Advanced well completions have proven to be an effective method of moderating gas breakthrough while producing a thin oil rim when placed in a heterogenous, carbonate reservoir. In addition, several studies have proven that the application of autonomous inflow control devices (AICDs) acts as a type of insurance policy against geological and dynamic reservoir uncertainties to reduce the risk and variation in the expected oil production profiles.
During 2019 and 2020, Sarawak Shell Berhad conducted development campaigns in the central Luconia province in a thin oil rim carbonate reservoir offshore Sarawak, Malaysia. The horizontal, approximately 6,000-ft development wells were expected to intersect with different geological layers with varying rock properties, resulting in an uneven reservoir influx toward the wellbore. Oil production from these wells was expected to suffer severely from early gas and water breakthrough.
To produce the oil rim without the risk of early gas production, global production optimization specialist, Tendeka, incorporated FloSure AICDs in the lower completion design at the reservoir interface along the horizontal section of the wells. As an active flow control device, the technology delivers a variable flow restriction in response to the properties of the fluid entering the wellbore and the rate of flow passing through it to help manage gas coning/cusping risks. The fluid is then lifted to surface with natural in-situ gas lift built into the upper completion. A three-phase development was planned for the field, and to date, two phases have been completed.
New-Generation ICD
The first AICD completion was installed in Norway in 2008 and widely implemented in the Troll field in 2013 with very encouraging results (SPE 159634). However, its use is relatively new to both the Asia Pacific region and this type of application.
Similar to a standard ICD which balances the influx of reservoir fluids, the FloSure AICD will delay the production of unwanted effluents prior to their breakthrough (proactive solution). However, once a breakthrough occurs, the device restricts the production of unwanted effluents with lower viscosity, such as gas (in light oil applications) and both gas and water in viscous oil production (reactive solution) (OTC 30403, OTC 30363, SPE 193718).
The device delivers a variable flow restriction in response to the properties of the fluid and the rate of flow passing through it. Flow enters the device through the nozzle in the top plate of the body. This impacts the disk and spreads radially through the gap between the disk and the top plate, then turns around the top plate and is discharged through several outlet ports in the body (Fig. 1).
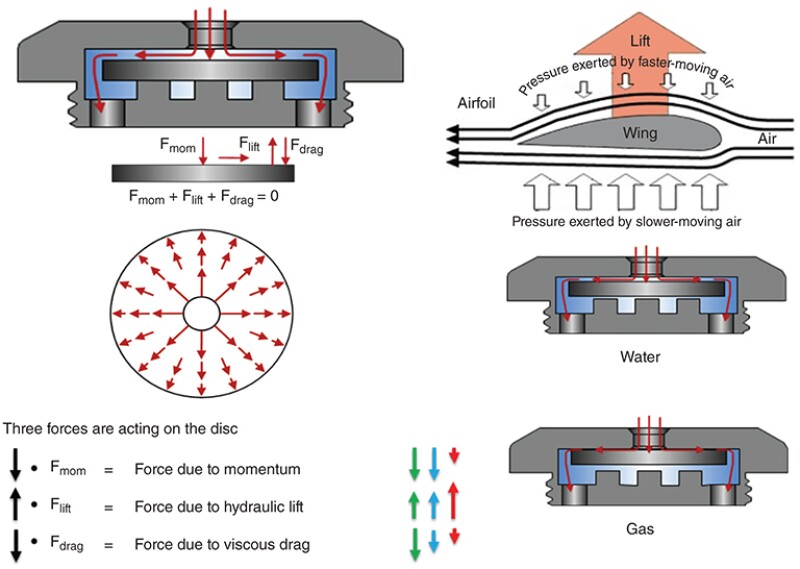
The overall geometry of the device is critical to its ability to balance these forces effectively and create the desired fluid-dependent pressure drop.
Field A employed 7.5-mm AICD valves to match the performance of the devices to the potential well flow rate. The oil, water, and gas viscosities are 0.40 cP, 0.27 cP, and 0.018 cP, respectively, at downhole flow conditions.
