Background
The important role of optimized injection wells has been recognized as a crucial element of reservoir management for optimum field development. Over the years, diverse approaches have been deployed to optimize fluid conformance in injection wells to enhance the effectiveness of water/gas/polymer flooding, ultimately maximizing field recovery. The functionality of most applied technologies to provide optimum injection conformance has been limited as the properties of injection wells are continually changing.
This article presents an overview of oilfield production data for using the first and only autonomous outflow control devices and demonstrates their benefit in various well-injection applications in the Middle East, Norway, North America, and China by optimizing well injectivity.
Multiple surveillance data such as injection logging tool (ILT), distributed temperature sensing (DTS),and step-rate and injectivity test data have proven the success of FloFuse both in terms of achieving the target injection profile and controlling the thief zones. The objectives of installations include controlling faults, natural and thermal fractures, and high-permeability zones for injection of water, gas, and polymer in both carbonate and sandstone reservoirs.
FloFuseTM Autonomous Outflow Control Device
Flow control devices in injection wells typically fall into two broad categories: passive and active devices. In the conventional sense, interval control valves ( ICVs) represent active devices that possess the capability to modify the inflow area, allowing operators to proactively and/or reactively control the well.
Despite the cost and complexity associated with ICVs completion, a significant challenge arises from the necessity for real-time knowledge of well and reservoir performance to justify adjusting valve positions. The substantial uncertainties involved in such operations restrict the practical application of these devices. On the other hand, passive devices like inflow control devices (ICDs) are more cost-effective, creating completions with fixed configurations that influence the well's outflow.
However, the impact of passive ICDs can be limited and diminished by the impacts of dynamic changes in reservoir properties, especially in proximity to the wellbore including the evolution of filter cakes, thermal fracture, solid deposition within the reservoir, chemical reactions, the (re)connection of vuggy spaces, or other phenomena altering the initial reservoir properties.
The autonomous outflow control device (FloFuseTM) has been developed to address such challenges and mitigate disproportionate fluid injection into thief zones that could lead to the short-circuiting to production wells (SPE197612). This bi-stable active flow control device operates in two conditions: initially, it functions as a normal passive outflow control device, and if the injected flow rate exceeds a predetermined limit, the device automatically shuts off. Fig. 1 depicts the cross section and key elements of the device, which is a spring-loaded, open injection outflow valve designed to limit the flow area to specific zones when a prescribed tripping flow rate is exceeded.
As mentioned before, under normal operating conditions, the device allows injection outflow to pass through a normally operating nozzle and then through sand controls like shrouds or screens if necessary (Fig. 2). If the pressure built up in the reservoir decreases due to the impacts of thief zones such as inducing, dilating, or propagating fractures, or change in mobility of fluid. etc., the injection rate into that zone significantly increases.
This results in an elevated pressure drop across the device, countering the return spring until the flow area between the seal face and the nozzle becomes fully restricted. This triggers the valve to the fused (closed) position, restricting outflow into that zone. As a result, the outflow into the "fused" zone is highly limited, allowing injection to be diverted into other completion zones. This performance enables operators to minimize the impact of thief zones on injected fluid conformance and respond to dynamic changes in reservoir properties, specifically the growth of fractures. Importantly, this technology eliminates the need and cost of running an ILT and the complex well interventions required to open/close integrated sliding sleeves (if available) in traditional completions, enabling optimized well performance autonomously.
The valve is fully reversible, and it will reset if the flow rate becomes sufficiently distributed again. The target normal operating rates, degree of outflow control, and trigger rates can be adjusted based on the application.
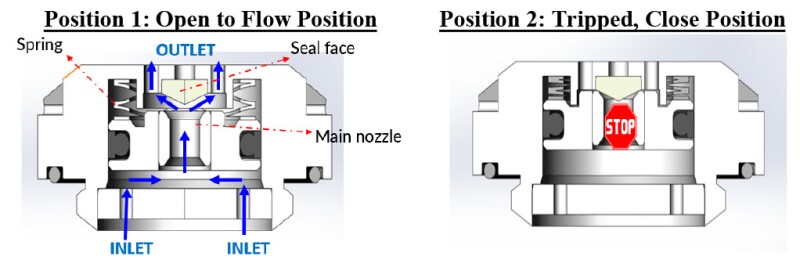

Thorough laboratory tests were conducted to assess the performance of a single valve under various fluid and gas-injection conditions. Specifically, a series of water-injection experiments were carried out to characterize the valve.
