The IADC/SPE Virtual International Drilling Conference held last week helped bolster the argument that if you want to see the bleeding edge of offshore technology, look no further than the Norwegian Continental Shelf (NCS).
Operators and service companies in the region used the annual event to showcase drilling innovations that after years of research and development are now poised for widespread use.
Among them is an unorthodox alternative to measurement-while-drilling (MWD) from Equinor that uses technology originally conceived for 4D seismic to track drill bits in real time.
Halliburton is also claiming a major breakthrough in automated drilling while Schlumberger touts a lost-circulation material that is making drilling through thief zones and within narrow-margin sections easier and safer.
Real-Time Bit Tracking With Seismic
In 2014, Equinor laid down nearly 3,500 seabed sensors over the Grane heavy-oil field for biannual seismic shots to see how the reservoir was changing, an approach known as 4D seismic.
The array was also used for microseismic monitoring of gas-injector wells, and it was while analyzing some of that data that petrotechnicals at Equinor discovered a signal coming from where an infill well was being drilled.
This eureka moment led the offshore operator to spend the past few years creating and testing a work flow to routinely use the array for real-time drill-bit tracking. Equinor considers this a highly cost-effective technique since it leverages the array while in passive mode, meaning no seismic vessels are needed to pulse the subsurface.
“What we are doing is listening to noise generated by the drill bit, or more generally the [bottomhole assembly] and trying to localize it,” Marianne Houbiers, a principal researcher of reservoir geophysics at Equinor, said while presenting the conference paper (SPE 204039) that details the novel approach.
She emphasized that the top business driver comes down to the shortcomings of position surveys based on magnetic and gyroscopic MWD tools.
Magnetic-based surveys might be thrown off by nearby casing, potentially a big problem for infill drilling, or when drilling east to west at high latitudes. For other reasons, MWD with gyros can also lead drillers astray as the bit moves closer to total depth.
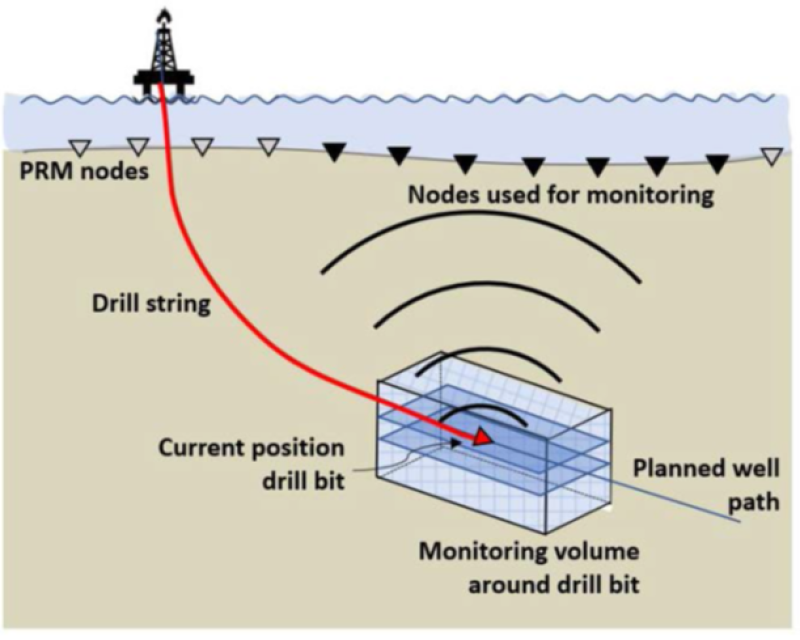
Houbiers showed an example from the Grane field in which the ellipse of uncertainty from a gyro tool widened out from 32 m on either side of the well path to 54 m as the bit moved about 2200 m deeper into the formation.
In clear contrast, the pulsing seismic signals from the drilling action offer little ambiguity as to the lateral positioning of the bit. With that, a more trustworthy well path can be updated and visualized.
One way that Equinor validated seismic bit tracking was to simply look at the rate-of-penetration data. Houbiers described the correlation as “strong,” which might be an understatement.
“We hear the drill bit when they are drilling into new formation. We don’t hear any noise when a new stand is added to the drillpipe,” she said, adding that it is as if the distinct signal “is being switched on and off.”
A feature of this approach involves using only a part of the seismic array at a time and focusing on a defined volume of rock that could be 200 m2 or 400 m2.
Within such a box, Equinor takes a look at the seismic data every 90 seconds and can do so in a relatively low-resolution manner without having trouble finding the bit location. This is key to the concept because it “ensures that we are able to process the data in real time with limited compute resources,” explained Houbiers.
Since 2018, Equinor has used seismic bit tracking on every new infill well in the Grane field and has recently expanded testing to its other offshore fields that have permanent arrays.
There are other use cases too, including the detection of serious issues such as a liner failure or to confirm where perforation shots happened.
The operator is also looking at how to use the drill bit as a seismic source for look-ahead-drilling applications. The early learnings on this front were shared at the conference in a separate paper (SPE 204060) presented by Norwegian geophysical monitoring firm Octio.
RSS Automation Comes of Age
Halliburton’s latest rotary-steerable system (RSS) is a reminder that the age of automated drilling is not coming, it is here. This is the message driven home by one of the company's conference papers (SPE 204016) that covers how its automated RSS drilled the entire curve section of an offshore well operated by Aker BP with zero human overrides.