Devices are deployed as part of the lower completion or retrofitted into an existing well where the valve is mounted into the basepipe or screen section. The lower completion is segmented into multiple compartments or zones with one or more devices within each zone. The number of compartments used in a wellbore depends on the heterogeneity of the reservoir rock, natural compartmentalization of the reservoir, the mechanism of the breakthrough of unwanted effluents, and the condition of the wellbore.
The sand-screen joint selected for Field A incorporates 150-micron premium mesh as shown in Fig. 2. The flow path from the reservoir is marked by arrows.

In order to be successful, some fundamental principles of AICD applications must be understood (SPE 173841).
- AICDs are not downhole separators—what enters the wellbore must leave the well through the AICDs and up the production conduit.
- There must be a significant difference in the fluid properties to allow the AICD to discriminate between fluids.
- For an AICD completion to reduce the gas/oil ratio (GOR) or water cut, there must be a difference in free gas or water cut between compartments along the length of the wellbore.
In the case of oil/water applications, the difference is primarily based on the viscosity of the fluids. For oil/gas applications, the difference is based on both viscosity and density.
To ensure optimized oil recovery in Field A and to mitigate the dominant threat of early gas breakthrough, the operator performed an extensive evaluation of the application of AICD completion. The performance model was implemented for the first time in the operator’s in-house dynamic simulation software. Fig. 3 shows the single-phase AICD performance curve with Field A conditions.
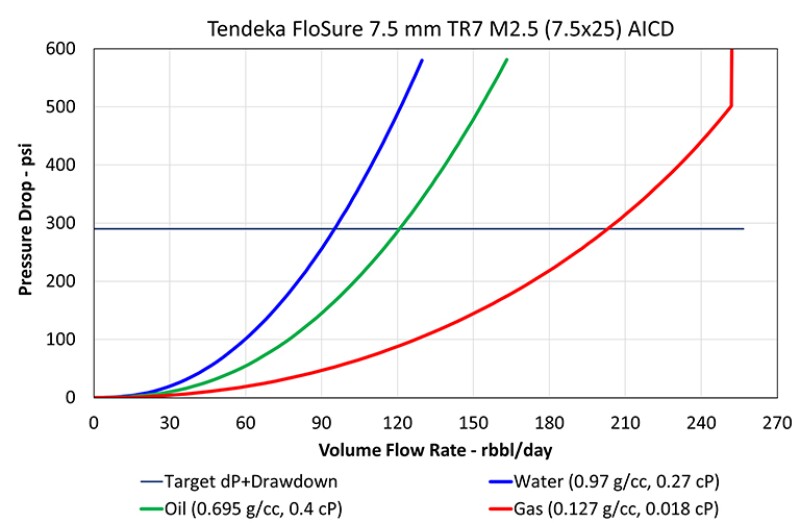
The lower completions in the wells in Field A were completed with 5½-in. AICD liner and swellable packers to satisfy zonal isolation and inflow control. Wellbore flow simulations run in OLGA simulation showed promising results. This suggests that the entire 6,000 ft of the horizontal section can fully unload to the toe section and contribute to the production of the well. A front-end engineering design process was employed to optimize the AICD completion design. This had to be sufficiently robust to restrict gas production and reduce GOR, allowing oil production during the initial flow period before gas coning.
Field A was developed in two stages—Phase 1 and Phase 2 over a 2-year period. A look-back analysis of one of the Phase 1 wells was completed to compare the pre-drill predicted production performance to the post-drill model (tuned with initial production data) and compared to the prediction of a standalone screen production performance as gas progressively breaks through.
Fig. 4 shows the permeability of the reservoir along the wellbore based on LWD logs, while Fig. 5 shows the fluid saturation profiles for the progressive breakthrough of gas along the wellbore.
