numerous chemical treatments including acids and bases were bottle tested to break or dissolve the scale. Minimal chemical reaction was observed with any chemical, even after long periods of exposure. This behavior was not typical of a calcium carbonate scale, and further analysis proved that organic amorphous silicate was also present. No successful procedure was found to dissolve or treat the scale. Consequently, the only options were to prevent the scale from precipitating or to remove it mechanically. At first, the scale was a combination of calcite and amorphous silicate, with the majority being calcite. Previous research suggested that, if the calcite were inhibited, it would prevent the silicate from precipitating. A chemical scale-inhibition program targeting calcite was implemented, initially on problem wells and later on almost every producing well. Scale inhibitor was injected into the well annulus on a continuous basis. The inhibition of calcite proved very successful at first, and the deposition of the mixed scale was effectively stopped. Problem wells did not experience failures until the next phase of scale. Inhibiting scale at the wells also reduced scale buildup in pipelines and at the facility.
Silicate Scale
The inhibition program using calcium carbonate inhibitor was put in place in early 2008 and was very successful for the first 6 months. The program -increased pump run life significantly and resulted in minimal or no scale buildup in pipelines or facilities. In late 2008, serious scale problems returned, indicated by numerous well failures and significant buildup of scale on downhole equipment. Servicing frequency increased dramatically, and the run life of pumps in some wells was less than 1 month (Fig. 2). Analysis showed that the proportion of silicate in the scale samples had increased. It was clear the calcium carbonate inhibitor was no longer effective at preventing the silicate from precipitating.

The scale deposition was so severe that some wells were completely full of scale. Many wells had rods scaled into the tubing, and scale was often present on the entire length of rods and on the inside and outside of the tubing. Removal of the scale was extremely difficult and could only be achieved through mechanical means.
Servicing work would often require complicated fishing operations on equipment stuck in the hole. In other wells, scale deposition was so severe that equipment was cemented into the wellbore and abandonment was required. In extreme cases, some wells were so scaled that the decision was made to suspend or redrill the wells.
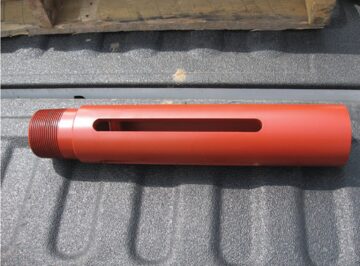
Silicate-Scale Mitigation
Mechanical Inhibition. Several mechanical solutions to prevent or slow scale buildup were implemented, including a slotted tag bar at the bottom of the progressing-cavity pump (Fig. 3) and coated no-turn tools (Fig. 4). Significant scale deposits were often located at the pump intake, so the slotted tag bar was constructed to increase the surface area of flow into the pump, which reduced the pressure differential at the intake. Coating the tag bar and the no-turn tool was performed to prevent scale from sticking to the equipment as much as possible in the area most detrimental to production. Several types of coatings were tried on the progressing-cavity rotors, with limited success. Scale did not appear to stick to the coated equipment and polylined tubing as easily as it did to bare steel, but scale buildup did occur if given enough time.
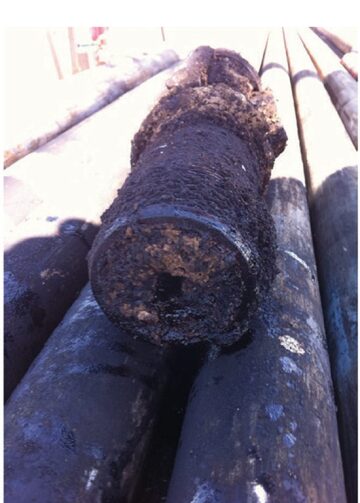
Chemical Inhibition. Field trials were performed with high concentrations of calcium carbonate inhibitor, but with little success. It was clear that the calcite inhibitor used for most of 2008 was no longer effective. Scale could not be removed once deposited; consequently, silicate inhibitors were needed. Existing commercial silicate-scale inhibitors were field tested and were found to be ineffective. New scale inhibitors had to be developed. Laboratory-test results showed that the scale inhibitors could not completely prevent the silicate-scale formation but that they could delay it. Laboratory analysis generated and tested potential inhibition efficiency, but much of the success came from piloting inhibitors in the field. After initial trials, the primary conclusion was that the same scale inhibitor had significantly different levels of effectiveness, depending on the inhibitor concentration and on the water chemistry of the individual wells. Inhibitors were field tested in each well until a successful product and a proper concentration were found.
Monitoring
Monitoring of the scale-inhibition program proved to be very important. On the basis of the data collected, it was concluded that, as the chemistry of the produced fluids changed over time, different scale inhibitors at different concentrations were required. As the ASP fluid moved through the reservoir, the producing well encountered various pH values and concentrations of silicate, calcium, and magnesium. Applying the proper chemical at the proper set of conditions was very important.
Many different silicate-scale inhibitors and concentrations were field tested, and corresponding data were collected. As a result, a system was set up to track how effective a given inhibitor was in a particular well.
A monitoring program was already in place for monitoring the ASP floods, including performing a water analysis of the produced fluid at each well on a monthly basis. The items tracked from the analysis included polymer concentration, calcium, magnesium, iron, sodium, total dissolved solids (TDS), and pH. Silicate content was first measured in 2009. The scale-inhibition chemical being used was tracked along with rate and concentration.
To estimate the scale-deposition rate in the wells, steel coupons were installed at the wellhead on scale-problem wells. Coupons were checked monthly for scale buildup. Analysis of the scale coupons was performed on a qualitative basis by assigning an evaluation to the coupon. The ratings used were: no scale, film, light scale, loose scale, scale, and heavy scale. Changes in the amount of scale on coupons were used to make changes to the inhibition program. The coupons were used to detect changes in the rate of scale deposition in the well. Pump information, including pump efficiency, torque, and fluid levels, was used in conjunction with the scale coupons to evaluate the performance of the mitigation program and to adjust it accordingly. This included adjustments to the concentration of scale inhibitor or switching to a new inhibitor.
Data were gathered for 7 years at two commercial ASP floods. After compiling and analyzing the degree of success of 12 different inhibitors, a model was created to select an ideal scale inhibitor for a given set of conditions in a well, such as pH; water production; amount of silicon, calcium, magnesium, iron, and sodium; and TDS. The model recommends the optimum scale inhibitor and concentration. After a new product is applied, data are collected continually to evaluate the performance of each inhibitor and optimize the concentration or product selection. The data used to create the model continue to grow and are used to increase understanding of scaling tendencies.
This article, written by Special Publications Editor Adam Wilson, contains highlights of paper SPE 165285, “The Use of Modeling and Monitoring To Control Scale in Alberta ASP Floods,” by Kate Hunter, SPE, Lee McInnis, SPE, and Tyler Ellis-Toddington, SPE, Husky Energy, and Scot Kerr, Baker Hughes, prepared for the 2013 SPE Enhanced Oil Recovery Conference, Kuala Lumpur, 2–4 July. The paper has not been peer reviewed.