In an effort to develop new measurement technologies for ultradeepwater oil and gas production, the US Department of Energy’s National Energy Technology Laboratory under the Research Partnership To Secure Energy for America (RPSEA) has initiated a new project. This project, titled More Improvements to Deepwater Subsea Measurement, has addressed those gaps that were identified by an earlier RPSEA project as the most pressing for multiphase-flow measurement.
Introduction
Approximately 15 years ago, as offshore production in the Gulf of Mexico and elsewhere moved off the continental shelf and into truly deep water, it became apparent that methods of measuring the flow of oil and gas would have to change in a significant manner. Not only did formidable technical challenges exist in performing production tests on wells that were many miles away in 1000 m or more of water, but the economics of installing test lines to perform such tests simply was not acceptable. Production from many wells would be commingled, and one of two alternatives would have to be chosen: Either a clever way of testing well rates from the combined flow would be developed, or each well’s rate of production would be measured before commingling.
Discussion
History. Past efforts of RPSEA and others to research improving deepwater exploration-and-production operations are detailed in the complete paper.
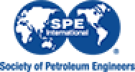