The characteristics were delineated, for example, by plotting the curve of differential pressure drop across the device against the flow rate passing through it. The pressure drops across valves of different sizes (2.2 mm, 3 mm, and 4.5 mm) are presented as a function of the single-phase flow rate of water in Fig. 3. The results indicate that, upon reaching a certain flow rate, the valve shuts off the water flow. The tripping points are contingent on the nozzle size of the valve, with differential pressure tripping points of 8, 9, and 14 bar for 2.2 mm, 3 mm, and 4.5 mm nozzles, respectively.
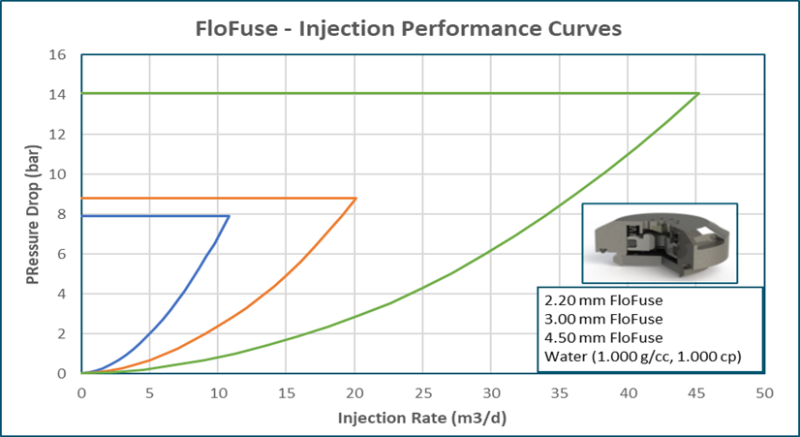
Global Applications of FloFuse Completion
Like other ICDs completion, these devices should be installed in several completion zones in the well by annular flow isolation tools like swell packers to provide independent control to each layer. Each zone normally comprises both FloFuse and ICDs to deliver optimum performance. When the autonomous valve shuts, the bypass ICD will still deliver the minimum flow rate desired to the zone. If this is not required, the ICDs could be opted out. The required number of each device and the number of zones depend on the case and should be determined through modeling practice.
Similar to other passive ICD completions, these devices should be positioned in multiple completion zones within the well, utilizing annular flow isolation tools such as swell packers to ensure independent control for each layer. For the FloFuse completion, each zone should normally incorporate both FloFuse and bypass valves such as ICDs to achieve optimal performance. In the event of autonomous valve closure, the bypass ICD will continue delivering the minimum desired flow rate to the zone. If this is not necessary, the option to exclude the ICDs is available.
The appropriate quantity of each device and the required number of zones relies on the unique characteristics of the specific case. To effectively deploy the FloFuse completion for each wellbore, a comprehensive modeling practices workflow will be initiated, often initiated pre-drilling and swiftly updated with the actual well properties once the well is drilled to deliver optimum performance.
Since its introduction in 2019, the device has gained recognition for its benefits from various operators globally. Supported by the findings of numerous simulation modeling studies and results obtained from a dozen field applications worldwide (SPE 207361, SPE 207647, SPE 211438) the FloFuse has been shown to deliver the optimum injection-well performance.
For example, in one well the production logging results from data post- and before installation confirmed that the flow-control devices were successful in controlling the water injection into the suspected thief zones by 42%. Another example in a polymer- injection well supported by DTS data as well as other surveillance data, it was confirmed that 93% of the anticipated conformance has been achieved, and the water cut from the oil producers nearby drastically dropped, resulting in less production of unwanted fluid and therefore more sustainable oil production.
The FloFuse device enables operators to deliver optimum water-, polymer-, acid-, and gas-injection techniques resulting in enhanced well-injectivity performance and hence more sustainable and increased oil production while avoiding costly and often complex well interventions. The device's characteristics make it an ideal completion for a range of injection operations, including water-injection wells (SPE 207647), polymer injection wells (SPE 207361, SPE 211438, SPE 211477), acid-injection stimulation operations (SPE 205975, SPE 211438), as well as WAG (water alternating gas) operations, geothermal wells, and CO2 EOR/storage wells.
