High-fidelity 3D engineering simulations can be valuable for operators looking to predict the behaviors of various components in their operations, but the computational requirements of these simulations can make them cost-prohibitive. To help alleviate the cost pressures, companies are examining the potential of integrating deep-learning neural networks (DNN) with computational fluid dynamics (CFD) to accelerate the simulation process.
Speaking at an SPE Gulf Coast Section CFD Study Group symposium on digital solutions for fluid flow problems, Kuochen Tsai, a staff engineer/researcher in CFD modeling at Shell, outlined the development of a DNN model trained by CFD simulations that would be capable of predicting oil/water separation in horizontal oil pipelines. The goal of the model was to provide useful information for operators to effectively determine the use of corrosion inhibitors, which could have significant financial and environmental impacts if used improperly.
Tsai said that multiphase flow simulations in CFD require expertise to set up, and their computational requirements can be expensive both in time (where they can possibly take months to complete) and in money. Implementing CFD results in more-accessible correlations requires a high number of independent variables, and that complexity can be problematic for operators.
“The complexity can be overwhelming, especially with the variables you need, but without it, the model is not very useful,” Tsai said.
Modeled loosely after the human brain, neural networks are a set of algorithms designed to recognize numerical patterns. They interpret sensory data through a kind of machine perception in which they label or cluster raw input. Compared to more commonplace single-hidden-layer neural networks, deep-learning neural networks require a higher number of node layers for data to pass in a multistep process of pattern recognition.
Machine learning in general, and DNN models in particular, can provide a systematic way to optimize high-dimensional interpolations, providing a possible route to archiving complex CFD results. Tsai said it can be effective in learning CFD simulation, even for 2D data.
Large quantities of data can be obtained through CFD simulation, which Tsai said is critical for data learning, but the downside is the time needed to run these simulations covering the parametric space [all possible combinations of values for all the different parameters contained in a particular mathematical model]. Recently, DNN algorithms have gained momentum in the way that they automate the construction of correlations between input and output data, allowing complex hyper-dimensional correlations to be built with higher accuracy and in shorter time frames. Tsai’s presentation focused on the construction of a DNN that could replace the time-consuming CFD simulator.
The CFD model Tsai discussed was developed over a 4-year period. It is designed to model oil/water separation in horizontal pipelines to predict the water wetting probability on carbon steel pipeline surfaces, which is important in determining possible corrosion. The model was validated extensively over the range of water cut, pipe diameter, fluid viscosity, surface tension, and mixture velocity. By parameterizing the CFD simulations, Tsai said it was possible to pre-calculate results in all necessary parametric spaces and use those results to train the DNN model.
“The DNN model is efficient,” Tsai said. “The good thing is that parametric space is well defined. You have your water cut, you have your pipe diameter, your pipe length, your velocity. These have all been well-defined.”
The DNN was used to predict the water/oil profile at the steady-state conditions where a solution no longer changes. It used 42,600 data samples, split randomly into a training set with 34,060 samples and a test set with the remaining 8,520 samples. The model took 2.5 seconds to train, compared to 30 minutes on the CFD model, and inferencing time on a single CPU core was 4 milliseconds. Tsai said the neural network model improved on the CFD model’s performance by six orders of magnitudes.
Validation of the model’s performance required a new data set with 1,775 samples corresponding to five pipeline core sections. The model used the inputs from the new data set to predict the outputs and compared those predictions with the CFD simulation outcomes.
Tsai discussed the preliminary results of the model testing in two parametric spaces, water cut and mixture velocity. The trained model showed high accuracy, with mean square errors of less than 0.01 in all cases. Total inference took 15 milliseconds for the five core sections on the laptop computer compared to a range of 30 minutes to 2 hours on 48 computer cores for the CFD simulator.
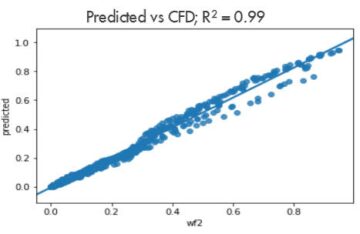