The autonomous tool covered 1630 m in 29 hours, equating to an average rate-of-penetration of 56 m/hr—1 m/hr above the pre-job target.
Directional drillers monitored the job from the comfort of an onshore control center. The operative word there is “monitored.” In addition to no longer being needed on the rig, directional drillers are increasingly not needed to drill.
“Normally today, the people executing the job—in terms of the directional driller—are performing an active role,” said Jorge Heredia, a senior technical advisor at Halliburton. “With this new model, they go to a more supervisory role. So, it’s more about planning and communication.”
Heredia is the lead author of the paper and while presenting it said that drilling this particular well, which had a complex trajectory, with automated technology “would have been unthinkable only a short time ago.”
Two of the chief innovations that Halliburton credits with turning that around are:
- An autonomous downhole navigation system that is built from an array of sensors, high-speed processors, and surveying units. This system maintains attitude and minimizes the number of downlink commands required to correct bit trajectory.
- The automation and advisory systems used for deviated steering ingest real-time information that flows down from the surface. Outputs feed a hybrid model that includes a digital twin of the bottomhole assembly and a calibrated steering model. This cyber tandem removes the traditional method of manually interpreting data, thus reducing human error.
The featured well was drilled about a year ago in the NCS and Halliburton says the commercialized tool has since been sent downhole in other parts of the region and elsewhere around the globe.
Lost-Circulation Innovation Solves Guess Work
The episodic loss of drilling fluids into the formation during drilling has been the source of much heartburn for operators over the decades. For service companies, it has been the source of a long stream of innovative ideas on how to stop these potentially dangerous wellbore evacuations.
That includes Schlumberger, which shared details at the conference (SPE 204062) on a new lost-circulation material that has been validated offshore Norway with Aker BP. The service company calls it a reinforced composite mat pill (RCMP) treatment.
Jose Barreiro, a cementing technical engineer with Schlumberger, explained that the technology is made of “flexible fiber additives that use synergy between the physical characteristics of fibers and customized solids to bridge fractures.”
The material, delivered in liquid containers to the rig, is designed to be used during drilling or in preparation for cementing jobs. Schlumberger says it has proven to reliably plug fractures up to 1 mm wide, plenty large enough to lead to the total loss of drilling fluid.
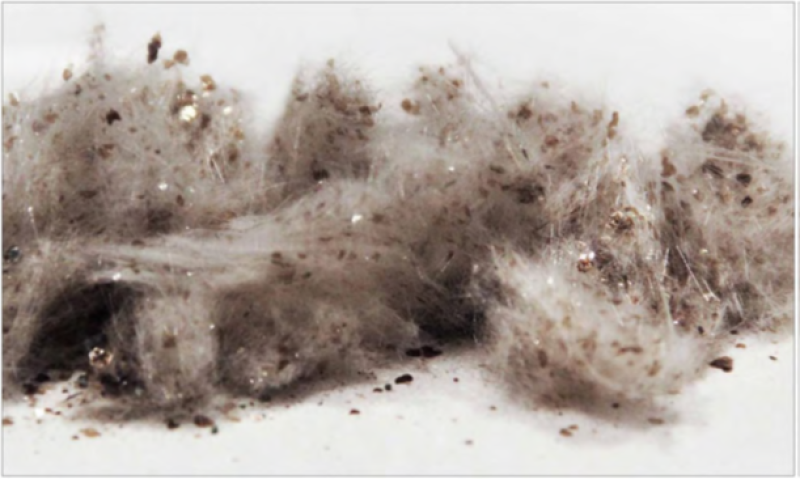
In further describing how the RCMP works, Barreiro said, “The fibers in the reinforced composite mat pill form a network at the mouth of the fracture. The solid particles then reach the fiber network and fill up the spaces between the fibers to stop the flow of drilling fluid or other wellbore fluids into the fracture.”
Since the case study, Aker BP has built the use of RCMP into its best practices and Schlumberger reports its use in at least 15 wells for various operators offshore Norway. The service company has also begun a global deployment.
Barreiro stressed that one of the most important aspects of the technology is that engineers do not need to run a plugging-efficiency test before pumping it down the well. When losses occur, he said, “time is always very short, and any additional time spent designing a lost- circulation package can become a costly exercise for the operator.”
Operators can trust this, he added, because of the technology’s consistent performance offshore Norway where the pre-job acceptance criteria have been met “on each and every occasion.”
Schlumberger is now looking beyond lost-circulation events and has used RCMP for wellbore-strengthening operations, i.e., stress caging, narrow-margin drilling.
For Further Reading
SPE 204039 High-Precision Drill Bit Tracking by Marianne Houbiers, Equinor, et al.
SPE 204060 Real-Time Lookahead Imaging Using the Drill Bit as Seismic Source by Alexander Valentin Goertz, Octio, et al.
SPE204016 Automated Directional Drilling is Now a Reality - An Example from the Norwegian Continental Shelf by Jorge Heredia, Halliburton, et al.
SPE204062 Successful Application of a Reinforced Composite Mat Pill Technology for Lost-Circulation Control in the Norwegian Continental Shelf by Jose A. Barreiro, Schlumberger, et al.