In storage applications, particularly in CO2 wells, the device could play a crucial role in ensuring injection conformance and minimizing risks related to compromised caprock integrity over time, thereby preventing containment loss to zones above while eliminating the crossflow. Additionally, the device can function as a mechanical diverter, effectively managing and optimizing matrix acid stimulation operations to improve injectivity profiles (SPE 205975).
References
SPE 197612 A Game Changer for Injection Wells Outflow Control Devices to Efficiently Control the Injection Fluid Conformance by Ismarullizam Ismail, Michael Konopczynski, and Mojtaba Moradi. Abu Dhabi International Petroleum Exhibition & Conference, Abu Dhabi, UAE, November 2019. https://doi.org/10.2118/197612-MS
SPE 205975 The New Flow Control Devices Autonomously Controlling the Performance of Matrix Acid Stimulation Operations in Carbonate Reservoirs by Mojtaba Moradi and Michael R. Konopczynski. SPE Annual Technical Conference and Exhibition, Dubai, UAE, September 2021. https://doi.org/10.2118/205975-MS
SPE 207361 Autonomous Outflow Control Technology in AOCD in New Water/Polymer Injectors in Heavy Oil Fields From South Sultanate of Oman by Ameera Al Harrasi, Muna Maskari, Gerardo Urdaneta, Ali Al-Jumah, Salim Badi, Iman Busaidi, Khalfan Harthy, Osama Abazeed, and Mojtaba Moradi. Abu Dhabi International Petroleum Exhibition & Conference, Abu Dhabi, UAE, November 2021. https://doi.org/10.2118/207361-MS
SPE 207647 The New Generation of Outflow Control Devices Autonomously Controlling the Conformance of Water-Injection Well—A Case Study with ADNOC Onshore by Sultan Ibrahim Al Shemaili, Ahmed Mohamed Fawzy, Elamari Assreti, Mohamed El Maghraby, Mojtaba Moradi, Prabodh Chaube, and Tawheed Mohammed. Abu Dhabi International Petroleum Exhibition & Conference, Abu Dhabi, UAE, November 2021. https://doi.org/10.2118/207647-MS
SPE 211438 A Polymer Flood Pilot With Autonomous Outflow Control Device Technology and Resilient Cost Management from South Sultanate of Oman by Ameera Al Harrasi, Salim Badi, Gerardo Urdaneta, Mohammed Ramli, Said Kindi, Yousuf Sinani, and Khalfan Harthy. ADIPEC, Abu Dhabi, UAE, October 2022. https://doi.org/10.2118/211438-MS
SPE 211477 Fiber-Optic Surveillance for Water and Polymer Conformance Monitoring in an EOR Project in Petroleum Development Oman by Mohammed Salim Al Hashemi. ADIPEC, Abu Dhabi, UAE, October 2022. https://doi.org/10.2118/211477-MS
SPE 0621-0038-JPT Autonomously Controlling the Conformance of Injection-Well Fluids by Mojtaba Moradi. J Pet Technol. https://doi.org/10.2118/0621-0038-JPT
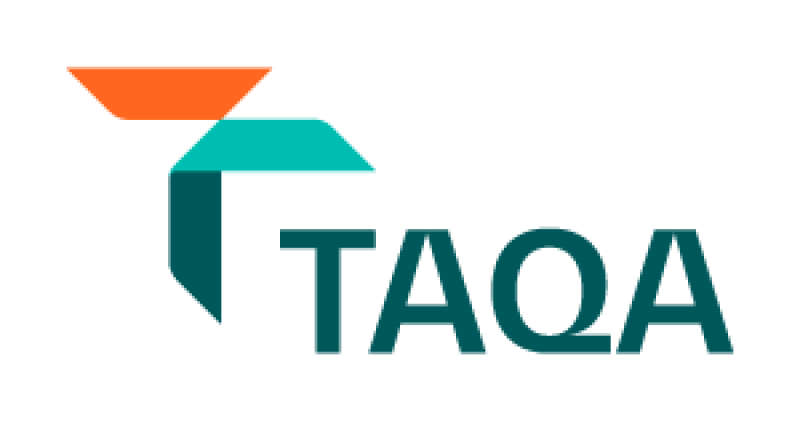