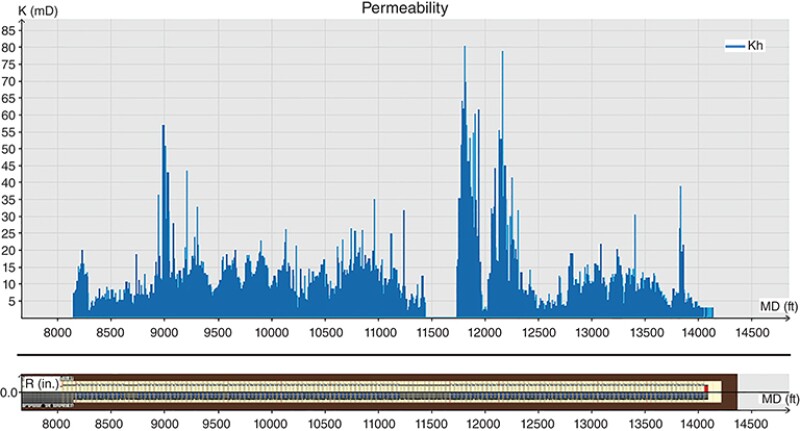
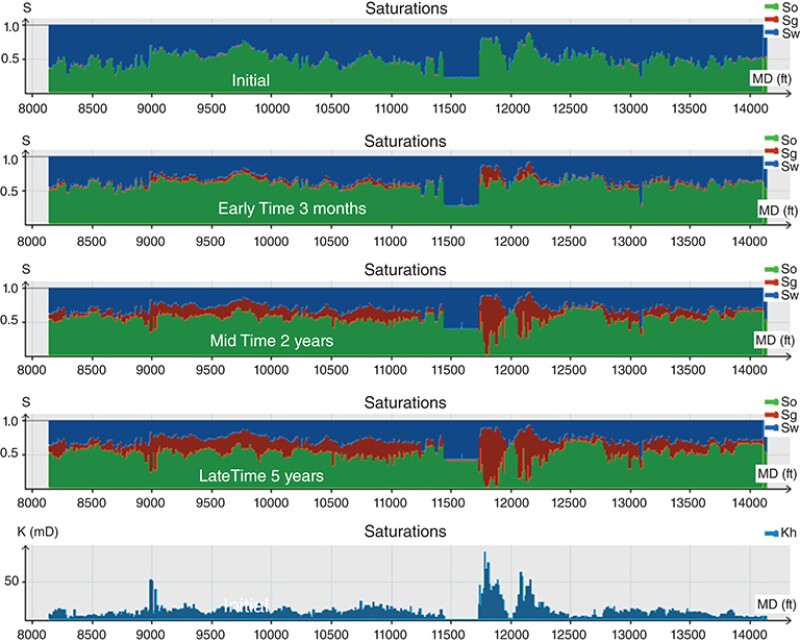
This analysis demonstrates the ability of the AICD completion to manage the GOR from the well while sustaining oil production and provides a basis for the completion equipment inventory required for each development phase.
Real-Time Analysis and Completion Design Modification While Drilling
Prior to drilling the reservoir section, a wellbore flow model was constructed based on the well construction prognosis (directional plan). A best estimate of reservoir properties was based on the geologic model. As drilling of the reservoir section progressed, the wellbore flow model was periodically updated with petrophysical data from LWD and directional survey, such that a significant amount of the AICD completion was enhanced to anticipate potential problems such as unproductive reservoir, washouts, and lost circulation zones before reaching total depth (TD).
Once at TD, the wellbore flow model was used to optimize the AICD completion design further to compensate for future gas breakthrough scenarios and to predict the productivity of the well. This was carried out while the wellbore was cleaned out and conditioned in preparation for running the completion.
Rig efficiency was assisted by the pre-modeling carried out with real-time data while drilling to TD. This allowed the tally to be completed by the time the drilling bottomhole assembly was back on the surface.
Completion Installation
Hole cleaning and check trips were conducted to ensure good hole conditions before running in the hole with the AICD liner. Heavyweight drillpipe and normal drillpipe configurations were used with a swivel tool to allow the string to be rotated at the surface. This provided more set-down weight to facilitate running in the hole. The AICD valves had shrouds as debris barriers which caused the outside diameter to be slightly larger than the 5.5‑in. tubing diameter. In the 8.5‑in. hole, there were no challenges to deploy to TD with swell packers and centralizers on each tubing joint.
Friction factors were monitored while torque and drag modeling was performed during drilling to predict a roadmap for the completion’s conveyance. As a result of these actions, the AICD tubing joints were conveyed successfully to the targeted TD.
Production Operational Challenges
As expected of thin oil rim producers, the gas breakthrough occurred a few months after production. As Well A2 gradually started to observe gas breakthrough and GOR increased, the drawdown eventually approached the drawdown limit. The pressure drops across the AICD completion in this well were calculated based on a static wellbore modeling to be around 700 psi vs. a recommended pressure drop of 600 psi. Degradation of AICD valves due to erosion are expected at a pressure drop of more than 600 psi.
As Field A production is gas-constrained, to meet the reservoir management strategy and to conserve reservoir energy, production from a lower-GOR well was preferred to maximize oil production in the field. However, despite being the lowest GOR well, the production of Well A2 had to be constrained within drawdown and AICD differential pressure limited, resulting in a lost opportunity to increase oil production in the field.
Production Results/PLT
In Well A1, gas production started to increase steeply within 2 months of production. As the gas rate increased, the productivity of the well significantly dropped from an initial productivity index of 50–100 bbl per day/psi to less than 20 bbl per day/psi in the following few months. This is likely due to the additional pressure drop contribution across AICD valves as they move to restrict the gas influx. However, frequent well tests were carried out every 2 to 4 weeks for each of the wells, and the history match of the dynamic model suggested that the production rates were largely as expected.
It should be noted that traditional productivity index calculation as described above may not be a great indicator of well performance once completed with flow control devices such as AICDs.
To understand the flow contribution in the lower completion and to calibrate both the dynamic reservoir and wellbore models, downhole production logging was planned in a number of wells in Field A. Despite operational challenges, the logging was successfully carried out in Well A1.
Results of the production logging were compared with the wellbore and dynamic model simulations. As seen in Fig. 6, the AICD was proven as working. A failed AICD would have resulted in a much higher flow rate, which was not seen from the logging result.
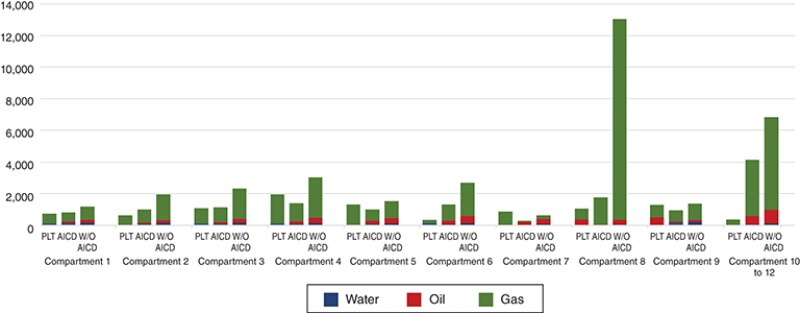
The PLT interpreted result is in line with the dynamic model from total hydrocarbon and water contribution along the well. High GOR observed in the well is likely driven by reservoir behavior rather than AICD failure to arrest high-gas compartment as shown in Fig. 7.
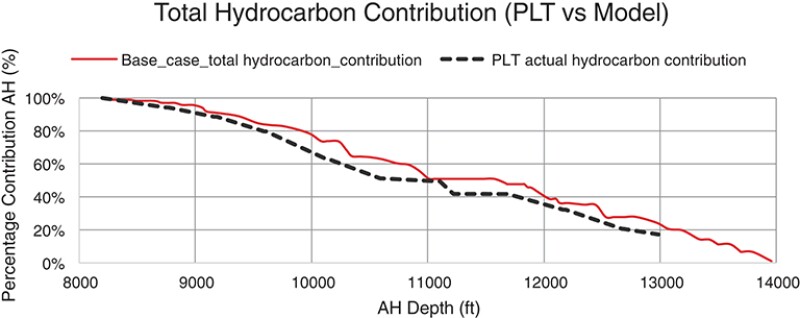
This provides confidence in the ability of the dynamic model to understand the future coning behavior of wells within the same pinnacle. The PLT also confirmed that almost all 6,000 ft of the horizontal section completed was contributing to flow, as per the models.
Summary and Conclusions
Despite some operational challenges and constraints during the installation and operational phase, AICD completions have proven to be an effective method of moderating gas breakthrough while producing a thin oil rim application located in a heterogenous, carbonate reservoir.
It is estimated that the cost savings of the AICD completions in six wells is greater than $20 million in capital and operating expense compared to a more conventional sliding side door (SSD) completion to manage gas breakthrough. In addition, the AICD completion avoids the risks associated with interventions to identify the location and shut-off gas breakthrough in the SSD completion.
The project won the Petronas 2019 COMSTEC Completions Award for the application of AICD technology.
The maximum ultimate reserves that will be recovered by Field A will be assessed in the coming years.
A post-installation review of the production performance of Phase 1 and Phase 2 wells was carried out, which included running a PLT on one well. This not only demonstrated the ability to accurately model the performance of these wells, but also that the AICD completions are effective in ensuring production contribution from all of the reservoir quality intervals in the long horizontal, and in restricting free-gas production from intervals experiencing gas-cap breakthrough.
As with any advanced completion application, the success of the project and value achieved is enhanced by extensive preparation. This includes an extensive reservoir and well performance modeling for the completion design, operations planning, site integrations tests, compatibility checks with chemical pumped, and anticipation of potential problems to provide contingency actions. Critical to this process is the participation of an integrated team of petroleum engineers, well construction engineers, project engineers, drilling contractor, and service and equipment providers.
For Further Reading
SPE 159634 Increased Oil Production at Troll by Autonomous Inflow Control With RCP Valves by Martin Halvorsen, Geir Elseth, and Olav Magne Nævdal, Statoil ASA.
OTC 30403 Sand Production Management While Increasing Oil Production of a Gravel Packed Well Equipped With RCP Autonomous Inflow Control Devices in a Thin Heavy Oil Reservoir in Offshore China by Shuquan Xiong, Fan Li, Congda Wei, and Donghong Luo, CNOOC China Ltd.-Shenzhen; and Mojtaba Moradi, Tendeka.
OTC 30363 Enhanced Oil Production with Autonomous Inflow Control Devices in a Thin Oil Rim Reservoir Malaysia by Fuziana Tusimin, Latief Riyanto, and Norbaizurah Ahmad Tajuddin, Petronas Carigali Sdn. Bhd.; and Mojtaba Moradi, Raam Marimuthu, and Michael Konopczynski, Tendeka.
SPE 193718 Production Optimisation of Heavy Oil Wells Using Autonomous Inflow Control Devicesby Mojtaba Moradi, Michael Konopczynski, Ismarullizam Mohd Ismail, and Iko Oguche, Tendeka BV.
SPE 173841 The Improvement of Production Profile While Managing Reservoir Uncertainties With Inflow Control Devices Completions by Mojtaba MoradiDowlatabad and Faraj Zarei (CMG Europe), Heriot-Watt University; and Morteza Akbari, Baker Hughes Inc.
SPE 205407 Annular Phase Separation With AICD Completions—The Impact on Well Flow Performance and Control of Unwanted Effluents by Michael R. Konopczynski and Mojtaba Moradi, Tendeka.
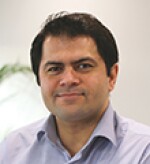
Mojtaba Moradi, SPE, is a principal reservoir engineer at Tendeka in Aberdeen. He holds a PhD in petroleum engineering from Heriot-Watt University. He is a member of the European Association of Geoscientists and Engineers (EAGE).
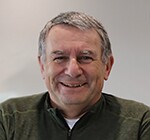
Michael Konopczynski, SPE, is a director of subsurface engineering at Tendeka in Houston. He holds a BSc in mechanical engineering from the University of Toronto. He is a member of the Association of Professional Engineers and Geoscientists of Alberta (APEGA).
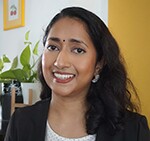
Thanushya Krishnan, SPE, is a production technologist in Shell Malaysia. She has almost 10 years of experience in oil and gas, working in fields in Malaysia and Russia. She holds a BSc in chemical engineering from University of Technology Petronas, Malaysia.
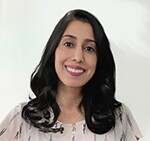
Harwinder Kaur Sandhu is a completions engineer in Shell Malaysia. She holds a BSc in mechanical engineering from University of Tenaga Nasional, Malaysia.